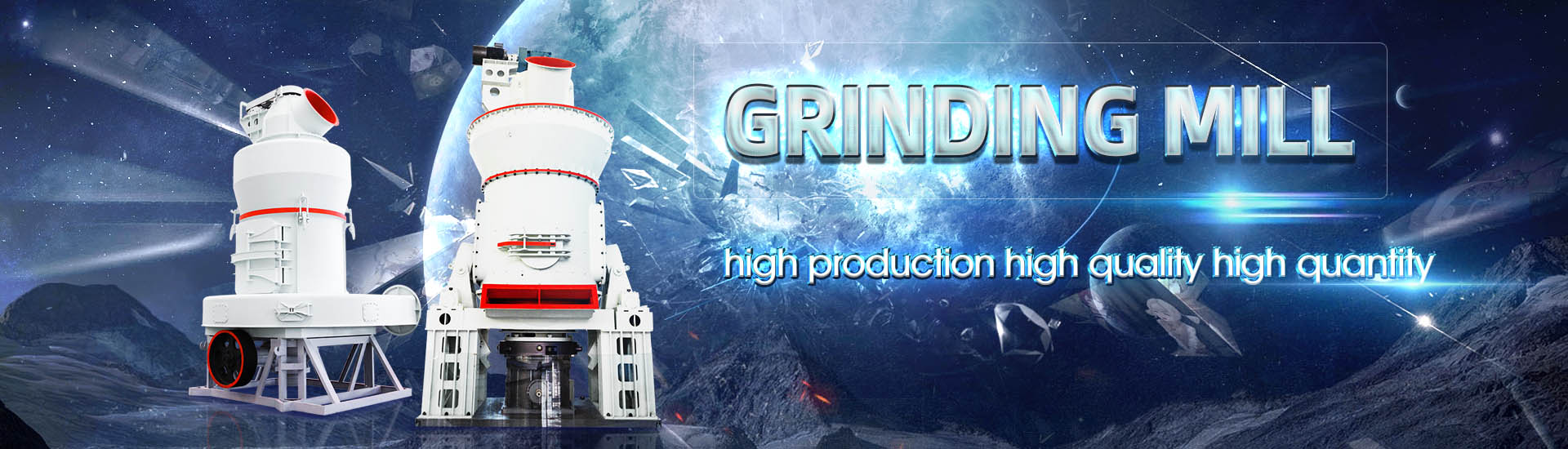
Cement plant workshop process flow design
.jpg)
Simulation and Optimization of an Integrated Process Flow Sheet
2021年3月9日 In this study the process flow diagram for the cement production was simulated using Aspen HYSYS 88 software to achieve high energy optimization and optimum cement The Cement Plant Operations Handbook is a concise, practical guide to cement manufacturing and is the standard reference used by plant operations personnel worldwide Providing a The Cement Plant Operations Handbook International Cement This study investigated four factors (water/binder ratio, silica fume, fly ash, and sand/binder ratio) using the orthogonal experimental design method to prepare the mix proportions of a Process flow diagram for the cement manufacturing process engineering for the cement lime industries mechanical engineering (plant design, piping, process gas handling, environmental controls, nuisance dust collection and materials PROCESS ENGINEERING FOR THE CEMENT LIME INDUSTRIES
.jpg)
Process flow diagram for the production of cement
In this study the process flow diagram for the cement production was simulated using Aspen HYSYS 88 software to achieve high energy optimization and optimum cement flow rate by varying• ETHZ has simulated and adapted the CAP system to different cementplant flue gases; • New ratebased model was developed and used to validate fullscale CAP simulations for cement Process characteristics of clinker and cement production SINTEFexperience in the cement sector and focus on specific technical measures that could be implemented by cement plants to reduce their operating costs and improve their carbon IMPROVING THERMAL AND ELECTRIC ENERGY EFFICIENCY AT 2020年2月15日 Cement plants basically consist of three manufacturing parts: (i) raw material and fuel supply preparation, (ii) clinker production (commonly named as the pyroprocessing Parametric Studies of Cement Production Processes
7TOCS.jpg)
CFD Modelling in the Cement Industry Turnell Corp
CFD is a branch of fluid dynamics that uses numerical methods to analyse fluid flows It estimates and predicts flow velocity, temperature, pressure, density, chemical concentrations and many 2023年11月1日 We give some tips for cement plant design, including cement site selection, mineral selection, 5000tpd Dry Process Cement Plant Project In Liaoning; including open flow grinding, ordinary closed circuit grinding, pre 8 Tips For Cement Plant Design Cement Download CAD block in DWG General plan of the cement manufacturing process it is a vertical grinding system (65357 KB)Cement plant in AutoCAD Download CAD free 2018年8月28日 Generally cement plants are fixed where the quarry of limestone is near bye After explaining the complete process of cement making, flow chart would be like that flow chart present the summary of whole process as shown Cement Manufacturing Process The Engineering
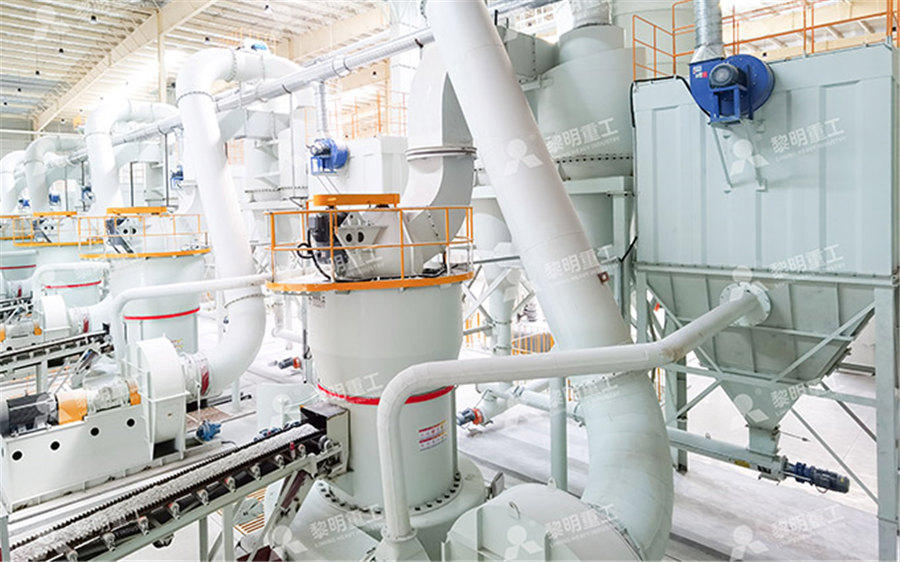
Cement plant design under EPC contract ESFC Investment Group
Choosing the optimal plant layout early in the engineering design of a cement plant is critical to ensuring the efficiency, safety and sustainability of the facility in the future The project must take into account a whole range of factors, ranging from the technology chosen, the raw materials and equipment used, to the expected productivity and operating time (usually about 20 hours per 2017年8月15日 Located in Westminster, MD, Process Systems Design (PSD) provides bulk materials handling equipment, plant systems engineering, specialty machine design, and process control engineering PSD has industry expertise and focus for bulk handling systems, Vape and ELiquid, Biomass, and plastics and polymersThe Cement Manufacturing Process Process Systems DesignDownload scientific diagram Process flow sheet of a CAP process integrated in a cement plant (adapted from [46]) from publication: CO2 Capture, Use, and Storage in the Cement Industry: State of Process flow sheet of a CAP process integrated in a cement plant The cyclone preheating system Phase IV: Calcination The calcination is the core phase of the cement making dry process The calcination of the preheated raw meal takes place in the rotary kiln of the cement plant The rotary kiln is a huge rotating furnace in which the raw meal is heated up to 1450 ⁰C and turned to clinkerHow Is Cement Produced in Cement Plants Cement Making Process
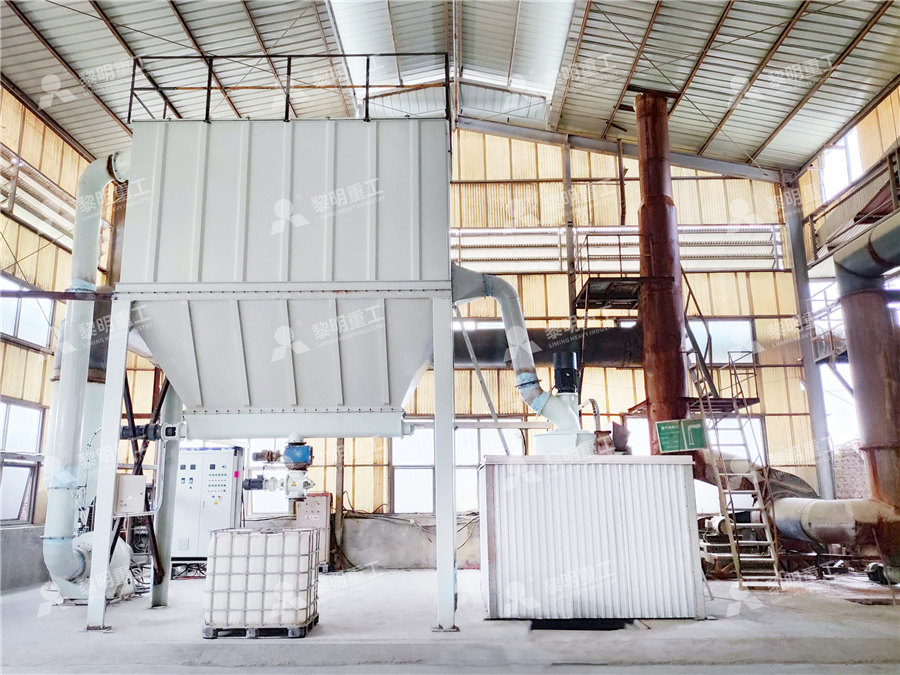
Nomograms for Design and Operation of Cement Plants BS
Cement Plants Process of making cement involves ‘calcination’ of limestone that is release of Carbon Dioxide almost all aspects of the design of cement plants He has been a pioneer in computerising process, 6 Options for Locations of WHR Systems Flow Charts 7 Ordering WHR Systems 8 Capital Costs, 2021年3月9日 In this study the process flow diagram for the cement production was simulated using Aspen HYSYS 88 software to achieve high energy optimization and optimum cement flow rate by varying the flow rate of calcium oxide and silica in the clinker feed Central composite Design (CCD) of Response Surface Methodology was used to design the ten experiments for Simulation and Optimization of an Integrated Process Flow Sheet Cement Plant: The Manufacturing Process worldcementassociation 1 Limestone (CaCO3) is taken from a quarry 2 4 3 The limestone is fed into a crusher and then stored until needed The clinker is mixed with additives, such as gypsum, and then ground in a Cement Plant: The Manufacturing Process 4 5 World Cement The 6 Main Process Fans in Cement factory IF YOU WORK IN A CEMENT PLANT AND YOU NEED COURSES AND MANUALS LIKE THIS MANUAL AND BOOKS AND It is considered as the ‘lung’ of the clinker burning system The 6 Main Process Fans in Cement factory
.jpg)
Typical cement manufacturing process flow
Finally, during the cement grinding and distribution process, firstly the cooled clinker is ground with around 5% of gypsum and other 17 JRTE2020 cementitious materials to form the final cement When designing a concrete batching plant, there are several key points to take account, including site selection, equipment configuration, mixing process design, and strategic plant layout, to ensure high efficiency, safety, and environmental Key Points in Concrete Batching Plant Design and LayoutRaw mill is generally called cement raw mill, raw mill in cement plant, it refers to a common type of cement equipment in the cement plantIn the cement manufacturing process, raw mill in cement plant grind cement raw materials into the raw mix, and the raw mix is sent to the cement kiln to make cement clinker, next, clinker and other admixtures will be ground into finished cement by Raw mill Cement Plantfor cement process plants As a global organization with more than 160 years experience in air processes Our equipment is providing constant, dependable service in many of the world’s most modern and productive cement plants We design the fans that operators designed deflectors that modify flow patterns to minimize detrimental Armored fan technology for cement process plants Chart
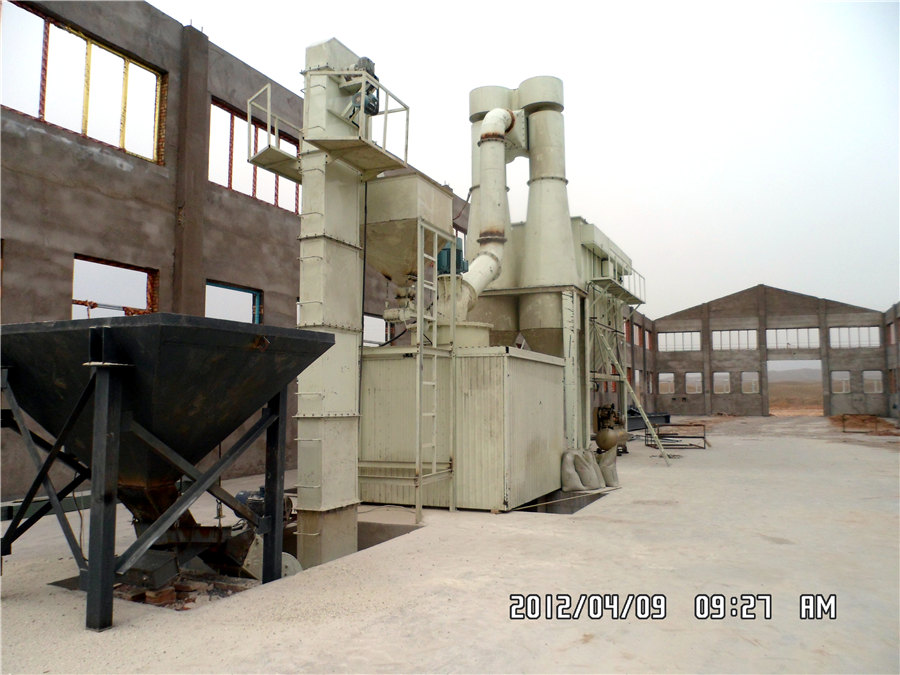
CEMENT PLANTS APPLICATIONS Boldrocchi Group
Boldrocchi Applications in Cement Plants HEAVY DUTY FANS Boldrocchi is the right partner to design, supply and successfully start up the complete gas handling and dedusting system of any cement plant Boldrocchi has the unique advantage of having the internal know how for each of the key components, including fans, bag filters, gas coolers,Cement plant operation handbook jorge pinedo sanchez download Download free PDF View PDF chevronright Production of Cement Engr Sajid Chaudhary download Download free PDF View PDF chevronright LAPORANKERJAPRAKTEKSEMENGRESIKBABIVpdfpdf nihayatul fadila(PDF) Handbook for Desinging Cement Plants Academia2020年7月4日 15 Cement Storage Silo The cement storage silo is used for storing the finished product – cement 16 Packing and Dispatch The cement is packed with the help of a rotary packer and finally dispatched to the market 17 Central Control Room It is the nerve center of the cement plant since all equipment is controlled from this placeBASIC CEMENT PLANT LAYOUT – Process Cement Forum The Cement Figure 11 A small section of a refinery showing equipment, piping system and other items The design of process plants is a complex team effort involving different disciplines of engineering: process (chemical), mechanical, piping, electrical, instrumentation, controls, materials and projectFundamentals of Process Plant Layout and Piping Design
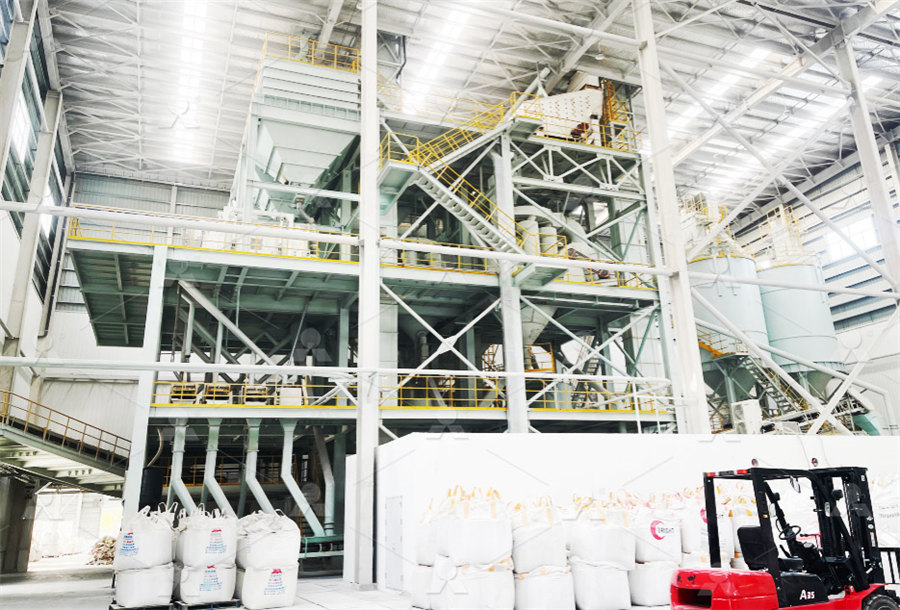
Analysis of material flow and consumption in cement production process
2015年8月1日 This cement plant operates on a dry process line with a fi vestage suspension preheater and an inline precalciner The kiln is 4 m in diameter and 60 m in length2012年8月30日 Generally cement plants are fixed where the quarry of limestone is near bye This saves the extra fuel cost and makes cement somehow economical Raw materials are extracted from the quarry and by means of Cement Manufacturing Process Engineering Intro2024年1月17日 Contemporary methods of manufacturing cement can be divided into two ways: dryprocess cement production and wetprocess cement production The latter measure has been widely utilized in the cement What Do You Know About Wet Process Of Cement Kakaras a,b a Chemical Process and Energy Resources Institute Centre for Research and Technology Hellas, 4th km NR PtolemaisKozani, 50200 Ptolemais, Greece Laboratory of Steam Boilers and Thermal Plants, National Integration of calcium looping technology in
.jpg)
Cement Production Process Cement Manufacturing Process AGICO CEMENT
2020年8月25日 Before you send inquiry Please provide us with project information as much as possible: For a complete project: the material availability, the required output capacity, the process technology, your budgetary and financing status, the estimated starting time, etc For singular machinery: the model, the capacity, your budgetary information, other requirements, etcThis involves optimizing fuel and electricity use in cement plants, which can significantly reduce CO 2 emissions This strategy holds great potential for reducing carbon emissions in cement Process flow diagram for the production of cementfor cement plants Upcoming work: CAP optimization • The Absorber and Direct Contact Cooler (DCC) units were tested under cementlike conditions at GE Power Sweden, Water wash section will be tested later in 2017 Chilled ammonia for cement plant CO 2 capture DCC pilot at GE Power Sweden CAP process flowsheetProcess characteristics of clinker and cement production SINTEF2024年5月23日 The belt conveyor in cement plant operations is an essential component that significantly contributes to the efficiency, safety, and environmental sustainability of the cement manufacturing process By providing a seamless, reliable, and costeffective method for transporting materials, belt conveyors play a vital role in ensuring the smooth operation of Optimizing Material Flow with Belt Conveyor in Cement Plant
.jpg)
Fans in Cement Plants BrownleeMorrow Company
Cement Grinding p p p p p p p p p p p p p p p p p p p p p p p p p p p Raw Mill EFilter p p p p Cement Mill Fan Also in difficult and extreme operational conditions TLTfans secure troublefree operation to our customers p Raw Mill Fan Typical Data volume flow: 80350 m3/s temperature: 90100 °C mech design temperature: 250 °C pressure 2022年5月1日 The waste heat recovery of cement plants has been extensively studied in the past few years Wang et al [16] evaluated an ORCbased WHRS for a typical cement production line, while hexane, isohexane, R601, R123, or R245fa was selected as the working fluidThe results showed that the scheme using R601 had the best economic and environmental Performance evaluation of a novel design for the waste heat 2021年3月24日 Cement manufacturing requires cooling down of hot clinker at temperature of about 1350o C to temperature lower than 100 o C in a cooling system known as clinker coolerModelling of clinker cooler and evaluation of its performance in 2023年11月1日 We give some tips for cement plant design, including cement site selection, mineral selection, 5000tpd Dry Process Cement Plant Project In Liaoning; including open flow grinding, ordinary closed circuit grinding, pre 8 Tips For Cement Plant Design Cement
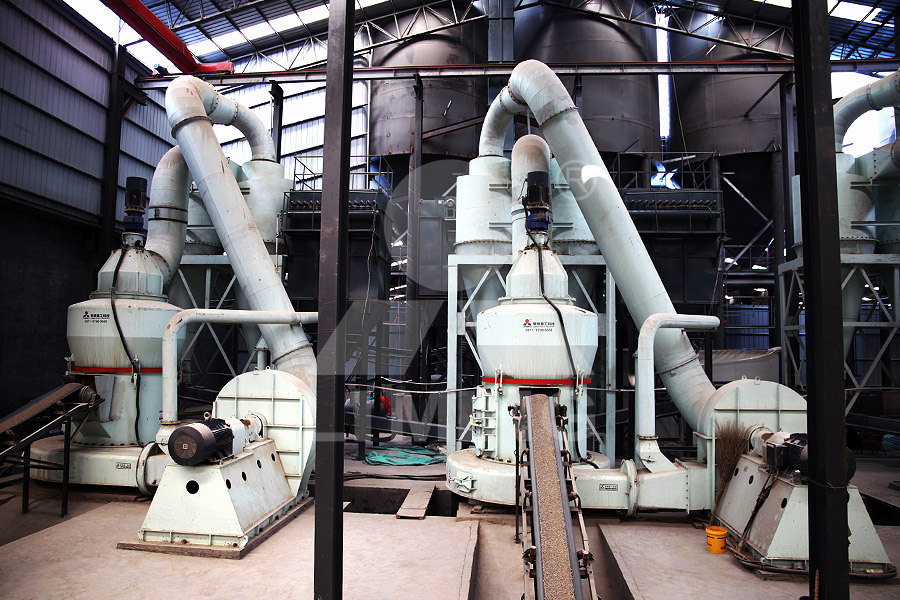
Cement plant in AutoCAD Download CAD free
Download CAD block in DWG General plan of the cement manufacturing process it is a vertical grinding system (65357 KB)2018年8月28日 Generally cement plants are fixed where the quarry of limestone is near bye After explaining the complete process of cement making, flow chart would be like that flow chart present the summary of whole process as shown Cement Manufacturing Process The Engineering Choosing the optimal plant layout early in the engineering design of a cement plant is critical to ensuring the efficiency, safety and sustainability of the facility in the future The project must take into account a whole range of factors, ranging from the technology chosen, the raw materials and equipment used, to the expected productivity and operating time (usually about 20 hours per Cement plant design under EPC contract ESFC Investment Group2017年8月15日 Located in Westminster, MD, Process Systems Design (PSD) provides bulk materials handling equipment, plant systems engineering, specialty machine design, and process control engineering PSD has industry expertise and focus for bulk handling systems, Vape and ELiquid, Biomass, and plastics and polymersThe Cement Manufacturing Process Process Systems Design
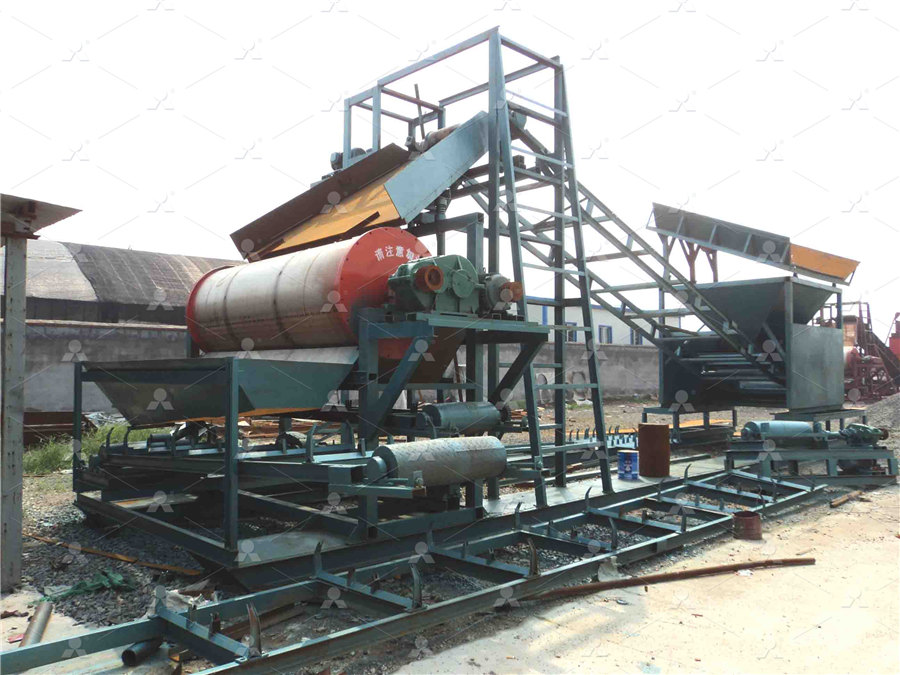
Process flow sheet of a CAP process integrated in a cement plant
Download scientific diagram Process flow sheet of a CAP process integrated in a cement plant (adapted from [46]) from publication: CO2 Capture, Use, and Storage in the Cement Industry: State of The cyclone preheating system Phase IV: Calcination The calcination is the core phase of the cement making dry process The calcination of the preheated raw meal takes place in the rotary kiln of the cement plant The rotary kiln is a huge rotating furnace in which the raw meal is heated up to 1450 ⁰C and turned to clinkerHow Is Cement Produced in Cement Plants Cement Making ProcessCement Plants Process of making cement involves ‘calcination’ of limestone that is release of Carbon Dioxide almost all aspects of the design of cement plants He has been a pioneer in computerising process, 6 Options for Locations of WHR Systems Flow Charts 7 Ordering WHR Systems 8 Capital Costs, Nomograms for Design and Operation of Cement Plants BS 2021年3月9日 In this study the process flow diagram for the cement production was simulated using Aspen HYSYS 88 software to achieve high energy optimization and optimum cement flow rate by varying the flow rate of calcium oxide and silica in the clinker feed Central composite Design (CCD) of Response Surface Methodology was used to design the ten experiments for Simulation and Optimization of an Integrated Process Flow Sheet
.jpg)
Cement Plant: The Manufacturing Process 4 5 World Cement
Cement Plant: The Manufacturing Process worldcementassociation 1 Limestone (CaCO3) is taken from a quarry 2 4 3 The limestone is fed into a crusher and then stored until needed The clinker is mixed with additives, such as gypsum, and then ground in a