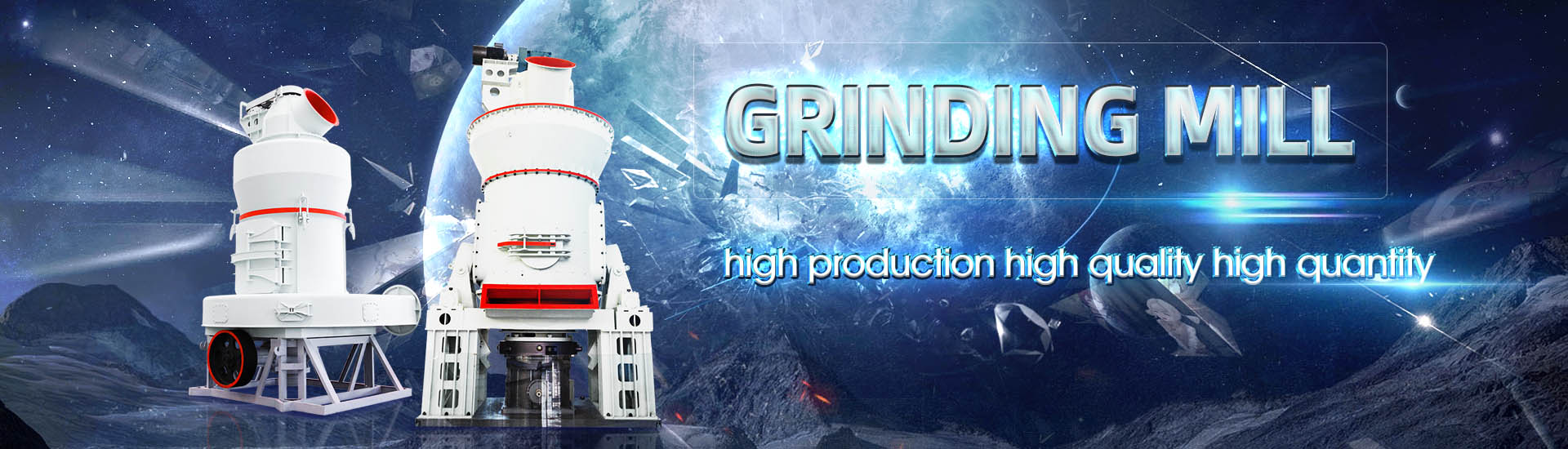
Coal mill coal mill coal mill
.jpg)
Coal Mill an overview ScienceDirect Topics
Coal mills or pulverizers play a very essential part in the coalfired power production system Coal mills grind the coal into fine powder, and the primary air entering the mill dries and drives the The first is that the CO 2 concentration in the flue gas is noticeably higher in a cement plant (Cement PlantThe Loesche coal grinding mill range is divided into two serial types: Small twin mills constructed to individual specifications (LM 122 D to LM 202 D), with table diameters from 1,200 to 2,000 LOESCHEMILLS2012年5月1日 The paper presents development and validation of a coal mill model to be used for improved mill control, which may lead to a better load following capability of power plants Derivation and validation of a coal mill model for control
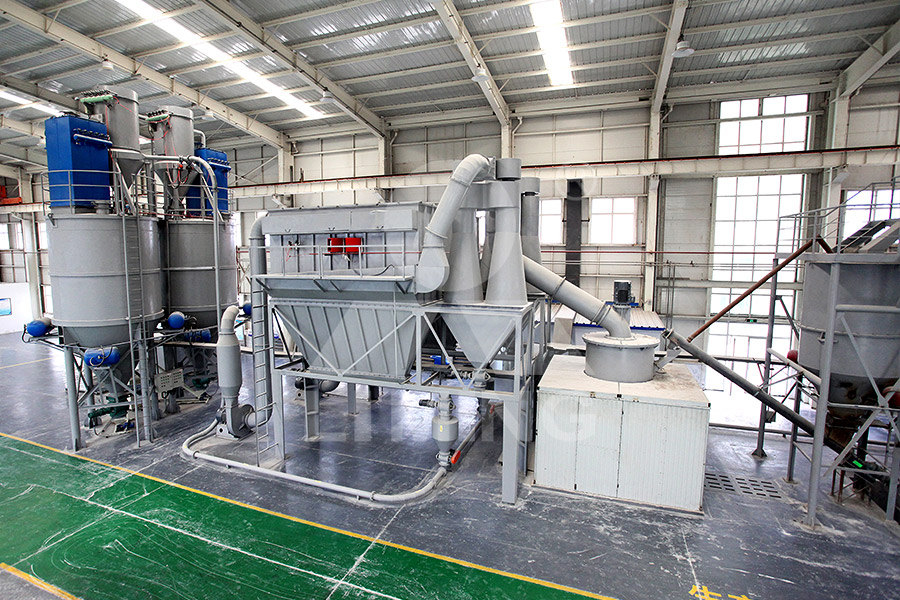
A unified thermomechanical model for coal mill operation
2015年11月1日 Coal mills are bottleneck in coal–fired power generation process due to difficulty in developing efficient controls and faults occurring inside the mills In this paper, a dynamic 2020年8月12日 This study shows the performance of a currently running vertical roller coal mill (VRM) in an existing coalfired power plant In a power plant, the coal mill is the critical An investigation of performance characteristics and energetic 2007年8月20日 This multisegment mathematical model is derived through analysis of energy transferring, heat exchange, and mass flow balances The work presented in the paper Development of a Multisegment Coal Mill Model Using an 2016年1月18日 Firstly, the principles of coal mill is presented, and a coal mill model is established Then we use prediction error method to identify the parameters of the model The Inferential predictive control method of coal mill IEEE
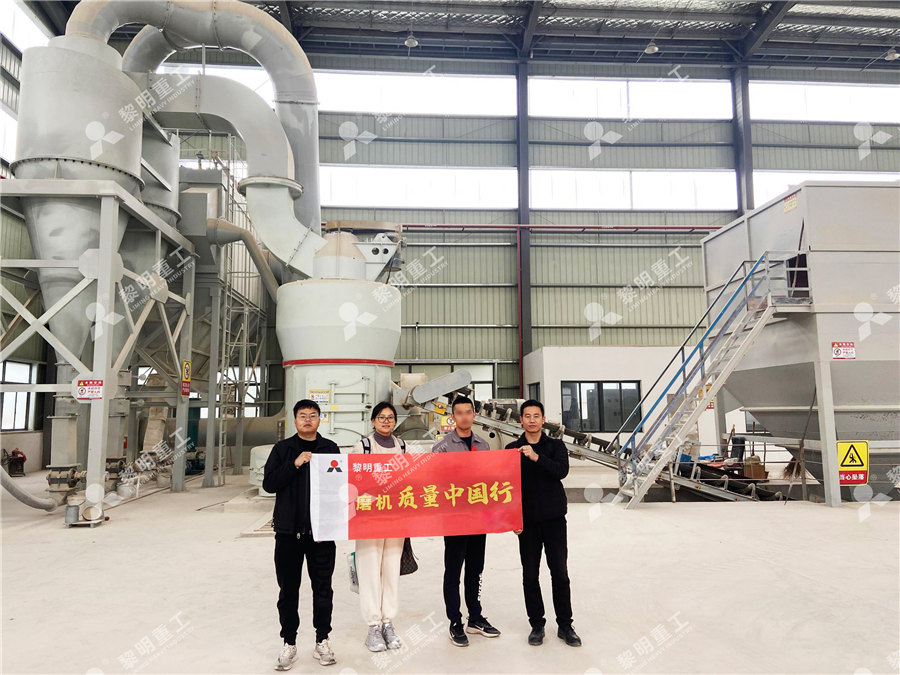
Bowl Mill Coal Pulverizer COAL HANDLING PLANTS
Coal Pulverizer are designed to reduce the size of the incoming raw coal to a fineness that will result in good furnace performance The grinding surface in the pulverizer resembles a shallow dish or bowl Therefore the name “Bowl Mill” Vertical Coal Mill (VCM) is equipment for grinding and pulverizing coal into micron size Rotary kilns then use the powders as fuel burners The VCM has a housing section equipped with aThe layout of the coal mill with a rotary classifier2015年8月1日 Power plant performance and reliability is highly influenced by coal mills that grind, dry, and transport coal to the furnace This paper presents a review of the current state Review of control and fault diagnosis methods applied to coal In bowl mill pulveriser raw coal coming from feeder gets ground between the grinding rolls and bull ring segments installed on the revolving Bowl Bowl is made to rotate at medium speed for proper pulverization of coal Springs exert Pulveriser in Thermal Power Plant Bowl Mill Ball Mill
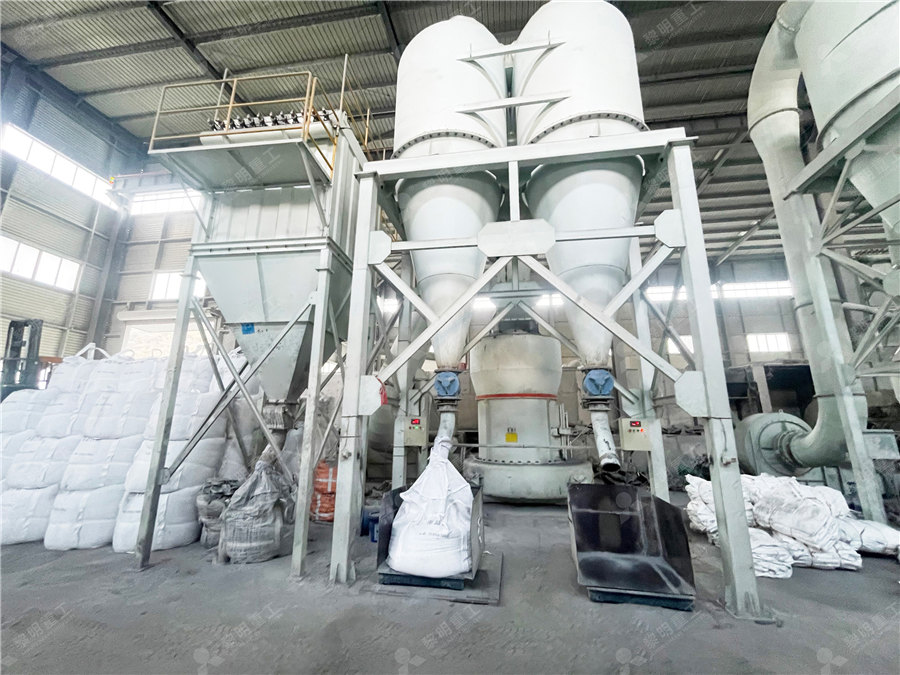
Best Practices and Precautions Coal Mill Safety, Explosion and
Coal mills, essential components in power generation and various industrial processes, pose significant safety risks if not properly managed These mills, used to grind coal into a fine powder for combustion, present potential hazards such as fire, explosion, and mechanical failures This article outlines best practices and precautions to ensure thCoal grinding mills are essential components of power plants, responsible for converting raw coal into fine coal powder that is essential for efficient combustion in power plant boilers Coal grinding mills can also be used to grind biomass and other alternative fuels, providing a more sustainable and renewable energy source for power generationWhat is a Coal Grinding Mill2020年8月12日 Vertical Coal Mill (VCM) is equipment for grinding and pulverizing coal into micron size Rotary kilns then use the powders as fuel burnersAn investigation of performance characteristics and energetic 2012年5月1日 Sensors for coal flow measurement from the mill to the furnace have become available on the market (Blankinship, 2004, Department of Trade and Industry, 2001, Laux et al, 1999)Unfortunately the equipment tends to be expensive and requires frequent calibration; thus it cannot be used directly for control purposes at this time of writingDerivation and validation of a coal mill model for control
.jpg)
A Comparison of Three Types of Coal Pulverizers Babcock Power
The BTM is a lowspeed mill that primarily grinds coal by impact and attrition The VRM is a medium speed mill that grinds coal by compression and, because of the low coal inventory in the mill and flat grinding surfaces, develops shearing action as well For both mills a constant centrifugal force is maintained The speedThe pulverized coal is taken out of the mill by hot air Advantages Compared with the vertical roller mill, the advantages of airswept ball mill are strong adaptability to raw coal quality, simple operation and low investment cost; the disadvantages are high power consumption and high noise Vertical Roller Mill Vertical Roller Coal MillCoal Mill in Cement Plant Vertical Roller Mill AirSwept Ball Mill2020年8月12日 In a power plant, the coal mill is the critical equipment, whose effectiveness impacts the overall power plant efficiency Uniform coal feeding mass flow rate and required particle size and temperature at the outlet channel throughout with better classifier performance are crucial indicators that characterize the coal mill performanceAn investigation of performance characteristics and energetic Since the first application using an MPS mill to process pulverized coal in Germany in the mid 1960s, there have been over 2,000 different MPS mill installations operating in coalfired power plants worldwide As one of the most popular coal pulverizers in the utility industry, the MPS mill was first introduced into the US in the early 1970sCOAL PULVERIZER DESIGN UPGRADES TO MEET THE DEMANDS
.jpg)
Review of control and fault diagnosis methods applied to coal
2015年8月1日 Substantial savings, owing to reduced maintenance costs and production losses, can be achieved through fewer mill choking incidents, fewer mill runbacks, optimal mill operation, and rapid diagnoses of mill faults [5]Over the years, considerable research has been carried out for improving the operation of coal mills using better controls and diagnosing faults in mills at The Raymond® Bowl Mill is considered the finest vertical rollermill available for pulverizing coal Each bowl mill system is designed to achieve thebest solution forthe processing application The mill, feeder, classifier, fan, cyclone,dust Raymond® Bowl Mill Coperion2014年1月1日 Two mill systems are employed for most coal grinding applications in the cement industry These are, on the one hand, vertical roller mills (VRM) that have achieved a share of almost 90% and, on (PDF) MPS mills for coal grinding ResearchGateCoal grinding mills LOESCHE coal grinding mills are distinguished by characteristics that improve efficiency, (CG Group) of the advantages of its vertical roller mill technology LOESCHE has managed to gain a new Coal Mills for Cement Plants Loesche

Detection of Malfunctions and Abnormal Working Conditions of a Coal Mill
2018年5月2日 Coal mill malfunctions are some of the most common causes of failing to keep the power plant crucial operating parameters or even unplanned power plant shutdowns Therefore, an algorithm has been developed that enable online detection of abnormal conditions and malfunctions of an operating mill Based on calculated diagnostic signals and defined A Study on 500 MW Coal Fired Boiler Unit’s Bowl Mill Performance through Coal Sampling and Characterization: CPRI’s Experience M G Anandakumar* and M Venkateswara Rao Training Division, Central Power Research Institute, Bengaluru , Karnataka, India; mgananda@cpri ISSN (Print) : 09730338 Vol 18(2)/165170, December 2022A Study on 500 MW Coal Fired Boiler Unit’s Bowl Mill 2019年11月7日 Comprehensive treatment,we should have a test on the 300 MV unit steel ball coal mill pulverizing systemAt the same time,analyze the main operating parameters before modificationTransform the Optimization and transformation of 300MV units steel ball coal mill At best, coal mill safety is not well understood and, at worst, it is ignored When it comes to coal mill systems, most cement plant operators just presume that the supplier of the equipment knows all of the standards and rules and is 100% capable of making a system that conforms to these and is therefore safeIn discussion: Coal Mill Safety Coal Mill Safety, Explosion and
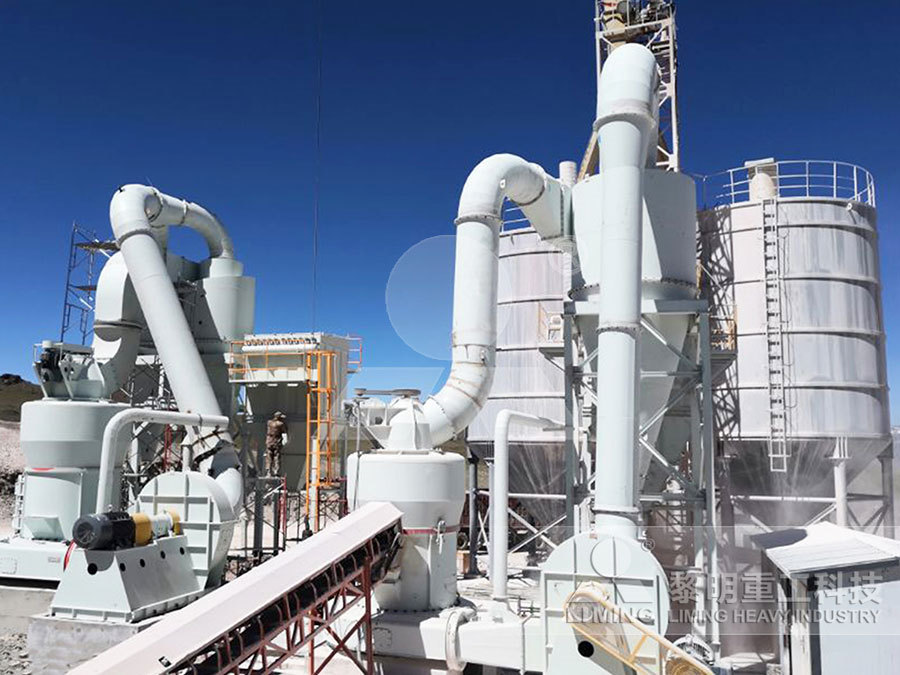
Vertical Coal Mill for Coal Grinding in Cement Plant Power Plant
Vertical coal grinding mill integrates crushing, drying, grinding, powder selection and conveying; It has simple system and compact structure Vertical coal mill covers an floor area about 50% of the coal ball mill with the same specification; Coal vertical mills can work in openair environments, greatly reducing the cost of investment The design of the vertical coal mill system is simple 2009年1月1日 This newlydeveloped coal mill model provides a valuable tool that can be used to improve the pulverizer design and optimize unit operation For example, reject coal rate, CFD Modeling of MPS Coal Mill for Improved Performance and SafetyThe coal vertical mill, also referred to as the vertical roller coal mill, is an advanced equipment developed by our company It combines modern technology with our extensive experience in powder manufacturing This coal pulverizer efficiently integrates coal grinding and drying, providing highperformance and energysaving featuresHighEfficiency Vertical Coal Mill Enhancing Coal Pulverization3 Precise Control and Automation: Bellian Machinery's coal mills feature advanced control systems that enable precise control over various operational parameters Operators can adjust grinding variables, such as coal flow and mill rotation speed, in realtime to achieve the desired coal fineness and optimize mill performanceCoal Mill in Thermal Power Plant: Enhancing Efficiency and
.jpg)
MPS mills for coal grinding AYS Engineering
2021年3月12日 So far, the biggest mill for lignite coal grinding will be delivered to Cemindo’s Bayah plant in Indonesia This MPS 4500 BK has been ordered for grinding lignite with a maximum moisture of 37% and it is able to produce a 2023年5月17日 coal hammer mill is a type of industrial equipment used to grind or pulverize coal into fine particles for combustion in furnaces or other industrial processes It is a machine that utilizes highspeed rotating hammers or blades to impact What Is Coal Hammer Mill? SBM Mill Crusher2021年3月31日 clean air curves • clean air curves plot covers mill differential versus stationary pitot differential with no coal flow • mill mtc requirement is based on increased coal spillage rate and running hours • clean air flow tests are being conducted on a shut unit only 31mar2021 total output power solutions 16Effect of Coal Quality and Performance of Coal pulverisers / MillsCoal mill hot air inlet temperatures should never be more than 600 ° F and the outlet temperature should not exceed 200°F on Raymond coal mills If the flow of raw coal to the coal mill is interrupted for any reason (for example: plugging, failure of the coal feeder, etc), the outlet temperature of the coal mill can quickly climb to coal feeders and coal mill Capabuild
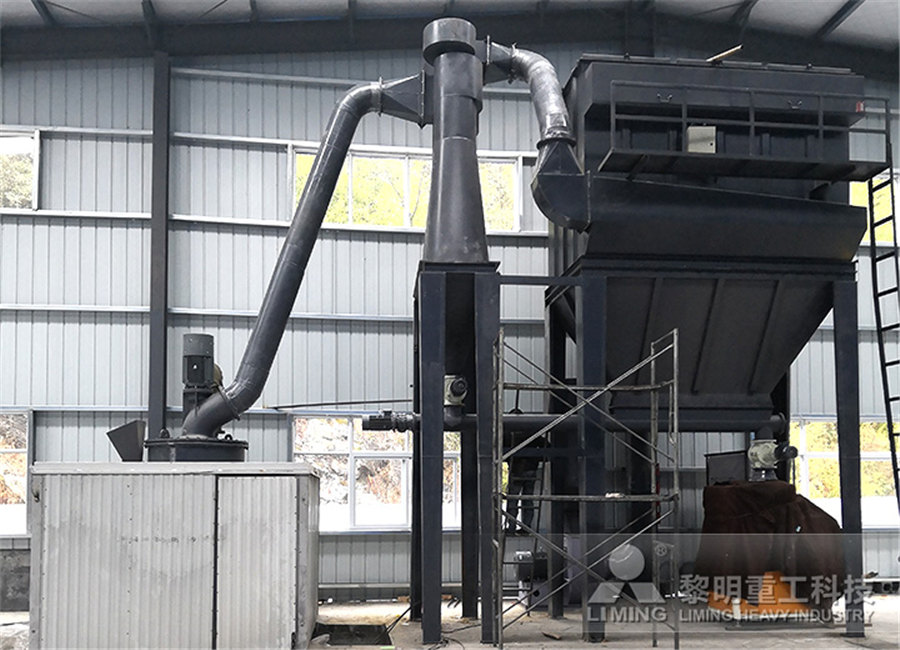
A unified thermomechanical model for coal mill operation
2015年11月1日 As presented by Andersen et al (2009) and Odgaard, Stoustrup, and Mataji (2007), coal moisture imposes limit on the maximum load at which a coal mill can be operated and the load gradient (how fast the mill may change its operating point), if it is desired that the pulverized coal entering the furnace has moisture content less than or equal to a certain value GC: What led you to establish Coal Mill Safety? VG: I established Coal Mill Safety (CMS) as a consultancy after I ‘retired’ in 2011 If a cement producer wants to install a new coal grinding system, they can commission CMS to look at the supplier’s design and probe it from a safety angle If it has an existingIn discussion: Vincent Grosskopf, Coal Mill Safety2024年3月3日 ignition permit for mill prior to start any mill the mill ignition energy must be adequate to support coal firing ignition permit for mill –a minimum 3 out of 4 honvs of elev ab open or mill b in service with >50% loading and boiler load is > 30%coal mill Feedercoal mill Feeder1 (2)ppt Free Download2021年8月1日 Yukio et al [7] proposed a model consisting of blending, grinding and classifying processes for pulverizer control Agarawal et al [8] differentiated coal powder into ten size groups, divided the bowl mill into four zones, and developed a unified model Palizban et al [9] derived nonlinear differential mass equations of raw coal, recirculation coal and suspension coal in Coal mill model considering heat transfer effect on mass
.jpg)
Pulveriser in Thermal Power Plant Bowl Mill Ball Mill
In bowl mill pulveriser raw coal coming from feeder gets ground between the grinding rolls and bull ring segments installed on the revolving Bowl Bowl is made to rotate at medium speed for proper pulverization of coal Springs exert Coal mills, essential components in power generation and various industrial processes, pose significant safety risks if not properly managed These mills, used to grind coal into a fine powder for combustion, present potential hazards such as fire, explosion, and mechanical failures This article outlines best practices and precautions to ensure thBest Practices and Precautions Coal Mill Safety, Explosion and Coal grinding mills are essential components of power plants, responsible for converting raw coal into fine coal powder that is essential for efficient combustion in power plant boilers Coal grinding mills can also be used to grind biomass and other alternative fuels, providing a more sustainable and renewable energy source for power generationWhat is a Coal Grinding Mill2020年8月12日 Vertical Coal Mill (VCM) is equipment for grinding and pulverizing coal into micron size Rotary kilns then use the powders as fuel burnersAn investigation of performance characteristics and energetic
.jpg)
Derivation and validation of a coal mill model for control
2012年5月1日 Sensors for coal flow measurement from the mill to the furnace have become available on the market (Blankinship, 2004, Department of Trade and Industry, 2001, Laux et al, 1999)Unfortunately the equipment tends to be expensive and requires frequent calibration; thus it cannot be used directly for control purposes at this time of writingThe BTM is a lowspeed mill that primarily grinds coal by impact and attrition The VRM is a medium speed mill that grinds coal by compression and, because of the low coal inventory in the mill and flat grinding surfaces, develops shearing action as well For both mills a constant centrifugal force is maintained The speedA Comparison of Three Types of Coal Pulverizers Babcock PowerThe pulverized coal is taken out of the mill by hot air Advantages Compared with the vertical roller mill, the advantages of airswept ball mill are strong adaptability to raw coal quality, simple operation and low investment cost; the disadvantages are high power consumption and high noise Vertical Roller Mill Vertical Roller Coal MillCoal Mill in Cement Plant Vertical Roller Mill AirSwept Ball Mill2020年8月12日 In a power plant, the coal mill is the critical equipment, whose effectiveness impacts the overall power plant efficiency Uniform coal feeding mass flow rate and required particle size and temperature at the outlet channel throughout with better classifier performance are crucial indicators that characterize the coal mill performanceAn investigation of performance characteristics and energetic
.jpg)
COAL PULVERIZER DESIGN UPGRADES TO MEET THE DEMANDS
Since the first application using an MPS mill to process pulverized coal in Germany in the mid 1960s, there have been over 2,000 different MPS mill installations operating in coalfired power plants worldwide As one of the most popular coal pulverizers in the utility industry, the MPS mill was first introduced into the US in the early 1970s2015年8月1日 Substantial savings, owing to reduced maintenance costs and production losses, can be achieved through fewer mill choking incidents, fewer mill runbacks, optimal mill operation, and rapid diagnoses of mill faults [5]Over the years, considerable research has been carried out for improving the operation of coal mills using better controls and diagnosing faults in mills at Review of control and fault diagnosis methods applied to coal