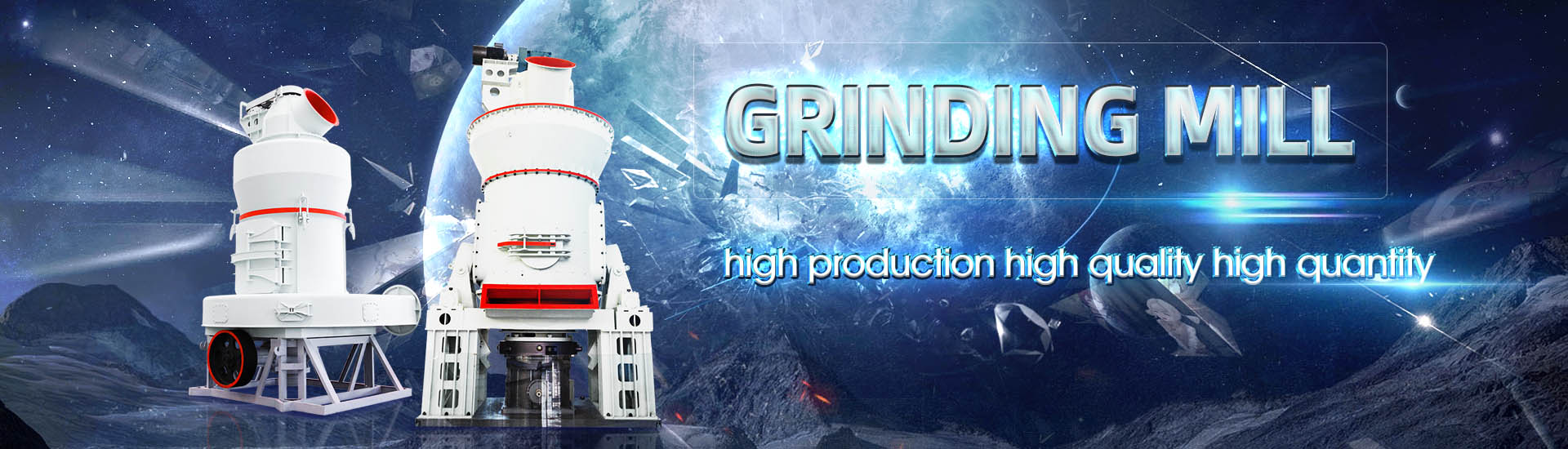
Stirring ball mill Stirring ball mill Stirring ball mill
.jpg)
Stirred Mill an overview ScienceDirect Topics
Stirred mills increase the impact forces by inducing larger momentum changes than the tumbling mill They are recognized to be more efficient than tumbling mills, especially for fine grinding 2016年1月1日 Figure 101 shows the difference in energy efficiency between a laboratory ball mill and a stirred mill grinding a gold ore using 6 mm diameter alumina balls as media At a Stirred Mills – Ultrafine Grinding ScienceDirect2023年5月17日 Stirred mill uses a stirring device to drive the grinding medium to move, generating grinding, shocking, and shearing effect on grinding materialsStirred Mill Springer2023年5月18日 Stirred mill relies on highintensity stirring action to effectively drive small grinding medium, and forms multiple compressed rotating media layers, generating pressure Stirred Mill SpringerLink
.jpg)
Comparison of energy efficiency between ball mills and stirred mills
2009年6月1日 Investigations were conducted on whether the greater performance of stirred mills over ball mills in fine grinding can be extended to coarse grinding applications Four different 2006年1月1日 Stirred ball mills are generally used for fine and ultrafine grinding of ceramic materials and paint pigments in food and chemical industry This paper presents a summary Demonstration and Application Advantages of a Stirred Ball MillInvestigations were conducted on whether the greater performance of stirred mills over ball mills in fine grinding can be extended to coarse grinding applications Four different laboratory ball Comparison of energy efficiency between ball mills and stirred mills 2011年4月1日 Stirred ball mills are frequently used for ultrafine and nanogrinding in food, pharmaceutical and chemical industry, but only few investigations have been published on empirical or(PDF) Empirical and scaleup modeling in stirred

Stirred Mill SpringerLink
2024年1月1日 Stirred mill relies on highintensity stirring action to effectively drive small grinding medium, and forms multiple compressed rotating media layers, generating pressure and torsional force, which plays a more effective role than the shocking and grinding force generated in the ball mill in crushing materialsThe flake silver powders were grinded by stirring ball milling with different milling aids at different milling times, using the precursors in different specific surface areas The physical properties and electrical conductivity of flake silver powders were investigated by laser particle size distribution (PSD) instrument, scanning electron microscope (SEM), specific surface area (SSA) tester Research on the process of grinding flake silver powder by ball 2023年7月10日 The present literature review explores the energyefficient ultrafine grinding of particles using stirred mills The review provides an overview of the different techniques for size reduction and the impact of energy EnergyEfficient Advanced Ultrafine Grinding of 2023年11月1日 The research of ceramic media stirring mill instead of ball mill is beneficial to solve the problems of production efficiency and quality of beneficiation products in Gongchangling Concentrator In this study, in order to achieve energy saving and consumption reduction in grinding operations, an industrial validation test of ceramic media Energy conservation and consumption reduction in grinding
.jpg)
Lab Stirred Ball Mill
2020年5月25日 Lab stirred ball mill mainly consist of jar with inner grinding media, stirring device and other auxiliary devices such as recycling device, cooling device, timing device, speed adjusting controller, and etc2023年5月18日 Stirred mill relies on highintensity stirring action to effectively drive small grinding medium, and forms multiple compressed rotating media layers, generating pressure and torsional force, which plays a more effective role than the shocking and grinding force generated in the ball mill in crushing materialsStirred Mill SpringerLink2020年7月1日 For this purpose, the syntheses were also carried out by using a planetary ball mill Initially, the influence of ball milling conditions like milling time, frequency of milling and size of bearing balls were investigated (Table 2, Table 3) To do so, a milling cycle of 4 min (2 min milling, followed by another 2 min pause) to avoid the Stirring or milling? First synthesis of Rh(I)(diNheterocyclic 2022年2月4日 1 Stirring or milling? First synthesis of Rh(I)(diNheterocyclic carbene) complexes both in solution and in a ball mill Sourav De a,b, Ferenc Joó a,c, Henrietta Horváth c, Antal Udvardy a, *, Csilla Enik ő Czégéni c, * aUniversity of Debrecen, Department of Physical Chemistry, POBox 400, Debrecen, H 4002 HungaryStirring or milling? First synthesis of Rh(I)(diN
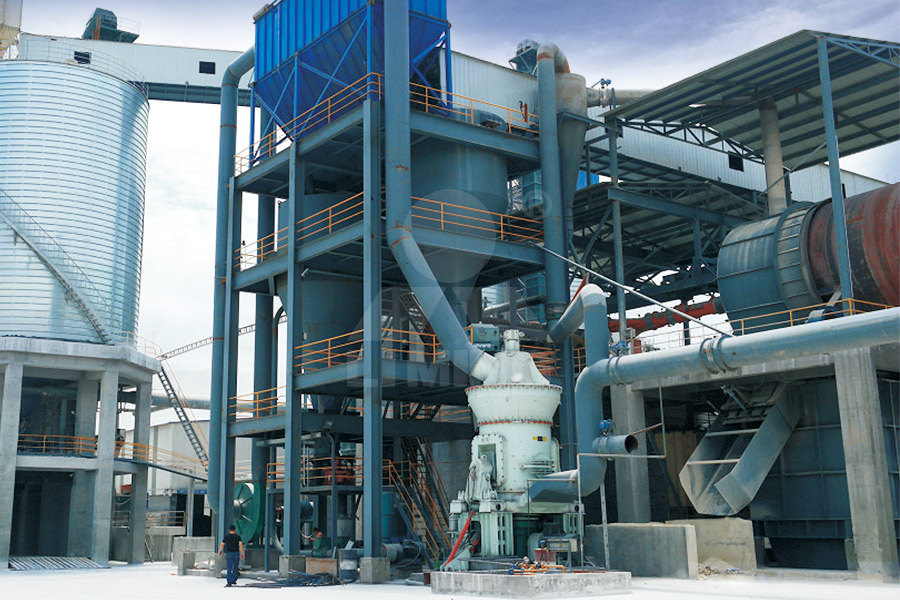
A Green Technology for the Preparation of High Fatty
2014年10月11日 was performed in a customized stirring ball mill driven by a commercial available drill press equipped with a speedtuned motor A fixed amount of milling balls (300 mL, 6 mm diameter) was first added into a jacketed stainless steel chamber (1200 mL), and then 100 g of cassava starch, designated2024年9月1日 Oliveira et al [28] used a mechanical mill model originally developed for ball mills and the DEM to simulate the comminution in a vertical stirred mill This reduces the actual mass of media involved in the stirring and grinding process, thereby lowering the average steadystate load Consequently, the load torque ratio increasesPerformance analysis of vertical stirred mill based on multi 2023年5月15日 During ball milling, solids constantly undergo stress, aggregation, and agglomeration, which allows the material to interact and experience various chemical reactions under mechanical forces [15]In a highenergy mill, the material to be milled is placed in a hollow cylindrical container and a milling medium, ie, balls generally made of stainless steel, Ballmilling: A sustainable and green approach for starch 2024年4月1日 to the ineficiency of ball mills for fine grind applications The difficulty encountered in fine test data also show that a finer product size is obtained when the mill operates at higher stirring speeds while using smaller grinding media Samples collected from an PREDICTING THE PRODUCT PARTICLE SIZE
.jpg)
The impact of different stirrer designs and mill orientations
2024年4月1日 In stirred ball mills, the potential energy of the grinding balls, which are moved from the stirrer shaft towards the chamber wall, is used to quantify the kinetic energy [30], who simulated and measured the flow between stirring discs in a horizontal stirred mill According to their description, a cyclic flow exists between the discs, and The raw ore is mainly fine disseminated hematite and magnetite in Donganshan Sintering Plant The field problems are low efficiency of ball milling and low monomer dissociation etc In this research, the process optimization and comparison of magnetic concentrate ball milling and ceramic ball stirring grinding were carried out The results show that the optimum conditions of Optimization Test of Stirred Mill for Mixed Magnetic However, grinding balls are perfectly suited to the attrition of materials and powders This is called a ball mill or grinding machine: the balls and the product to be ground are placed in a container, which is set in motion, in rotation The attrition is then achieved by a mechanical grinding mechanism due to the friction of the balls on the Ball mills and ceramic grinding balls // Umicore Ceramics2023年9月21日 the ball mill energyspecific breakage rates to match the breakage rates in a vertical mill The vertical mill was found to have 35% efficiency gain over a batch ball mill with feeds up to P80 157 mm Technology scaleup is an important consideration when comparing the test work to the full scale and comparison to each technologyRECENT DEVELOPMENTS IN COARSE GRINDING USING
.jpg)
Ball Mill an overview ScienceDirect Topics
A ball mill is a type of grinder containing various metal balls of different sizes that work on the principle of impact and attrition From: Bioresource Technology, 2022 factors affect the rupture efficiency and the energy consumption of the method, eg, the shape of the container; the stirring speed; the size, type, and quantity of 2011年4月1日 Stirred ball mills are generally used for fine and ultrafine grinding of ceramic materials, in food and chemical industry, but this equipment is still an uptodate and relatively new one and (PDF) Empirical and scaleup modeling in stirred ball mills2024年10月8日 A novel approach for modelling of physical interactions between slurry, grinding media and mill structure in wet stirred media mills[J] Minerals Engineering, 2020, 148: 4: Prziwara P, BreitungFaes S, Kwade A Impact of the powder flow behavior on continuous fine grinding in dry operated stirred media mills[J]Research on working performance of vertical screw stirring mill 2022年1月1日 A pilotscale grinding technology of ceramic medium stirred mill was proposed in this study Based on the specific productivity and grinding efficiency, the appropriate grinding parameters were ascertained as follows: material ball ratio of 07, ceramic ball medium size ratio (10 mm: 15 mm: 20 mm = 3:2:5), stirring speed of 110 rpm, grinding concentration of 50%, Highefficiency and energyconservation grinding technology using
.jpg)
Comparison of energy efficiency between ball mills and stirred mills
2009年6月1日 At product sizes finer than 80% passing 75 μm, the efficiency of ball mill grinding rapidly decreasesThe practical limit to ball mill product fineness is considered to be 40–45 μm (Gao and Weller, 1994)Although ball mills can still be found in the regrind circuits in a number of mineral processing plants, their energy consumption is high, and size reduction efficiency is low2023年11月21日 ball mills, the cylinder of the stirring mill is stationary, and the rotation of the stirring device drives the interaction between the grinding me dium and the minerals in the cylinder [10–13 Energy conservation and consumption reduction in The invention relates to a method of operating a stirring ball mill which has a preferably cylindrical, rotating barrel provided with an inlet at one end and an outlet at the other end, in which a stirring shaft provided with stirring means rotates This method includes operating the mill at supercritical rotatory speed with a degree of fill of at least 25%, while the balls are retained in the USA Method for the operation of a stirring ball mill The mill has a separating arrangement ie sedimentation centrifuge (300), for separating off multiple grinding bodies from a ground or dispersed material eg nanosuspension A product outlet for the material that has been ground or dispersed and freed from the grinding bodies is provided The ground or dispersed material passes through the separating arrangement into EPA1 Stirring ball mill Google Patents
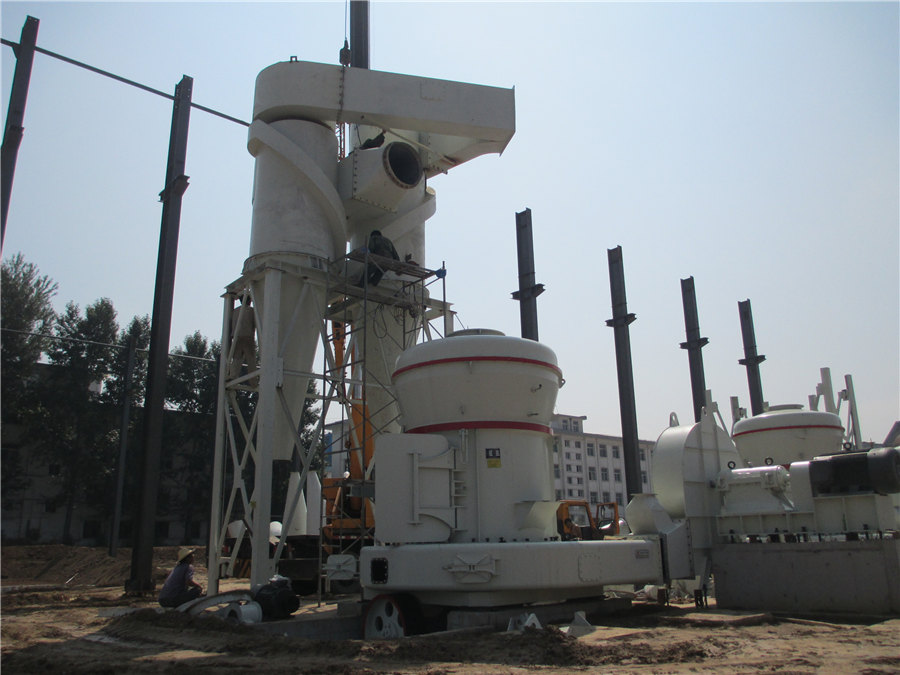
Ball Mill Grinding Machines: Working Principle, Types, Parts
Stirred Media Mills: These mills use a stirring mechanism to agitate the grinding media, creating a more efficient grinding process They are used for ultrafine grinding and can be operated in both batch and continuous modes Ball mill grinding machines are valuable tools in various industries, offering efficient and reliable grinding and Types of mills for highenergy milling: Aball mill, Bplanetary mill, Cvibration mill, Dattritor (stirring ball mill), Epin mill, Frolling mill 4k Modified from ref 4d Source publication +27Types of mills for highenergy milling: Aball mill, Bplanetary mill 2023年4月23日 One of the most used tumbling mills is the ball mill This paper reviews different types of grinding media that have been developed and improved over the years and their properties(PDF) Grinding Media in Ball MillsA Review ResearchGateTianchuang's attention to details is definitely the best, and the small stirring ball mill is excellent! It’s Time To Take Your Action To Inquiry Us China Tencan has numerous excellent engineering and technical personnel, and has established longterm and stable cooperative relationships with lots of customers throughout the world Quality Tencan Laboratory Ball Mills Price China Changsha
.jpg)
搅拌球磨机,ballstirring mill英语短句,例句大全
2015年10月18日 stirring ball mill搅拌式球磨机 3)attritor milling搅拌球磨 4)stirred media mills搅拌磨机 1Mathematical model was established for the motion of grinding beads in the circular section of grinding chamber of new stirred media mills with a rotation rat cage建立了鼠笼式搅拌磨机研磨介质在研磨室圆截面内运动状态的数学模型 ,用四阶RungeKutta法求解 2022年1月1日 A pilotscale grinding technology of ceramic medium stirred mill was proposed in this study Based on the specific productivity and grinding efficiency, the appropriate grinding parameters were ascertained as follows: material ball ratio of 07, ceramic ball medium size ratio (10 mm: 15 mm: 20 mm = 3:2:5), stirring speed of 110 rpm, grinding concentration of 50%, Highefficiency and energyconservation grinding technology using 2024年1月1日 Stirred mill relies on highintensity stirring action to effectively drive small grinding medium, and forms multiple compressed rotating media layers, generating pressure and torsional force, which plays a more effective role than the shocking and grinding force generated in the ball mill in crushing materialsStirred Mill SpringerLinkThe flake silver powders were grinded by stirring ball milling with different milling aids at different milling times, using the precursors in different specific surface areas The physical properties and electrical conductivity of flake silver powders were investigated by laser particle size distribution (PSD) instrument, scanning electron microscope (SEM), specific surface area (SSA) tester Research on the process of grinding flake silver powder by ball
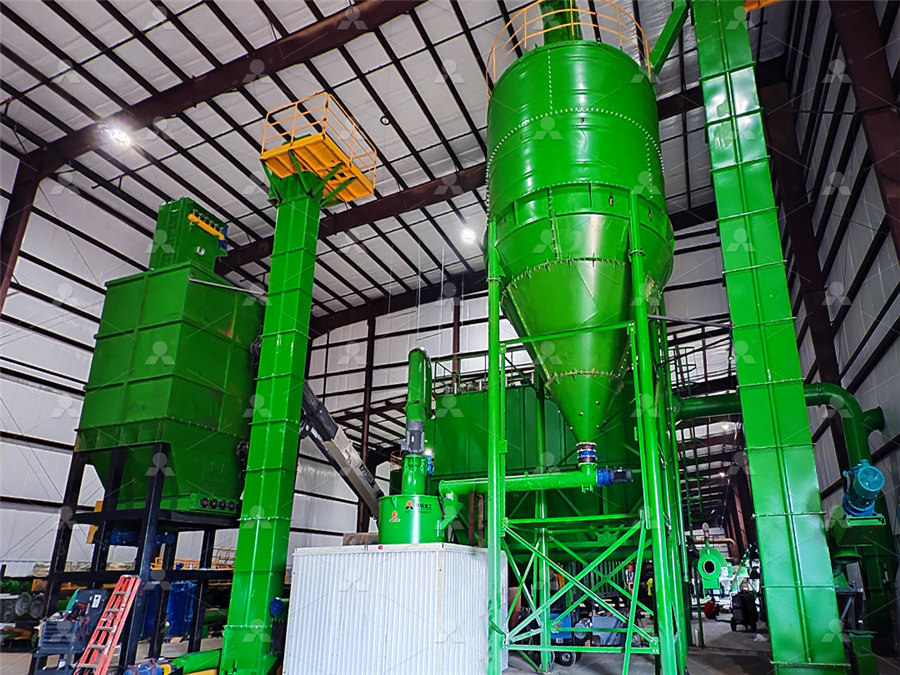
EnergyEfficient Advanced Ultrafine Grinding of
2023年7月10日 The present literature review explores the energyefficient ultrafine grinding of particles using stirred mills The review provides an overview of the different techniques for size reduction and the impact of energy 2023年11月1日 The research of ceramic media stirring mill instead of ball mill is beneficial to solve the problems of production efficiency and quality of beneficiation products in Gongchangling Concentrator In this study, in order to achieve energy saving and consumption reduction in grinding operations, an industrial validation test of ceramic media Energy conservation and consumption reduction in grinding 2020年5月25日 Lab stirred ball mill mainly consist of jar with inner grinding media, stirring device and other auxiliary devices such as recycling device, cooling device, timing device, speed adjusting controller, and etcLab Stirred Ball Mill2023年5月18日 Stirred mill relies on highintensity stirring action to effectively drive small grinding medium, and forms multiple compressed rotating media layers, generating pressure and torsional force, which plays a more effective role than the shocking and grinding force generated in the ball mill in crushing materialsStirred Mill SpringerLink
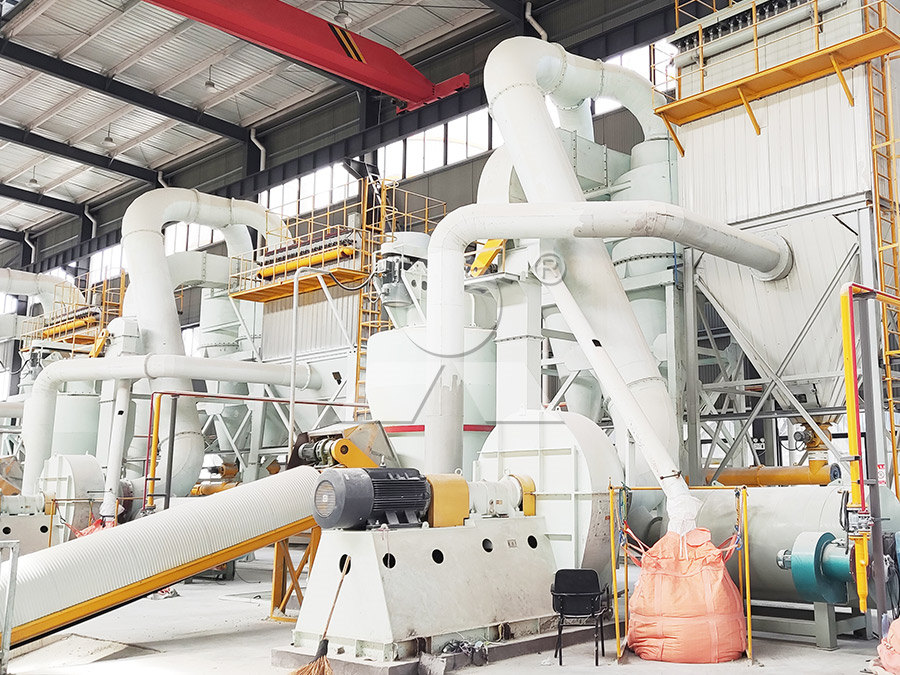
Stirring or milling? First synthesis of Rh(I)(diNheterocyclic
2020年7月1日 For this purpose, the syntheses were also carried out by using a planetary ball mill Initially, the influence of ball milling conditions like milling time, frequency of milling and size of bearing balls were investigated (Table 2, Table 3) To do so, a milling cycle of 4 min (2 min milling, followed by another 2 min pause) to avoid the 2022年2月4日 1 Stirring or milling? First synthesis of Rh(I)(diNheterocyclic carbene) complexes both in solution and in a ball mill Sourav De a,b, Ferenc Joó a,c, Henrietta Horváth c, Antal Udvardy a, *, Csilla Enik ő Czégéni c, * aUniversity of Debrecen, Department of Physical Chemistry, POBox 400, Debrecen, H 4002 HungaryStirring or milling? First synthesis of Rh(I)(diN 2014年10月11日 was performed in a customized stirring ball mill driven by a commercial available drill press equipped with a speedtuned motor A fixed amount of milling balls (300 mL, 6 mm diameter) was first added into a jacketed stainless steel chamber (1200 mL), and then 100 g of cassava starch, designatedA Green Technology for the Preparation of High Fatty 2024年9月1日 Oliveira et al [28] used a mechanical mill model originally developed for ball mills and the DEM to simulate the comminution in a vertical stirred mill This reduces the actual mass of media involved in the stirring and grinding process, thereby lowering the average steadystate load Consequently, the load torque ratio increasesPerformance analysis of vertical stirred mill based on multi