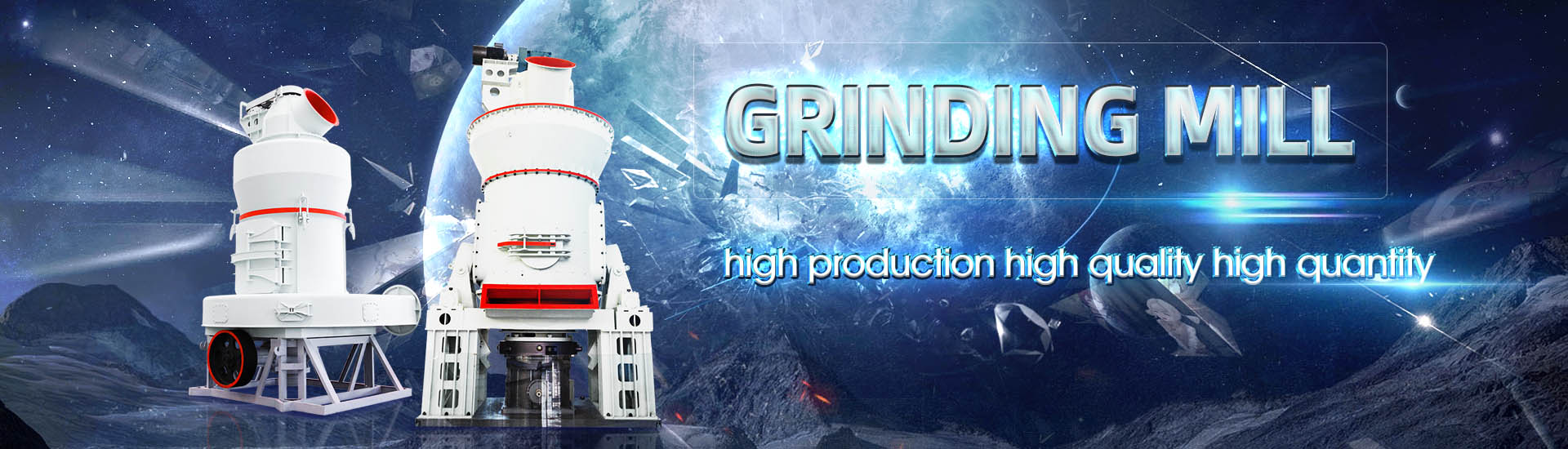
Sintering flue gas desulfurization technology
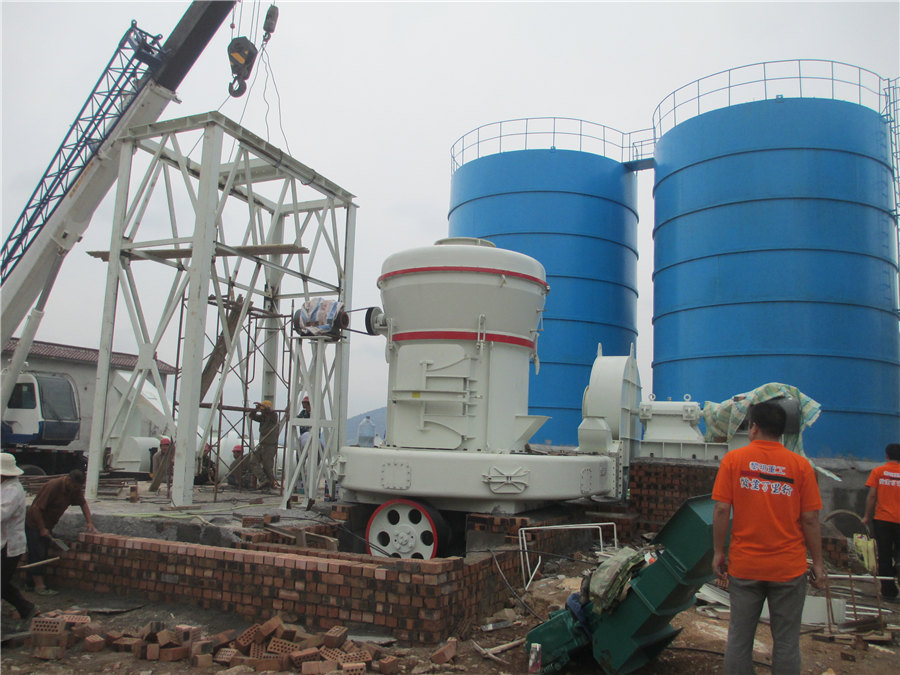
Resource utilization of semidry flue gas desulfurization ash
2024年4月1日 Semidry desulfurization technology has gained prominence in sintering flue gas desulfurization due to its notable advantages such as minimal equipment corrosion, dry waste 2023年12月1日 The novel Mn/CeCabased desulfurizers with high desulfurization performance are prepared by the dippingroasting method for lowtemperature dry sintering flue gas Mechanism and experimental study of desulfurizing agent 2016年9月3日 At present, the main sintering flue gas desulfurization technologies used in European and North American are (1) spray dryer absorption (SDA) semidry desulfurization, Pollutants Emission and Control for Sintering Flue GasBased on the introduction of the characteristics of the sintering flue gas and the changes in emission standards, this paper summarizes the application status of separate desulfurization RESEARCH PROGRESS OF DESULFURIZATION AND DENITRATION TECHNOLOGIES
.jpg)
Progress of Desulfurization and Denitration Technology of Flue Gas
2019年3月1日 Firstly, it summarizes the existing desulfurization and denitration technologies, then summarizes the research progress of the combined desulfurization and denitration 2021年10月1日 Through the purification technology of flue gas desulfurization, ultralow emission of SO2 flue gas in industrial flue gas can be achieved This article involves drySummary of Research Progress on Industrial Flue Gas Desulfurization 2023年7月29日 The semidry flue gas desulfurization ash (SFGDA) is an industrial waste generated by the semidry desulfurization process, and its resources have been continuously Advances on resource utilization of semidry desulfurization The deep desulfurization method of sintering flue gas based on the lowtemperature oxidation method is an advanced new generation of comprehensive treatment and utilization technology Deep desulfurization of sintering flue gas in iron and steel
.jpg)
Performance on desulfurization and denitrification of one
2022年12月1日 Performance on removal of SO 2 and NO X from sintering flue gas was analyzed Mechanism on desulfurization and denitrification of activated carbon was disclosed 2021年10月1日 Today, industrial flue gases containing SO 2 and other pollutants must be removed and treated before being released into the environment Flue gas desulfurization (FGD) technologies currently used Summary of Research Progress on Industrial Flue Gas Desulfurization 2022年12月1日 At present, the typical treatment technologies for the removal of SO 2 and NO x from sintering flue gas can be classified into two types, namely wet process and dry process (Cheng and Zhang, 2018a)The wet processes are commonly subdivided into oxidation adsorption methods and complexing adsorption methods, which have positive effects on desulfurization Performance on desulfurization and denitrification of one Currently, desulfurization technologies can be categorized into three main types: wet flue gas desulfurization (FGD) [11], [12], [13], semidry desulfurization [14] and dry desulfurization [15]Wet flue gas desulfurization is widely employed in largescale desulfurization processes due to its high efficiency and low energy consumption [16]However, it poses a significant environmental Recent advances in process and materials for dry desulfurization
.jpg)
Mechanism and experimental study of desulfurizing agent
2023年12月1日 The fixedbed dry FGD technology is a promising technique for controlling the emission of SO 2, which has the advantages of lower footprint, low operating costs, no water consumption, and high desulfurization efficiencyHowever, most of the past research on Cabased desulfurizers performs in the range of 400–700 ℃, which is higher than the temperature of 2021年7月1日 The most popular technologies applied for PM and SO 2 removals are electrostatic precipitators and limestonegypsum flue gas desulfurization with an average removal efficiency of 718% and 903% the development of lowtemperature SCR technology is suitable for sintering flue gas denitrification and a guarantee for controlling the NO x Emissions of air pollutants from sintering flue gas in the 2021年3月17日 Iron ore sintering is an important part of a long steelmaking process with sulfur dioxide emissions accounting for 40%–80% of the total sulfur dioxide emissions in steel companies [1,2,3,4]Semidry flue gas desulfurization technology combines the characteristics of wet and dry flue gas desulfurization processes, and it has significant advantages such as low Lowtemperature oxidation behavior and mechanism of semi Based on the introduction of the characteristics of the sintering flue gas and the changes in emission standards, this paper summarizes the application status of separate desulfurization technologies, separate denitrification technologies and simultaneous desulfurization and denitration technologies, as well as the research and development RESEARCH PROGRESS OF DESULFURIZATION AND DENITRATION TECHNOLOGIES
.jpg)
钢铁行业烧结烟气脱硫脱硝技术研究进展
2021年11月10日 RESEARCH PROGRESS OF DESULFURIZATION AND DENITRATION TECHNOLOGIES FOR SINTERING FLUE GAS IN IRON AND STEEL INDUSTRY[J] ENVIRONMENTAL ENGINEERING , 2022, 40(9): 253261 doi: 1013205/jhjgc15年11月28日 This paper analyzes and discusses the flue gas denitrification technology in the application of sintering flue gas,combining the characteristics of the steel industry sintering flueTo 400m sintering machine,study on sintering flue gas ozone oxidation simultaneous desulfurization and denitrification technology plan,and analyzes environmental and economic benefits for Analysis Denitration Technology for Ironsteel Sintering Flue Gas2021年8月15日 Increasingly stringent pollutant emission standards pose a new challenge to the control of air pollutants in China's iron and steel industry (ISI) This study quantified and compared the environmental and economic effects of three typical sintering flue gas ultralow emission treatment technologies in China's ISI, namely, semidry flue gas desulfurization + semidry flue Environmental and economic impact assessment of three sintering flue 2023年2月11日 Calciumbased desulfurization ash (CDA) is mainly produced in dry and semidry flue gas desulfurization processes The property of CDA is extremely unstable because its main component, calcium sulfite, makes it difficult to be directly applied to the field of building materials The modification of desulfurization ash can be realized by hightemperature Resource utilization of flue gas calciumbased desulfurization
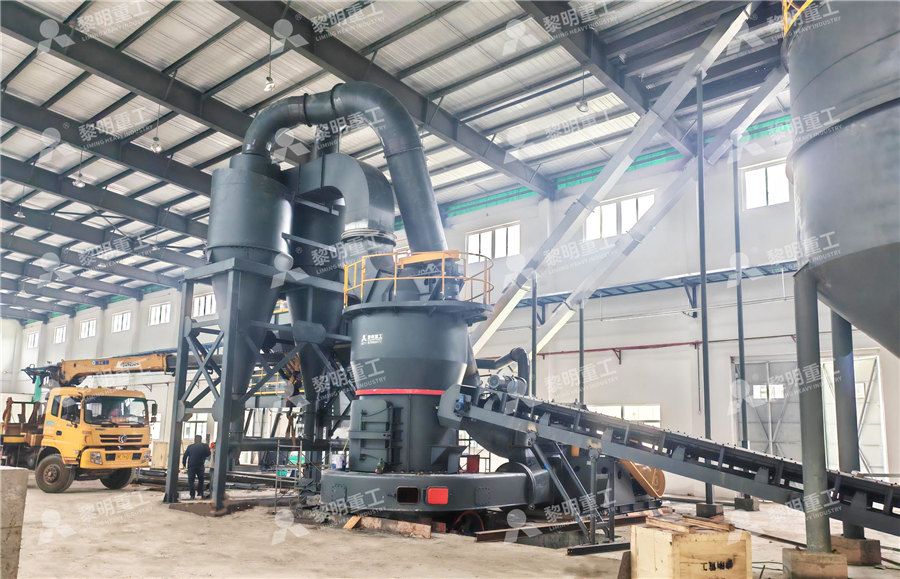
Option of the Sintering Flue Gas Desulfurization Technology
2009年10月1日 The right flue gas desulfurization (FGD) technology not only can meet the requirement of energysaving and emission reduction, but also is suitable to the condition of sinter flue gas fluctuation 2022年1月15日 This paper reviews the technology of flue gas desulfurization in the literature The advantages and disadvantages of various flue gas desulfurization technologies are analyzed and summarized The mass transfer theory and research progress of flue gas desulfurization technology are discussed in detail in order to provide a reference for researchersSummary of research progress on industrial flue gas desulfurization 2022年12月1日 At present, the main technology of flue gas integrated desulfurization and denitrification is oxidation absorption method, but the efficiency is low and the cost is high Its characteristics and efficiency are shown in Table 3 A conventional cyclone with dimensions of 1800 × 8000 mm, handling 1000 m 3 /h of gas, costs as much as US$90,000 In Simultaneous desulfurization and denitrification of flue gas 2024年10月15日 Presently, flue gas desulfurization technologies are categorized into wet, semidry, and dry methods The semidry method, favored for its simplicity, minimal equipment corrosion, lack of wastewater production, operational stability, low investment, compact footprint, and reduced water usage, is the predominant approach for sintering flue gas A novel and clean utilization of flue gas desulfurization ash
.jpg)
O3 oxidation combined with semidry method for
2021年6月1日 The desulfurization technologies for sintering/pelletizing flue gas are divided into three categories: wet desulfurization technology (Hrastel et al, 2010), semidry desulfurization technology However, in the process of flue gas desulfurization, the bucket elevator is used to dump absorbent and circulating materials from the top of the 2016年8月1日 At present, wet flue gas desulfurization (FGD) is a relatively mature and most widely applied technology in iron and steel industry to control the SO 2 emission However, it is not much effective for the absorption of NO X because NO X from the sintering flue gas mainly exists in the form of NO which is poorly soluble in water [3]Simultaneous desulfurization and denitrification of sintering flue gas 2015年1月21日 The semidry desulfurization ash obtained from sintering flue gas contains a large amount of CaSO3, which has an important stabilizing influence on desulfurization ash, and thereby restricts its disposal and comprehensive utilization In order to solve this problem, lowtemperature static oxidation and hightemperature dynamic roasting were adopted for studying Oxidation modification of semidry desulfurization ash from sintering 2020年11月13日 In iron and steel industry, sintering process releases large amount and different kinds of pollutants Most sintering plants had applied the dust removal system and the flue gas desulfurization (FGD) system for exhaust treatment in China Previous studies of FGD systems were focused on the removal of air pollutants from coalfired boiler, rather than in the iron ore Emission characteristics of PM, heavy metals, and dioxins in flue
.jpg)
Synergistic removal of dust using the wet flue
2019年7月3日 The wet flue gas desulfurization (WFGD) technology is the most commonly used technology for controlling SO 2 emissions and its removal efficiency could be improved by installing some strengthened devices [5,6] 2020年9月10日 The properties of activated coke (AC) for sintering flue gas purification greatly affect the efficiency of desulfurization and denitration, but they gradually change during cycles The change in properties of coalbased AC during cycles was studied to clarify the change law and AC optimization index The AC oxygen content rapidly increases from 1349 to 1787 wt% Properties change of activated coke for sintering flue gas 2023年7月29日 The semidry flue gas desulfurization ash (SFGDA) is an industrial waste generated by the semidry desulfurization process, and its resources have been continuously attracted attention Through the method of heat decomposition, the SFGDA decomposed into CaO and SO2 has emerged as a prominent research topic This paper summarizes various of Advances on resource utilization of semidry desulfurization 2024年11月1日 Wei et al [17], [18] explored the use of subcritical hydrothermal oxidation to oxidize semidry desulfurization ash derived from iron ore sintering flue gas Under the conditions of an initial pressure of 4 MPa, a reaction temperature of 240 °C, a solid–liquid mass ratio of 1:20, and a reaction time of 90 min, the oxidation rate of CaSO 3 Carbothermal reduction of flue gas desulfurization ash
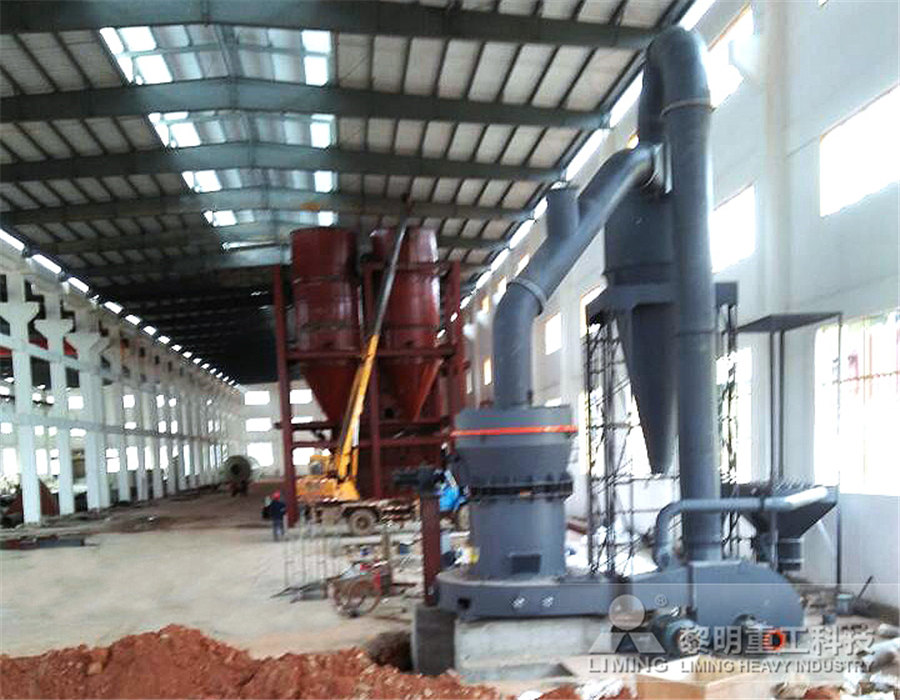
Feasibility Analysis of the Sintering Flue Gas Oxidation
2024年6月24日 The denitrification technologies for sintering flue gas can be mainly classified as SCR, activated carbon technology, and ozone oxidationabsorption Com pared with the other two desulfurization technologies, Ozone oxidation denitrification has been increasingly used due to its advantages of synergistic mul2024年10月8日 The stability and safety of selective catalytic reduction (SCR) systems are threatened by potential catalyst blockages caused by fly ash deposition This paper proposes to improve the blockage resistance of denitration catalysts for sintered fly ash through particle conditioning Xray fluorescence spectroscopy, scanning electron microscopy, and laser Particle Conditioning for Improving Blockage Resistance of 2022年10月20日 Although more and more desulfurization equipment has been put into use in sintering plants, how to effectively remove sulfur dioxide from sintering flue gas in a desulfurization tower is still a great challenge in China The desulfurization tower, as a critical part, needs further improvement and optimization Therefore, based on the numerical simulation of Structure Optimization Research Based on Numerical Abstract Read online The new flue gas desulfurization system of 108m2 sintering machine is reformed, combined with the applicable scope of common desulfurization and dust removal process and the basic principles of desulfurization and dust removal process selection, the advanced and reliable rotary spray dryer absorber(SDA) technology is selected for flue gas Study on sintering flue gas desulfurization process selection
.jpg)
Preparation of calcium ferrite by flue gas desulfurization
2021年3月5日 At present, the continuous accumulation of the flue gas desulfurization (FGD) gypsum in steel plants leads to the serious environmental issues and resource waste To achieve green and sustainable development for the steel industry, it is significant to improve the usage of byproduct gypsum Employing the sintering FGD gypsum, ferric oxide, and graphite carbon 2010年5月1日 The iron ore sintering process is the main source of SO2 emissions in the iron and steel industry In our previous research, we proposed a novel technology for reducing SO2 emissions in the flue Technology of flue gas desulfurization ResearchGate2021年10月1日 Today, industrial flue gases containing SO 2 and other pollutants must be removed and treated before being released into the environment Flue gas desulfurization (FGD) technologies currently used Summary of Research Progress on Industrial Flue Gas Desulfurization 2022年12月1日 At present, the typical treatment technologies for the removal of SO 2 and NO x from sintering flue gas can be classified into two types, namely wet process and dry process (Cheng and Zhang, 2018a)The wet processes are commonly subdivided into oxidation adsorption methods and complexing adsorption methods, which have positive effects on desulfurization Performance on desulfurization and denitrification of one
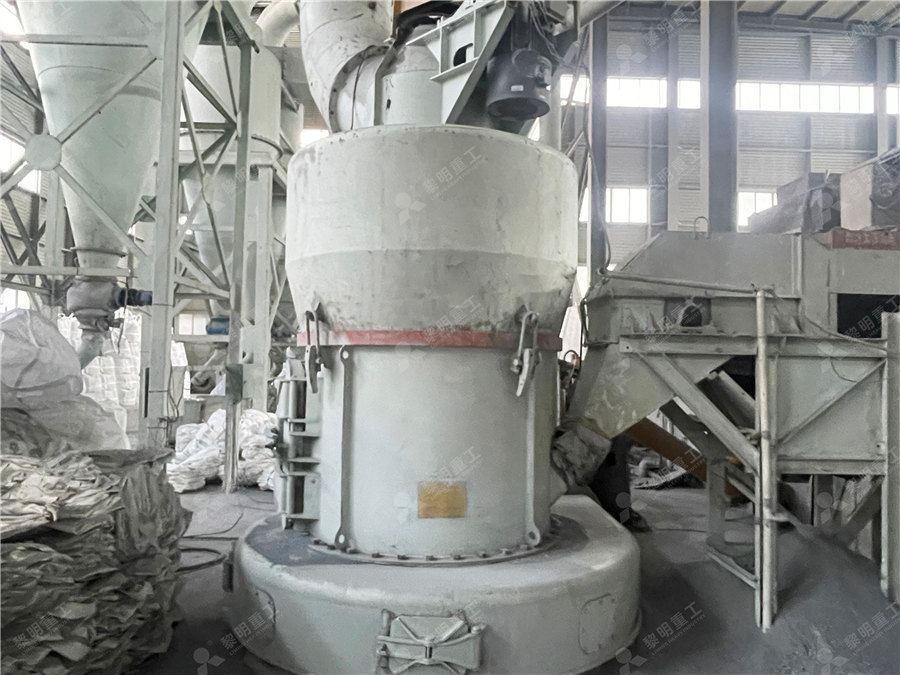
Recent advances in process and materials for dry desulfurization
Currently, desulfurization technologies can be categorized into three main types: wet flue gas desulfurization (FGD) [11], [12], [13], semidry desulfurization [14] and dry desulfurization [15]Wet flue gas desulfurization is widely employed in largescale desulfurization processes due to its high efficiency and low energy consumption [16]However, it poses a significant environmental 2023年12月1日 The fixedbed dry FGD technology is a promising technique for controlling the emission of SO 2, which has the advantages of lower footprint, low operating costs, no water consumption, and high desulfurization efficiencyHowever, most of the past research on Cabased desulfurizers performs in the range of 400–700 ℃, which is higher than the temperature of Mechanism and experimental study of desulfurizing agent 2021年7月1日 The most popular technologies applied for PM and SO 2 removals are electrostatic precipitators and limestonegypsum flue gas desulfurization with an average removal efficiency of 718% and 903% the development of lowtemperature SCR technology is suitable for sintering flue gas denitrification and a guarantee for controlling the NO x Emissions of air pollutants from sintering flue gas in the 2021年3月17日 Iron ore sintering is an important part of a long steelmaking process with sulfur dioxide emissions accounting for 40%–80% of the total sulfur dioxide emissions in steel companies [1,2,3,4]Semidry flue gas desulfurization technology combines the characteristics of wet and dry flue gas desulfurization processes, and it has significant advantages such as low Lowtemperature oxidation behavior and mechanism of semi
.jpg)
RESEARCH PROGRESS OF DESULFURIZATION AND DENITRATION TECHNOLOGIES
Based on the introduction of the characteristics of the sintering flue gas and the changes in emission standards, this paper summarizes the application status of separate desulfurization technologies, separate denitrification technologies and simultaneous desulfurization and denitration technologies, as well as the research and development 2021年11月10日 RESEARCH PROGRESS OF DESULFURIZATION AND DENITRATION TECHNOLOGIES FOR SINTERING FLUE GAS IN IRON AND STEEL INDUSTRY[J] ENVIRONMENTAL ENGINEERING , 2022, 40(9): 253261 doi: 1013205/jhjgc钢铁行业烧结烟气脱硫脱硝技术研究进展2015年11月28日 This paper analyzes and discusses the flue gas denitrification technology in the application of sintering flue gas,combining the characteristics of the steel industry sintering flueTo 400m sintering machine,study on sintering flue gas ozone oxidation simultaneous desulfurization and denitrification technology plan,and analyzes environmental and economic benefits for Analysis Denitration Technology for Ironsteel Sintering Flue Gas2021年8月15日 Increasingly stringent pollutant emission standards pose a new challenge to the control of air pollutants in China's iron and steel industry (ISI) This study quantified and compared the environmental and economic effects of three typical sintering flue gas ultralow emission treatment technologies in China's ISI, namely, semidry flue gas desulfurization + semidry flue Environmental and economic impact assessment of three sintering flue