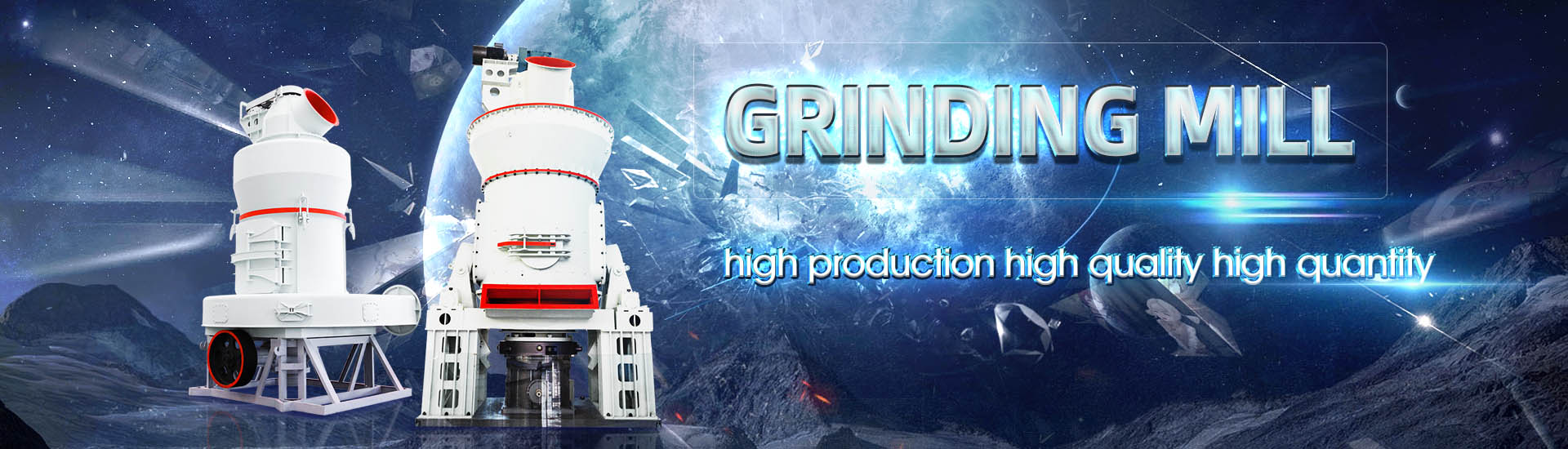
Mechanical crushing method for iron oxide production equipment
.jpg)
(PDF) SIZE REDUCTION BY CRUSHING
2017年3月4日 Crushing is the first step of mineral processing where the ore/rocks from the mine site is fed into the mechanical equipment in order to 2010年1月1日 Crushing is used to very quickly produce a fine powder from a bulk material or fine particle using mechanical crushing This technique is essentially used to investigate Mechanical Preparation Techniques SpringerLink2024年7月26日 In a cone crusher the stones are crushed with both SPB and IPB as the material moves down through the chamber The relative amounts of IPB and SPB depends on factors Crushing Principles of Mechanical Crushing 911 mechanical crushing In addition, in the liberation of iron oxide ores (hematite and magnetite), some studies resulted in lower slime production and lower silica and phosphorus recovery in The effect of high voltage electrical pulses on iron ore
.jpg)
Research into the crushing and grinding processes of
mechanical crushing and grinding of iron ore under production conditions has been proven A patent of Ukraine for a jaw crusher design implementing simultaneous impact of mechanical 2022年1月1日 Most of the highgrade hematite iron ores are typically subjected to simple dry processes of crushing and classification to meet the size specifications required for direct Comminution and classification technologies of iron ore2021年1月2日 Dephosphorization treatment of high phosphorus iron ore by prereduction, mechanical crushing and screening methodsA novel direct reductionflash smelting separation process of There are four main processes used in powder production: solidstate reduction, atomization, electrolysis, and chemical In solidstate reduction, selected ore is crushed, typically mixed with carbon, and passed through a continuous furnaceMaking Metal Powder MPIF
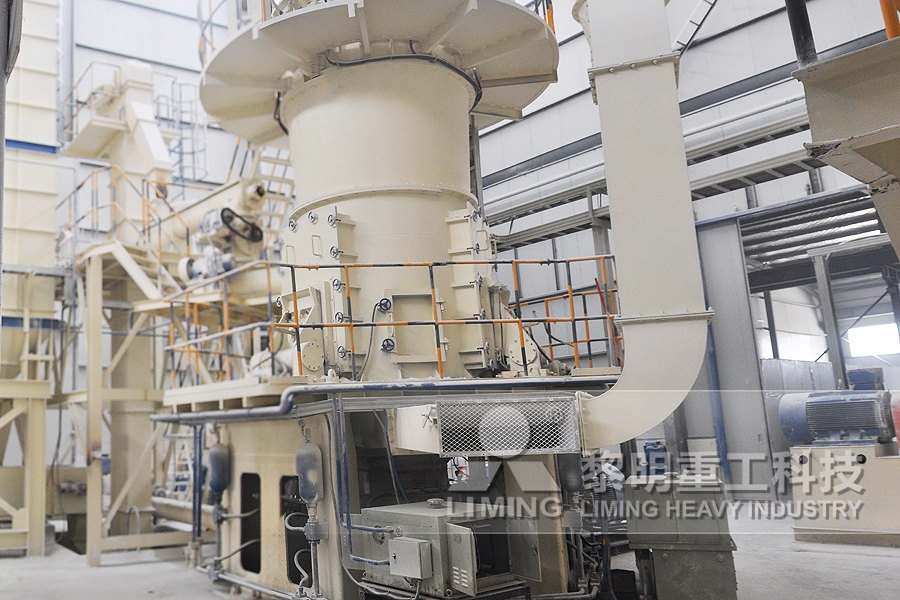
Iron Ore Processing, General SpringerLink
2022年10月20日 Making iron and steel from iron ore requires a long process of mining, crushing, separating, concentrating, mixing, agglomeration (sintering and pelletizing), and 2011年1月31日 It is well known that magnetic iron oxide nanoparticles can be synthesized using many methods hydrothermal reaction [14][15][16] , microwave [17] , solgel method [18,19] , micro emulsion method Preparation of iron oxide nanoparticles by mechanical milling2024年6月28日 The efficiency of mechanical crushing is a key metric for evaluating machinery performance However, traditional contactbased methods for measuring this efficiency are unable to provide realtime Energy Efficiency Measurement of Mechanical Crushing 2018年12月26日 Crushing by compression is done between two surfaces, with the work being done by one or both surfaces For example, jaw crushers using this method of compression are suitable for reducing extremely hard and abrasive rock As a mechanical reduction method, compression should be used for the following If the material is hard and toughConstruction, Working and Maintenance of Crushers for
.jpg)
Crushing Principles of Mechanical Crushing 911
2024年7月26日 Manager Crushing Chamber and Materials Development Product Development Center Crushing (RD) Master of Science in Mechanics, specialized in mechatronics PhD 2007, Chalmers University Partly funded by Sandvik Modeling, simulation and optimization of crushing plants TechnicalEconomic Optimization Sandvik employee since 年2月17日 The dephosphorization treatment of the prereduced iron ore by mechanical crushing and screening methods was evaluated as a function of the initial reduction condition, screen size, and the Dephosphorization Treatment of High Phosphorus Iron Ore 2023年2月15日 After crushing, the ore is ground to realize the monomer separation of minerals, and then the highgrade concentrate is obtained by the gravity separation Compared with other beneficiation methods, gravity separation can be applied to a wide range of materials and has the advantages of low production cost and less harm to the environmentHow to Extract Iron from Hematite: Methods and Plants2018年10月23日 The ore is Hematite, chemical name is iron III oxide, the chemical formula is Fe 3 O 4, It has a blood red colour, it is more easily reduced, Iron is from 5060 %, place of deposits is Oasis area (western desert) and western part of Aswan The ore is Limonite, chemical name is Hydrated iron III oxide, the chemical formula is 2Fe 2 O 33H 2 O, It has a yellow hydrated Extraction of Iron from its ores, Iron dressing, Reduction production
.jpg)
Powder metallurgy P/M University of Technology, Iraq
2018年1月28日 Metal powders are produced by mechanical methods or chemical methods as shown in figure (1 2) The commonly used methods include water and gas atomization, milling, mechanical alloying, electrolysis, and chemical methods including reduction of oxides Suitable methods for powder production depend on required production2022年6月23日 Keywords: iron oxide nanoparticles, synthesis processes, green synthesis processes, characterization techniques, physicochemical properties 1 Introduction Iron oxides are transition metal oxides ubiquitously found in nature, having many implications in various biological and geological processes [1–4] They occur naturallyNew Approaches in Synthesis and Characterization 2023年1月28日 What is iron ore pellet Iron ore pellets are made by adding a small amount of additives to the fine ore powder (200 mesh, that is, the ore powder with a particle size of less than 0074mm accounts for more than 80%, and the specific surface area is more than 1500cm2/g), adding water to the pelletizer, relying on capillary force and mechanical force of Iron ore pellets for blast furnace a technical guide MAXTON2009年12月31日 Mechanical alloying/milling technique is characterized by the repeated welding and fracturing of powder particles in a highenergy ball mill, which often results in excessive cold welding and Mechanical Crushing and Grinding ResearchGate
.jpg)
Development of technology for the production of natural red iron oxide
2017年1月1日 The most common inorganic pigment is red iron oxide World production of iron oxide pigments is about 600 thousand tons per year and greatly exceeds the production of other color pigments, with mechanical crushing In addition, in the liberation of iron oxide ores (hematite and magnetite), some studies resulted in lower slime production and lower silica and phosphorus recovery in iron ore concentrate in the electrical crushing method than the mechanical one (Andres et al, 1999; Andres et al, 2001; Andres, 2010)The effect of high voltage electrical pulses on iron ore 2021年12月20日 The main problem for the application of hydrogen generated via hydrolysis of metal alloys is the low hydrogen generation rate (HGR) In this paper, active Al alloys were prepared using a new (PDF) Enhanced Hydrogen Generation Performance of Al2023年6月29日 The objective of this study is to describe primary lithium production and to summarize the methods for combined mechanical and hydrometallurgical recycling of lithiumion batteries (LIBs) This study also aims to draw attention to the problem of lithium losses, which occur in individual recycling steps The first step of hydrometallurgical treatment is leaching, Lithium Production and Recovery Methods: Overview of
.jpg)
Iron processing Definition, History, Steps, Uses, Facts
Although the Romans built furnaces with a pit into which slag could be run off, little change in ironmaking methods occurred until medieval times By the 15th century, many bloomeries used low shaft furnaces with water power to drive the bellows, and the bloom, which might weigh over 100 kilograms, was extracted through the top of the shaft The final version of this kind of bloomery 2021年7月12日 Keywords: Mechanical milling, copper oxide nanoparticles 1 Introduction CuO nanoparticles are being studied for their unique thermal and mechanical characteristics The ball mill is a topdown method for creating ultrafine particles Produit from severe plastic deformation of coarse granules Top down techniques such as highMechanical Milling Of Copper Oxide Nanoparticles EUDLNatural iron oxides occur widely, and are exploited from a variety of deposit types World iron oxide pigment mine production in 2014 is given in Table 1 Micaceous iron oxide (also known as specular hematite, specularite) is a variety of hematite mineral with a silvery metallic luster It is mainly used in pigment industry and in welding Micaceous iron oxide production by application of 2021年9月24日 Throughout human history, any society’s capacity to fabricate and refine new materials to satisfy its demands has resulted in advances to its performance and worldwide standing Life in the twentyfirst century cannot be predicated on tiny groupings of materials; rather, it must be predicated on huge families of novel elements dubbed “advanced materials” Mechanical Milling: A Superior Nanotechnological Tool for
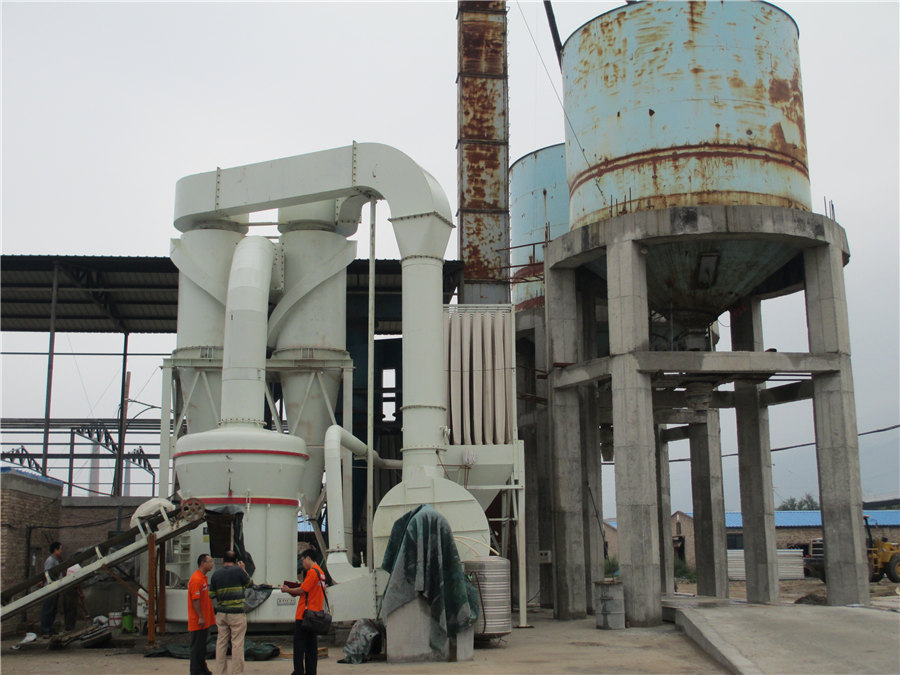
Iron Ore Processing, General SpringerLink
2022年10月20日 Iron ore handling, which may account for 20–50% of the total delivered cost of raw materials, covers the processes of transportation, storage, feeding, and washing of the ore en route to or during its various stages of treatment in the mill Since the physical state of iron ores in situ may range from friable, or even sandy materials, to monolithic deposits with hardness of Ensuring the safety of personnel and equipment is paramount in kiln operation Common Hazards and Prevention Strategies Heat and Fire Hazards: Implementing proper insulation, ventilation, and fire suppression systems Comprehensive Guide to Cement Kilns: 2012年2月3日 Synthesis of nanomaterials by a simple, low cost and in high yield has been a great challenge since the very early development of nanoscience Various bottom and top down approaches have been developed so far, for the commercial production of nanomaterials Among all top down approaches, high energy ball milling, has been widely exploited for the synthesis Mechanical Milling: a Top Down Approach for the Synthesis 2023年7月23日 The transformation from traditional iron and steelmaking technologies to green H2based new technologies will require an improvement in the quality and purity of iron ore burden materials Iron ore pellets are Developing Iron Ore Pellets Using Novel Binders
.jpg)
Recent advances in the marketing, impurity characterization
2023年11月28日 Mechanical crushing, highpressure crushing, ultrasonic crushing, and current pulse crushing are the main methods used for crushing The selection of the crushing method should consider its efficacy in separating quartz from associated minerals, avoidance of impurities introduction into the raw material, as well as its energysaving and 2022年10月1日 Demand for lithiumion batteries (LIBs) increased from 05 GWh in 2010 to approximately 526 GWh in 2020 and is expected to reach 9,300 GWh by 2030 [1, 2]The technology has inherent advantages compared to leadacid, nickel–metal hydride, and nickel–cadmium storage technologies due to its high energy density [3], high life cycle [4], and Preprocessing of spent lithiumion batteries for recycling: 2023年6月30日 PDF Over the last few decades, the demand for energyefficient mineralprocessing methods has continued study is crushing equipment It is a complex of units designed to reduce the fraction Modeling and Improving the Efficiency of Crushing Equipment2021年1月1日 Currently, approximately 14 billion tons per year of iron ore tailing wastes (IOT) are generated, mainly in Australia, Brazil, and China This work describes the characterization and application (PDF) Iron Ore Tailings: Characterization and Applications
.jpg)
SIZE REDUCTION BY CRUSHING METHODS By
Crushing is the process of transferring a force amplified by mechanical advantage through a material made of molecules that bond together more strongly, and resist deformation more, than those in the2024年6月28日 The efficiency of mechanical crushing is a key metric for evaluating machinery performance However, traditional contactbased methods for measuring this efficiency are unable to provide realtime data monitoring and can potentially disrupt the production process In this paper, we introduce a noncontact measurement technique for mechanical crushing efficiency Energy Efficiency Measurement of Mechanical Crushing 2022年1月23日 Reactions of silica, iron oxides, titania The stoichiometry of the dissolution reaction of kaolinite and the formation of DSP a re very similar as ha s been described in Section 411(PDF) Chemical Processing of Bauxite: Alumina and Silica 2011年1月31日 It is well known that magnetic iron oxide nanoparticles can be synthesized using many methods hydrothermal reaction [14][15][16] , microwave [17] , solgel method [18,19] , micro emulsion method Preparation of iron oxide nanoparticles by mechanical milling
.jpg)
Energy Efficiency Measurement of Mechanical Crushing
2024年6月28日 The efficiency of mechanical crushing is a key metric for evaluating machinery performance However, traditional contactbased methods for measuring this efficiency are unable to provide realtime 2018年12月26日 Crushing by compression is done between two surfaces, with the work being done by one or both surfaces For example, jaw crushers using this method of compression are suitable for reducing extremely hard and abrasive rock As a mechanical reduction method, compression should be used for the following If the material is hard and toughConstruction, Working and Maintenance of Crushers for 2024年7月26日 Manager Crushing Chamber and Materials Development Product Development Center Crushing (RD) Master of Science in Mechanics, specialized in mechatronics PhD 2007, Chalmers University Partly funded by Sandvik Modeling, simulation and optimization of crushing plants TechnicalEconomic Optimization Sandvik employee since 2004Crushing Principles of Mechanical Crushing 911 2011年2月17日 The dephosphorization treatment of the prereduced iron ore by mechanical crushing and screening methods was evaluated as a function of the initial reduction condition, screen size, and the Dephosphorization Treatment of High Phosphorus Iron Ore
.jpg)
How to Extract Iron from Hematite: Methods and Plants
2023年2月15日 After crushing, the ore is ground to realize the monomer separation of minerals, and then the highgrade concentrate is obtained by the gravity separation Compared with other beneficiation methods, gravity separation can be applied to a wide range of materials and has the advantages of low production cost and less harm to the environment2018年10月23日 The ore is Hematite, chemical name is iron III oxide, the chemical formula is Fe 3 O 4, It has a blood red colour, it is more easily reduced, Iron is from 5060 %, place of deposits is Oasis area (western desert) and western part of Aswan The ore is Limonite, chemical name is Hydrated iron III oxide, the chemical formula is 2Fe 2 O 33H 2 O, It has a yellow hydrated Extraction of Iron from its ores, Iron dressing, Reduction production 2018年1月28日 Metal powders are produced by mechanical methods or chemical methods as shown in figure (1 2) The commonly used methods include water and gas atomization, milling, mechanical alloying, electrolysis, and chemical methods including reduction of oxides Suitable methods for powder production depend on required productionPowder metallurgy P/M University of Technology, Iraq2022年6月23日 Keywords: iron oxide nanoparticles, synthesis processes, green synthesis processes, characterization techniques, physicochemical properties 1 Introduction Iron oxides are transition metal oxides ubiquitously found in nature, having many implications in various biological and geological processes [1–4] They occur naturallyNew Approaches in Synthesis and Characterization
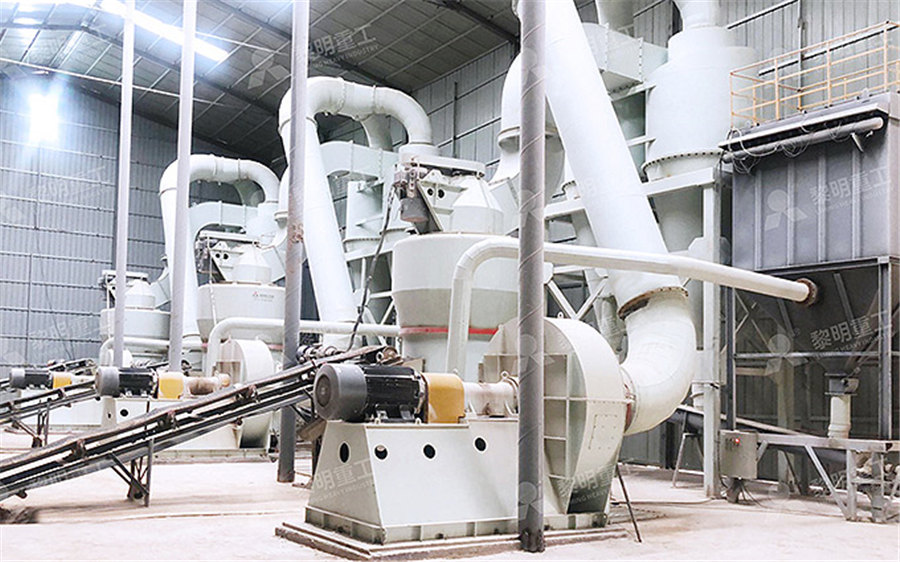
Iron ore pellets for blast furnace a technical guide MAXTON
2023年1月28日 What is iron ore pellet Iron ore pellets are made by adding a small amount of additives to the fine ore powder (200 mesh, that is, the ore powder with a particle size of less than 0074mm accounts for more than 80%, and the specific surface area is more than 1500cm2/g), adding water to the pelletizer, relying on capillary force and mechanical force of