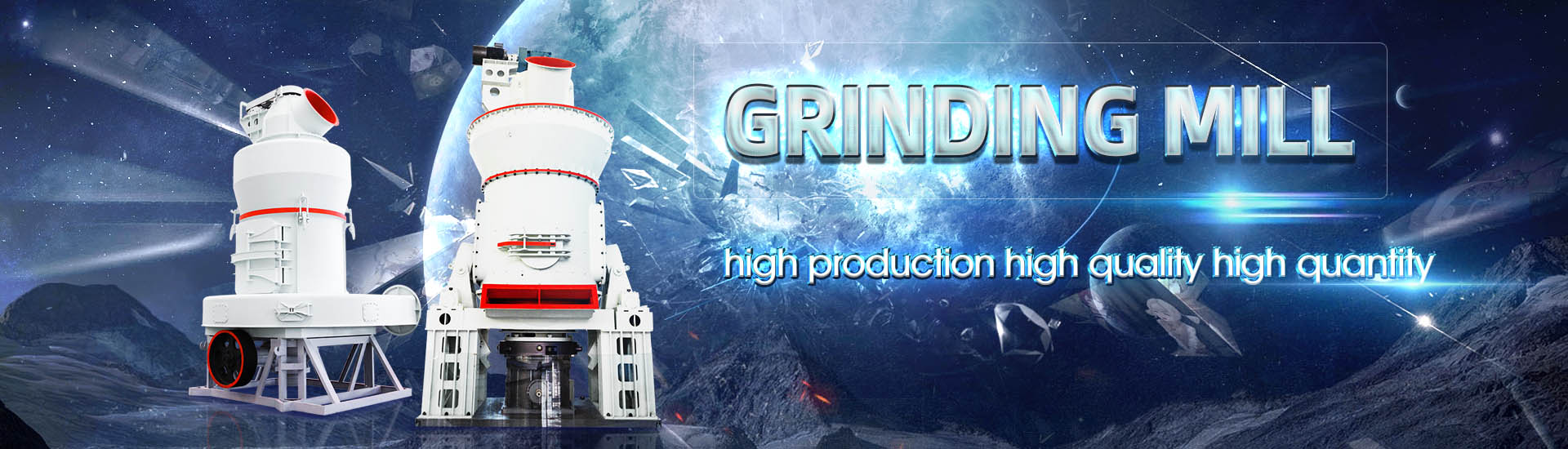
Cement powder grinding process flow chart
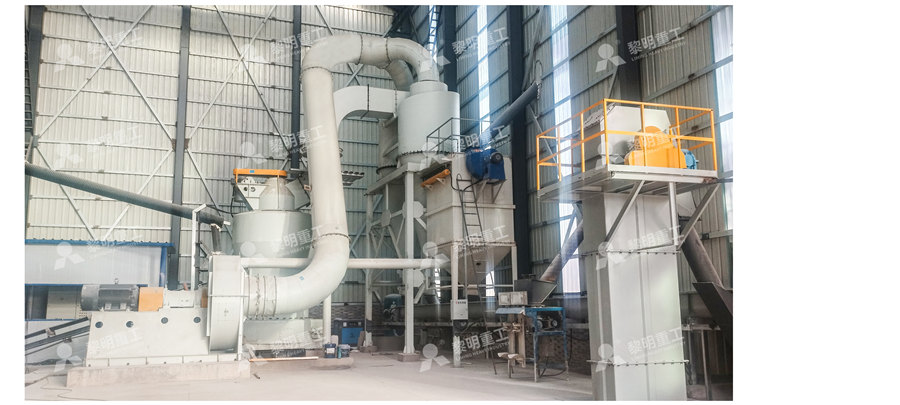
Typical cement manufacturing process flow
Finally, during the cement grinding and distribution process, firstly the cooled clinker is ground with around 5% of gypsum and other 17 JRTE2020 cementitious materials to form the final2019年7月20日 The whole process of cement manufacturing in Messebo Cement plant which consists of two separate Cement Production lines can be summarized into the following CEMENT PRODUCTION AND QUALITY CONTROL A 2024年7月29日 Process flow diagram for the cement manufacturing process, showing electricity and heat consumption or inputs [39] The paper presented herein investigates the effects of usingProcess flow diagram for the cement What are the steps involved in manufacturing cement? Cement production involves several key steps, including: Crushing the raw materials Homogenizing the mixture Proportioning the raw materials accurately Grinding the materials StepbyStep Guide to the Manufacturing of
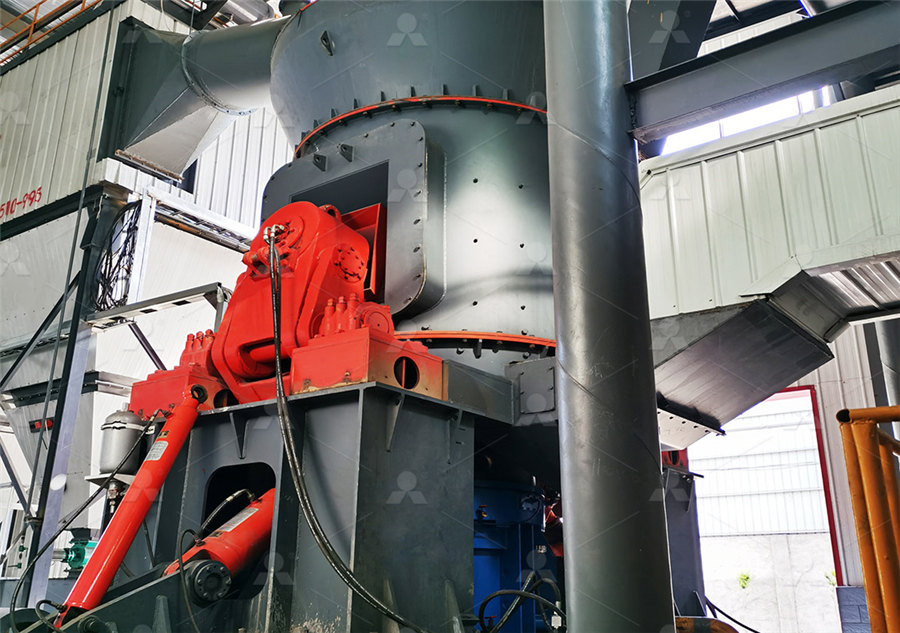
Flow chart of the grinding and blending process
Flow chart of the grinding and blending process The objective of the present study is to use a reliable model of the raw meal mixing process dynamics in raw meal production2 天之前 raw materials, burning, grinding and quality control are supported by a range of chapters addressing critial topics such as maintenance and plant reporting, alongside a The Cement Plant Operations Handbook International 2019年8月26日 41 Cement Manufacturing: Basic Process and Operation To design the Refractory for the lining of different equipments in a cement plant, it is necessary to Chapter 4 Cement Manufacturing and Process Control2024年5月22日 The cement production process 1 The Quarry: The cement production process begins with the extraction of limestone and clay from the quarry 2 Crusher and PreBlending: A practical guide to improving cement manufacturing
.jpg)
How Is Cement Produced in Cement Plants
Nowadays, the dry process is the most popular cement making process which is widely adopted by cement plants all over the world for its great advantages in energy saving and environmental protection Cement Making Process The 2023年12月20日 Cement manufacturing is a complex process that begins with mining and then grinding raw materials that include limestone and clay, to a fine powder, called raw meal, which is then heated to a sintering temperature as The Cement Manufacturing Process Thermo 2024年9月5日 The Manufacturing Process of Cement Now, let’s explore the steps involved in the cement production process in more detail: 1 Mining and Crushing The process of making cement begins with mining, where raw A Comprehensive Guide to the Cement Burning: In this operation, the slurry is directly fed into a long inclined steel cylinder called a Rotary kilnIn this kiln there are 3 different zones shown in fig below Cement Manufacturing Process Flow Chart (i) Drying Zones: In the wet process, the drying zone is comparatively larger than the dry process It is because the raw material in slurry form is directly fed into the kiln Manufacturing of Cement By Dry and Wet Process Expert
.jpg)
Manufacture Of Portland Cement Process Flow chart civil
2019年11月30日 Manufacture Of Portland Cement Process Flow chart – civil learners July 23, 2021 November 30, 2019 by Maruthi Baddi The powder is mixed in require proportions to get a dry raw mix which is stored in silos (storage tank) and kept ready to be fed into the rotary kiln cement grinding, and packing technologies with advanced process 2024年11月23日 Cement Extraction, Processing, Manufacturing: Raw materials employed in the manufacture of cement are extracted by quarrying in the case of hard rocks such as limestones, slates, and some shales, with the aid of blasting when necessary Some deposits are mined by underground methods Softer rocks such as chalk and clay can be dug directly by Cement Extraction, Processing, Manufacturing Britannica2024年3月16日 The document describes the cement manufacturing process used by Lafarge, a French industrial company The process involves 5 main steps: 1) mining of raw materials like limestone and clay, 2) crushing and storing the materials, 3) drying, grinding and mixing the materials into raw meal, 4) firing the raw meal in a kiln to produce cement clinker, and 5) Cement Manufacturing Process PDF Mill (Grinding) ScribdThe final step in cement manufacturing is the grinding of clinker into cement powder, followed by the finalization process that ensures the product meets all required specifications and standards This stage is crucial as it defines the physical and chemical properties of the cement, making it suitable for various construction purposesCement Making Guide: Steps, Impact Green Alternatives
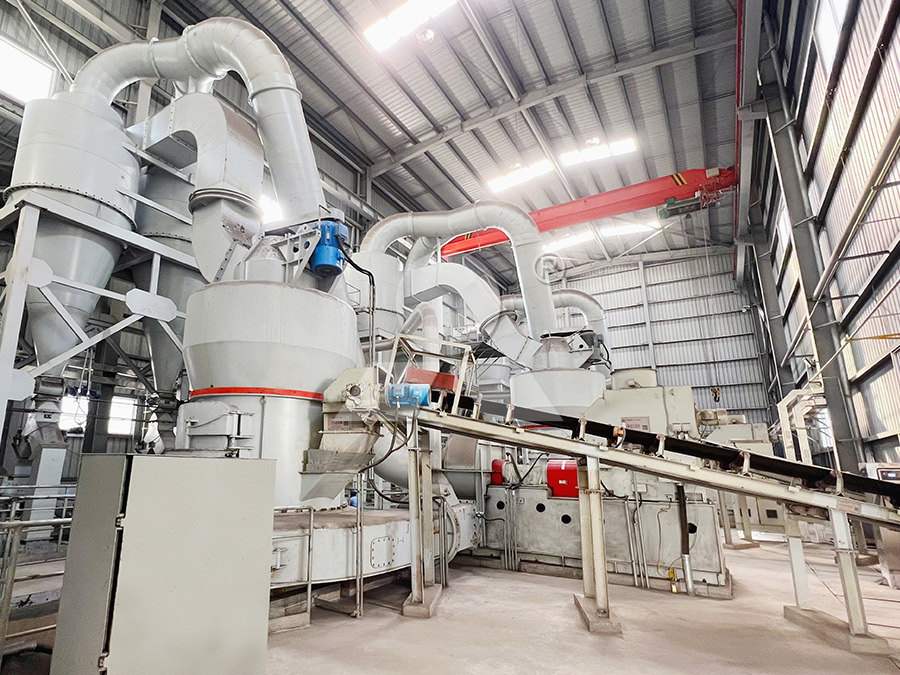
Cement Production Demystified: StepbyStep Process and
2024年1月18日 The use of fossil fuels such as coal, natural gas, and oil is common in cement production, both as a fuel for the kiln and as a source of heat for other parts of the process which leads to CO2 emitted by combustionHowever chemical reactions happening in the kiln (calcination) are also responsible for up to 60% of the total of emissions of the Chunks are then ground into a fine powder Site A Sustainable Future Some manufacturers grind the raw materials dry, while others use a wetgrinding process involving water Quarrying Cement manufacturers quarry raw materials including limestone, clay, and sand Each step of the cement production process is carefully monitored How Cement is Made Portland Cement AssociationFinally, during the cement grinding and distribution process, firstly the cooled clinker is ground with around 5% of gypsum and other 17 JRTE2020 cementitious materials to form the final cement Typical cement manufacturing process flow 1 天前 This grainy cement is then passed through a grinder again to get fine cement powder This Cement is then ready to be packed in bags Now, to produce the concrete, this cement is used in a ratio of 15 % with 10 % of IELTS Diagram: Model Answer Band Score 9 with
.jpg)
Cement Grinding Unit Clinker Grinder AGICO
The cement grinding unit manufactured by our company merges drying, grinding, powder classifying, dust collecting and cement packing into a single It can not only grind cement clinker but also process cement admixture, such as 2016年10月5日 1 Introduction Cement is an energyintensive industry in which the grinding circuits use more than 60 % of the total electrical energy consumed and account for most of the manufacturing cost []The requirements for the cement industry in the future are to reduce the use of energy in grinding and the emission of CO 2 from the kilns In recent years, the production EnergyEfficient Technologies in Cement Grinding2020年10月5日 Cement industry : grinding process of ball mill Download as a PDF or view online for free Submit The resulting hard substance, called 'clinker', is then ground with a small amount of gypsum into a powder to make 'Cement', the most commonly used type of cement This cement is called Ordinary Portland Cement • Ordinary Portland Cement industry : grinding process of ball mill PPT2024年5月14日 Cement manufacturing process is a reliable bonding material It is obtained by burning calcareous material (lime) and argillaceous material (clay) and then grinding, types of cement The cement manufacturing process was first produced by Joseph Aspidin, a mason from England As its color resembled a variety of sandstone found in Portland, he named it Portland CEMENT MANUFACTURING PROCESS ! TYPES OF CEMENT, FLOW CHART
.jpg)
Flow chart of the grinding and blending process
Download scientific diagram Flow chart of the grinding and blending process from publication: Effective Optimization of the Control System for the Cement Raw Meal Mixing Process: I PID Tuning 2016年1月20日 Over the last century, Portland cementbased concrete has become the highest manufactured product on Earth in terms of volume Concrete is used worldwide as a building material and is the most consumed substance on Earth after water (Sakai, 2009)The volume of concrete produced globally is approximately 530 billion m 3 per year (Roskos et al, 2011), Analysis of material flow and consumption in cement production process The slurry is introduced into a rotary kiln, a lengthy cylindrical boiler that rotates on its axis The kiln consists of three zones: the upper zone, known as the preheating zone, where hot gases from the lower zone dry and heat the slurry; the middle zone, known as the calcining zone, where a temperature of about 1500 °C is reached and the calcium carbonate in the slurry breaks down 2 Types of Manufacturing of Cement Wet and Dry ProcessCement grinding operation may be performed in one of the following mill setups Ball and tube mills Vertical Roller Mills (VRM) Roller press with Ball mill Ball Mill Ball mills with high efficiency separators have been used for cement grinding in cement plants all these years Ball mill is a cylinder rotating at about 7080% of critical Cement Grinding Cement Plant Optimization
.jpg)
How cement additives aid the grinding process GCPAT
Cement additives are chemicals that are used to improve cement grindability and/or performance This is accomplished by addressing several challenges in the production of cement For example, as cement grinding progresses and grains become smaller, the attractive thermodynamic, physical, mechanical and chemical forces result in strong adhesion of particles1971年8月17日 116 Portland Cement Manufacturing 1161 Process Description17 Portland cement is a fine powder, gray or white in color, that consists of a mixture of hydraulic cement materials comprising primarily calcium silicates, aluminates and aluminoferrites More than 30 raw materials are known to be used in the manufacture of portland cement, and these116 Portland Cement Manufacturing US EPA5 天之前 Definition of the Dry Process The dry process is a method of cement production that involves grinding and mixing raw materials in their dry state This contrasts with the wet process, where materials are mixed with water In the dry process, moisture content is minimized from the outset, leading to significant savings in energy and fuel consumption during the subsequent Dry Process of Cement Manufacturing: StepbyStep Guide 2020年8月25日 A full cement production process includes the cement crushing process, raw mill process, clinker process, and cement grinding process, cement packing process, and related process Find more! Skip to content +86 s about blog contact EN ES Menu Menu Home; add certain water into raw meal powder to make Cement Production Process Cement Manufacturing Process AGICO CEMENT
.jpg)
Understanding the Role of Clinker Grinding in Cement
2023年10月19日 Clinker is a critical component in the production of cement and forms the intermediate product during the cement manufacturing process It can be best described as a nodular material, usually grayish in color, which is produced by sintering limestone and aluminosilicate materials such as clay at high temperatures in a cement kiln2020年4月7日 The primary raw materials for the mass production of cement can either be calcareous or argillaceous The former ingredient is obtained from limestone, marl, cement rock, chalk, etc, whereas the latter one is procured from clay, slate, blast furnace slag, shale, etc The process of manufacturing cement can either be a wet process or a dry processManufacturing Process of Cement Construction How2024年11月26日 Learn about our cement grinding process and plant stages for high quality cement Amrit Support About Amrit Support; Services; Activities; Corporate Annual Return FY 202021; FY 202122; FY 202223; Nomination and Remuneration Policy; Whistle Blower Policy (VIGIL MECHANISM) csr CSR Philosophy and Approach;Cement Grinding Unit Process High Quality Cement Grinding 2017年5月19日 Grinding is an essential operation in cement production given that it permits to obtain fine powder which reacts quickly with water, sets in few hours and hardens over a period of weeks i Overview of cement grinding: fundamentals, additives, technologies
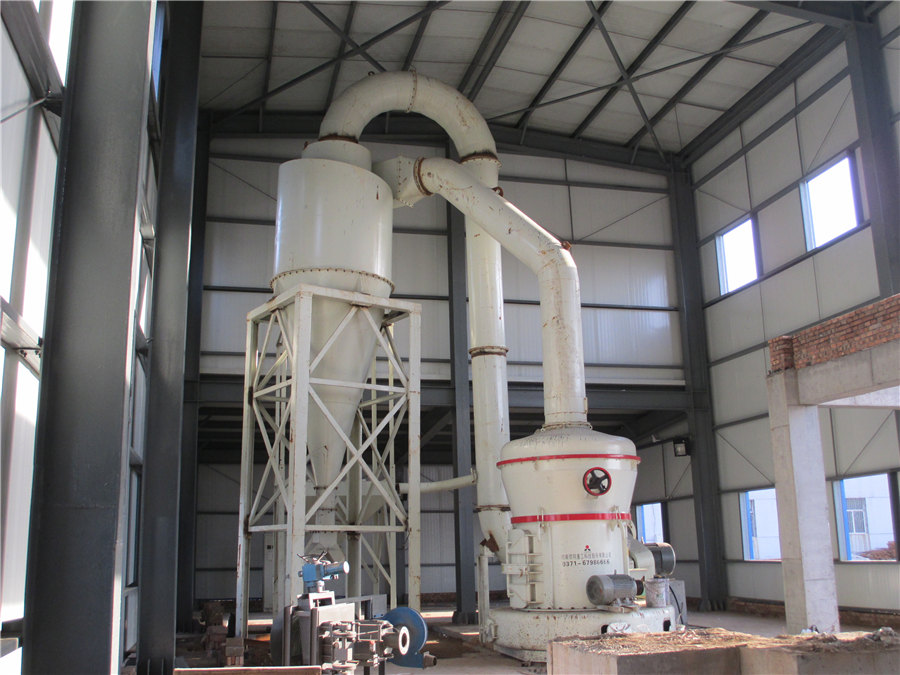
Cement Manufacturing Process Chemical Engineering World
2020年9月26日 Cement Manufacturing Process Cement Manufacturing Process Cement Manufacturing Process Cement is a material which is used to bind other materials together Binding means it has an effect of gluing the substances together due to cohesive and adhesive action and then hardens and sets in order to become permanent Cement is usually not used The main impact on the energy consumption of cement production is the burning process of cement clinker in a rotary kiln, and the energy costs associated with burning cement clinker constitute 50 Stages in cement production flow chart [43] ResearchGateNowadays, the dry process is the most popular cement making process which is widely adopted by cement plants all over the world for its great advantages in energy saving and environmental protection Cement Making Process The How Is Cement Produced in Cement Plants2023年12月20日 Cement manufacturing is a complex process that begins with mining and then grinding raw materials that include limestone and clay, to a fine powder, called raw meal, which is then heated to a sintering temperature as The Cement Manufacturing Process Thermo
.jpg)
A Comprehensive Guide to the Cement
2024年9月5日 The Manufacturing Process of Cement Now, let’s explore the steps involved in the cement production process in more detail: 1 Mining and Crushing The process of making cement begins with mining, where raw Burning: In this operation, the slurry is directly fed into a long inclined steel cylinder called a Rotary kilnIn this kiln there are 3 different zones shown in fig below Cement Manufacturing Process Flow Chart (i) Drying Zones: In the wet process, the drying zone is comparatively larger than the dry process It is because the raw material in slurry form is directly fed into the kiln Manufacturing of Cement By Dry and Wet Process Expert 2019年11月30日 Manufacture Of Portland Cement Process Flow chart – civil learners July 23, 2021 November 30, 2019 by Maruthi Baddi The powder is mixed in require proportions to get a dry raw mix which is stored in silos (storage tank) and kept ready to be fed into the rotary kiln cement grinding, and packing technologies with advanced process Manufacture Of Portland Cement Process Flow chart civil 2024年11月23日 Cement Extraction, Processing, Manufacturing: Raw materials employed in the manufacture of cement are extracted by quarrying in the case of hard rocks such as limestones, slates, and some shales, with the aid of blasting when necessary Some deposits are mined by underground methods Softer rocks such as chalk and clay can be dug directly by Cement Extraction, Processing, Manufacturing Britannica
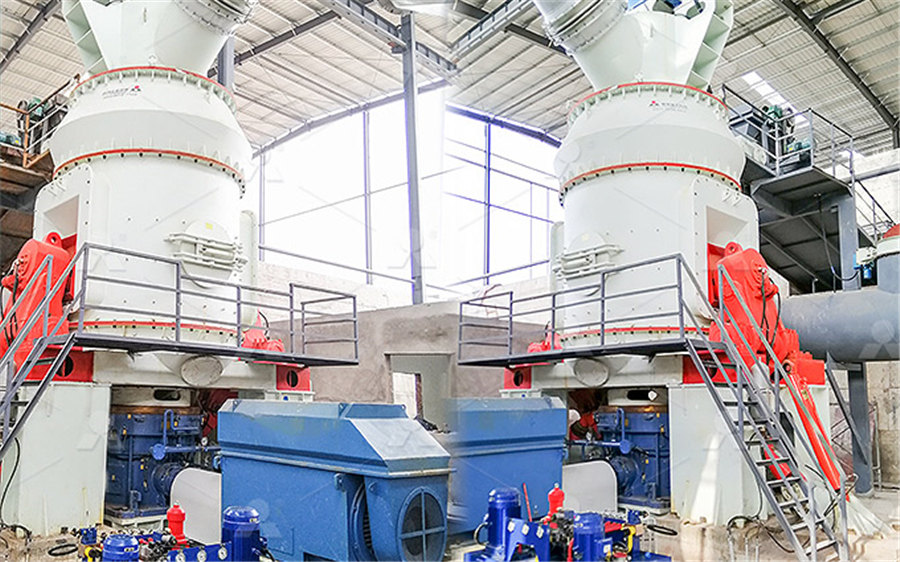
Cement Manufacturing Process PDF Mill (Grinding) Scribd
2024年3月16日 The document describes the cement manufacturing process used by Lafarge, a French industrial company The process involves 5 main steps: 1) mining of raw materials like limestone and clay, 2) crushing and storing the materials, 3) drying, grinding and mixing the materials into raw meal, 4) firing the raw meal in a kiln to produce cement clinker, and 5) The final step in cement manufacturing is the grinding of clinker into cement powder, followed by the finalization process that ensures the product meets all required specifications and standards This stage is crucial as it defines the physical and chemical properties of the cement, making it suitable for various construction purposesCement Making Guide: Steps, Impact Green Alternatives2024年1月18日 The use of fossil fuels such as coal, natural gas, and oil is common in cement production, both as a fuel for the kiln and as a source of heat for other parts of the process which leads to CO2 emitted by combustionHowever chemical reactions happening in the kiln (calcination) are also responsible for up to 60% of the total of emissions of the Cement Production Demystified: StepbyStep Process and Chunks are then ground into a fine powder Site A Sustainable Future Some manufacturers grind the raw materials dry, while others use a wetgrinding process involving water Quarrying Cement manufacturers quarry raw materials including limestone, clay, and sand Each step of the cement production process is carefully monitored How Cement is Made Portland Cement Association