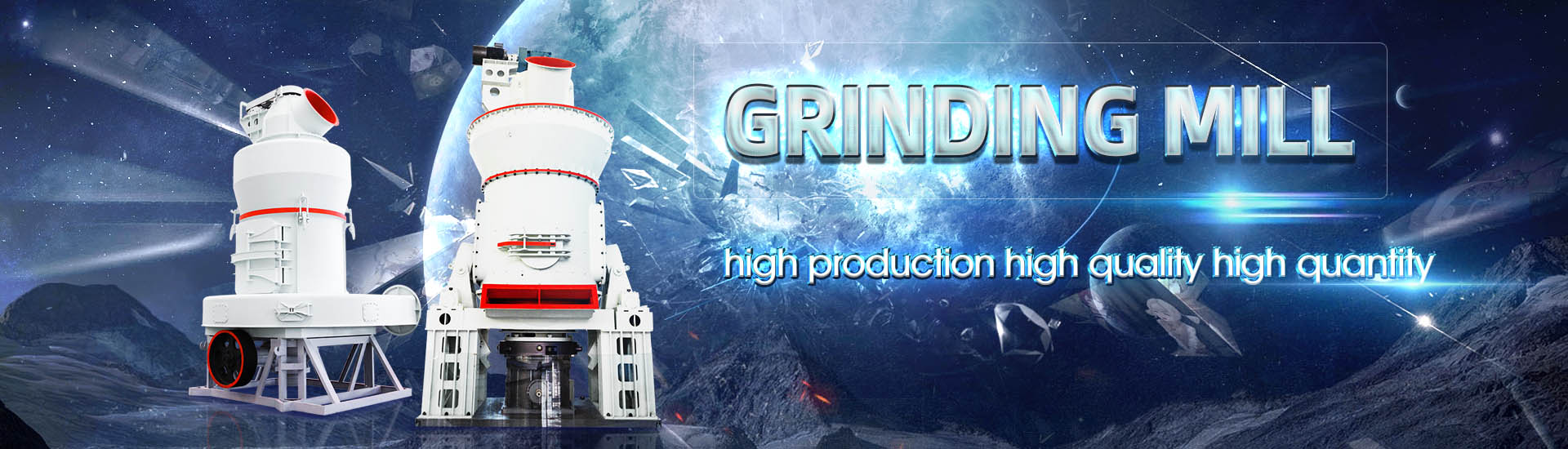
How much does it cost to produce cement clinker machine
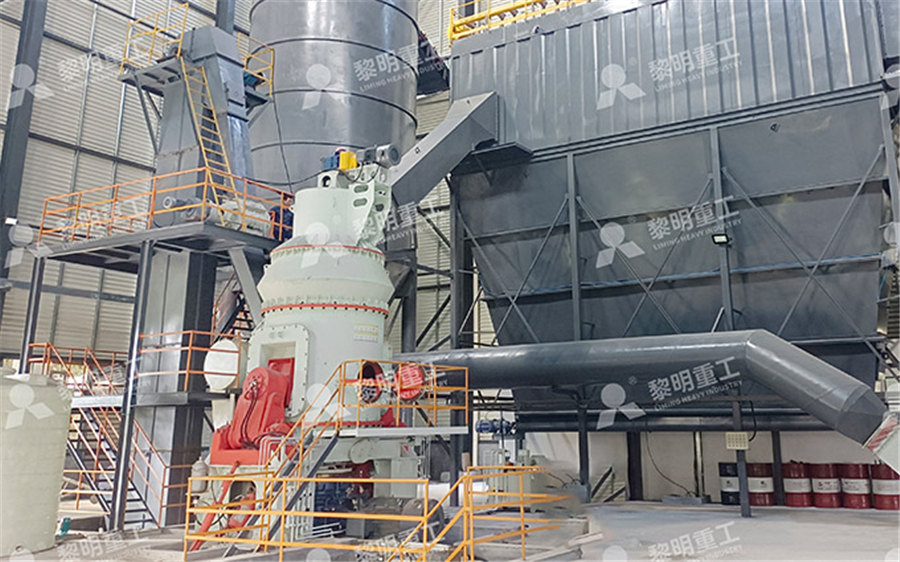
The Comprehensive Guide to Cement Plant
5 Clinker Storage Clinker storage is essential for maintaining a buffer between the kiln and the finish mill Equipment: Clinker silos, stackerreclaimers Technical Specifications: Clinker Silos: 10,00050,000 tons capacity Stacker 2020年5月15日 While the wet process requires almost 1,3001,600 kcal/kg of clinker and 110115 kwh of power to manufacture 1 tonne of cement, the dry process requires 720990 kcal/kg of clinker and 95110 kwh of power The four major costs associated with cement 2022年11月7日 The goal of the transformation cost calculator is to make an initial, qualified estimate of the additional costs of a climatefriendly cement clinker production via the Oxyfuel and ELEILAC routes compared to the cement Cement Transformation Cost Calculator agora Costs for clinker and cement production [] In the context of strategical planning in support of the energy transition, industry plays a key role, producing alone more than 20 % directCosts for clinker and cement production ResearchGate
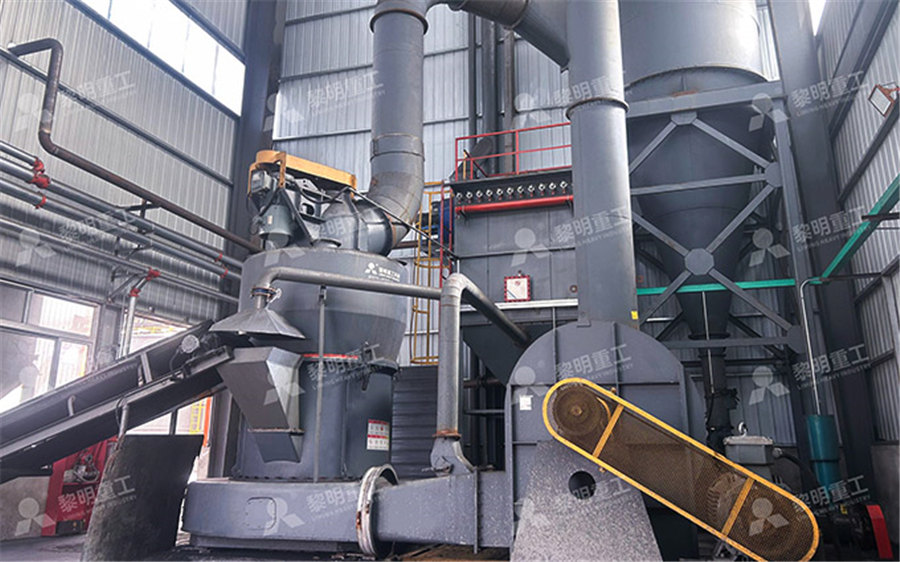
Clinker Production Clinker Manufacturing
Clinker is the material produced in the calcination stage and is usually used as the binder in many cement products In other words, it is a semifinished cement product by preparing limestone, clay, iron raw materials, etc, in proper Breakdown of the clinker costs for the cement kilns with and without CaL system [] The scope of this work is to perform a technoeconomic analysis of two Calcium Looping processes (CaL) forBreakdown of the clinker costs for the cement 41 Cement and Clinker Production Cement is a hydraulic blinder used to produce building materials such as mortar and concrete It mainly consists of clinker (about 70%) in addition to Clinker Production an overview ScienceDirect TopicsThis section provides an indepth review of major solutions deployed to decarbonize cement manufacturing, including alternative formulations of clinker, alternative fuels for cement Cement Clinker Production an overview ScienceDirect Topics
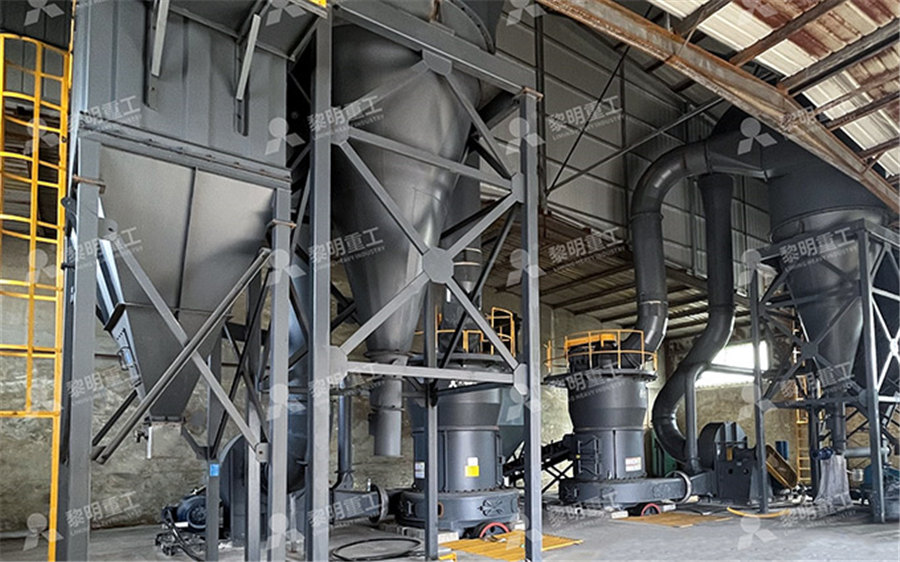
Cement and Clinker Production by Indirect
However, the clinkerization process, which is the basis of cement production, is responsible for an approximate annual global CO 2 emission of 2 billion tons As part of CEMBUREAU’s 5C strategy, the European cement industry aims to 2023年6月6日 Production Process of Clinker Cement manufacturers create clinkers through a multistep process that includes ingredient selection, heating, and grinding Raw Mineral Preparation – The main ingredients in clinker Cement Clinker: Production, Composition, Types, The cyclone preheating system Phase IV: Calcination The calcination is the core phase of the cement making dry process The calcination of the preheated raw meal takes place in the rotary kiln of the cement plant The rotary kiln is a How Is Cement Produced in Cement PlantsThe shaft kiln is not so widely used in cement plant as rotary kiln, but its structure is simple, the space occupation is small so the investment is relatively low Besides, it has a long service life and can produce cement of stable quality, Cement Manufacturing Machine Cement
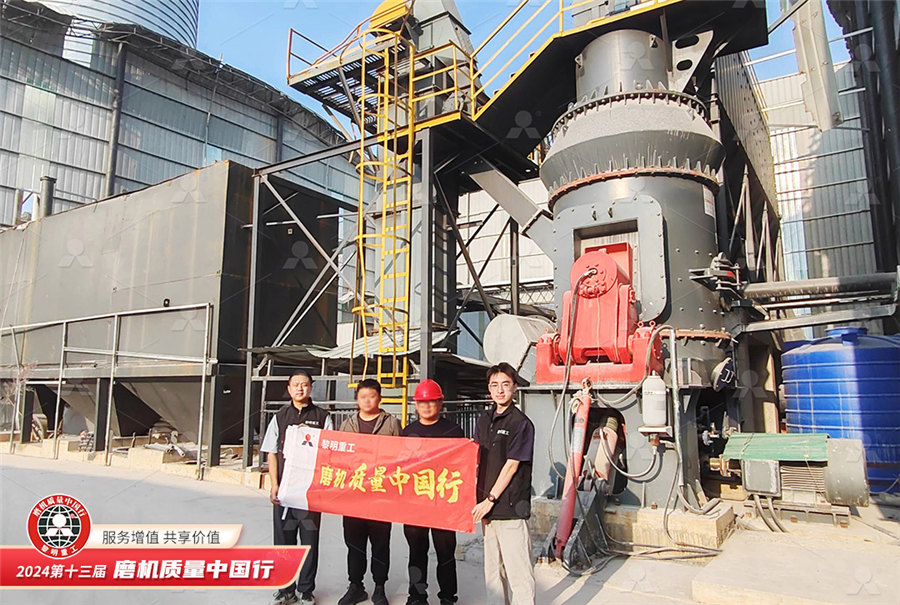
Everything you need to know about
In summary, the mill system limitations have more impact on production rates relating to weathered or stored clinker versus fresh clinker than does the grindability of the clinker itself A ball mill is optimised for certain conditions – if Clinker production was 526 million tonnes in 202021, up 2 per cent yearonyear but down 5 per cent over 201516 and 19 per cent below 201011 levels Clinker imports (including nonCIF member imports) were 396 million tonnes in 202021, a rise of 2 per cent yearonyear While imports are down 5 per cent over 201516 levels, Clinker imports are now more than double Production – CementThe cement clinker calcination is an important step in the cement production process It mainly occurs in cement kiln and can be roughly divided into six reaction stages, namely drying, preheating, chemical decomposition, exothermic reaction, sintering and coolingCement Clinker Calcination in Cement Production Process AGICO Cement The cost is for reference only and is subject to specific requirements Mini Cement Plant: A smallscale cement plant that spends around 100150 tons of cement per day could cost around $3 million to $4 million or even more, depending on the factors ; Medium Cement Plant: A mediumscale cement plant spends a few hundred tons to around 1000 tons of cement per day and How Much Does It Cost To Build A Cement Factory?

Cement Clinker Quality Control AGICO
In portland cement manufacturing process, the quality of cement clinker directly affects the quality of the finished product cement The following are several important factors affecting the cement clinker quality In the process of clinker production, strict control of these factors can ensure the production of highquality, highyield clinker 12021年5月24日 Large clinker nodules (Figure 2) are difficult to cool, transport and grind into cement Clinker should ideally have a smaller average nodule size and a narrow nodule size range More uniformly sized clinker is more evenly distributed into the cooler and has more consistent bed porosity, which enables more stable cooler and kiln operationBetter and cheaper cement: Optimising the right clinker 2019年9月27日 In general, we can divide the cement production line into three main steps: raw material preparation of cement, clinker production, and cement grinding Each step has some cement manufacturing machines, such as raw mill, cement crusher, cement mill, cement kiln, cement cooler, cement dryer, cement silo, cement packer, etcCement Euipment Overview Cement Making Machines Cement 2023年6月6日 Clinker Cooling – After leaving the kiln, the clinker is extremely hot Manufacturers must cool the clinker rapidly to ensure its physical properties They use air or water in specialized cooling units called clinker coolers Clinker Grinding – Cement machines such as ball mills or vertical rollers mills grind the cooled clinker into a Cement Clinker: Production, Composition, Types, and Impact
.jpg)
Cement and Clinker Production by Indirect
2022年9月21日 The study explores the indirect mechanosynthesis process for cement and clinker production, highlighting its impact on global cement output2019年4月23日 Introduction Portland cement underpins modern global development As such, it is the most abundantly produced material in the world (Deolalkar Citation 2016)The world has an abundance of the primary raw An overview of alternative raw materials used in The clinker cooler, also known as grate cooler or cement cooler, it is a necessary equipment of cement clinker productionThe clinker cooler is mainly used to cool and transport the cement clinker At the same time, cement cooler also Clinker Cooler, Cement Cooler, Grate CoolerAGICO Cement provides cement equipment of clinker production, including rotary kiln, preheater, and precalciner, start cement plant now! Skip to content +86 s about blog contact Find out single cement manufacturing machine of Clinker Production Clinker Plant Cement Plant Equipment
.jpg)
Effects and Control of Chemical Composition of Clinker for Cement
2020年10月15日 The objectives of this research were to obtain the chemical composition of cement clinker sample data after the xray diffraction (XRD) analysis from the quality control department of the two 2023年5月5日 The AAC block plant is not a single piece of equipment, but a production line composed of multiple aac block making machinery Generally, a complete AAC block production line includes 10 main equipment and 6 auxiliary equipment, such as a jaw crusher, ball mill, bucket elevator, slurry metering tank, computer control console, mixer, pouring machine, Cost Of Setting Up AAC Block Manufacturing Plant AGICO CEMENTClinker cooler serves two main objective of cooling clinker from temperature of about 1350 0C to the temperature (65150 0C) where it can be handled by conveyors like pan conveyors, chain, Elevators etc and heat recovery from hot clinker coming out of kiln A huge development has happened in clinker coolers designs and types as wellClinkerization Cement Plant OptimizationThis is where vertical roller mill technology comes in Vertical roller mill (VRM) is a grinding machine that has revolutionized the cement industry by enabling efficient and ecofriendly cement production This article will explore the application of vertical roller mills in the cement industry, including their benefits, efficiency, and eco Application of Vertical Roller Mill in Cement Production
.jpg)
CO2 Emissions Profile of the US Cement Industry US EPA
2015年9月10日 Cement production also is a key source of CO2 emissions, due in part to the significant reliance on coal and petroleum coke to fuel the kilns for clinker production Globally, CO2 emissions from cement production were estimated at 829 MMTCO2 in 2000 7, approximately 34% of global CO 2 emissions from fossil fuel combustion and cement production2024年9月16日 What is Cement Clinker? Cement clinker is an intermediary product produced during the manufacturing of cement It looks solid and dark grey in colour It is collected as lumps or nodules appear in 3mm to 25mm in diameter The cement clinker is produced by heating clay and limestone together at a temperature range of 1400 to 1500 degrees CelsiusCement Clinker: Its Types, Uses and Composition2024年11月23日 Cement Extraction, Processing, Manufacturing: Raw materials employed in the manufacture of cement are extracted by quarrying in the case of hard rocks such as limestones, slates, and some shales, with the Cement Extraction, Processing, Manufacturing4 天之前 Cement clinker is a nodular material that forms the basis of cement production It is produced by heating a mixture of limestone, clay and other materials at high temperatures in a kiln What role does cement clinker perform in cement production? Cement clinker acts as the main ingredient in the production of cementCement Clinker: Types and Uses of Cement Clinker JK Cement
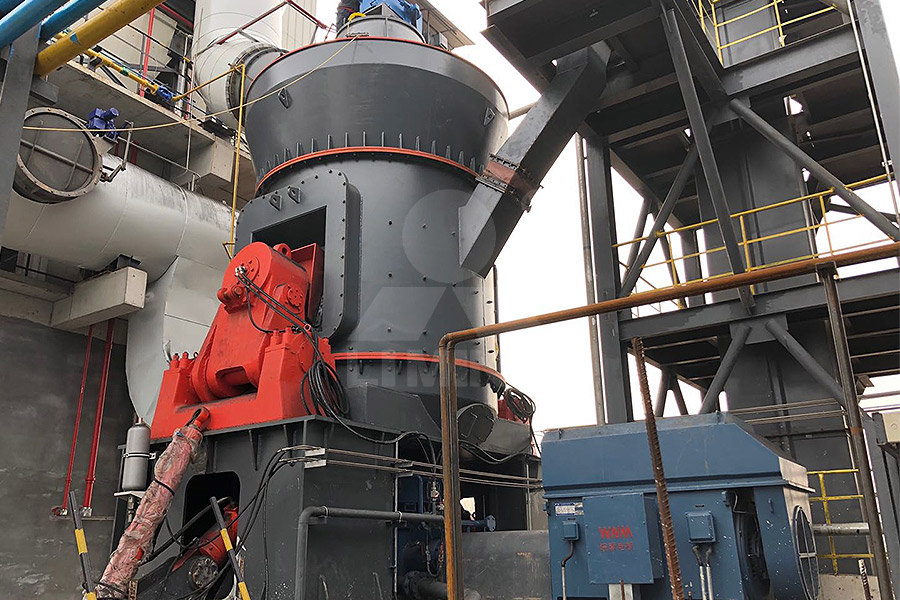
Deep decarbonisation of industry: The cement sector
2021年2月8日 By 2050, cement production in the EU is expected to remain below pre2010 levels, ranging between 165Mt and 206Mt in the FORECAST model scenarios (4), which fed the industry analysis of the European Commission’s LongTerm Strategic Vision (5) Process heat overview Clinker, and clinker substitutes, are the activeMobile Batching Plant AGICO CEMENT offers concret e batching plants in various models, including AGHZS35, AGHZS50, AGHZS60, AGHZS75, AGHZS90, AGHZS120, AGHZS180, AGHZS240, and AGHZS300, with different configurations If you want to know how much the specific cost of a concrete batching plant is, you first need to figure out how much output you How Much Does It Cost to Build a Concrete Batching Plant2024年11月16日 Extraction and Preparation of Raw Materials The main raw materials (limestone, clay chalk or basalt) are quarried from natural rocks They are crushed and transferred to preblending storage where other substances (such as sand, iron ore, bauxite, shale, slag, fly ash) are added to get the desired chemical compositionCement Clinker Manufacturing Process with Reactions2024年11月16日 Clinker is a nodular material produced in the kilning stage during the production of cement and is used as the binder in many cement products The lumps or nodules of clinker are usually of diameter 325 mm and dark grey in color It is produced by heating limestone and clay to the point of liquefaction at about 1400°C1500°C in the rotary kiln What is Cement Clinker? Composition, Types Uses
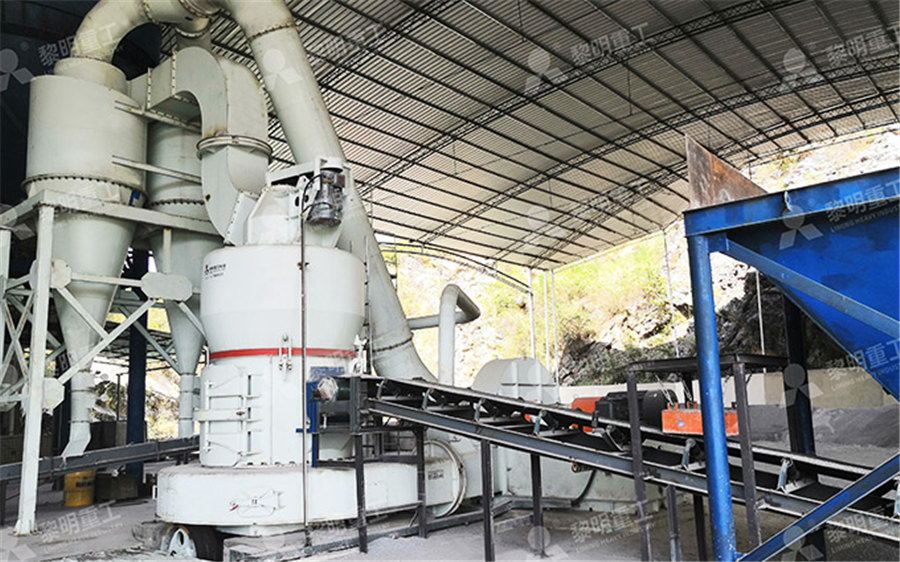
Understanding the Role of Clinker Grinding in Cement Production
2023年10月19日 Clinker is a critical component in the production of cement and forms the intermediate product during the cement manufacturing process It can be best described as a nodular material, usually grayish in color, which is produced by sintering limestone and aluminosilicate materials such as clay at high temperatures in a cement kilnAnd when the clinker strength is high, mixtures are added more, which can also increase the output of cement and reduce the cost and heat consumption So the calcination of cement clinker is the key process of cement production Among them, clinker kiln as the clinker production equipment is the core of the whole cement production lineCalcining Technology Of Clinker Kiln Cement Rotary KilnReaction (1), the decarbonation of limestone, is the cause behind the largest source of CO 2 emissions in cement production Thus, reducing the amount of CaO in the binder results directly in a reduction of CO 2 emissions The second one is the hydraulic ability, or reactivity, of the phases that are present in the CaOSiO 2 system Besides the main oxides, CaO and SiO 2, in their Alternative Clinker Technologies for Reducing Carbon 2020年3月1日 Manufacturing cement requires energy intensive processes; and consumes almost 15% of the total demand for energy in industry [3]On average, to produce one ton of cement, 34 GJ of thermal energy (in dry process) and 110 kWh of electrical energy are needed [4, 5]Furthermore, manufacturing a ton of cement releases 073–099 tons of CO2 [6] which A decision support tool for cement industry to select energy
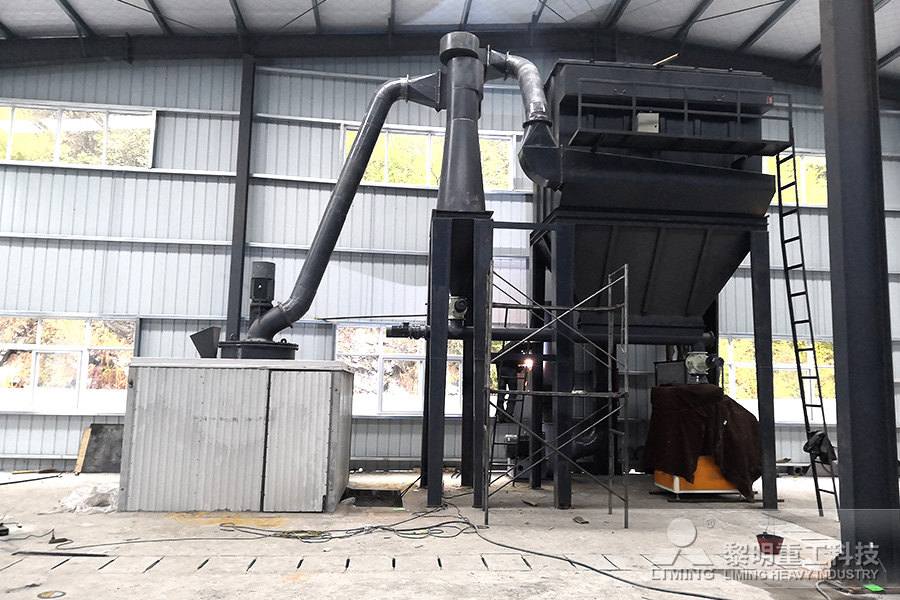
How Is Cement Produced in Cement Plants
The cyclone preheating system Phase IV: Calcination The calcination is the core phase of the cement making dry process The calcination of the preheated raw meal takes place in the rotary kiln of the cement plant The rotary kiln is a The shaft kiln is not so widely used in cement plant as rotary kiln, but its structure is simple, the space occupation is small so the investment is relatively low Besides, it has a long service life and can produce cement of stable quality, Cement Manufacturing Machine Cement In summary, the mill system limitations have more impact on production rates relating to weathered or stored clinker versus fresh clinker than does the grindability of the clinker itself A ball mill is optimised for certain conditions – if Everything you need to know about Clinker production was 526 million tonnes in 202021, up 2 per cent yearonyear but down 5 per cent over 201516 and 19 per cent below 201011 levels Clinker imports (including nonCIF member imports) were 396 million tonnes in 202021, a rise of 2 per cent yearonyear While imports are down 5 per cent over 201516 levels, Clinker imports are now more than double Production – Cement
.jpg)
Cement Clinker Calcination in Cement Production Process AGICO Cement
The cement clinker calcination is an important step in the cement production process It mainly occurs in cement kiln and can be roughly divided into six reaction stages, namely drying, preheating, chemical decomposition, exothermic reaction, sintering and coolingThe cost is for reference only and is subject to specific requirements Mini Cement Plant: A smallscale cement plant that spends around 100150 tons of cement per day could cost around $3 million to $4 million or even more, depending on the factors ; Medium Cement Plant: A mediumscale cement plant spends a few hundred tons to around 1000 tons of cement per day and How Much Does It Cost To Build A Cement Factory?In portland cement manufacturing process, the quality of cement clinker directly affects the quality of the finished product cement The following are several important factors affecting the cement clinker quality In the process of clinker production, strict control of these factors can ensure the production of highquality, highyield clinker 1Cement Clinker Quality Control AGICO2021年5月24日 Large clinker nodules (Figure 2) are difficult to cool, transport and grind into cement Clinker should ideally have a smaller average nodule size and a narrow nodule size range More uniformly sized clinker is more evenly distributed into the cooler and has more consistent bed porosity, which enables more stable cooler and kiln operationBetter and cheaper cement: Optimising the right clinker
.jpg)
Cement Euipment Overview Cement Making Machines Cement
2019年9月27日 In general, we can divide the cement production line into three main steps: raw material preparation of cement, clinker production, and cement grinding Each step has some cement manufacturing machines, such as raw mill, cement crusher, cement mill, cement kiln, cement cooler, cement dryer, cement silo, cement packer, etc2023年6月6日 Clinker Cooling – After leaving the kiln, the clinker is extremely hot Manufacturers must cool the clinker rapidly to ensure its physical properties They use air or water in specialized cooling units called clinker coolers Clinker Grinding – Cement machines such as ball mills or vertical rollers mills grind the cooled clinker into a Cement Clinker: Production, Composition, Types, and Impact