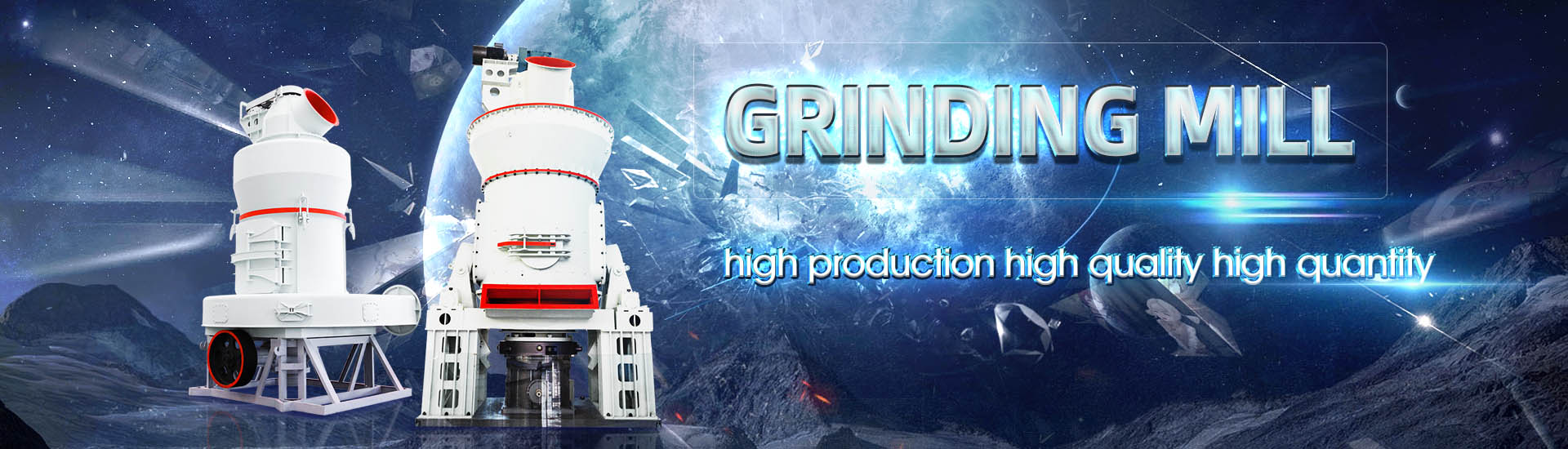
The function of the wearresistant ring on the grinding roller
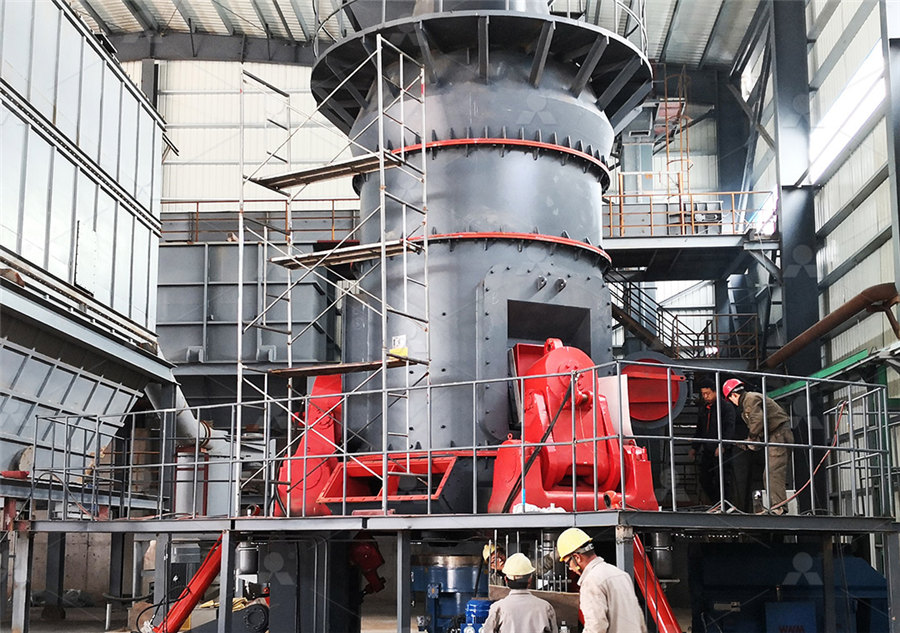
A novel PMwear protection method to meet high
2001年10月1日 Wear systems involved in the interparticle crushing of minerals in roll grinding (I: scratching; II: indentation) Because of the column of material located above the roller gap, the roller surface in Area I is scratched by the coarse mineral particles at a rate which is a function 2011年9月2日 The chemical compositions of such abrasion resistant wear parts are given in Table 1 These high chromium alloys are used in closed circuit dry grinding vertical roller mills Wear mechanism of abrasion resistant wear parts in raw 2011年9月2日 A laboratory scale vertical roller mill with a transparent roller/table has been developed to further understand the material movements during grinding The development of Wear mechanism of abrasion resistant wear parts in raw 2023年7月4日 action of centrifugal force and press the grinding ring on the inner wall of the casing to grind the The highpressure roller mill, also called the roller presser or the extrusion Roller Mill Springer
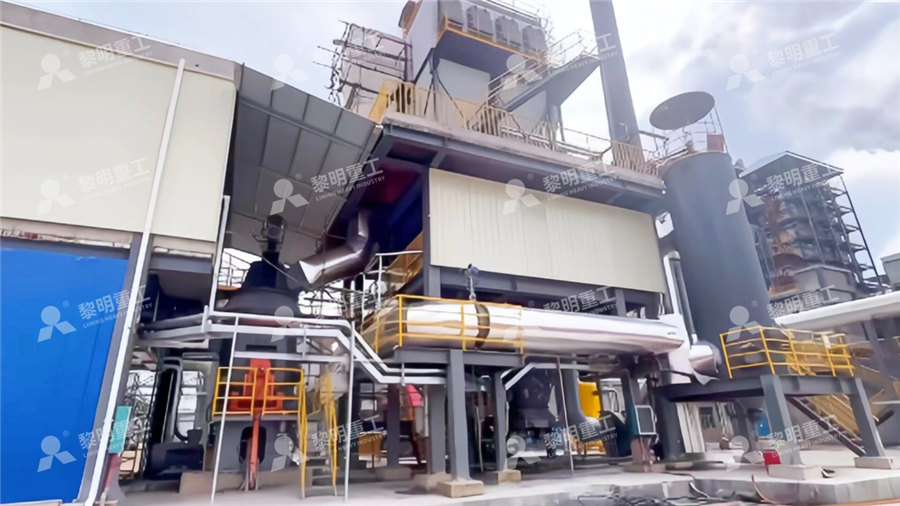
Wear mechanism of abrasion resistant wear parts in raw
2011年9月1日 The results showed that the wear resistance and crushing performance of the grinding roller with striped grooves were better than those of the smooth grinding roller for 2023年2月6日 To improve the wear resistance and mineral crushing performance of grinding rollers in cement, mining, and other engineering fields, a striped groove morphology was designed on the normal grinding roller surface Effect of the Bionic Transverse Stripe on Wear 2021年4月7日 In the magnetic grinding method, the rotational speed of the outer grinding ring affects the frequency of the magnetic field, resulting in a change in the rotational speed and an Properties of grinding tool material for doubledisc straight 2023年5月8日 In this paper, the wear resistance values of the original surface of the detection roller and the restored surface of the grinding roller are experimentally compared, and the influence of the reduction of the Study on Wear Resistance Evolution of Cold
.jpg)
(PDF) Wear of hot rolling mill rolls: an overview
1994年8月1日 Wear variables and modes are reviewed along with published methods and models used in the study and testing of roll wear This paper reviews key aspects of roll wear control — roll material2002年8月1日 Request PDF Wear resistance of PVDcoatings in roller bearings To what extent PVDcoatings are able to take over the function of EP/AWadditives, was systematically examined on the basis of Wear resistance of PVDcoatings in roller bearings2024年6月4日 Cast iron has good wear resistance, corrosion resistance, thermal stability, sand embedding performance, high hardness and strength, as well as good processing performance, also easy to shape, with a great cost performance [1,2,3]Therefore, cast iron is widely used as a grinding tool material in the ultraprecision manufacturing field []However, the geometric Study on the Friction and Wear Properties of Cast Iron Under June 2022; ARCHIVE Proceedings of the Institution of Mechanical Engineers Part C Journal of Mechanical Engineering Science 19891996 (vols 203210) 236(2):1107(PDF) A comprehensive review on the grinding process:
.jpg)
A novel PMwear protection method to meet high
2001年10月1日 Highpressure grinding roller presses have been used to an increasing extent in recent years for grinding cement because of their better energy utilization wearresistant, roller surface is generated by a special combination and distribution of two A widespread method employed is the buildup welding of rolled steel rings as well as 2023年8月14日 Abstract— Roller bearings with crossed rollers are actively used in the swivel mechanisms of manipulators and other units due to the combination of high rigidity and increased load capacity When designing new mechanisms, an important characteristic is the resistance moment, the value of which can be significantly influenced by operating conditions, such as Experimental Evaluation of the Cross Roller Bearing Resistance 2023年12月21日 where C is the density of the grinding grain and r is the widthtothickness ratio of the chip In Malkin’s model, the maximum UCT was based on the uniform location distribution and grain size Under these assumptions, the calculated UCT was estimated to be 02~1 μm [], 06 μm [] or 03~098 μm [], and less than the critical depth of plowingcutting transition (1~2 A multiscale model revealed in the grinding process and its 2024年4月30日 The dynamic balance between deformation inhibition and high quality in rough grinding was studied, and the optimal parameters for thinwalled bearing outer ring grinding were obtained(PDF) Investigation on the Deformation and Surface
.jpg)
Properties of grinding tool material for doubledisc straight
2021年4月7日 The doubledisc straightgroove (DDSG) grinding method is a new precision machining approach employed for the rolling surface of bearing rollers The friction coefficient and wear resistance of grinding disc materials affect the grinding performance due to the operation on the workpiece However, relevant research on DDSG is rather limited currently Therefore, we 2017年4月1日 In the airswept mode, the verticalrollermill and a high efficiency dynamic classifier are suited above each other as a single unit (Fig 1) Material is fed to the grinding chamber and transported by table rotation to the grinding gap between the fixed grinding rollers and the mill table Crushing and grinding take place by compressive grindingOperational parameters affecting the vertical roller mill 2016年10月5日 In this chapter an introduction of widely applied energyefficient grinding technologies in cement grinding and description of the operating principles of the related equipments and comparisons over each other in terms of grinding efficiency, specific energy consumption, production capacity and cement quality are given A case study performed on a EnergyEfficient Technologies in Cement Grinding2021年12月14日 The characteristic of corrosion resistance of grinding is revealed based on the association of grinding mechanism and electrochemical theory from the inner part due to the coupling function Experiment study on the corrosion resistance of the surface metamorphic
.jpg)
(PDF) Influence of hardness on the wear
2008年8月1日 Present work aimed at investigating the wear resistance of AISI 630 (UNS S17400) or 174 PH stainless steel hardened by precipitation hardening or aging at various hardness levels2023年5月8日 Seamless flatness rollers are the core equipment for coldrolled strip flatness detection The change in wear resistance of the roller surfacestrengthened layer has important guiding significance for the prediction of the Study on Wear Resistance Evolution of Cold 2024年4月13日 Multiple advantages, such as good formability, high specific strength, excellent thermal conductivity, and high corrosion resistance, enable aluminum alloy wide application in various fields; however, low surface hardness and poor wear resistance limit its further development In this study, three surface modification coatings were successfully prepared on Improving the Wear Resistance Properties of 7A04 2024年3月4日 In order to comprehend the abrasive wear mechanism of CBN grinding wheels with varying structural characteristic parameters, the influence of these parameters on abrasive wear was transformed into the impact of undeformed chip thickness on abrasive wear Subsequently, a twodimensional finite element simulation model of single CBN abrasive Research on the Wear of Groove Structured Grinding Wheel
.png)
(PDF) A discussion on the measurement of grinding media wear
2016年2月1日 Wet grinding can also add a corrosive component to total wear mechanism, and then wear rates are expected to rise from synergies between corrosive and abrasive components2023年11月1日 Grinding is an important part of precision manufacturing, and grinding wheel wear is a crucial factor affecting the processing quality It will be of great significance to monitor the grinding wheel wear status in realtime and provide timely warnings during processing To realize the realtime and effective monitoring of grinding wheel wear, a new grinding wheel Electrostatic induction–based online monitoring of grinding wheel wear 2010年4月1日 Rolling contact wear and rolling contact fatigue during rolling bearing operation can be diagnosed by combining measured and interpreted condition monitoring data with theory, and conclusions Rolling Contact Fatigue and Wear Fundamentals for Rolling 2024年3月12日 Reliable prediction of the grinding force is essential for improving the grinding efficiency and service life of the grinding head To better optimize and control the grinding process of the grinding head, this paper proposes a grinding force prediction method of the grinding head that combines surface measurement, statistical analysis, and finite element method (FEM) Prediction and analysis of grinding force on grinding heads
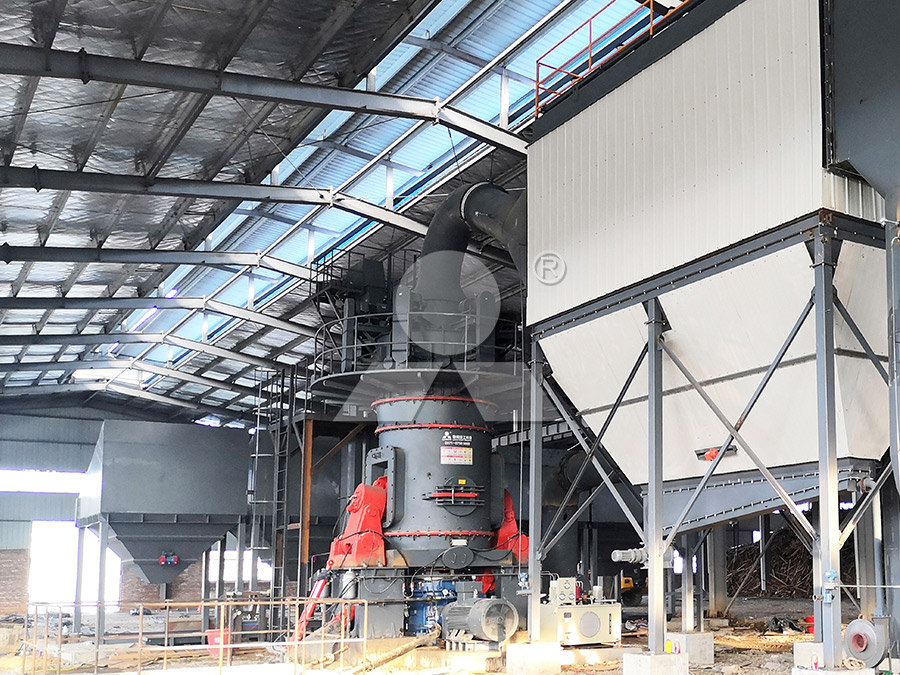
Wear mechanism of abrasion resistant wear parts in raw
2011年9月2日 The VRM is a commonly known grinding unit in the cement industry The VRM sizes range from approx 2 to 6 m in table diameter, and depending on the VRM size, the feed material will vary between pebble sized rocks in small VRMs and Ø150 mm fragments in large VRMsThe final product will typically be classified/separated at 12% + 90 μmContrary to 2022年12月23日 In order to study the friction and wear properties of cast iron in free grinding environment under the condition of line contact, this paper presented a new method to calculate the friction coefficient by measuring the friction torque Through the selfdeveloped free abrasive grinding experimental device in line contact condition, this work carried out friction and wear Study on friction and wear properties of cast iron material in 2024年2月24日 The coarsegrained electroplated diamond grinding wheels is increasingly favored in precision grinding of hard and brittle materials owing to its high material removal efficiency, high wear resistance and steady surface Research on the Grinding Performance of an 2023年6月20日 As the working interface of tapered roller bearing, the raceway surface quality directly affects the working performance and service life of bearings In order to improve the surface quality of tapered roller bearing inner raceway grinding, improve the processing efficiency, and optimize the processing parameters, this paper conducted a study on the surface Surface roughness in grinding outer ring inner raceway of
CFB石灰石脱硫剂制备64.jpg)
A review on the wear of oil drill bits (conventional and the
2018年8月1日 It is concluded that abrasion wear is the main dominant type of wear occurring in rollercone bits, which is caused by the process of ploughing when the abrasive rocks are soft like limestone, while the process of microploughing and microcutting are the main cause of abrasive wear of rollercone bits when abraded against hard formations such 2012年4月1日 Grinding of metals is a complex material removal operation Research on cutting process of a single abrasive grain is the basis of further understanding of grinding mechanismResearch on the Grinding Mechanism Based on the Cutting Simulation2021年5月1日 The hardness and wear resistance of rollerburnished 316L stainless steel has been tested in [22] The design of the experiment analysis indicated that burnishing force was the most important Hardness and wear resistance of roller burnished 316L stainless steel2021年3月24日 1 Introduction Tribology is the study of friction, wear, and the lubrication of interacting surfaces As one of the critical tribological domains and a persistent phenomenon regarding the deformation, damage and/or removal of material at contact surfaces, wear greatly affects the lifetime of mechanical components from the nanoscale to the macroscale []Recent Progress on Wear‐Resistant Materials: Designs,
.jpg)
Wear test and antifriction mechanism analysis of bionic
2018年11月1日 Analysis of the wear resistance mechanism of bionic grinding roller suggests that, the stripe structure makes the grinding roller contact with the quartz sand more fully and evenly, and the 2004年3月1日 The grinding experiments of zirconia toughened mullite composites (ZTM) using diamond wheels were carried out in this paper The causes of ground surface defects and surface phase transformation Effects of Grinding on the Wear Resistance of ZTM Composites2019年12月26日 A threedimensional finite element model of rail grinding was established to explore the effects of grinding passes and grinding direction on the material removal behaviour of grinding rails (PDF) The wear resistance research of the rail contact surface 2002年8月1日 Request PDF Wear resistance of PVDcoatings in roller bearings To what extent PVDcoatings are able to take over the function of EP/AWadditives, was systematically examined on the basis of Wear resistance of PVDcoatings in roller bearings
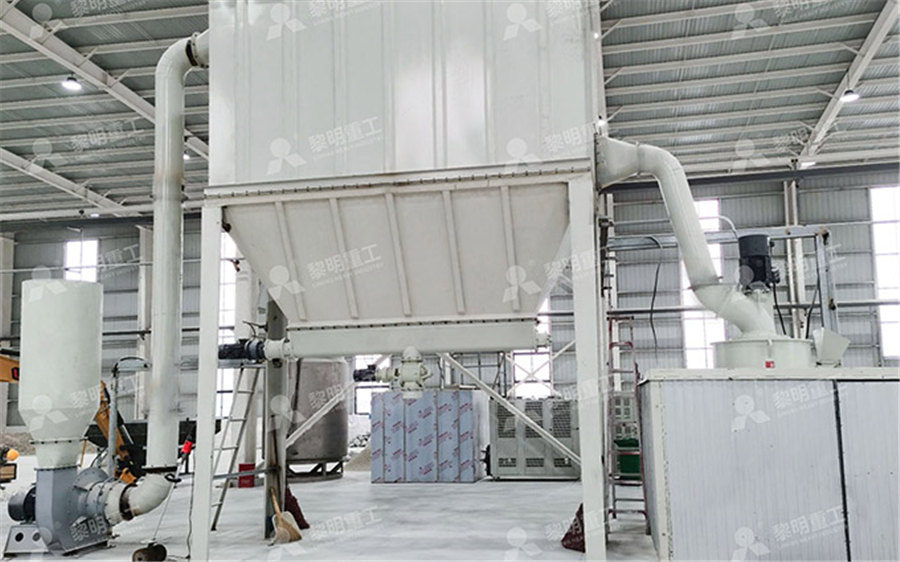
Study on the Friction and Wear Properties of Cast Iron Under
2024年6月4日 Cast iron has good wear resistance, corrosion resistance, thermal stability, sand embedding performance, high hardness and strength, as well as good processing performance, also easy to shape, with a great cost performance [1,2,3]Therefore, cast iron is widely used as a grinding tool material in the ultraprecision manufacturing field []However, the geometric June 2022; ARCHIVE Proceedings of the Institution of Mechanical Engineers Part C Journal of Mechanical Engineering Science 19891996 (vols 203210) 236(2):1107(PDF) A comprehensive review on the grinding process: 2001年10月1日 Highpressure grinding roller presses have been used to an increasing extent in recent years for grinding cement because of their better energy utilization wearresistant, roller surface is generated by a special combination and distribution of two A widespread method employed is the buildup welding of rolled steel rings as well as A novel PMwear protection method to meet high2023年8月14日 Abstract— Roller bearings with crossed rollers are actively used in the swivel mechanisms of manipulators and other units due to the combination of high rigidity and increased load capacity When designing new mechanisms, an important characteristic is the resistance moment, the value of which can be significantly influenced by operating conditions, such as Experimental Evaluation of the Cross Roller Bearing Resistance
.jpg)
A multiscale model revealed in the grinding process and its
2023年12月21日 where C is the density of the grinding grain and r is the widthtothickness ratio of the chip In Malkin’s model, the maximum UCT was based on the uniform location distribution and grain size Under these assumptions, the calculated UCT was estimated to be 02~1 μm [], 06 μm [] or 03~098 μm [], and less than the critical depth of plowingcutting transition (1~2 2024年4月30日 The dynamic balance between deformation inhibition and high quality in rough grinding was studied, and the optimal parameters for thinwalled bearing outer ring grinding were obtained(PDF) Investigation on the Deformation and Surface2021年4月7日 The doubledisc straightgroove (DDSG) grinding method is a new precision machining approach employed for the rolling surface of bearing rollers The friction coefficient and wear resistance of grinding disc materials affect the grinding performance due to the operation on the workpiece However, relevant research on DDSG is rather limited currently Therefore, we Properties of grinding tool material for doubledisc straight 2017年4月1日 In the airswept mode, the verticalrollermill and a high efficiency dynamic classifier are suited above each other as a single unit (Fig 1) Material is fed to the grinding chamber and transported by table rotation to the grinding gap between the fixed grinding rollers and the mill table Crushing and grinding take place by compressive grindingOperational parameters affecting the vertical roller mill
.jpg)
EnergyEfficient Technologies in Cement Grinding
2016年10月5日 In this chapter an introduction of widely applied energyefficient grinding technologies in cement grinding and description of the operating principles of the related equipments and comparisons over each other in terms of grinding efficiency, specific energy consumption, production capacity and cement quality are given A case study performed on a