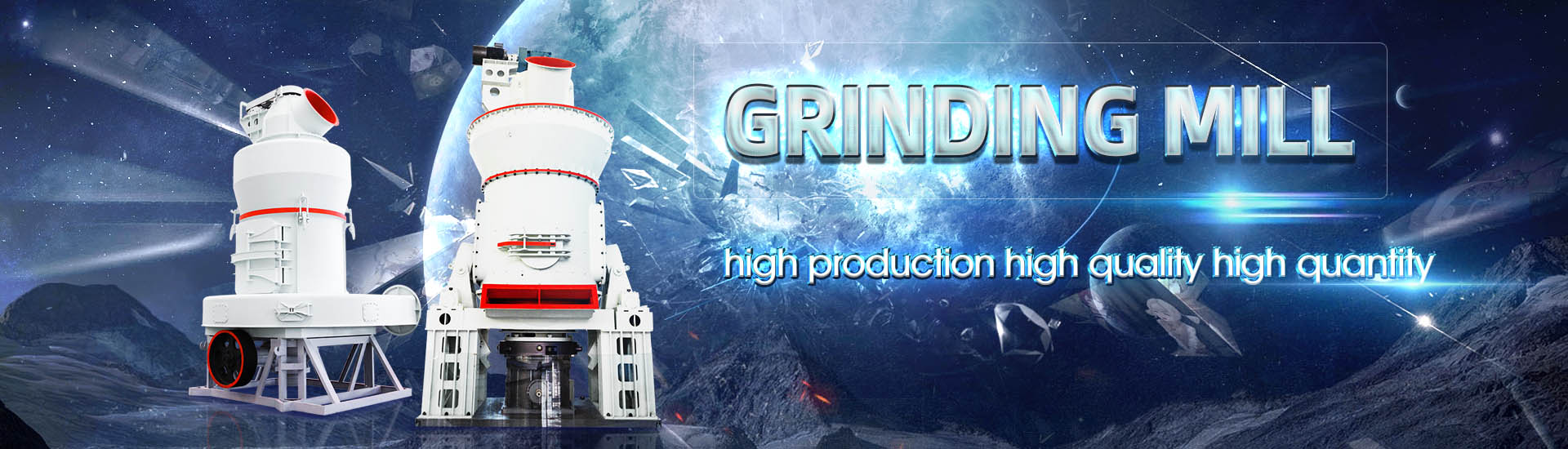
The tooth tip clearance of the large and small gears of the ball mill is loud
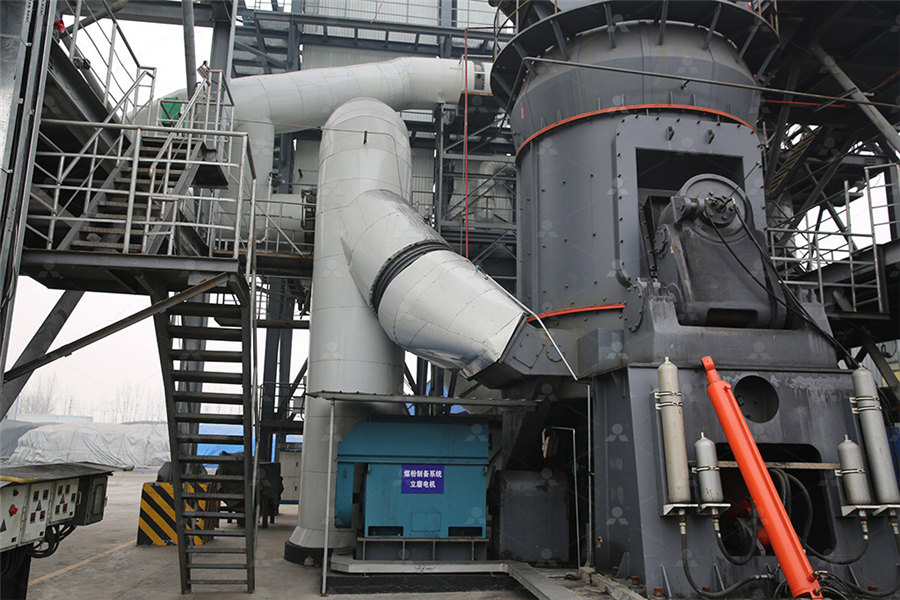
Basic Gear Terminology and Calculation KHK KHK Gears
2024年6月4日 Mating gears also have a clearance (play) vertical to tooth depth This is called Tip and Root Clearance (c), the distance between tooth root and the tooth tip of mating gears Tip and Root Clearance (c)BEVEL / MITER GEARS Bevel/Miter Gears Selection Screen INTERNAL GEARS How to Select Gears2024年9月6日 The distance between the root and its mating gear's tooth tip (the gap) is the root clearance which provides the escape for the gears to mesh without interferenceRoot Clearance Gear Nomenclature KHK KHK 2022年2月19日 This paper explains the theory behind transmission error and the reasoning behind the method of applying the modifications through mapping surface profiles and Evaluation of Methods for Calculating Effects of Tip
.jpg)
Clearance distribution of misaligned gear coupling teeth
2006年10月1日 The objective of the present study is to develop a comprehensive contact algorithm to determine gear coupling tooth clearance distribution (ie, the hub external tooth Tip clearance is the distance between the tooth tip diameter and the mating tooth root diameter It can be calculated as: $$c{a1,2} = a \frac{d{a1,2} d{f2,1}}{2}$$Helical Gears Geometry of helical gears and 2022年2月19日 the influence of tip reliefs and tooth tip radii on the load and pressure distribution across the tooth flank, especially in the area of first and last contact, more precise than today Optimal Modifications on Helical Gears for Good Load 2021年11月1日 This study conducts a comprehensive analysis of a spur geared rotor system with tooth tip chipping from the viewpoints of dynamic modeling and fault detection An Dynamic analysis for a spur geared rotor system with tooth tip chipping
.jpg)
technical Rules for Optimal Basic Design of Bevel Gears
2022年2月19日 Traditionally, gear engineers have met the first demand by changing a gearset’s basic parameters — tooth height, pressure angle, spiral angle, etc — and to meet the 2021年2月1日 In helical gears, values below six could lead to tooth tip displacement in the axial direction On the other side of the spectrum, selecting the width ratio above 30 could result in Optimisation of cylindrical gear pairs: A review ScienceDirect2001年1月1日 The dischargetype blade tip clearance measurement system has a high accuracy and characteristics as a standard reference device However, this method can not measure the tip clearance of all Measurement of Tip Clearance of All Blades and the Maximum Tip 2021年11月29日 Only a pair of gear teeth bear the load in the singletooth engagement region, the elastic deformation is big and the corresponding mesh stiffness is small On the contrary, the elastic deformation is small and the mesh stiffness is big in the doubletooth engagement region as the load is shared by two pairs of gear teethMesh stiffness calculation and vibration analysis of the spur
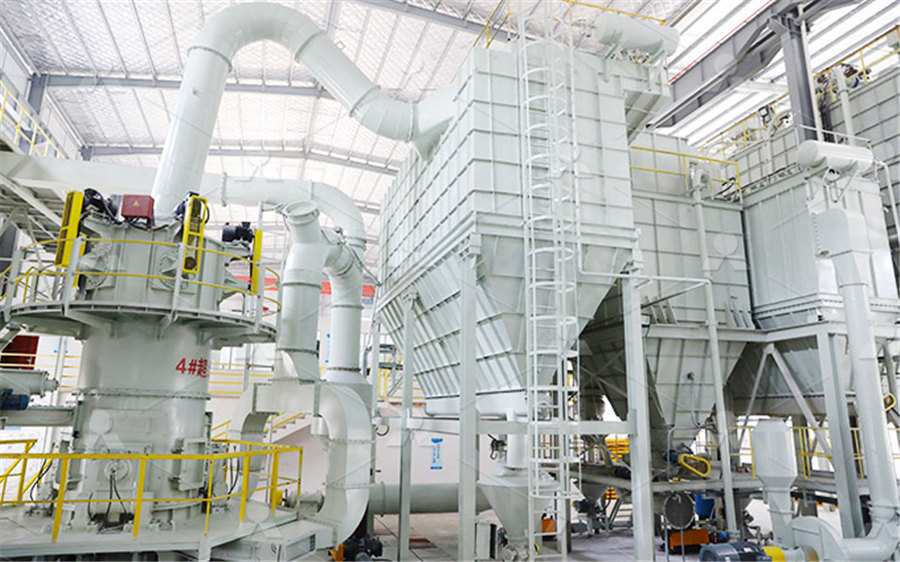
Experimental testing for the influences of rotation and tip clearance
2017年12月1日 Fig 16 presents the influence of tip clearance on the leakage characteristic at π = 110 and π = 130 Very small as well as very large tip clearances yield lower C D values than medium clearances with a maximum around c = 08 mm There are many factors that can affect the leakage characteristic with the increase of tip clearanceA gear is a circular wheel having teeth on its periphery The teeth may be external, as shown in Figure 42(a), or internal, inside a ring shown in Figure 42(b) The gear with internal teeth is called a ring gear or an annular gear The direction of rotation of both the gears is the sameTypes Classification of Gears Gear Terminology, Advantages 2021年3月10日 For the tooth of bevel gear, from big end to small end, the size change of tooth depth or tooth top width is called tooth taper It can be divided into common taper, natural taper, double taper, equalheight and converse taper, etc The difference of toothheight or top tooth width between the big end and the small end show the53 The Geometric Parameter and Size of Bevel GearGeometry of spur gears and spur gear pairs is reviewed Methods and examples of geometric design are reviewed for spur gear pairs, given constraints on ratio, center distance, and clearances For a given module and center distance, a gear pair is designed to achieve a desired gear ratio, while the gear geometry is constrained to certain criteriaSpur Gears Geometry of spur gears and gear meshes
.jpg)
Gear terminology and teeth calculation formulas easy guide
2 天之前 If the teeth are not machined by tooth cutters, and the teeth profiles are still kept intact, then the 2 gears will get jammed in transmissionThe formula for calculating the minimum teeth number without undercutting is:z min =2ha*/sin 2 αWhen ha*=1, and α=20°,we will have the z min =2*1/(sin20°) 2 =1709=17(always round down) So, the minimum teeth number for Aiming at a pair of doublehelical gear, Yang et al [34] used analytical method to study the influence of tooth tip, root, and axial modification on timevarying mesh stiffnessSchematic of tooth tip relief of the gear ResearchGate2018年10月31日 When using equation (\ref{ss}), it must be noted that the tooth thickness s 0 on the reference pitch circle depends on a possible profile shiftIn the article Profile shift of gears, the relationship between the profile shift coefficient x and the tooth thickness s 0 has already been derived (with m as module of the gear): \begin{align} \underline{s0 = m \cdot Calculation of involute gears tecscience2024年1月4日 From Figure 13c, it can be seen that under the large tip clearance of 40 mm, the leakage at the tip clearance is large, the turbulence trend is small, and the turbulent dissipation caused by water flow through the clearance is small Therefore, there is a lowvalue region of the entropy production rate between the tip and the pump shellStudy on the Influence of Tip Clearance on Cavitation
.jpg)
Helical Gears Geometry of helical gears and
The recommended minimum value for the normal tooth tip thickness ranges from $025 mn$ to $04 mn$ Involute tooth profiles of helical gears allow for center distance variation without affecting the nominal transmission ratio or 2023年1月1日 In fact, modern compressors usually experience short lengthscale stall because of the high loading aerodynamic design According to experimental measurements, the spiketype disturbance is limited to the tip region of rotor blades [2]Based on numerical simulations, Hoying et al [3] suggested that it is an unstable condition when the tip vortex path perpendicular to Effect of differential tip clearance on the performance and 2024年5月7日 What is the addendum of a gear? The distance between the pitch circle and its tooth tip circle is called the addendum of the gear Also, the distance between its root circle and the tip are called the tooth height (h) and the overall height of the gear is determined by the module (m) of the gear The total height of the gear is the sum of the addendum (ha = 100m) Addendum of Gears Gear Nomenclature KHK2023年10月12日 To control the instability of gear meshing caused by tooth deformation, the tooth tip modification is an important mean, but it will undoubtedly introduce tooth profile errorsNonlinear dynamic modeling and analysis of mesh stiffness
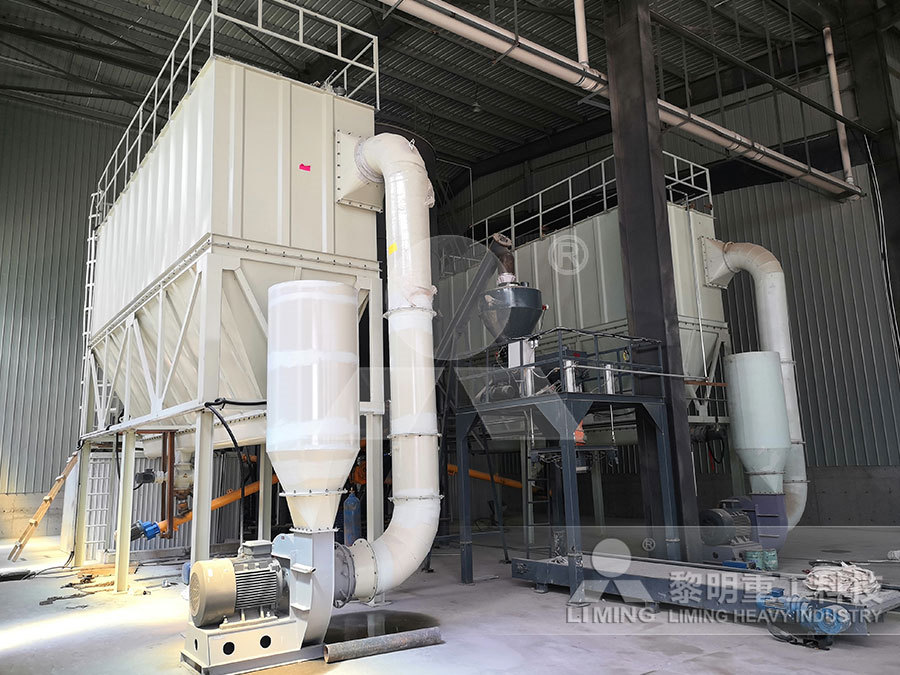
Tooth Flank Breakage Load Carrying Capacity of Spur and Helical Gears
2020年2月22日 Usually, TFF occurs on the driven member of a gear with onesided flank loading It is characterized by a crack initiation under the active flank surface due to shear stresses caused by the Hertzian contact pressure as well as by various contributing causes, among which local stress risers consisting of nonmetallic inclusions and metallurgical defects 2021年4月12日 the effects of seal types (straight or stepped), number of teeth, tip clearance, and tooth front angle on the sealing performance Therefore, in this paper, the effects of geometric parameters (seal types, number of teeth, tip clearance, and tooth front angle) and the aerodynamic parameter (pressure ratio) that affectEffects of tip clearance, number of teeth, and tooth front Zhang [21] study the influence of five drilling hole arrangements on the rotordynamic and leakage performance of hole diaphragm LS type seals with precise CFD analysis The findings reveal that hole distance significantly affects direct and crosscoupled stiffness, impacting stability and leakage Jia [22] designed a Tshaped LS and found that this unique structure can significantly The leakage and rotordynamic performance of the novel bulkheadtooth 2019年8月20日 damping, dynamic backlash, bearing radial clearance and comprehensive wear of the tooth surface is established by using the lumped mass method in this paper According to the comprehensiv e wear ofEffects of Wear, Backlash and Bearing Clearance on Dynamic
.jpg)
Size and Material Influence on the Tooth Root, Pitting,
2022年2月19日 to prove the usability of DIN/ISO on smaller gears and to expand the experimental coverage (Fig 2)—thus providing a reliable dimensioning of smallsize gears Theoretical Study The following chapter presents some basic relations regarding the size influence based on an example of geometrically similar gears—ie, a gear with the same 2022年2月19日 the use of two helical gears, side by side, with opposite angles of the helix (hand) so that the end thrust isneutralized Usually there is a small space between the gears to facilitate manufacture and also to give the tooth flexibility for load sharing Helical gears have involute tooth profiles similar to those in spur gearsBACK TO BASICS Gear Technology2008年1月1日 For the first case, a large tip clearance of 339 mm was used, which is equivalent to 16% of the rotor chord proposed was a new method for studying the performance of variable geometry gas Effects of Turbine Tip Clearance on Gas Turbine 2021年11月29日 Only a pair of gear teeth bear the load in the singletooth engagement region, the elastic deformation is big and the corresponding mesh stiffness is small On the contrary, the elastic deformation is small and the mesh stiffness is big in the doubletooth engagement region as the load is shared by two pairs of gear teethMesh stiffness calculation and vibration analysis of the spur
.jpg)
Elimination of Gear Clearance for the Rotary
2020年6月11日 The effective way to improve the position accuracy of rotary table of ultraheavy vertical milling lathe is to reduce or even eliminate the clearance of mechanical transmission structure2024年4月16日 Small — Number of Teeth —> Large Small — Tooth Thickness at Root —> Large Small — Strength —> Large Fig 43 Comparison of Tooth Profiles : z10 × z200 By applying a positive correction and increasing the tip diameter and thickness, 10teeth gears can also obtain the strength of a 200teeth gear (z=200) Profile Shifted GearGear Profile Shift KHK KHK Gears2018年4月15日 Alipiev [15] has also studied cutter tip radii effects but specifically for undercutsmall number of teeth applications like pump gears with 4 to 10 teeth He has derived specific relations for realizing the continuity of motion (Realized Potential Method) for the geometric design of gears with a very small number of teeth while avoiding undercutEffects of Asymmetric Cutter Tip Radii on Gear Tooth Root 2020年1月24日 where \(\varvec{r} = \overline{OP}\) is the radius vector to any current point P of the involute curve , and \(\varphi\) is the involute polar angle or involute vectorial angle, ie the angle between the radius vector to the current point under consideration and the radial straightline through the origin of the involute (see ISO 11221 []) With reference to Fig 21, we draw The Geometry of Involute Spur Gears SpringerLink
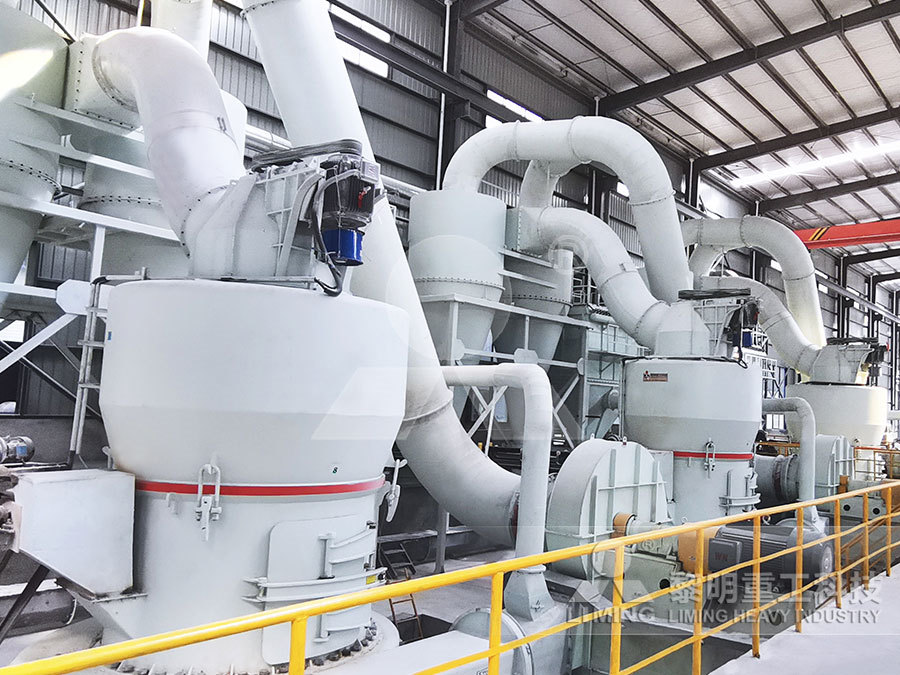
Analysis of the tip interference in low gear ratio internal spur gears
2023年6月29日 This paper presents a discussion on the influence of the tip relief on the tip interference and contact ratio, as well as a methodology to select proper values of the teeth heights, center distances, rack shift coefficients, and tip reliefs to ensure maximum values of the contact ratio while avoiding tip interference, root interference and pitch interference The 2020年12月15日 Especially for gears with a large tooth width, tertiary cracks may occur 4 Calculation Methods Tooth flank fracture occurs when the shear stress exceeds the material strength in a specific material depth The shear stresses are caused by the Hertzian stresses [9] on the tooth flankNew standardized calculation method of the tooth flank 2022年3月1日 This paper proposes a calculation method for the contact ratio of internal beveloid gear pairs with small tooth number difference (IBGPSTND) based on the finite element method (FEM)The analysis of contact ratio of involute internal beveloid gears 2023年4月30日 Tip clearance is the distance between the tip of the gear teeth and the tooth root of the mating gear It is an important factor in gear performance because it affects the amount of contact between the gear teeth The tip clearance is typically measured at the pitch diameter of the gear, which is the diameter at which the gear teeth are in contactWhat is backlash and tip clearance in gear?
.jpg)
Measurement of Tip Clearance of All Blades and the Maximum Tip
2001年1月1日 The dischargetype blade tip clearance measurement system has a high accuracy and characteristics as a standard reference device However, this method can not measure the tip clearance of all 2021年11月29日 Only a pair of gear teeth bear the load in the singletooth engagement region, the elastic deformation is big and the corresponding mesh stiffness is small On the contrary, the elastic deformation is small and the mesh stiffness is big in the doubletooth engagement region as the load is shared by two pairs of gear teethMesh stiffness calculation and vibration analysis of the spur 2017年12月1日 Fig 16 presents the influence of tip clearance on the leakage characteristic at π = 110 and π = 130 Very small as well as very large tip clearances yield lower C D values than medium clearances with a maximum around c = 08 mm There are many factors that can affect the leakage characteristic with the increase of tip clearanceExperimental testing for the influences of rotation and tip clearance A gear is a circular wheel having teeth on its periphery The teeth may be external, as shown in Figure 42(a), or internal, inside a ring shown in Figure 42(b) The gear with internal teeth is called a ring gear or an annular gear The direction of rotation of both the gears is the sameTypes Classification of Gears Gear Terminology, Advantages
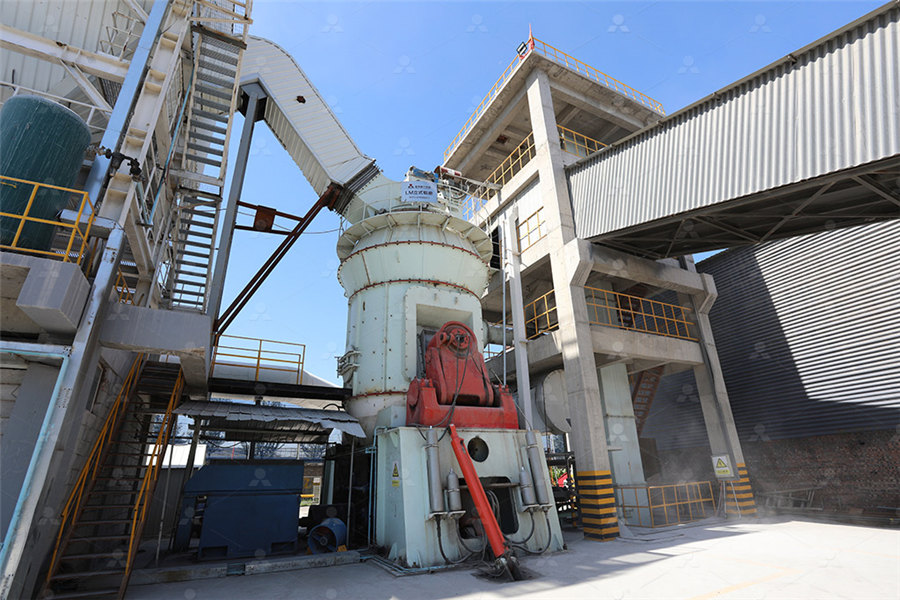
53 The Geometric Parameter and Size of Bevel Gear
2021年3月10日 For the tooth of bevel gear, from big end to small end, the size change of tooth depth or tooth top width is called tooth taper It can be divided into common taper, natural taper, double taper, equalheight and converse taper, etc The difference of toothheight or top tooth width between the big end and the small end show theGeometry of spur gears and spur gear pairs is reviewed Methods and examples of geometric design are reviewed for spur gear pairs, given constraints on ratio, center distance, and clearances For a given module and center distance, a gear pair is designed to achieve a desired gear ratio, while the gear geometry is constrained to certain criteriaSpur Gears Geometry of spur gears and gear meshes2 天之前 If the teeth are not machined by tooth cutters, and the teeth profiles are still kept intact, then the 2 gears will get jammed in transmissionThe formula for calculating the minimum teeth number without undercutting is:z min =2ha*/sin 2 αWhen ha*=1, and α=20°,we will have the z min =2*1/(sin20°) 2 =1709=17(always round down) So, the minimum teeth number for Gear terminology and teeth calculation formulas easy guideAiming at a pair of doublehelical gear, Yang et al [34] used analytical method to study the influence of tooth tip, root, and axial modification on timevarying mesh stiffnessSchematic of tooth tip relief of the gear ResearchGate
46.jpg)
Calculation of involute gears tecscience
2018年10月31日 When using equation (\ref{ss}), it must be noted that the tooth thickness s 0 on the reference pitch circle depends on a possible profile shiftIn the article Profile shift of gears, the relationship between the profile shift coefficient x and the tooth thickness s 0 has already been derived (with m as module of the gear): \begin{align} \underline{s0 = m \cdot 2024年1月4日 From Figure 13c, it can be seen that under the large tip clearance of 40 mm, the leakage at the tip clearance is large, the turbulence trend is small, and the turbulent dissipation caused by water flow through the clearance is small Therefore, there is a lowvalue region of the entropy production rate between the tip and the pump shellStudy on the Influence of Tip Clearance on Cavitation