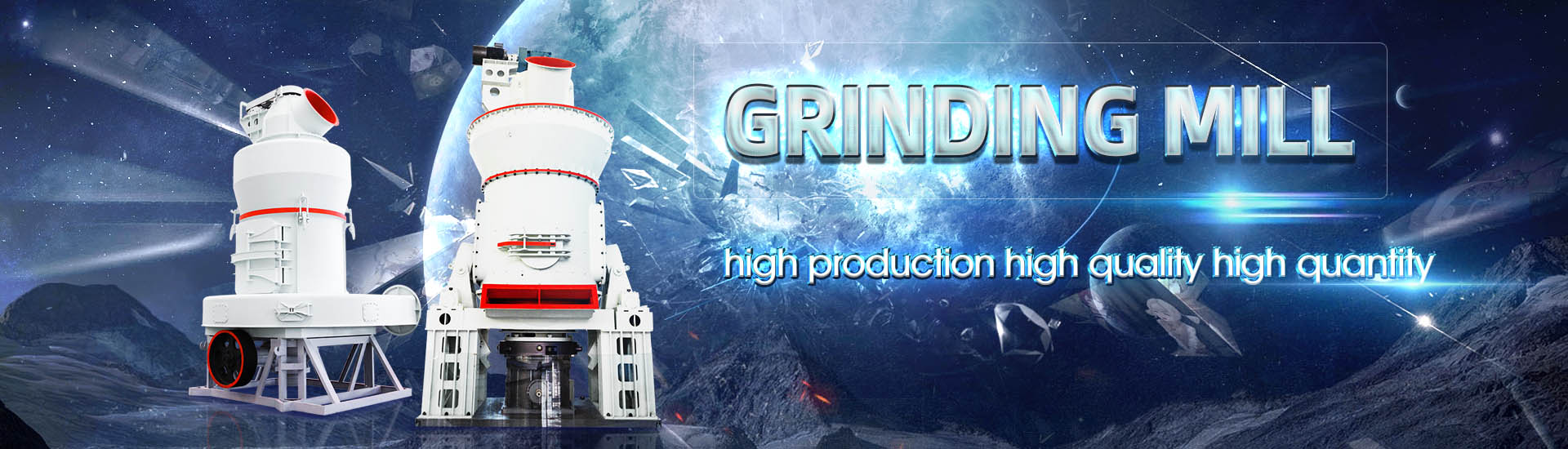
Main faults and solutions of imported MBF24.0 coal mill
.jpg)
进口MBF240型磨煤机主要故障及解决方法 道客巴巴
2015年4月2日 16华北电力技术NORTHCHINAELECTRICPOWER增刊12009进口MBF一24.0型磨煤机主要故障及解决方法王锐,曳前进,张宝武(内蒙古大唐国际托克托发电有限责任公 2015年8月1日 In this paper, a review of researches done on the mill control and methods employed for fault diagnosis of coal mills is provided, with the aim of improving performance Review of control and fault diagnosis methods applied to coal mills 2024年5月1日 To avoid abnormal operating conditions of coal mills in time and effectively, a dual fault warning method for coal mill is proposed Three typical faults of coal mill plugging, coal Dual fault warning method for coal mill based onAn understanding of the mill system, control issues and major faults influencing the mill performance are discussed Control strategies applied for mill controls such as control using Review of control and fault diagnosis methods applied to coal
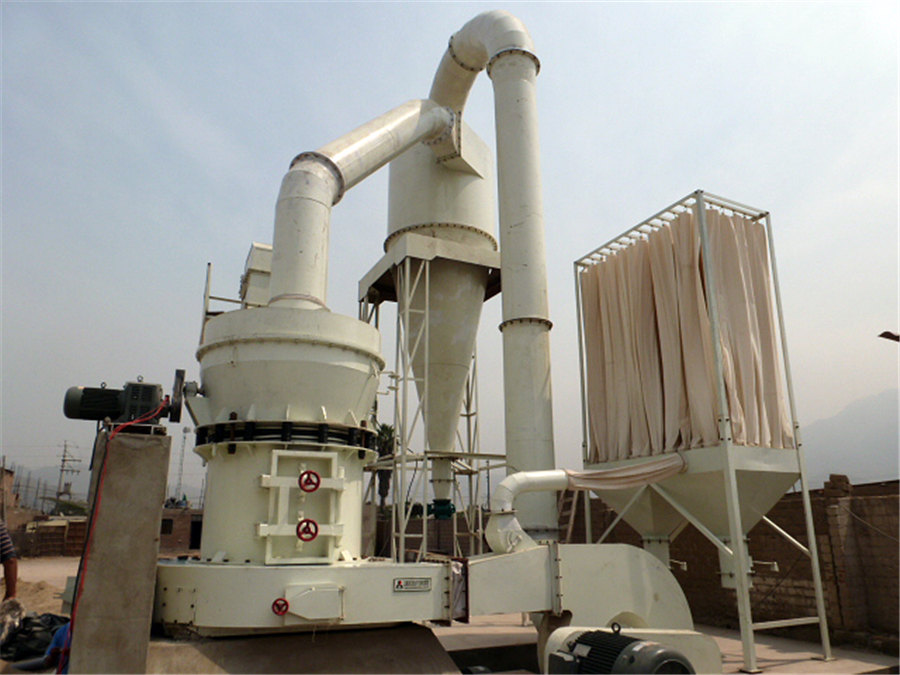
Review of Control and Fault Diagnosis Methods Applied to Coal Mills
2015年5月7日 Power plant performance and reliability is highly influenced by coal mills that grind, dry, and transport coal to the furnace This paper presents a review of the current state 2015年8月1日 A modelbased residual evaluation approach, which is capable of online fault detection and diagnosis of major faults occurring in the milling system, is proposed and shows Review of control and fault diagnosis methods applied to coal mills2016年7月7日 In this paper, a modelbased residual evaluation approach, which is capable of online fault detection and diagnosis of major faults occurring in the milling system, is proposed Intelligent Decision Support System for Detection and Root 2008年8月1日 In this paper an observerbased method for detecting faults and estimating moisture content in the coal in coal mills is presented Handling of faults and operation under Observerbased fault detection and moisture estimating in coal mills
.jpg)
(PDF) Application of ModelBased Deep Learning Algorithm in Fault
2020年8月14日 In this paper, a modelbased deep learning algorithm for fault diagnosis is proposed to effectively detect the operation state of coal mills Based on the system The experimental results show that it can effectively detect the coal blocking and coal breaking faults of the coal feeder and the coal mill, effectively reduce the system false alarm rate, Research and Application of Coal Blockage Early Warning 2023年9月15日 As the significant ancillary equipment of coalfired power plants, coal mills are the key to ensuring the steady operation of boilers In this study, a fault diagnosis model was proposed on the Fault Diagnosis of Coal Mills Based on a Dynamic Model2009年9月1日 The coal mill used in the coalfired power plants is modeled in view of the controller design rather than the educational simulator The coal mass flow and the outlet temperature are modeled by reinvestigating the mass balance and heat balance models physically The archived data from a plant database are utilized to identify the model Modeling and Parameter Identification of Coal Mill
.jpg)
Fault analysis and optimization technology of HP bowl type
2021年8月1日 The common faults of this type o f coal mill are analyzed as fol lows: Rjj 90=4+08n V daf % the main sealing air pipe of coal mill to the bottom of the hot air baffle door The switch 2020年8月14日 The coal mill is one of the important auxiliary engines in the coalfired power station Its operation status is directly related to the safe and steady operation of the units(PDF) Application of ModelBased Deep Learning Algorithm in Fault Coal blockage is one of the main reasons for coal mill malfunction It is highly essential to accurately detect the critical blockage in coal mills to ensure a safe and stable operation of theEarly Warning of Critical Blockage in Coal Mills Based on 2020年1月1日 Coal mills are bottleneck in coalfired power generation process due to difficulty in developing efficient controls and faults occurring inside the mills In this paper, a dynamic coal mill model (PDF) Modelling and multiloop selective control of industrial coal
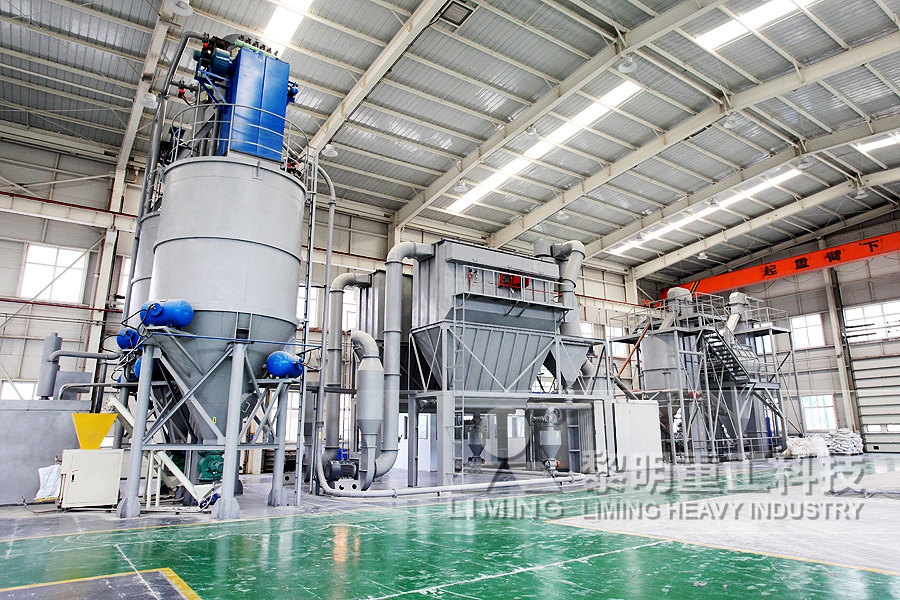
Coal Mill an overview ScienceDirect Topics
A simple energy balance model of the coal mill is derived in (Odgaard and Mataji 2006), this model is based on a more detailed model found in (Rees and Fan 2003)In this model the coal mill is seen as one body with the mass m mThe following variables are defined: T(t) is the temperature in the coal dust flow in the mill, ṁ PA (t) is the primary air mass flow, T PA (t) is 2013年12月1日 Abstract The paper presents development and validation of coal mill model (including the action of classifier) to be used for improved coal mill control The model is developed by using the mass and heat balance equations of the coal mill Genetic Algorithm is used to estimate the unknown parameters that are used in the model validation The [PDF] Modeling and Control of Coal Mill Semantic Scholar2017年8月1日 A modelbased residual evaluation approach, which is capable of online fault detection and diagnosis of major faults occurring in the milling system, is proposed and shows that how fuzzy logic and Bayesian networks can complement each other and can be used appropriately to solve parts of the problem Coal mill is an essential component of a coalfired Intelligent Decision Support System for Detection and Root 2024年8月22日 The BTM is a lowspeed mill that primarily grinds coal by impact and attrition The VRM is a medium speed mill that grinds coal by compression and, because of the low coal inventory in the mill and flat grinding surfaces, develops shearing action as well For both mills a constant centrifugal force is maintained The speedA Comparison of Three Types of Coal Pulverizers

Review of Control and Fault Diagnosis Methods Applied to Coal Mills
2015年5月7日 The mean value of coal flow parameter is 13584 kg/s, coal mass accumulation is 2,196 kg, coal output temperature is 83296 0C, coal moisture is 0021, and coal fineness is 75338 % View Show 2020年1月1日 Coal blockage is one of the main reasons for coal mill malfunction It is highly essential to accurately detect the critical blockage in coal mills to ensure a safe and stable operation of the unitEarly Warning of Critical Blockage in Coal Mills 2016年7月7日 Remarkable examples of intelligent solutions for faults' detection in coal mills are given in [18] [19] [20], while methods for modeling a coal mill for fault monitoring and diagnosis are Intelligent Decision Support System for Detection and Root The raw material of coal powder is coal with various hardness, and it drying in the coal mill grinding process to obtain finished coal powder which can be efficiently burned Coal ball mills are widely used in the cement industry and thermal power generation industry, and are also suitable for metallurgical industry, chemical industry, sugar Coal Ball Mill Grinding for Different Kinds of Pulverized Coal
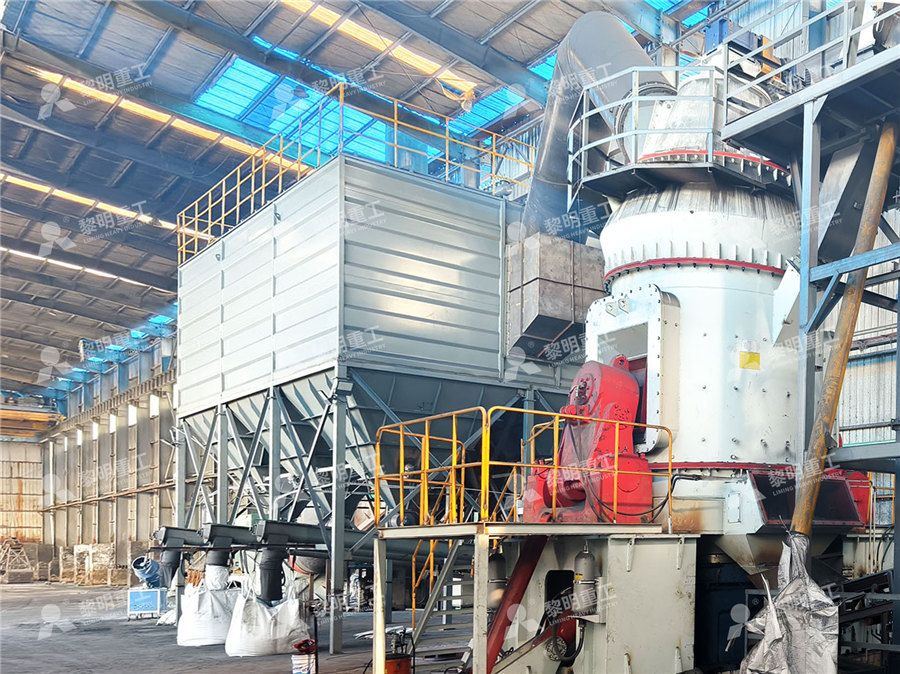
A Novel MultiMode Bayesian Method for the Process
2021年1月28日 A Novel MultiMode Bayesian Method for the Process Monitoring and Fault Diagnosis of Coal MillsIf the voltage and power factor of coal mill are constant, grinding current can be used to replace the power of coal mill In this paper, through collecting field historical operation data and data preprocessing, the current model of coal mill is established by using double hidden layers BP (Back Propagation) neural network to predict the wear Monitoring Model of Coal Mill in Power Plant Based on Big 2013年1月1日 The coal mills are key equipments in the power plant []Faults often happen because they work in the complex operating environment Through analyzing faults, we find that faults of the coal mills present characteristics of fuzzy and uncertain, which a kind of fault may exhibit a variety of different fault symptoms, and for different fault types may also produce the The Research on Fault Diagnosis Method of the Coal Mill 1997年8月1日 DOI: 101016/S14746670(17)464470 Corpus ID: ; Analysis of coal Mill Dynamic Characteristics Under Normal and Abnormal Operating Conditions @article{Fan1997AnalysisOC, title={Analysis of coal Mill Dynamic Characteristics Under Normal and Abnormal Operating Conditions}, author={G Q Fan and N W Rees and David Parker}, Analysis of coal Mill Dynamic Characteristics Under Normal
.jpg)
DETECTION OF MALFUNCTIONS AND ABNORMAL OPERATING CONDITIONS OF A COAL MILL
2016年3月25日 Coal mill malfunctions are some of the most common causes of failing to keep the power plant crucial operating parameters or even unplanned power plant shutdowns Therefore, an algorithm has been developed that enable online detection of abnormal conditions and malfunctions of an operating mill Based on calculated diagnostic signals and defined 2015年8月1日 Mill problems originate mainly due to poor controls or faults occurring within the milling system As discussed by GQ Fan and NW Rees [3], the control of mills remains very simple in most of the power plants due to the fact that the mill system is highly nonlinear with strong coupling among the variables and it is very difficult to measure some important Review of control and fault diagnosis methods applied to coal mills 2015年8月1日 A modelbased residual evaluation approach, which is capable of online fault detection and diagnosis of major faults occurring in the milling system, is proposed and shows that how fuzzy logic and Bayesian networks can complement each other and can be used appropriately to solve parts of the problemReview of control and fault diagnosis methods applied to coal mills2015年11月1日 Section 6 presents an application of the model for online estimation of the moisture content in the raw coal Finally, in Section 7, main conclusions are highlighted The nomenclature is provided in the appendix Further, mill operation and availability is highly influenced by common faults such as coal hang up at the mill inlet, mill A unified thermomechanical model for coal mill operation
.jpg)
Intelligent Decision Support System for Detection and Root
2016年7月7日 Coal mill is an essential component of a coalfired power plant that affects the performance, reliability, and downtime of the plant The availability of the milling system is influenced by poor controls and faults occurring inside the mills There is a need for automated systems, which can provide early information about the condition of the mill and help operators 2021年3月31日 3 COAL QUALITY –IMPACT COMPLEX • Pulverizer capacity, fineness wear • Slagging fouling in boiler • Corrosion erosion in boiler • Ash characteristics affect efficient collection in ESP • Affects furnace convective pass heat absorption boiler availability • Quantification of impact is complex 31Mar2021 total output power solutions 3Effect of Coal Quality and Performance of Coal pulverisers / Mills2011年1月1日 The main faults and its solution of a BIVIS mechanical pulping system in a mill were introduced in this paper By modifying the feedingside shaft end and its surrounding equipment of 1# BIVIS The main faults and its solution in BIVIS mechanical pulping2013年8月1日 The reliability of a coal mill's operation is strongly connected with optimizing the combustion process Monitoring the temperature of a dust–air mixture significantly increases the coal mill's Modeling and outlet temperature control of coal mill using
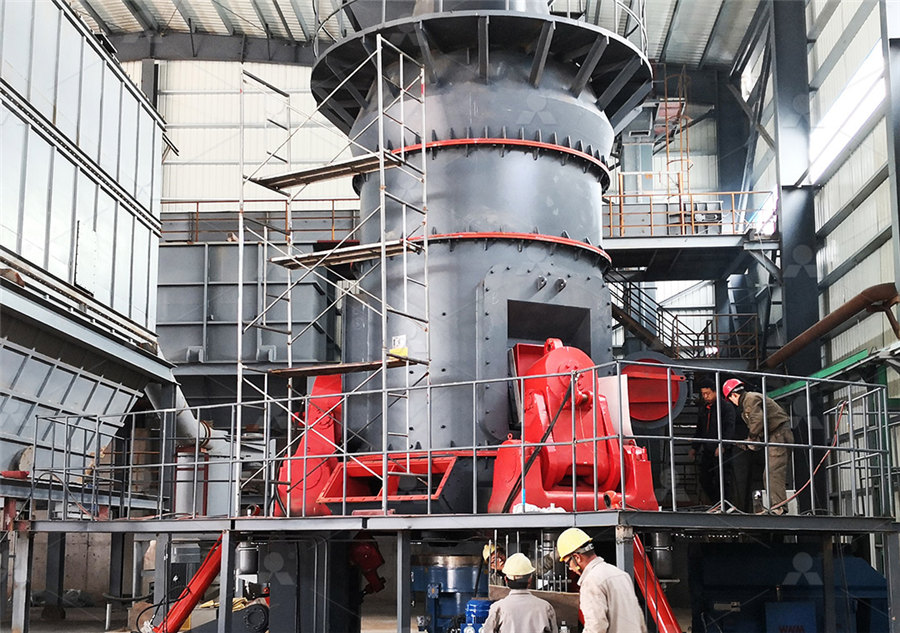
(PDF) A Modeling and Optimizing Method for Electricity
2022年3月25日 The electricity current intensity of coal mills can be reduced or minimized subject to the coal type parameters and the load of the boiler through optimizing the coal mill operations2024年11月26日 Coal grinding mills LOESCHE coal grinding mills are distinguished by characteristics that improve efficiency, safety and environmental protection, from the standard version to topoftherange installations Special versions are available with characteristics that meet special safety regulation or output control requirementsCoal Mills for Cement Plants Loesche2024年10月31日 Coal mills, essential components in power generation and various industrial processes, pose significant safety risks if not properly managed These mills, used to grind coal into a fine powder for combustion, present potential hazards such as fire, explosion, and mechanical failures This article outlines best practices and precautions to ensure thEnsuring Safety in Coal Mills Coal Mill Safety, Explosion and 2009年9月20日 A control oriented model was then developed by Fan (1994) and Fan and Rees (1994) In 2009, coal flow and outlet temperature of mill were modelled using mass and heat balance equations for startup (PDF) Modeling and Parameter Identification of Coal Mill
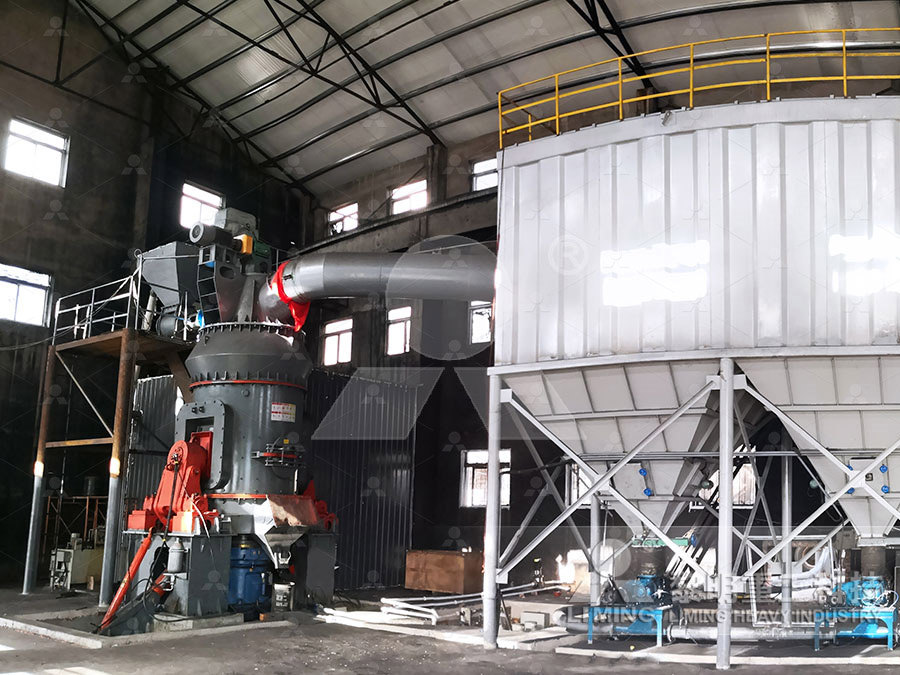
Fault Diagnosis of Coal Mills Based on a Dynamic Model
2023年9月15日 As the significant ancillary equipment of coalfired power plants, coal mills are the key to ensuring the steady operation of boilers In this study, a fault diagnosis model was proposed on the 2009年9月1日 The coal mill used in the coalfired power plants is modeled in view of the controller design rather than the educational simulator The coal mass flow and the outlet temperature are modeled by reinvestigating the mass balance and heat balance models physically The archived data from a plant database are utilized to identify the model Modeling and Parameter Identification of Coal Mill2021年8月1日 The common faults of this type o f coal mill are analyzed as fol lows: Rjj 90=4+08n V daf % the main sealing air pipe of coal mill to the bottom of the hot air baffle door The switch Fault analysis and optimization technology of HP bowl type 2020年8月14日 The coal mill is one of the important auxiliary engines in the coalfired power station Its operation status is directly related to the safe and steady operation of the units(PDF) Application of ModelBased Deep Learning Algorithm in Fault
.jpg)
Early Warning of Critical Blockage in Coal Mills Based on
Coal blockage is one of the main reasons for coal mill malfunction It is highly essential to accurately detect the critical blockage in coal mills to ensure a safe and stable operation of the2020年1月1日 Coal mills are bottleneck in coalfired power generation process due to difficulty in developing efficient controls and faults occurring inside the mills In this paper, a dynamic coal mill model (PDF) Modelling and multiloop selective control of industrial coal A simple energy balance model of the coal mill is derived in (Odgaard and Mataji 2006), this model is based on a more detailed model found in (Rees and Fan 2003)In this model the coal mill is seen as one body with the mass m mThe following variables are defined: T(t) is the temperature in the coal dust flow in the mill, ṁ PA (t) is the primary air mass flow, T PA (t) is Coal Mill an overview ScienceDirect Topics2013年12月1日 Abstract The paper presents development and validation of coal mill model (including the action of classifier) to be used for improved coal mill control The model is developed by using the mass and heat balance equations of the coal mill Genetic Algorithm is used to estimate the unknown parameters that are used in the model validation The [PDF] Modeling and Control of Coal Mill Semantic Scholar
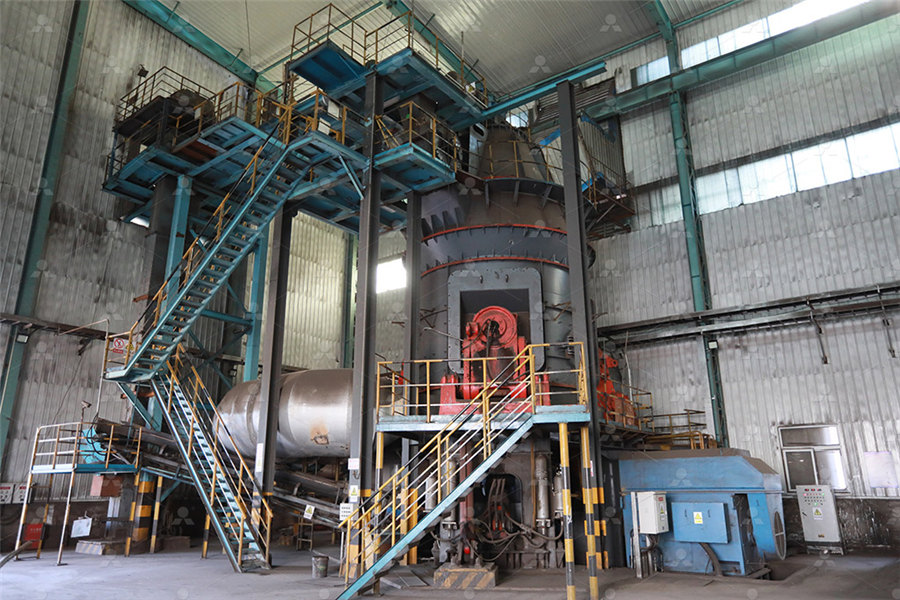
Intelligent Decision Support System for Detection and Root
2017年8月1日 A modelbased residual evaluation approach, which is capable of online fault detection and diagnosis of major faults occurring in the milling system, is proposed and shows that how fuzzy logic and Bayesian networks can complement each other and can be used appropriately to solve parts of the problem Coal mill is an essential component of a coalfired 2024年8月22日 The BTM is a lowspeed mill that primarily grinds coal by impact and attrition The VRM is a medium speed mill that grinds coal by compression and, because of the low coal inventory in the mill and flat grinding surfaces, develops shearing action as well For both mills a constant centrifugal force is maintained The speedA Comparison of Three Types of Coal Pulverizers