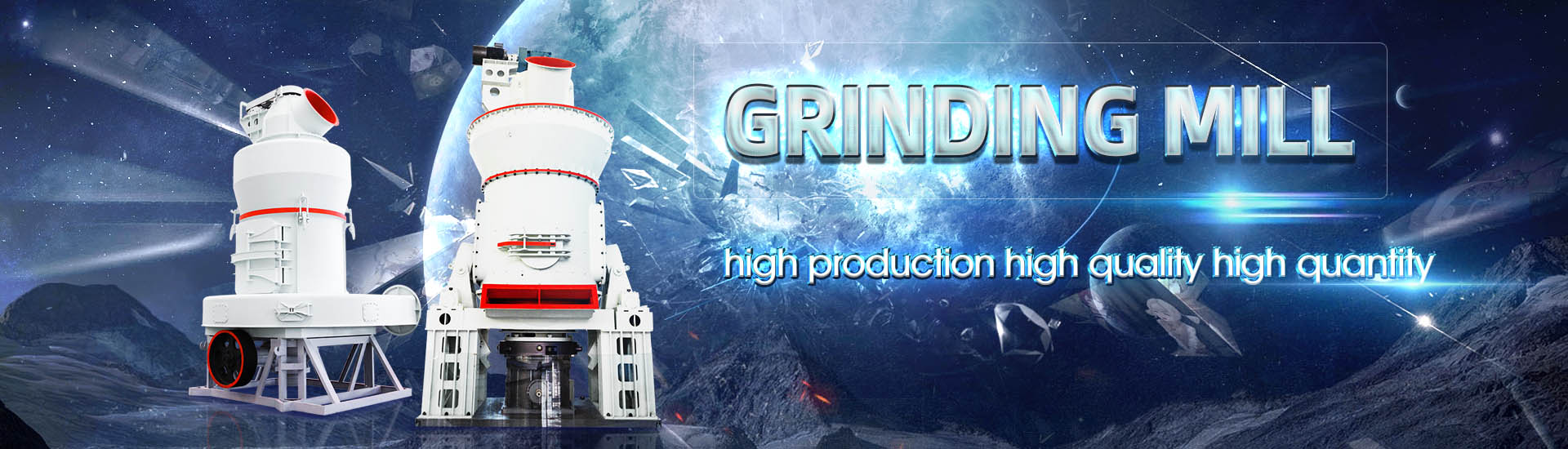
Ball mill gear tip clearance
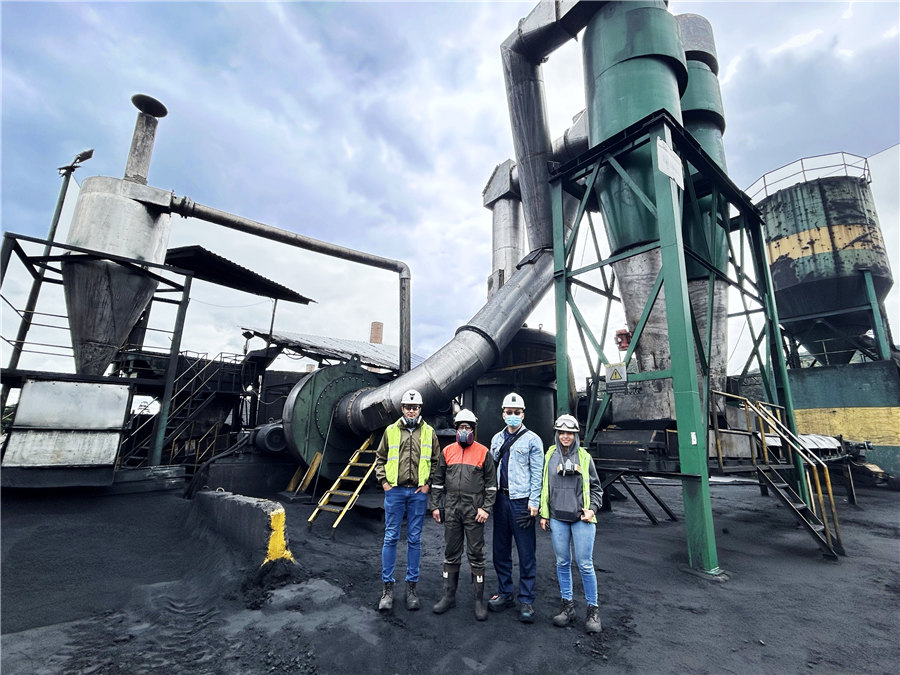
Grinding ball mill girth gear root clearance GlobalSpec
2008年12月25日 How do you measure the root clearance between a girth gear and a pinion of a grinding ball mill and what is the recommended root clearance This ball mill uses helical 2017年2月23日 Fitting of girth gear to mill A: The spigot reference diameters can have 12 mm clearance The girth gear is to be fitted to the mill body in the same position with respect to GIRTH GEAR Artec Machine摘要 介绍了球磨机边缘传动装置的安装找正方法,通过大小齿轮的找正和齿顶隙、齿侧隙的调整,满足大小齿轮啮合面接触面积不小于齿高的40%、齿宽的50%,确保齿轮安装质量和使用寿 球磨机大小齿轮的安装2022年2月7日 To avoid permanent damage to gears, pinion bearings and soleplates, we recommend a complete inspection and evaluation using our four step process; scope Gears and pinions Metso
.jpg)
Kiln Gear and Pinion Alignment INFINITY FOR
Readjust the rollers now to set the required backlash and root clearance 15% Conversely if the backlash is zero (the root clearance is too tight) there would be tooth tip interference, which can overload a tooth as much as 200% and cause 2021年6月1日 In all cases, it is possible to chamfer either, or both, the Toe and Heel edges, and the Tip edges In many instances, adjusting chamfer parameters such as the Pivot Angle Gear Tooth Edge Deburring and Chamfering in 5Axis CnC2022年11月21日 mills for the grinding and drying of a wide variety of materials, thyssenkrupp Industrial Solutions offers solutions to suit your every need The ball mill that best suits your Industrial Solutions polysius ball mills ThyssenKrupp2024年2月1日 According to the specification requirements: the radial runout of the large ring gear, the diameter of the pitch circle per meter should not exceed 025mm; the end face of the large ring gear beats, the diameter of the pitch Ball mill girth gear detection and adjustment
.jpg)
Early Detection of IndustrialScale Gear Tooth Surface
2020年7月21日 Keywords Ball mill Largescale helical gear Vibration condition monitoring Pitting Introduction One of the most important parts of ball mills is transmission system and gears The transmission system has to Clearance (inch/mm) 028033/7385 Table 2 The bearing characteristics Parameter Symbol Value Unit2023年6月19日 This document provides instructions for installing a 16x22ft, 2800kW ball mill It outlines 8 key steps: 1) Prepare the foundation and install the trunnion bearing sole plates 2) Assemble and mount the trunnion bearings 16' X 22' Ball Mill Installation Manual PDF Scribd2023年2月15日 High temperature of the ball mill will affact the efficiency 3 For every 1% increase in moisture, the output of the ball mill will be reduced by 8% 10% 4 when the moisture is greater than 5%, the ball mill will be unable to 17 Signs of Problems with Ball Mills: Quickly 2021年6月1日 In all cases, it is possible to chamfer either, or both, the Toe and Heel edges, and the Tip edges In many instances, adjusting chamfer parameters such as the Pivot Angle allows chamfering every part of the tooth; this is especially true of End Mill and Ball Mill tools, although Ball Mill tools leave a double lip because of their spherical tipGear Tooth Edge Deburring and Chamfering in 5Axis CnC
.jpg)
Gears and pinions Metso
2022年2月7日 A complete range of gear and pinion sets, inspections, design, installation and alignment services to drive your mill’s performance Introducing a new name • AG and SAG mills • Ball and FGD mills •Pebble and rod mills • Multicompartment mills • Rotary kilns and dryers • Mixers and other equipment Benefits:2024年2月1日 A dial gauge E is placed at the midpoint of girth gear tooth width The micrometer pointer is to be vertically measured to measure the radial runout of girth gear; a dial gauge A is placed on the end face of the girth gear to measure the end face runout of the girth gear; two dial gauges B and C are respectively placed at the shoulder of the ball mill trunnion and separated Ball mill girth gear detection and adjustment2023年7月18日 When maintaining the ball mill, the following tools and equipment may be helpful: 1 Wrench: used to disassemble and install fastening bolts, nuts, and other components 2 Lubricating oil gun: used to add lubricating oil to bearings, gears, transmission devices, and other parts 3 Lubricating oil: selecting appropriate lubricating oil is crucial for ball mill Ball Mill Maintenance Process and Methods Miningpedia2024年9月6日 The distance between the root and its mating gear's tooth tip (the gap) is the root clearance which provides the escape for the gears to mesh without interference TEL : +81 48 254 1744 This distance (the gap) is also called the root clearance, top clearance, bottom clearance or simply the clearance When the dedendum is 125m and the Root Clearance Gear Nomenclature KHK
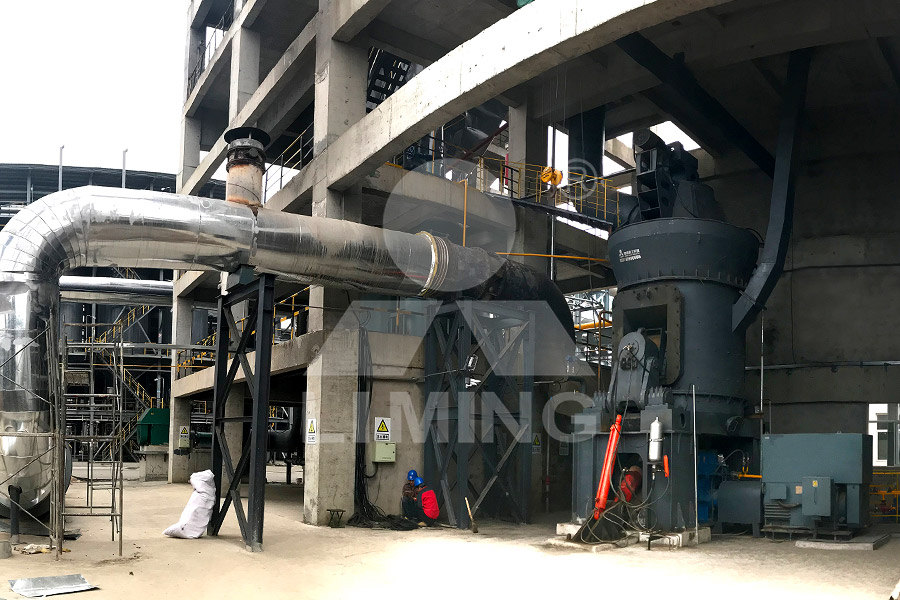
Grinding Mill Gear Assembly 911Metallurgist
2015年7月28日 We will begin with the mill’s bull gear assembly and work towards the motor, The BULL GEAR, sometimes called the RING GEAR is designed to turn the mill transforming the energy of the motor into motion for the mill By mill we refer to Ball Mills, Rod Mills and SAG Mills Anything gear and pinion really The discharge end of the mill; For the 2015年7月28日 Ball Mill TRUNNION BEARINGS Swivel type leadbronze bushed trunnion bearings are generally furnished on large diameter ball Mills The bearing swivels are of Meehanite metal spherically turned outside and bored and faced inside to receive the removable bushing The bushing is bored and scraped to fit the mill trunnionTrunnion Bearing Assembly Ball Mill Rod Mill2023年10月20日 The basic components and structure of a ball mill play a crucial role in its operation and performance Understanding these elements is essential for effectively operating the equipment 1 Cylindrical Shell The ball mill Comprehensive Guide on Operating a Ball Mill2013年1月24日 Ball nosed end mills don't have enough clearance Of course if it's a shallow hole and you can back off the feed rate it may work In FR4, I always use a fishmouthed rasp style cutter to mill and drill withAre all ball nose end mills able to directly drill holes?
.jpg)
Maximizing Ball Mill Performance: A Comprehensive Guide
2023年6月15日 This article provides essential preventive measures for ball mill maintenance to ensure optimal performance and longevity +86 ; xlyin@xinhaimining; Check the gear teeth for wear, cracks, and other damage Rod Mill Maintenance: Tips for Longevity and Performance read more Laura Oct 29, 2024Ball Mill Girth Gear Root Clearance Calculation and Ball ball mill girth gear maximum allowable axial runout ball mill dynamic ball mill pinion runout Coal Inquire Now Sag Mill Syncronis Motor high axial vibration non axial runout of mill flange Axial and radial runout of girth gears Thermal profile of girth gear and pinion Root to tip ball mill girth gear root clearance Sebocom Construction2020年6月14日 This week’s tip goes back to a question that was recently asked by a member of the Mobil SHC Club: “What is the cause of high temperature in a slide shoe bearing on a ball mill?” A mineral based gear or RO oil (and oil specifically formulated to better combat rust and oxidation) may be used to lubricate the slide shoe Mobilgear XP Improving Mill Shoe Bearing Reliability and Productivity2022年4月1日 This research paper contains the design aspects and analysis of the gear box used in the ball mill The ball mill is used for the conversion of the raw stone material into the powder form by using Design and simulation of gear box for stone crushing ball mill
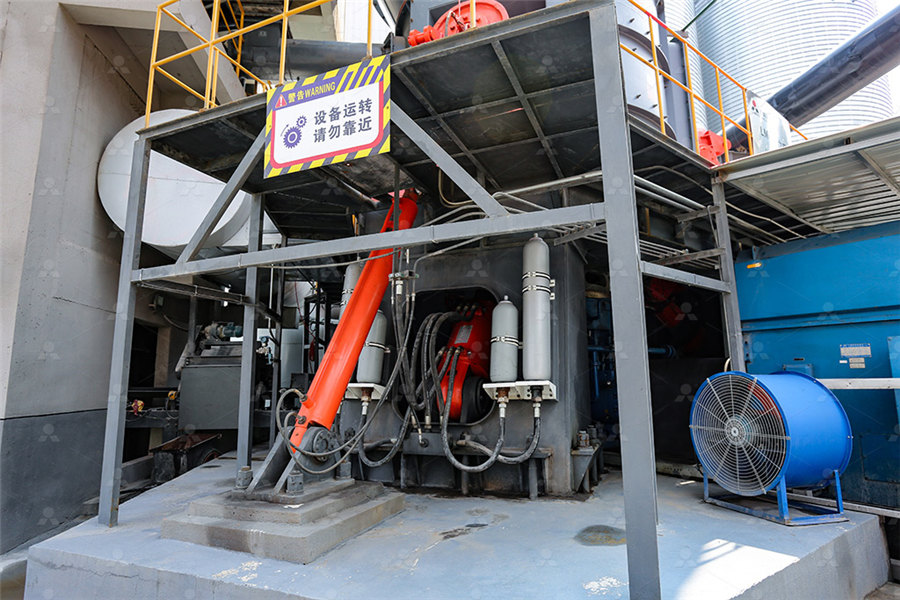
Common problems and treatment methods of ball mill gear
2024年6月6日 Once the gear of the ball mill is damaged, the wait for the ball mill is to stop production and repair Recently, we have consulted some clients about gear wear in ball mills, hoping to learn how to improve gear wear in ball mills In fact, the main reason that affects the service life of ball mill gears is gear wearDesigned to deliver exceptional levels of performance and value, David Brown Santasalo ball mill drives are optimised for primary and secondary grinding applications Extensively field tested and proven in harsh cement applications, our mill drive gearboxes cover all grinding applications up to 10 MW per drive and we have single, double and Ball Mill Drives Crushing Grinding Drives David Brown 2020年4月19日 Monitoring pinion temperatures on mill gear pinions is an effective and efficient means of monitoring alignment and operating condition Toll Free USA +1 (866) 4191619; Worldwide +1 (715) 2142162; LinkedIn; We use a ball mill for production, but our project did not realize the pinion gear temperature monitoringGirth Gear Pinion Infrared Imaging and Temperature Measurements2012年6月1日 The mill is driven by a girth gear bolted to the shell of the vessel and a pinion shaft moved by a prime mover The prime movers are usually Ball mills can grind a wide range of materials (PDF) Grinding in Ball Mills: Modeling and Process Control
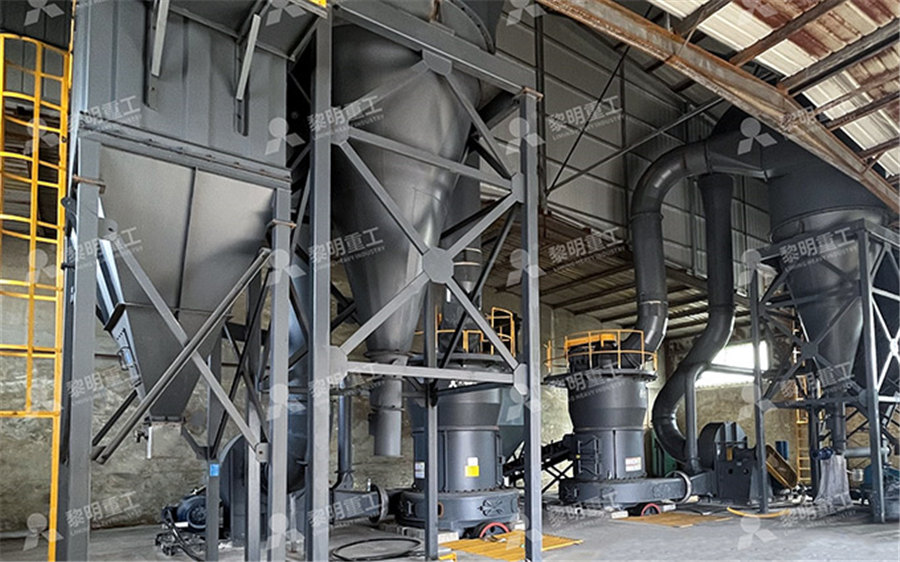
5 Mustknow Ball Mill Parts And Functions
Ball mill is a kind of grinding equipment for repulverizing primary crushed materials It is widely used in cement, construction, fertilizer, mineral processing, and other industries Ball mill grinder is used for dry or wet grinding of various 2021年1月1日 Comchambered with the design of Φ 35 × 13m threechamber ball mill, the design process of ball mill is described in detail General arrangement of the mill Filling rate of grinding body in each (PDF) Design of Threechamber Ball MillA ball mill operates by rotating a cylinder with steel or ceramic balls, causing the balls to fall back into the cylinder and onto the material to be ground The rotation of the cylinder is typically between 4 to 20 revolutions per minute, depending on the diameter of the millA Comprehensive Guide to Ball Mill Manual ball mills supplierHere, we introduce the two common faults of the ball mill girth gear and provide detailed solutions for each We hope to help customers solve practical problems in the application process of wet ball mills Severe vibration of the small gear in industrial ball mills The normal operation of wet ball mill relies on the motor driving the ball Common Two Faults of Ball Mill Gear and Their Solutions
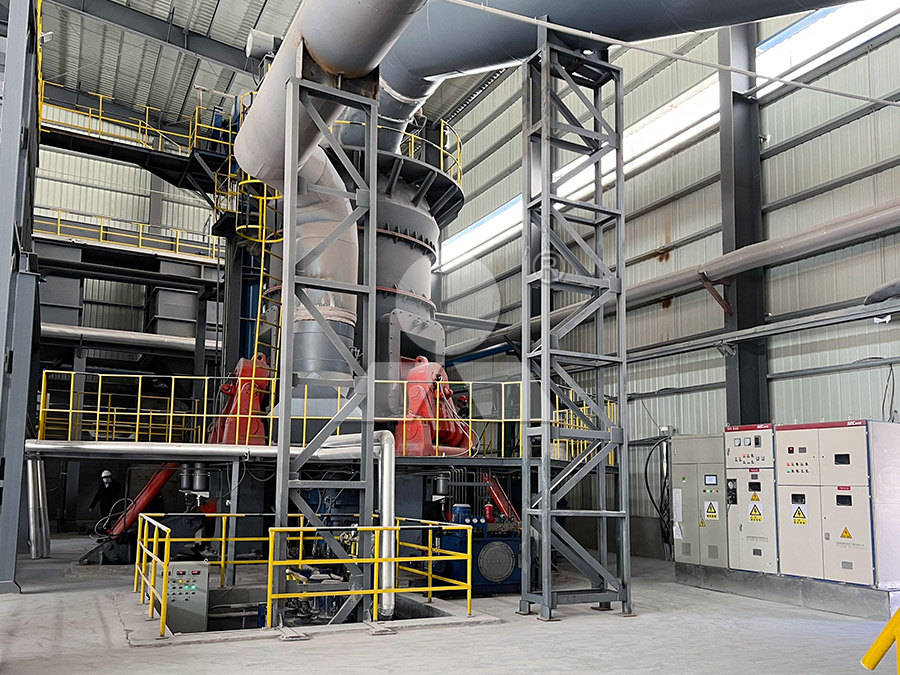
Industrial gear unit drive solution for ball mills
Power to mill and grind: Industrial gear units and gear wheel rims for ball mills Ball mill: Drive solutions for small and large torques Flexible drive solutions for use in ball mills A ball mill is a horizontal cylinder filled with steel balls or the like This cylinder rotates around its axis and transmits the rotating effect to the ballsThe highperformance gear unit you need to drive your ball mill Our MAAG® GEAR CPU Central Drive Gear Unit uses a twostage planetary arrangement to enhance your cement grinding process It delivers the highest productivity for your ball mill – and takes up less space than a traditional multistage spur gear unitMAAG® GEAR CPU Gear UnitThe Across International PQ Series GearDrive Planetary Ball Mills are suitable for various applications, including mixing, homogenizing, fine grinding, mechanical alloying, cell disruption, smallvolume hightech material production, and colloidal grinding These units have a rotational speed of 350 rpm and can run continuously for 72 hours They can operate two or four jars PQ Series GearDrive Planetary Ball Mill Across InternationalThe ball mill pinion gear are crafted from materials like ZG45#, 35SiMn, 45MnB, and 40Cr, tailored to customer specifications and drawings The pitch diameter, calculated based on the number of teeth and pitch, and the backlash (clearance between teeth) ensure proper meshing, allowing for thermal expansion and lubrication Surface Finish Ball Mill Pinion Ball Mill Pinion Gear Supply AGICO CEMENT
.jpg)
BallMillManualpdf
Mill Installation Manual 16x22ft, 2800kW Ball Mill 107 1 TROUBLE SHOOTING GEAR AND PINION VIBRATION Excessive Backlash Move the mill gear toward the pinion to attain proper backlash readings Insufficient Backlash Move the mill gear away from the pinion and check for proper backlash clearances Misalignment2019年1月8日 I have an issue with a gear drive on a ball mill 2XGM is rising and i have sidebands at 107cpm and I don't know why they are at 107 (not relevant to any turning speeds ect) I checked the root clearance a week ago and the inboard is about a 066 smaller than the outboard The pinion is 24" long and has 24 teeth It is obvious i have misalignmentAnd there Ball Mill Pinion Vibration Analysis Machinery Diagnostics 2020年7月21日 Keywords Ball mill Largescale helical gear Vibration condition monitoring Pitting Introduction One of the most important parts of ball mills is transmission system and gears The transmission system has to Clearance (inch/mm) 028033/7385 Table 2 The bearing characteristics Parameter Symbol Value UnitEarly Detection of IndustrialScale Gear Tooth Surface2023年6月19日 This document provides instructions for installing a 16x22ft, 2800kW ball mill It outlines 8 key steps: 1) Prepare the foundation and install the trunnion bearing sole plates 2) Assemble and mount the trunnion bearings 16' X 22' Ball Mill Installation Manual PDF Scribd
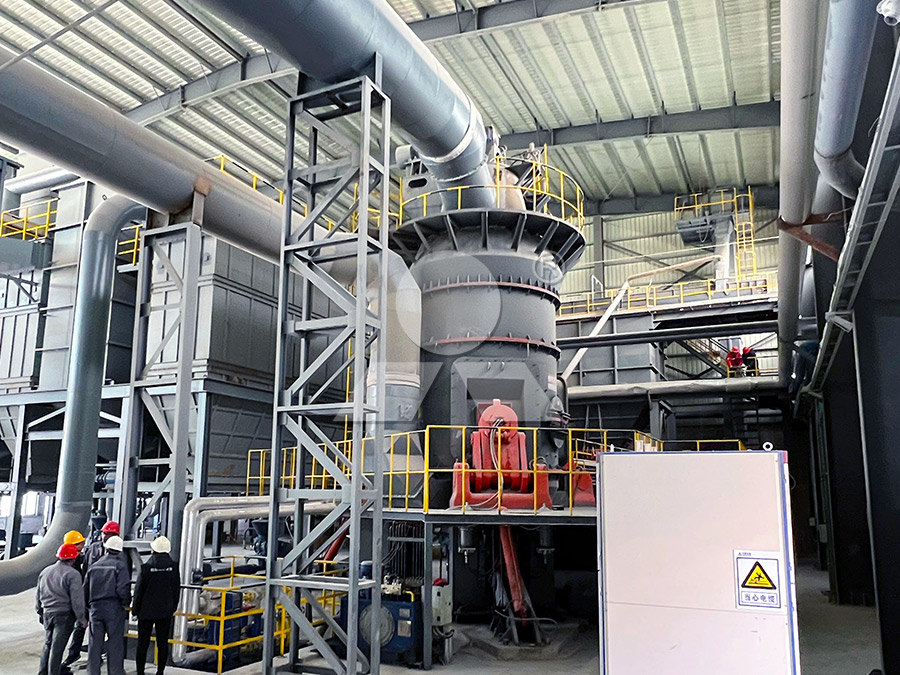
17 Signs of Problems with Ball Mills: Quickly
2023年2月15日 High temperature of the ball mill will affact the efficiency 3 For every 1% increase in moisture, the output of the ball mill will be reduced by 8% 10% 4 when the moisture is greater than 5%, the ball mill will be unable to 2021年6月1日 In all cases, it is possible to chamfer either, or both, the Toe and Heel edges, and the Tip edges In many instances, adjusting chamfer parameters such as the Pivot Angle allows chamfering every part of the tooth; this is especially true of End Mill and Ball Mill tools, although Ball Mill tools leave a double lip because of their spherical tipGear Tooth Edge Deburring and Chamfering in 5Axis CnC2022年2月7日 A complete range of gear and pinion sets, inspections, design, installation and alignment services to drive your mill’s performance Introducing a new name • AG and SAG mills • Ball and FGD mills •Pebble and rod mills • Multicompartment mills • Rotary kilns and dryers • Mixers and other equipment Benefits:Gears and pinions Metso2024年2月1日 A dial gauge E is placed at the midpoint of girth gear tooth width The micrometer pointer is to be vertically measured to measure the radial runout of girth gear; a dial gauge A is placed on the end face of the girth gear to measure the end face runout of the girth gear; two dial gauges B and C are respectively placed at the shoulder of the ball mill trunnion and separated Ball mill girth gear detection and adjustment
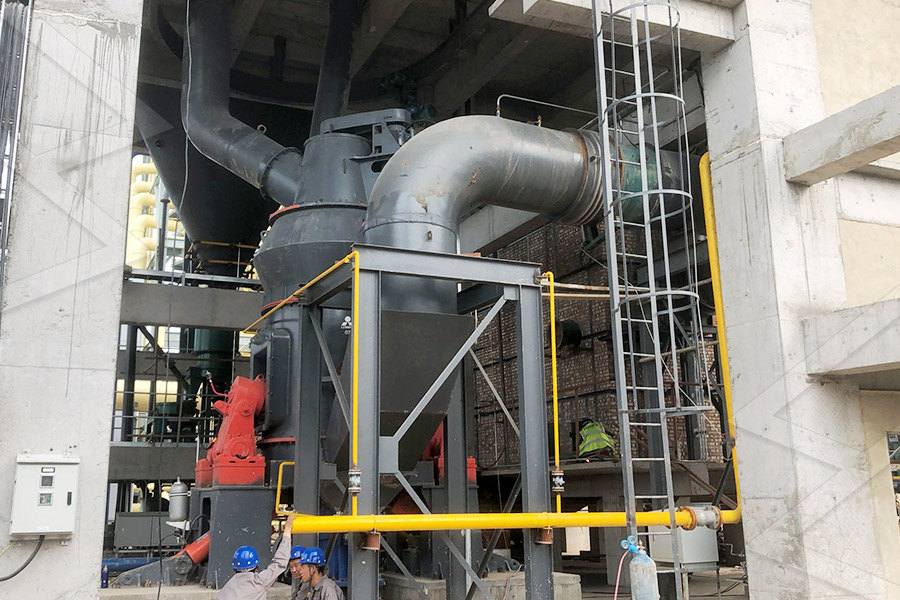
Ball Mill Maintenance Process and Methods Miningpedia
2023年7月18日 When maintaining the ball mill, the following tools and equipment may be helpful: 1 Wrench: used to disassemble and install fastening bolts, nuts, and other components 2 Lubricating oil gun: used to add lubricating oil to bearings, gears, transmission devices, and other parts 3 Lubricating oil: selecting appropriate lubricating oil is crucial for ball mill 2024年9月6日 The distance between the root and its mating gear's tooth tip (the gap) is the root clearance which provides the escape for the gears to mesh without interference TEL : +81 48 254 1744 This distance (the gap) is also called the root clearance, top clearance, bottom clearance or simply the clearance When the dedendum is 125m and the Root Clearance Gear Nomenclature KHK2015年7月28日 We will begin with the mill’s bull gear assembly and work towards the motor, The BULL GEAR, sometimes called the RING GEAR is designed to turn the mill transforming the energy of the motor into motion for the mill By mill we refer to Ball Mills, Rod Mills and SAG Mills Anything gear and pinion really The discharge end of the mill; For the Grinding Mill Gear Assembly 911Metallurgist2015年7月28日 Ball Mill TRUNNION BEARINGS Swivel type leadbronze bushed trunnion bearings are generally furnished on large diameter ball Mills The bearing swivels are of Meehanite metal spherically turned outside and bored and faced inside to receive the removable bushing The bushing is bored and scraped to fit the mill trunnionTrunnion Bearing Assembly Ball Mill Rod Mill