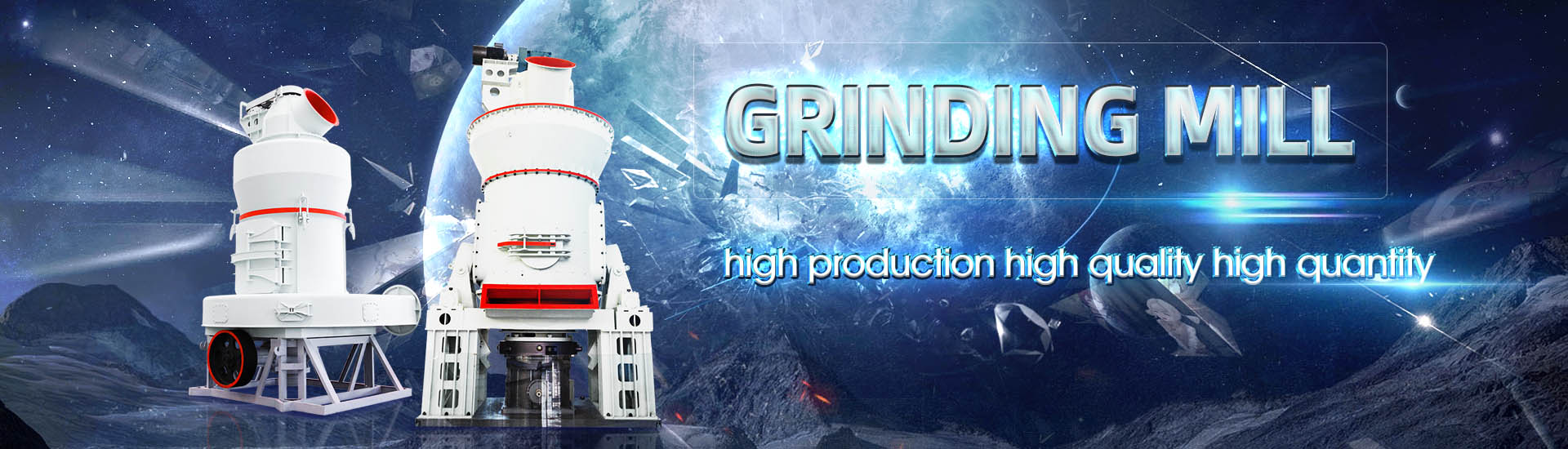
Selection of air volume for coal mill with less wind
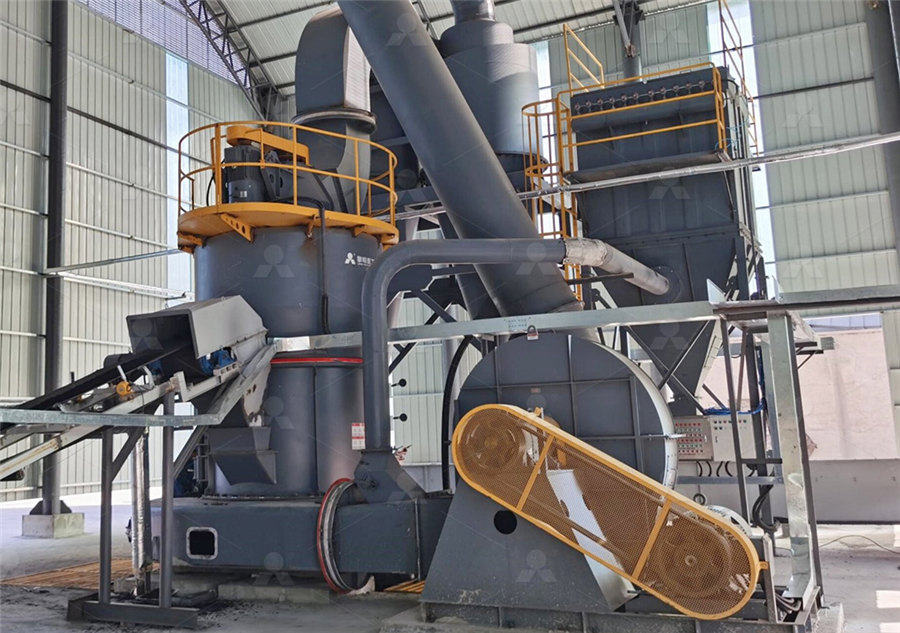
Calculation of Required Air Volume and
2023年6月26日 Taking the air demand and ventilation capacity of the Xinyuan coal mine as the research object, the air demand of the coal mining face, excavation face, backup face, chamber, and other2023年1月1日 In a pulverized coalfired (PCF) thermal power plant (TPP), mixture of coal, air and gas is supplied into the furnace volume via the mill duct system and coal/air distribution Mixing Characteristics and Flow Fields Optimization of Primary Air 2023年8月16日 This study takes the ventilation system of the Xinli Submine of Sanshandao Gold Mine as an example to analyze the airflow volume regulation demand of the deeplevel section stope to further improve the coordination of Optimization of Branch Airflow Volume for Mine 2024年5月13日 Purpose of this paper is to analyze which roadway is required to be distributed with air quantity, put forward a reasonable method to distribute air quantity in coal mine Analysis of distribution method of designed air quantity in coal
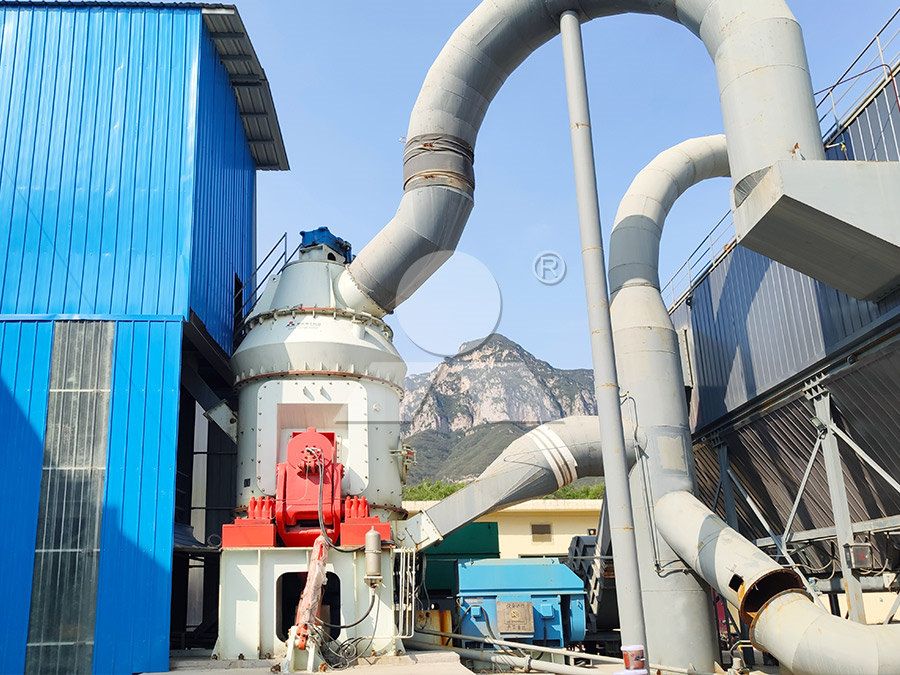
Mixing Characteristics and Flow Fields Optimization of Primary Air
2023年1月1日 This paper mainly focuses on the problems of inaccurate measurement of the primary air flow rate in a coalfired power plant The feasibility of improving the uniformity of 2023年12月4日 According to the Coal Mine Safety Regulations, the average wind speed of the inlet tunnel shall not exceed 8 m/s, so the maximum inlet air volume of the Wulihou coal mine is 128 m 3 /s, and the ventilation air volume Influence of Air Volume and Temperature in the 2024年5月13日 In a coal mine, air leakage exists in some roadways through doors and other ventilation structures inevitably Based on this opinion, there are diferent views on whether Analysis of distribution method of designed air quantity 2017年10月1日 Automated ventilation system adjustment software has been developed by monitoring the air volume of the minimum remainder branch in the network, and all air volumes Intelligent safety adjustment of branch airflow volume
.jpg)
Analysis of multifactor ventilation parameters for reducing energy air
2023年9月1日 Based on the results of multifactor analysis, the best ventilation parameters for reducing coal dust pollution during coal energy mining are as follows: the distance between 2012年1月1日 In this paper, the desiccant medium choice, desiccant medium composition and main design parameters (calculation of the oxygen content of the coal mill export, coal mill The Research on Design Parameters of Fan Mill Direct2021年8月1日 Yukio et al [7] proposed a model consisting of blending, grinding and classifying processes for pulverizer control Agarawal et al [8] differentiated coal powder into ten size groups, divided the bowl mill into four zones, and developed a unified model Palizban et al [9] derived nonlinear differential mass equations of raw coal, recirculation coal and suspension coal in Coal mill model considering heat transfer effect on mass 2020年8月12日 To understand the performance of a vertical roller coal mill, the real operational tests have been performed considering three different coal sources Obtained results indicate that grinding pressure, primary air (PA) temperature and mill motor current have a tendency to rise by increasing coal feeding mass flow rates for all used coalAn investigation of performance characteristics and
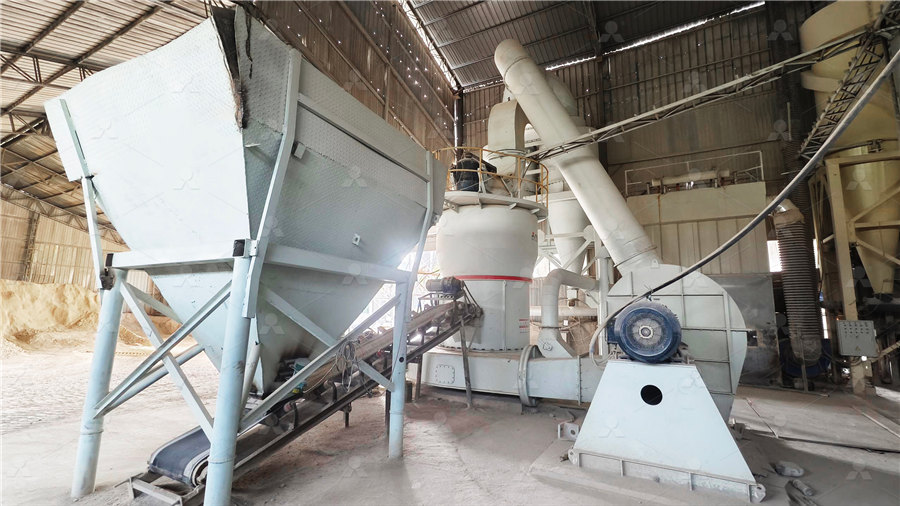
Review of control and fault diagnosis methods applied to coal mills
2015年8月1日 This paper is organized as follows: Section 2 provides an understanding of the mill system together with the control issues and major faults influencing the mill performance Section 3 deals with the review of different control strategies applied to the milling system Control using estimated mill states and advanced control schemes developed for mills such as 2020年8月12日 This study shows the performance of a currently running vertical roller coal mill (VRM) in an existing coalfired power plant In a power plant, the coal mill is the critical equipment, whose An investigation of performance characteristics and 2024年8月22日 cast abrasionresistant liners and partially filled with hardened steel balls Coal and preheated primary air enter one or both ends of the mill from a crusher/dryer or feeder As the mill rotates, the balls cascade and pulverize the coal by impact and attrition The pulverized coal is then conveyed by air to centrifugal classifiersA Comparison of Three Types of Coal Pulverizers2019年1月1日 The work in this part is based on a ZGM113N medium speed coal mill equipped in a subcritical 600MW unit Combined with existing research [1, 53] and relevant theoretical knowledge [54], 15 Abnormal Condition Monitoring and Diagnosis for Coal Mills
.jpg)
Optimization and transformation of 300MV units steel
2023年11月7日 Content from this work may be used under the terms of the CreativeCommonsAttribution 30 licence Any further distribution of this work must maintain attribution to the author(s) and the title of 2023年2月7日 Coal mill modeling with nonlinear differential equations of coal mill includes primary air, coal quantity, and outlet temperature mill [4] In this study, the lumped parameter modeling method is adopted with the following assumptions: 1) LowRank Call (LRC) coal modeling using coal moisture data parameters; 2)International Journal of Scientific Engineering 2009年9月20日 The ball tube mill requires less mass flow rate of primary air and raw coal per MW of power produced than the bowl mill It contains larger mass of raw and pulverized coal but less grinding heat (PDF) Modeling and Parameter Identification of Coal MillCoal mill is an important component of the thermal power plant It is used to grind and dry the moisturized raw coal and transport the pulverized coal – air mixture to the boiler Poor dynamic performance of coal mill will lead to decrease in the overall efficiency of the power plant, slow load take up rate and frequent shut down(PDF) Modeling and Control of Coal Mill Academia
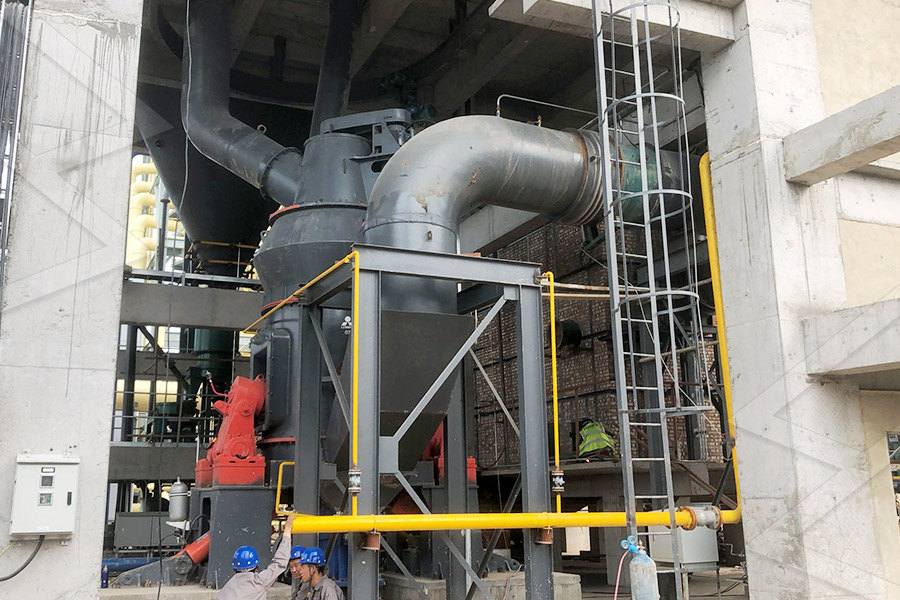
Mixing Characteristics and Flow Fields Optimization of Primary Air
2023年1月1日 In a pulverized coalfired (PCF) thermal power plant (TPP), mixture of coal, air and gas is supplied into the furnace volume via the mill duct system and coal/air distribution should ideally be 2021年8月1日 A root cause failure analysis of coal mill vertical shaft used in thermal power plant has been carried out The failed parts of the shaft showed the signature of fatigue failuresFault analysis and optimization technology of HP bowl type 2018年5月2日 Coal mill malfunctions are some of the most common causes of failing to keep the power plant crucial operating parameters or even unplanned power plant shutdowns Therefore, an algorithm has been developed that Detection of Malfunctions and Abnormal Cold Air Locking at Mill Inlet: This is very important for coal mill, as ambient air throttling the drying capacity of mill as well as increases the oxygen content of kiln gases making it riskier Oxygen percentage of more than 1214% is considered catalyst for fire/explosion riskCoal Grinding Cement Plant Optimization
.jpg)
Optimization of windandwater coordinated dust reduction
2024年8月1日 Designed windandwater coordinated dust reduction device And through the spray experiment platform and CFD simulation software, the droplet size, fog field concentration and effective fog field height of the device were analyzed, and the optimal spray pressure, fan air volume and nozzle diameter of the device were obtained2012年12月31日 This phenomenon reveals that during combustion the emission of fine PM, especially the PM 25 , is greatly affected by coal fineness, which is consistent with the work by Ninomiya et al (2004)The Research on Design Parameters of Fan Mill Direct 2015年9月1日 Introducing an urban wind turbine in the crowded and complex City of North Sydney built environment can provide a significant opportunity to generate onsite wind energy and reduce electric demand (PDF) Site Selection for Wind Farm Installation ResearchGate2021年3月14日 The flow, combustion, heat transfer and NOx emission characteristics of a 600 MW subcritical Wflame boiler were numerically simulated under different combined operation modes of coal mills, and Combined operation mode of subcritical Wflame boiler and coal mill
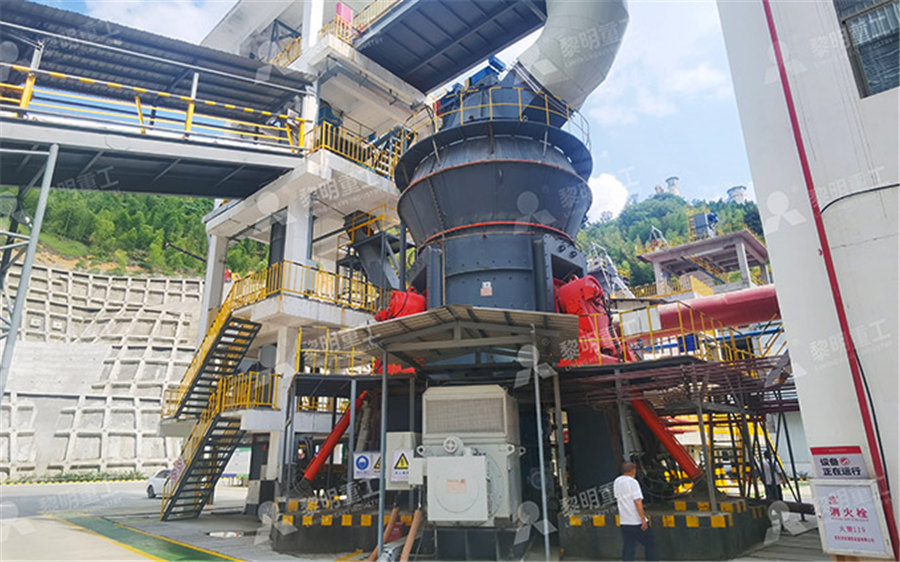
PERFORMANCE ANALYSIS OF COAL MILLS SlideServe
2012年1月23日 PERFORMANCE ANALYSIS OF COAL MILLS P M V Subbarao Associate Professor Mechanical Engineering Department IIT Delhi Correct Size, shape and quantity of Diet For Complete Digestion Combustion Limits on Furnace Design • The lower limit of the furnace volume is dominated by the space required for burning the fuel completely, or • to an 2014年1月1日 The emission factors of kiln end, kiln head, coal mill, crushing and cement mill was 0156 clinker g/t, 3914 clinker g/t, 1538 coal g/t, 0016 stone g/t and 0056 cement g/t respectively, the (PDF) MPS mills for coal grinding ResearchGate2013年11月20日 Coal mill is an important component of the thermal power pla nt It is used to grind and dry the moisturized raw coal and transport the pulverized coal ± air mixture to the boiler Poor dynamic performance of coal mill will lead to decrease in the overall efficiency of the power plant, slow load take up rate and fr equent shut downModeling and Control of Coal Mill NTNU2015年11月1日 The coal mill grinds the raw coal into fine powder and hot air entering the mill dries and carries the pulverized coal to the burners of the furnace Maffezzoni (1986 ) emphasized that coal mills are the primary cause of slow load following capability and regular plant shutdownsA unified thermomechanical model for coal mill operation
.jpg)
Mill Inerting and Pulverizer/Mill Explosion Mitigation
2018年6月7日 undertable, reject area, pyrite area or primary air inlet wind box depending on the type of mill Fogging and deluge systems can be very effective at “washing” away hazards air to coal ratios of 2:1 or less Coal Mill Air to fuel ratios are higher during: – Startup – Shutdown2020年12月8日 The air to fuel ratio is regarded here to be the total air leaving the mills divided by the total coal flow; therefore, it might be different from some AFRs in the literature because of the (PDF) A Control Strategy of the Air Flow Rate of CoalFired 2024年2月20日 This document provides a draft design guide for inerting medium speed vertical spindle coal pulverizers It discusses inerting system design considerations such as inerting media selection, steam source considerations, and steam piping considerations The most common inerting media are steam, CO2, and N2, with steam being the most commonly used The Inerting Steam For Coal Mill Fire PDF PDF Combustion2020年4月7日 The primary air system of a coal mill is mainly responsible for two tasks of coal po wder drying and transmitting The inlet primary air flow is mainly determined according to the differential(PDF) Modeling of Coal Mill System Used for Fault Simulation
.jpg)
Derivation and validation of a coal mill model for control
2012年5月1日 Coal fired power plants are heavily used due to large and long lasting coal resources compared with oil or natural gas An important bottleneck in the operation of this particular kind of plants, however, is the coal pulverization process, which gives rise to slow takeup rates and frequent plant shutdowns (Rees Fan, 2003)In typical coal fired power plants, The airswept ball mill has a similar structure to the ordinary mill, but the input size and the output size are less, and most of the power of the material is supported by wind The airswept coal mill is a critical component in coalfired power plants and industrial furnacesAir Swept Coal Mill Cement Plant Equipment Coal Grinding Mill2020年1月1日 Coal mills have a significant influence on the reliability, efficiency, and safe operation of a coalfired power plant Coal blockage is one of the main reasons for coal mill malfunctionEarly Warning of Critical Blockage in Coal Mills Based on 2024年5月10日 The objective of this study is to perform an analysis to determine the most suitable type of wind turbine that can be installed at a specific location for electricity generation, using annual Wind energy resource assessment and wind turbine selection
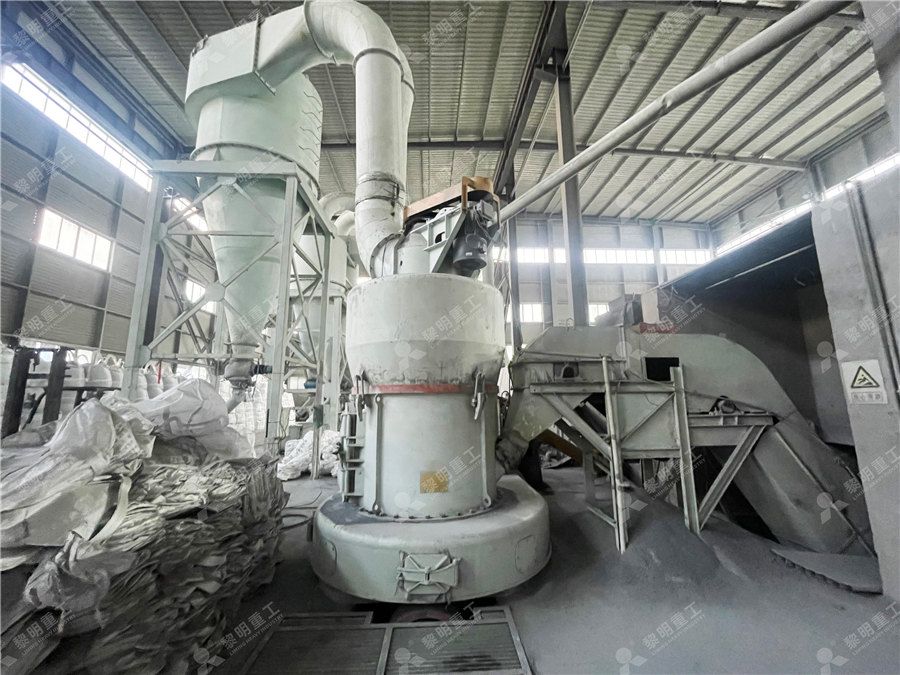
Coal mill model considering heat transfer effect on mass
2021年8月1日 Yukio et al [7] proposed a model consisting of blending, grinding and classifying processes for pulverizer control Agarawal et al [8] differentiated coal powder into ten size groups, divided the bowl mill into four zones, and developed a unified model Palizban et al [9] derived nonlinear differential mass equations of raw coal, recirculation coal and suspension coal in 2020年8月12日 To understand the performance of a vertical roller coal mill, the real operational tests have been performed considering three different coal sources Obtained results indicate that grinding pressure, primary air (PA) temperature and mill motor current have a tendency to rise by increasing coal feeding mass flow rates for all used coalAn investigation of performance characteristics and 2015年8月1日 This paper is organized as follows: Section 2 provides an understanding of the mill system together with the control issues and major faults influencing the mill performance Section 3 deals with the review of different control strategies applied to the milling system Control using estimated mill states and advanced control schemes developed for mills such as Review of control and fault diagnosis methods applied to coal mills2020年8月12日 This study shows the performance of a currently running vertical roller coal mill (VRM) in an existing coalfired power plant In a power plant, the coal mill is the critical equipment, whose An investigation of performance characteristics and
.jpg)
A Comparison of Three Types of Coal Pulverizers
2024年8月22日 cast abrasionresistant liners and partially filled with hardened steel balls Coal and preheated primary air enter one or both ends of the mill from a crusher/dryer or feeder As the mill rotates, the balls cascade and pulverize the coal by impact and attrition The pulverized coal is then conveyed by air to centrifugal classifiers2019年1月1日 The work in this part is based on a ZGM113N medium speed coal mill equipped in a subcritical 600MW unit Combined with existing research [1, 53] and relevant theoretical knowledge [54], 15 Abnormal Condition Monitoring and Diagnosis for Coal Mills 2023年11月7日 Content from this work may be used under the terms of the CreativeCommonsAttribution 30 licence Any further distribution of this work must maintain attribution to the author(s) and the title of Optimization and transformation of 300MV units steel 2023年2月7日 Coal mill modeling with nonlinear differential equations of coal mill includes primary air, coal quantity, and outlet temperature mill [4] In this study, the lumped parameter modeling method is adopted with the following assumptions: 1) LowRank Call (LRC) coal modeling using coal moisture data parameters; 2)International Journal of Scientific Engineering
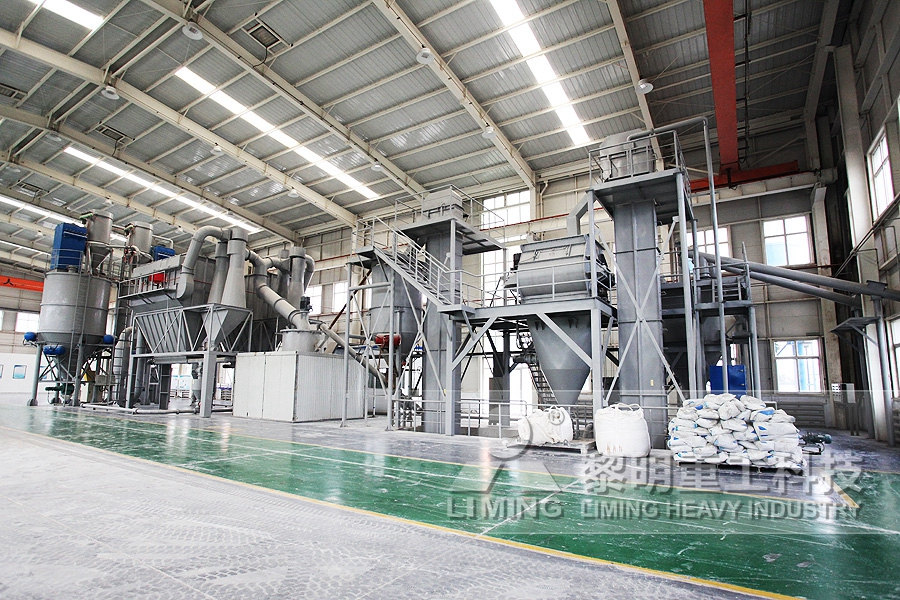
(PDF) Modeling and Parameter Identification of Coal Mill
2009年9月20日 The ball tube mill requires less mass flow rate of primary air and raw coal per MW of power produced than the bowl mill It contains larger mass of raw and pulverized coal but less grinding heat Coal mill is an important component of the thermal power plant It is used to grind and dry the moisturized raw coal and transport the pulverized coal – air mixture to the boiler Poor dynamic performance of coal mill will lead to decrease in the overall efficiency of the power plant, slow load take up rate and frequent shut down(PDF) Modeling and Control of Coal Mill Academia