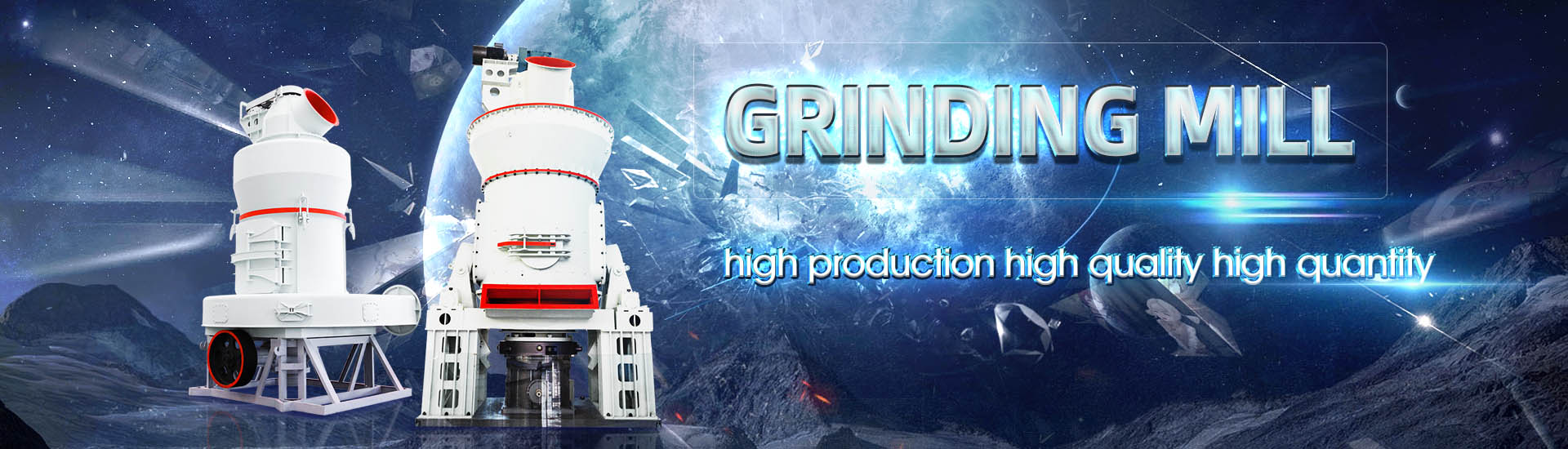
Simple processing equipment for cleaning coal powder
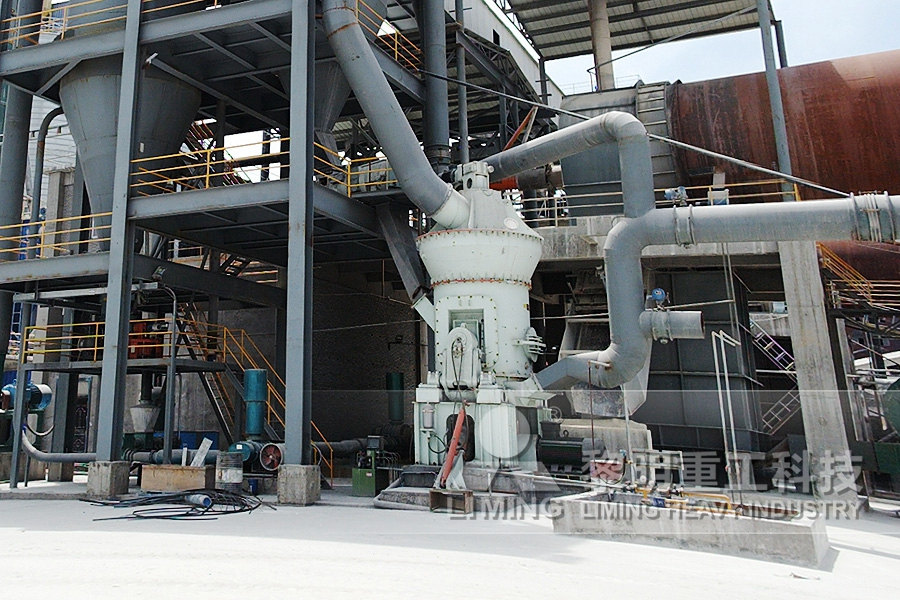
Clean Coal Processing Eriez
magnetic separation equipment by partnering with Erie, PAbased Eriez The use of specialized magnetic separation equipment for coal processing involves a variety of magnet strengths, models, and operating efficiency For example, suspended electromagnets (SEs) help remove 2001年1月1日 The present work is a review and critical assessment of topics relevant to dry processing of coal, comprising comminution, size classification, characterisation and analysis, sorting at coarse(PDF) Pneumatic dry Cleaning of Coal ResearchGateCoal cleaning was largely developed to remove ashforming minerals from coking coal The cokemaking industry has long recognized the benefits of clean coal, and most of the coal used by CHAPTER 3 Coal Preparation and Cleaning2015年7月1日 Unlike coarse coal cleaning, fine coal separation is characterized by numerous equipment options and several flowsheet variations While flotation is widely used for the A review of stateoftheart processing operations in coal
.jpg)
Coal Preparation and Cleaning SpringerLink
Most coal requires some preparation before use Preparation may range from simply crushing to provide a size consist suitable for certain types of boilers to extensive size reduction and By absorbing technologies from home and abroad and combining demand of market, kefid launched a series of grinding mill that used for making coal powder We recommend the What is the cleaning equipment used for making coal powder?Dry coal cleaning has claimed an important place in the current coal processing technology The most important and reliable plants include rotary breakers, air jigs, FGX separators, air dense Coal Cleaning an overview ScienceDirect Topics2019年4月1日 Large vibrating screen is the key equipment to improve the clean and efficient utilization of coal In recent years, various advanced design techniques and methods have A review on the advanced design techniques and methods of
.jpg)
Coal Centrifuges SIEBTECHNIK TEMA
coal centrifuges operating in worldwide coal preparation plants In order to improve the processing capacity of this equipment, SIEBTECHNIK has developed clean coal centrifuge with larger 2023年1月21日 Among all the separation technologies, gravitybased separation is the most commonly used for coal cleaning because they are robust, easy to operate and maintain, Conventional and recent advances in gravity separation 2014年1月1日 The use of coal is negatively perceived, since the use of fossil fuels in power generation and other industry sectors contributes significantly to the CO 2 emissions worldwide Of the main fossil fuels, coal has the lowest H:C ratio, and consequently coal has the highest CO 2 footprint per unit of combustion energy produced Coal also contains percentage levels of Coal Processing and Use for Power Generation ScienceDirect2024年1月11日 With a vertical roller mill (VRM) VRMs consist of a rotating table or bowl and rollers 1 To grind the coal, feed raw or initially crushed coal into the mill which is then ground between the rotating components; 2 Finally, hot air How to Process Coal into Pulverized Coal in 5 Steps?
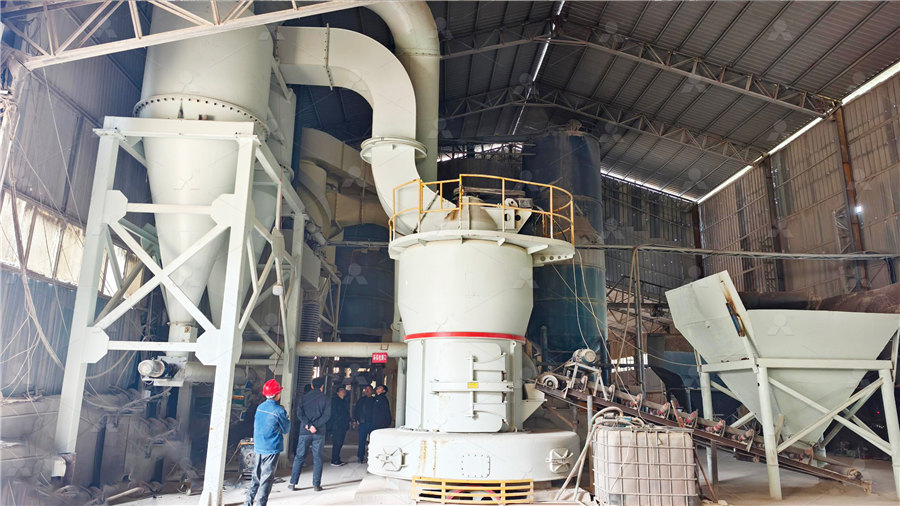
What Is Coal Preparation? Energygov
Levels of Coal Cleaning • Level 1 – Rough Scalping and Crushing • Level 2 – Coarse Coal (+1/2 inch) Cleaning – Coarse, Fine, and Ultra Fine Coal Cleaning • Level 5 – Level 4 Cleaning plus middlings crushing and rewash EquipmentCleaning • Conventional – Heavy media separators (vessels and cyclones) – Pulse water 2 Steps for using coal powder for boilers 1)Coal powder preparation: Select suitable coal as raw material based on the combustion requirements and coal quality characteristics of the boiler; The raw coal is crushed into small pieces by a crusher and then sent to a coal mill for grinding to prepare coal powder that meets the requirements of boiler combustionGuilin Hongcheng HMM Series Bowl Coal Mill Promoting Efficient, Clean 2015年7月1日 Unlike coarse coal cleaning, fine coal separation is characterized by numerous equipment options and several flowsheet variations While flotation is widely used for the fraction below 150 μm, particles from 1 mm to 150 μm can be processed by one or more waterbased, gravity separationsA review of stateoftheart processing operations in coal preparation 2023年5月3日 Manufacturer of coal processing and cleaning equipment, specifically vibrating trays Features 40 tons of coals per hour cleaning rate Other products include single and dualfrequency reaction cells, hexagon and sonochemical reaction vessels, ultrasonic power probes and slide processors, sonic shoes, and minimegasonic dropin transducersCoal Processing Equipment Suppliers Thomasnet
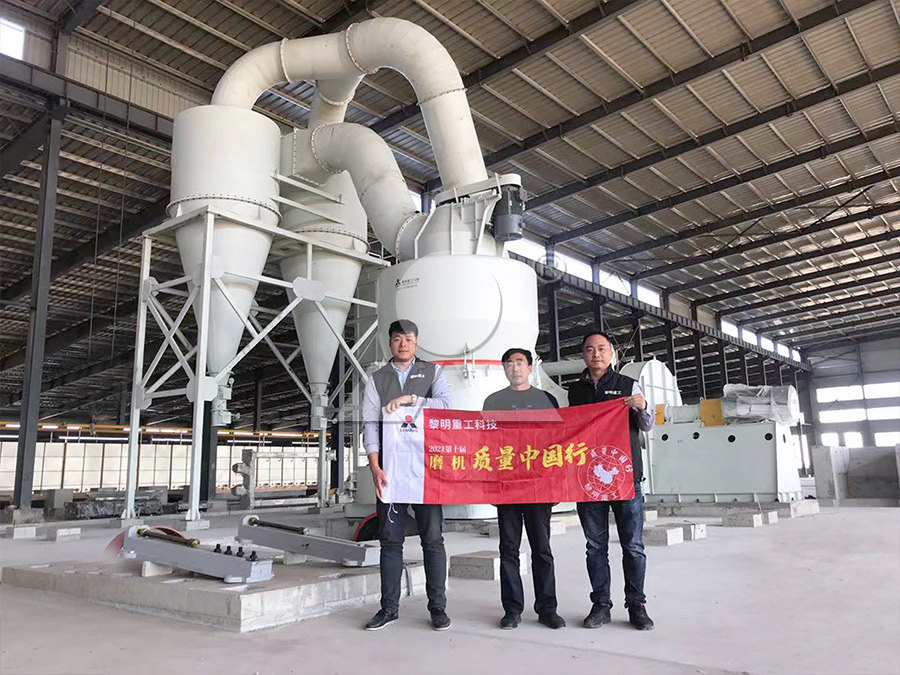
(PDF) Coal preparation plant optimization: A critical review of
2006年4月1日 Conventional floatsink testing is considered the standard test method for generating coal washability data (Temel, Majumder, and Bakır 2015, Galvin 2006, Callen et al 2002, Callen et al 2008 distribution curves for the plant’s cleaning equipment, generate a report detailing the performance screens, centrifuges, magnetic separators and other processing equipment while provide specific, workable recommendations to help you resolve any issues Optimizing the performance of a coal prep plant can increase profits with only a smallCoal Preparation Plant Services In Plant SGS2019年4月1日 In reality, a large vibrating screen, which has a screen surface width of no less than 36 m and a screening area of no less than 200m 2, usually oscillates with extremely complex dynamic characteristics of the screen body [10,11]As shown in Fig 2 (b), generally, except for the dominated strong alternating load yielded by two boxtype exciters, a large A review on the advanced design techniques and methods of 2018年7月21日 (The POC scale is intermediate to those of pilot plant and demonstration plant) The design and performance specifications for the plant were 1) at least 85% pyriticsulfur rejection; 2) at least 85% energy recovery; 3) no more than 6% ash in the final clean coal product; and 4) a final clean coal and refuse moisture content of 35% or lessCoal Cleaning Technology 911Metallurgist
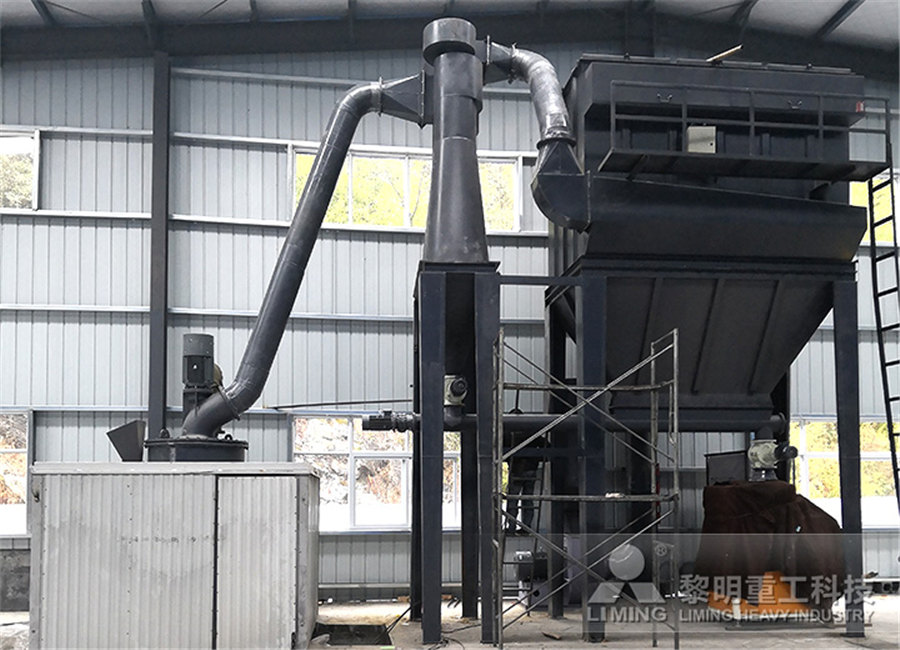
Environmental, Health and Safety Guidelines for Coal Processing
filtration for pn eumatic coal cleaning equipment; • Use of enclosed conveyors combined with e xtraction and filtration equipment on conve yor transfer points ; and • Suppression of dust during coal processing (eg, crushing, sizing, and drying) and transfer (eg, conveyor systems) using, for example, ware spraying systems with waterJanuary 1976 (40 CFR Subpart Y) These standards specify emission limits for PM from coal cleaning thermal dryers and pneumatic cleaning equipment sources, and opacity limits for fugitive emissions from coal processing and conveying equipment, coal storage systems, and coal transfer and loading systems 11/95 Coal Cleaning 111031110 Coal Cleaning US EPA2015年7月1日 Unlike coarse coal cleaning, fine coal separation is characterized by numerous equipment options and several flowsheet variations While flotation is widely used for the fraction below 150 μm, particles from 1 mm to 150 μm can be processed by one or more waterbased, gravity separationsA review of stateoftheart processing operations in coal preparation Coal fired power plants also known as coal fired power stations are facilities that burn coal to make steam in order to generate electricityThese stations, seen in Figure 1, provide ~40% of the world's electricity Countries such as South Africa use coal for 94% of their electricity and China and India use coal for 7075% of their electricity needs, however the amount of coal China Coal fired power plant Energy Education
.jpg)
(PDF) Conventional and recent advances in gravity separation
2023年2月1日 Conventional and recent advances in gravity separation technologies for coal cleaning: A systematic and critical review2010年3月1日 Application of energy system models for designing a lowcarbon society Toshihiko Nakata, Mikhail Rodionov, in Progress in Energy and Combustion Science, 2011 247 Clean coal technologies Clean coal technologies (CCTs) for energy generation describe a new generation of energy processes that sharply reduce air emissions and other pollutants Clean Coal Technology an overview ScienceDirect Topics2018年3月1日 Vibrating screen is the key screening equipment in coal cleaning With the increase in coal production, vibrating screen with large processing capacity, high reliability, and excellent screening Impact of screening coals on screen surface and multiindex 2023年1月1日 The flowsheet for a coal preparation plant can typically be represented by a series of sequential unit operations for sizing, cleaning, and dewatering (Fig 181)This sequence of steps is repeated for each size fraction, since the processes used in modern plants have a limited range of applicability in terms of particle size (Osborne, 1988)Optimization, simulation, and control of coal preparation plants
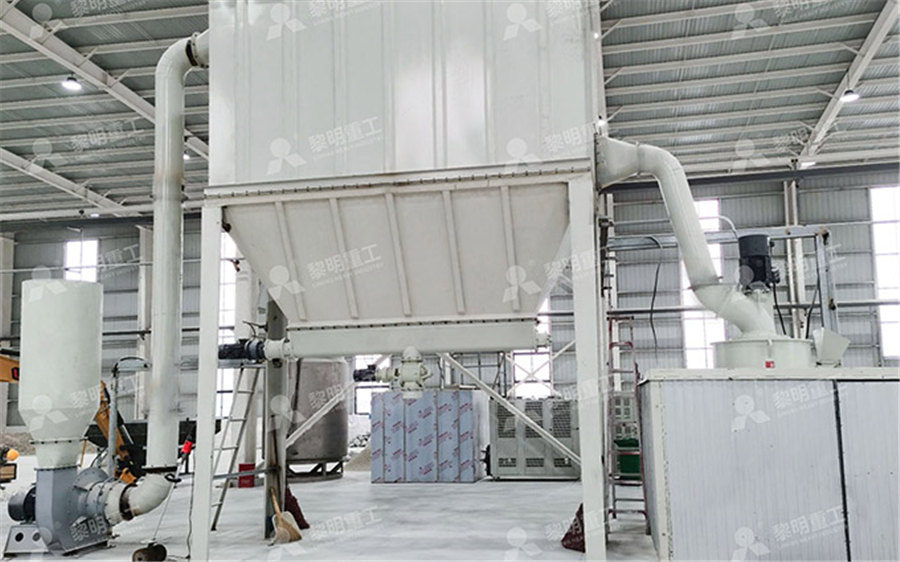
Bulk material powder handling equipment Matcon IBC
Industrial Powder Blending Highly effective blending of powder with quick cleaning in between batches – achieve high OEE rates with an IBC Industrial Mixer The use of IBCs as the blending vessel means faster loading unloading of the IBC Tumble Blender, along with no cleaning downtime (as the IBCs are cleaned offline), eliminating the wasted time associated with 2011年12月31日 Lignite and bituminous coals will be tested for the oxycoal combustion and CO2 capture The flue gas cleaning system comprises electrostatic precipitator (ESP), scrubber and condenser(PDF) Flue Gas Cleaning for CO2 Capture from Coalfired Oxyfuel Clean Coal Processing OnlineTEs June/July 2010 pg 34 Clean Coal Processing Coal is pulverized into fine powder, for proper combustion, and then it is fed to boil aration equipment for coal processing involves a variety of magnet strengths, models, and operating efficiencyClean Coal Processing EriezThe project is to build a highefficiency clean coal powder production line with an annual output of 300,000 tons for customers in Vietnam Customers specialize in the coal powder products business, processing coal into highefficiency clean 20tph Coal Ball Mill for Clean Coal Powder
.jpg)
Coal Mining and Processing The National Academies
The term coal quality is used to distinguish the range of different commercial steam coals that are produced directly by mining or are produced by coal cleaning 3 Generally, coal quality for steam coals (ie, coal used for electricity for coal processing Since pull strength of today’s magnets is much greater than its predecessors, magnetic separators are an even more effective tool for preventing costly damage and shutdowns Through the installation of advanced magnetic separation equipment, coal processing operations are running more efficiently than ever before eriezClean Coal Processing2022年10月10日 Clean coal technology is one of the most economical and practical technologies to optimize highsulfur coal resources and simple treatment equipment, 7632% However, the recovery rate of clean coal was only 6435% During magnetic separation, a certain amount of coal powder is brought out in the processing of Desulfurization mechanism of highsulfur coal by heating reduced 2019年10月1日 This results in a significant amount of fine coal reporting to the plant which also requires to be processed at low relative densities in order to yield coking coal Processing of the coal at low A simple and efficient process for smallscale cleaning of poorly
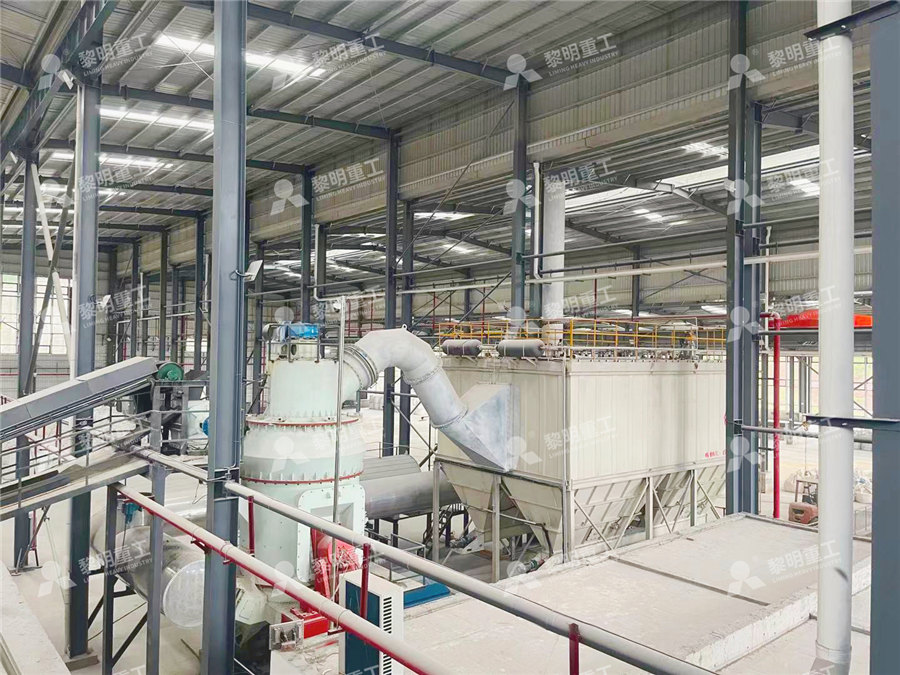
Clean Coal Processing Eriez
Clean Coal Processing OnlineTEs June/July 2010 pg 34 Clean Coal Processing Coal is pulverized into fine powder, for proper combustion, and then it is fed to boil aration equipment for coal processing involves a variety of magnet strengths, models, and operating efficiencyPowder Blending Features: » Easy access for cleaning and maintenance » Available in a range of sizes from 100 to 25,000 liter capacity » Low energy, gentle mixing action with minimal heat generation » Rapid mixing with fast and full discharge guaranteed » Minimum wear even when processing highly abrasive materialsPowder Processing Equipment Systems Qlar2023年1月21日 Clean coal technologies can be divided into three categories: (i) precombustion technologies (eg, coal cleaning, coal briquetting, coal liquid mixture, coal liquefaction, coal gasification): that pretreats coal using physical and/or chemical methods to remove undesirable substances and impurities, such as dust, ash, rocks, and pyritic sulfur [, , , , ], (ii) in Conventional and recent advances in gravity separation 2022年2月24日 Production of clean pulverized coal for boiler combustion heating and power supply Fineness: 200 mesh, D8090, according to the needs of backend combustion Suitable coal types: bituminous coal, anthracite, blue carbon, etc The production of clean pulverized coal is used for boiler combustion heating and power supply to improve the operating efficiency of How is pulverized coal processed? SBM Ultrafine Powder
.jpg)
Coal Processing and Use for Power Generation ScienceDirect
2014年1月1日 The use of coal is negatively perceived, since the use of fossil fuels in power generation and other industry sectors contributes significantly to the CO 2 emissions worldwide Of the main fossil fuels, coal has the lowest H:C ratio, and consequently coal has the highest CO 2 footprint per unit of combustion energy produced Coal also contains percentage levels of 2024年1月11日 With a vertical roller mill (VRM) VRMs consist of a rotating table or bowl and rollers 1 To grind the coal, feed raw or initially crushed coal into the mill which is then ground between the rotating components; 2 Finally, hot air How to Process Coal into Pulverized Coal in 5 Steps?Levels of Coal Cleaning • Level 1 – Rough Scalping and Crushing • Level 2 – Coarse Coal (+1/2 inch) Cleaning – Coarse, Fine, and Ultra Fine Coal Cleaning • Level 5 – Level 4 Cleaning plus middlings crushing and rewash EquipmentCleaning • Conventional – Heavy media separators (vessels and cyclones) – Pulse water What Is Coal Preparation? Energygov2 Steps for using coal powder for boilers 1)Coal powder preparation: Select suitable coal as raw material based on the combustion requirements and coal quality characteristics of the boiler; The raw coal is crushed into small pieces by a crusher and then sent to a coal mill for grinding to prepare coal powder that meets the requirements of boiler combustionGuilin Hongcheng HMM Series Bowl Coal Mill Promoting Efficient, Clean
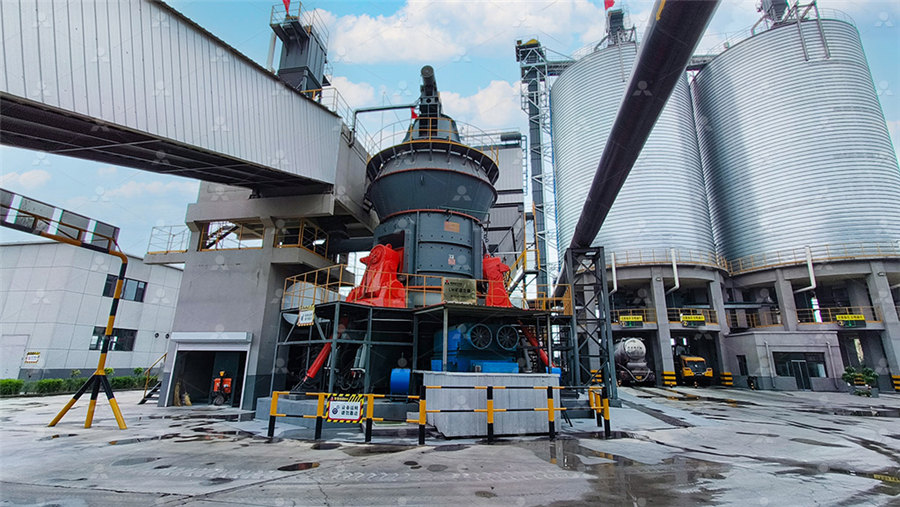
A review of stateoftheart processing operations in coal preparation
2015年7月1日 Unlike coarse coal cleaning, fine coal separation is characterized by numerous equipment options and several flowsheet variations While flotation is widely used for the fraction below 150 μm, particles from 1 mm to 150 μm can be processed by one or more waterbased, gravity separations2023年5月3日 Manufacturer of coal processing and cleaning equipment, specifically vibrating trays Features 40 tons of coals per hour cleaning rate Other products include single and dualfrequency reaction cells, hexagon and sonochemical reaction vessels, ultrasonic power probes and slide processors, sonic shoes, and minimegasonic dropin transducersCoal Processing Equipment Suppliers Thomasnet2006年4月1日 Conventional floatsink testing is considered the standard test method for generating coal washability data (Temel, Majumder, and Bakır 2015, Galvin 2006, Callen et al 2002, Callen et al 2008 (PDF) Coal preparation plant optimization: A critical review of distribution curves for the plant’s cleaning equipment, generate a report detailing the performance screens, centrifuges, magnetic separators and other processing equipment while provide specific, workable recommendations to help you resolve any issues Optimizing the performance of a coal prep plant can increase profits with only a smallCoal Preparation Plant Services In Plant SGS
.jpg)
A review on the advanced design techniques and methods of
2019年4月1日 In reality, a large vibrating screen, which has a screen surface width of no less than 36 m and a screening area of no less than 200m 2, usually oscillates with extremely complex dynamic characteristics of the screen body [10,11]As shown in Fig 2 (b), generally, except for the dominated strong alternating load yielded by two boxtype exciters, a large 2018年7月21日 (The POC scale is intermediate to those of pilot plant and demonstration plant) The design and performance specifications for the plant were 1) at least 85% pyriticsulfur rejection; 2) at least 85% energy recovery; 3) no more than 6% ash in the final clean coal product; and 4) a final clean coal and refuse moisture content of 35% or lessCoal Cleaning Technology 911Metallurgist