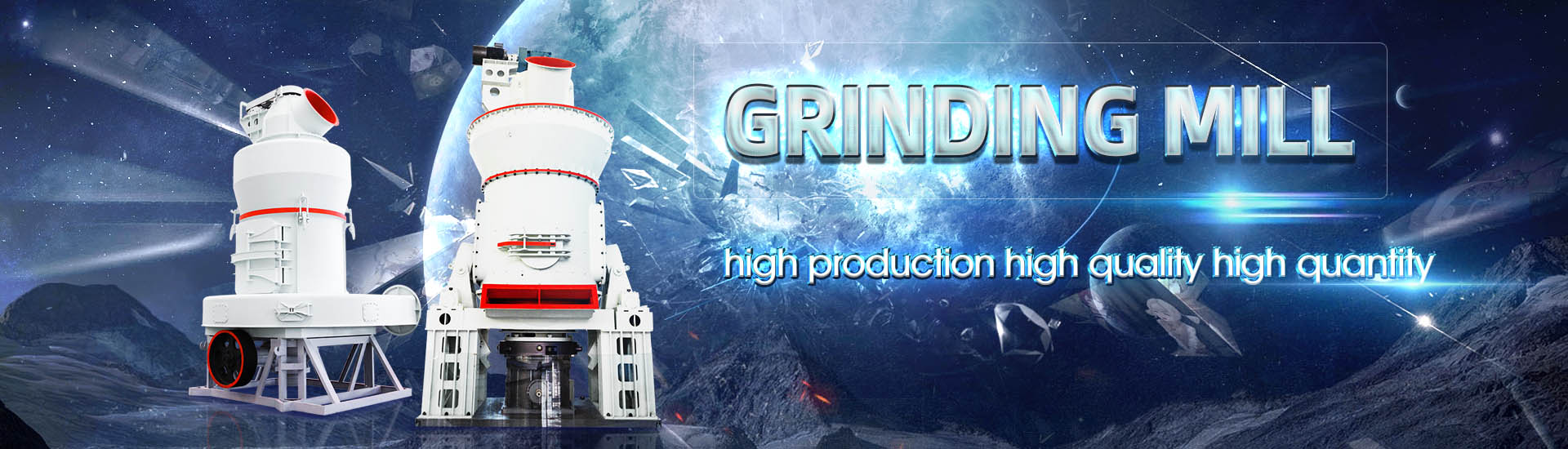
HOME→Introduction to the process flow of the cement grinding station Introduction to the process flow of the cement grinding station Introduction to the process flow of the cement grinding station
Introduction to the process flow of the cement grinding station Introduction to the process flow of the cement grinding station Introduction to the process flow of the cement grinding station
.jpg)
Cement grinding optimisation ScienceDirect
2004年11月1日 This paper describes the tools available for the analysis and optimisation of cement grinding circuits The application of the Bond based methodology as well as The purpose of this study is to examine the production process, its economic support, raw material availability, demand, process modification, optimization steps to implement the production Typical cement manufacturing process flow diagram The following process steps are taking place in the system: 1 Drying 2 Coarse grinding 3 Fine grinding 4 Cooling and mill ventilation 5 Classification 6 Mill operation and control To Thomas Holzinger, Holzinger Consulting, grinding system tended chapter on alternative fuels Key sections covering raw materials, burning, grinding and quality control are supported by a range of chapters addressing critial topics such as The Cement Plant Operations Handbook International Cement
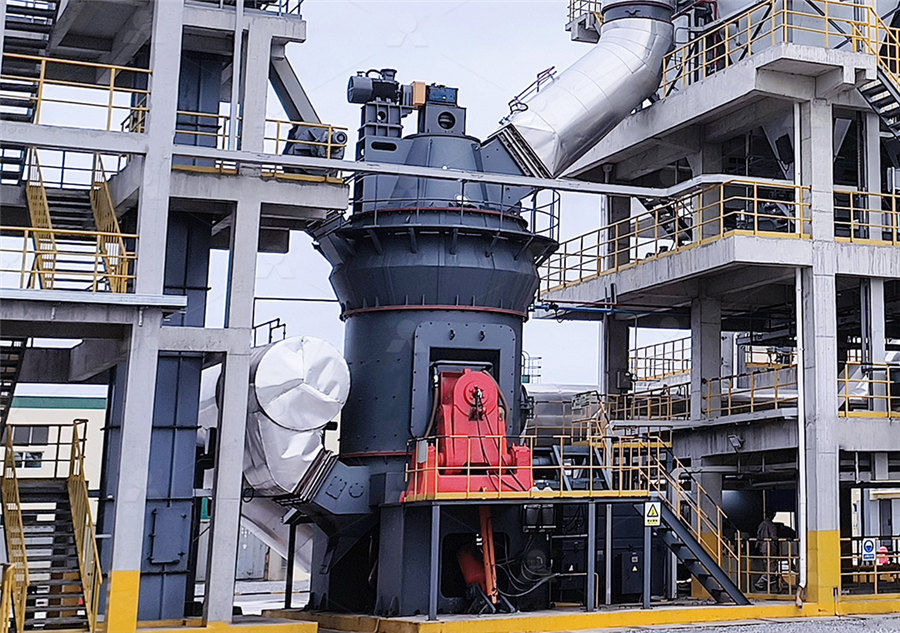
Cement Grinding Cement Plant Optimization
Highly energy intensive unit operation of size reduction in cement industry is intended to provide a homogeneous and super fine (30004000 Blain) cement Grinding operation is monitored for 2016年11月1日 The paper focusses on improving the energy utilization of a cement grinding circuit by changing the flow sheet of the process The circuit was comprised of ball mill, static Simulation aided flow sheet optimization of a cement grinding 2021年3月9日 In this study the process flow diagram for the cement production was simulated using Aspen HYSYS 88 software to achieve high energy optimization and optimum cement Simulation and Optimization of an Integrated Process Flow Sheet l electrical energy used for the production of cement The optimization of this process would yield substantial be the grinding process, maintenance and product quality The objective is to OPTIMIZATION OF CEMENT GRINDING OPERATION IN BALL MILLS
.jpg)
Simulation and Optimization of an Integrated Process Flow Sheet
2021年3月9日 In this study the process flow diagram for the cement production was simulated using Aspen HYSYS 88 software to achieve high energy optimization and optimum cement flow rate by varying the flow 2021年4月2日 1111 Chemical Compositions Four main compounds make up Portland cement They include tetracalcium aluminoferrites (4CaOAl 2 O 3 Fe 2 O 3), tricalcium aluminates (3CaOAl 2 O 3), dicalcium silicates (2CaOSiO 2), and tricalcium silicates (3CaOSiO 2) (Demis et al 2014)These compounds are abbreviated as C 3 S, C 2 S, C 3 A, and C 4 AF, Introduction to the Principles of Cement and Concrete CompositesStage 2: Grinding, Proportioning, and Blending The crushed raw ingredients are made ready for the cementmaking process in the kiln by combining them with additives and grinding them to ensure a fine homogenous mixture The composition of cement is proportioned here depending on the desired properties of the cement Generally, limestone is 80%, and the remaining 20% How Cement is Made Cement Manufacturing Process2019年1月3日 Clinker grinding technology is the most energyintensive process in cement manufacturing Traditionally, it was treated as "low on technology" and "high on energy" as grinding circuits use more than 60 per cent of total energy consumed and account for most of the manufacturing cost Since the increasing energy cost started burning the benefits significantly, Clinker grinding technology in cement manufacturing
.jpg)
Cement Grinding Station Solution Ball Mill and Vertical Mill
The new cement grinding process includes mixed material crushing, cement batching station, pregrinding, high fine grinding, fine powder separation, dust treatment, automatic control and other technologies, so that cement high yield, high quality, energy saving, in line with the requirements of energy saving and emission reductionCement production involves quarrying limestone and clay, grinding and blending the materials, burning them at high temperatures to form clinker, and finely grinding the clinker to produce cement powder The key steps are: 1) Quarrying limestone and clay and grinding them to powder; 2) Blending the powders in precise proportions; 3) Burning the blend at high heat to form Chapter 1 Introduction To Cement Production2021年3月9日 In this study the process flow diagram for the cement production was simulated using Aspen HYSYS 88 software to achieve high energy optimization and optimum cement flow rate by varying the flow rate of calcium oxide and silica in the clinker feed Central composite Design (CCD) of Response Surface Methodology was used to design the ten experiments for Simulation and Optimization of an Integrated Process Flow Sheet 2014年6月10日 Evolution of the cement Process • Wet process easiest to control chemistry better for moist raw materials • Wet process high fuel requirements fuel needed to evaporate 30+% slurry water • Dry process kilns less fuel requirements • Preheater/Precalciner further enhance fuel efficiency allow for high production ratesCement manufacturing process PPT Free Download SlideShare
.jpg)
Analysis of material flow and consumption in cement production process
2015年8月1日 The results show that approximately 248t, 469t, and 341t of materials are required to produce a ton of the product in raw material preparation, clinker production, and cement grinding stages 2023年8月21日 Tushar Khandhadia, General Manager – Production, Udaipur Cement Works, discusses the role of grinding in ensuring optimised cement production and a high quality end product How does the grinding process contribute to the production of highquality cement?The quality of cement depends on its reactive properties and particle size grinding helps to reduce Grinding process is a critical stage in cement productionThe final manufacturing stage at a cement plant is the grinding of cement clinker from the kiln, mixed with 45% gypsum and possible additives, into the final product, cement In a modern cement plant the total consumption of electrical energy is about 100 kWh/t The cement grinding process accounts for approx 40% if this energy consumptionCEMENT GRINDING SYSTEMS INFINITY FOR CEMENT EQUIPMENT2016年1月20日 In the surveyed cement plant, three balances are established between input and output material in the raw mill, clinker production, and cement grinding system 248 t, 469 t, and 341 t of materials are required to produce a ton of the product in raw material preparation, clinker production, and cement grinding stages; waste gases account for the largest proportion of the Analysis of material flow and consumption in cement production process
.jpg)
Typical cement manufacturing process flow
Finally, during the cement grinding and distribution process, firstly the cooled clinker is ground with around 5% of gypsum and other 17 JRTE2020 cementitious materials to form the final cement CEMENT PRODUCTION AND QUALITY CONTROL A Cement manufacturing Process Source:civilengineeringforumme The whole process of cement manufacturing in Messebo Cement plant which consists of two separate Cement Production lines can be summarized into the following processes ;as can be seen in the process and Quality flow diagram below; 1CEMENT PRODUCTION AND QUALITY CONTROL A Cement manufacturing ProcessCement grinding operation may be performed in one of the following mill setups (ThyssenKrupp) A simplified process flow these separators is as follows Material is fed onto a rotating dispersion plate via air slide, whence it is dispersed off into the classifying air streamCement Grinding Cement Plant OptimizationThe details of the cement manufacturing process are very broad No two plants are the same and there may be differences within the same plant in particular since new kiln and their associated equipment can be added to existing ones: for example, wet and dry processes can operate side by side using the same raw materials and producing the same final product and having An introduction to Portland Cement Manufacturing
.jpg)
What is Grinding: Definition, Process, Types Specifications
2024年1月23日 The introduction of powerdriven grinding machines in the late 1800s marked a significant leap in the evolution of grinding technology These machines, The grinding process, integral to modern manufacturing, is not a onesizefitsall operation Depending on the workpiece’s shape, size, 2023年7月10日 Cement manufacturing is a significant industrial activity that plays a vital role in the construction sector However, the process of cement production is associated with various environmental Cement Manufacturing Process and Its Environmental Impact2016年10月5日 In this chapter an introduction of widely applied energyefficient grinding technologies in cement grinding and description of the operating principles of the related equip‐ ments and comparisons over each other in terms of grinding efficiency, specific energy consumption, production capacity and cement quality are given A case study per‐ formed on a EnergyEfficient Technologies in Cement Grinding1 INTRODUCTION The VRM is a type of grinding mill integrated with multi functions such as grinding, drying and separation, used for grinding of coal, petroleum coke and minerals Most recently this technology has been employed for comminution of Blended, Slag and Port Land cement grinding The cement grinding and dryingPROCESS CONTROL FOR CEMENT GRINDING IN VERTICAL
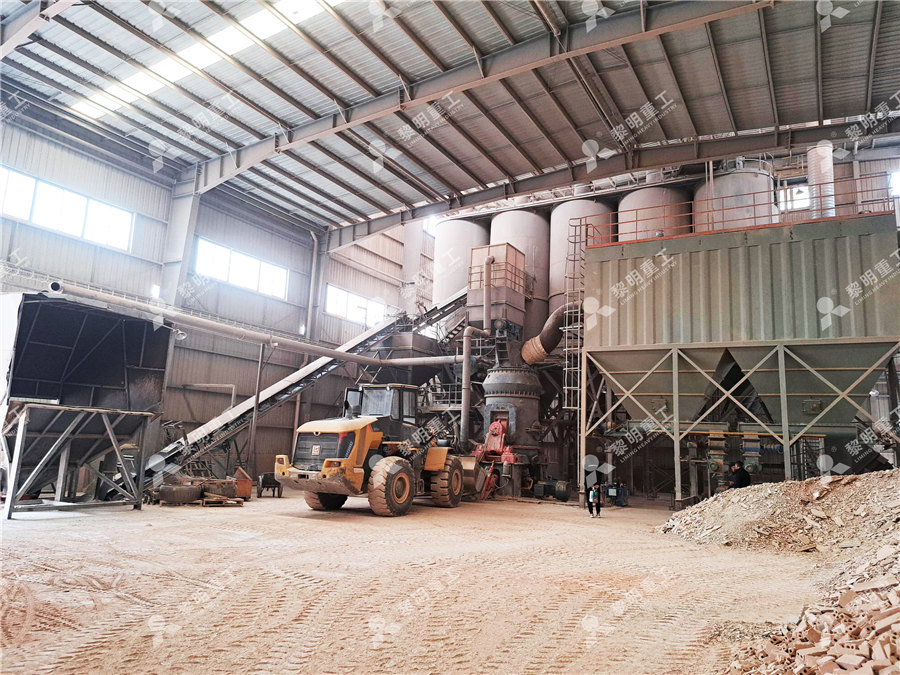
Thomas Holzinger, Holzinger Consulting, grinding system
grinding system optimisation Introduction The cement industry uses a wide range of different systems in raw material, coal, and cement grinding While new plants mainly focus on highly energy‑efficient systems, using roller comminution systems like vertical roller mills (VRMs) and high pressure grinding units (roller presses), less efficientClinker is ground with gypsum (36%) to adjust setting time Packing marketting Wet process Dry process Dry process with preheating tower THE CEMENT MANUFACTURING PROCESS • • • • • • • Quarry Grinding Burning (PDF) THE CEMENT MANUFACTURING PROCESS2019年10月29日 Cement grinding station introduction Cement grinding station is a production unit of cement finished products, which doesn’t include the last finished stage of the cement production process Cement Grinding StationPrice Preference and Process Description Cement clinker grinding unit, or called cement grinding plant, cement grinding station, is an individual grinding plant in the finished cement production Cement grinding plants are primarily used to produce finished cement products by grinding cement clinkers and moderate mixed materialsCement Grinding Plant CHAENG
.jpg)
The Cement Manufacturing Process Thermo Fisher Scientific
2023年12月20日 Accurate cement production also depends on belt scale systems to monitor output and inventory or regulate product loadout, as well as tramp metal detectors to protect equipment and keep the operation running smoothly The Cement Manufacturing Process flow chart sums up where in the process each type of technology is making a differencewould be a length of 135 m and a diameter of 25 m, with a speed of approximately 20 revolutions per minute Such a mill would normally have a load of approximately 90 tons of grinding media, graduated from 90 mm to 60 mm in the first chamber, 50 mm to 15 mm in the second chamber and 15 mm down in the final chamberAn Introduction to Clinker Grinding and Cement Storage2021年3月24日 Cement manufacturing requires cooling down of hot clinker at temperature of about 1350o C to temperature lower than 100 o C in a cooling system known as clinker coolerModelling of clinker cooler and evaluation of its performance in 2018年1月10日 3 INTRODUCTION TO CEMENT • Cement is a fine mineral powder manufactured with very precise processes Mixed with water, this powder transforms into a paste that binds and hardens when submerged in water Because the composition and fineness of the powder may vary, cement has different properties depending upon its makeupManufacturing of cement PPT Free Download SlideShare
.jpg)
Cement clinker grinding station, cement production plant
2023年9月18日 A cement grinding facility is purposebuilt for the specific task of grinding and pulverizing clinker, a critical element in cement manufacturing, into a finely powdered form This finely milledJune 2022; ARCHIVE Proceedings of the Institution of Mechanical Engineers Part C Journal of Mechanical Engineering Science 19891996 (vols 203210) 236(2):1107(PDF) A comprehensive review on the grinding process: 2021年3月9日 In this study the process flow diagram for the cement production was simulated using Aspen HYSYS 88 software to achieve high energy optimization and optimum cement flow rate by varying the flow Simulation and Optimization of an Integrated Process Flow Sheet 2021年4月2日 1111 Chemical Compositions Four main compounds make up Portland cement They include tetracalcium aluminoferrites (4CaOAl 2 O 3 Fe 2 O 3), tricalcium aluminates (3CaOAl 2 O 3), dicalcium silicates (2CaOSiO 2), and tricalcium silicates (3CaOSiO 2) (Demis et al 2014)These compounds are abbreviated as C 3 S, C 2 S, C 3 A, and C 4 AF, Introduction to the Principles of Cement and Concrete Composites
.jpg)
How Cement is Made Cement Manufacturing Process
Stage 2: Grinding, Proportioning, and Blending The crushed raw ingredients are made ready for the cementmaking process in the kiln by combining them with additives and grinding them to ensure a fine homogenous mixture The composition of cement is proportioned here depending on the desired properties of the cement Generally, limestone is 80%, and the remaining 20% 2019年1月3日 Clinker grinding technology is the most energyintensive process in cement manufacturing Traditionally, it was treated as "low on technology" and "high on energy" as grinding circuits use more than 60 per cent of total energy consumed and account for most of the manufacturing cost Since the increasing energy cost started burning the benefits significantly, Clinker grinding technology in cement manufacturingThe new cement grinding process includes mixed material crushing, cement batching station, pregrinding, high fine grinding, fine powder separation, dust treatment, automatic control and other technologies, so that cement high yield, high quality, energy saving, in line with the requirements of energy saving and emission reductionCement Grinding Station Solution Ball Mill and Vertical MillCement production involves quarrying limestone and clay, grinding and blending the materials, burning them at high temperatures to form clinker, and finely grinding the clinker to produce cement powder The key steps are: 1) Quarrying limestone and clay and grinding them to powder; 2) Blending the powders in precise proportions; 3) Burning the blend at high heat to form Chapter 1 Introduction To Cement Production
.jpg)
Simulation and Optimization of an Integrated Process Flow Sheet
2021年3月9日 In this study the process flow diagram for the cement production was simulated using Aspen HYSYS 88 software to achieve high energy optimization and optimum cement flow rate by varying the flow rate of calcium oxide and silica in the clinker feed Central composite Design (CCD) of Response Surface Methodology was used to design the ten experiments for 2014年6月10日 Evolution of the cement Process • Wet process easiest to control chemistry better for moist raw materials • Wet process high fuel requirements fuel needed to evaporate 30+% slurry water • Dry process kilns less fuel requirements • Preheater/Precalciner further enhance fuel efficiency allow for high production ratesCement manufacturing process PPT Free Download SlideShare2015年8月1日 The results show that approximately 248t, 469t, and 341t of materials are required to produce a ton of the product in raw material preparation, clinker production, and cement grinding stages Analysis of material flow and consumption in cement production process2023年8月21日 Tushar Khandhadia, General Manager – Production, Udaipur Cement Works, discusses the role of grinding in ensuring optimised cement production and a high quality end product How does the grinding process contribute to the production of highquality cement?The quality of cement depends on its reactive properties and particle size grinding helps to reduce Grinding process is a critical stage in cement production