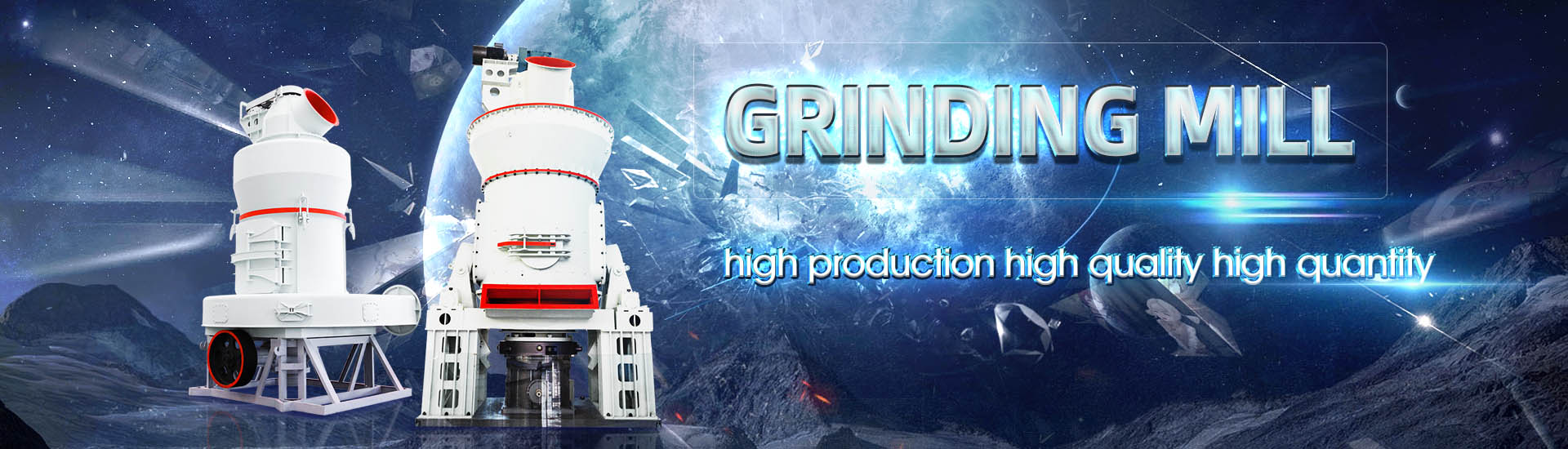
HOME→The process of producing zinc oxide from steel slag The process of producing zinc oxide from steel slag
The process of producing zinc oxide from steel slag The process of producing zinc oxide from steel slag
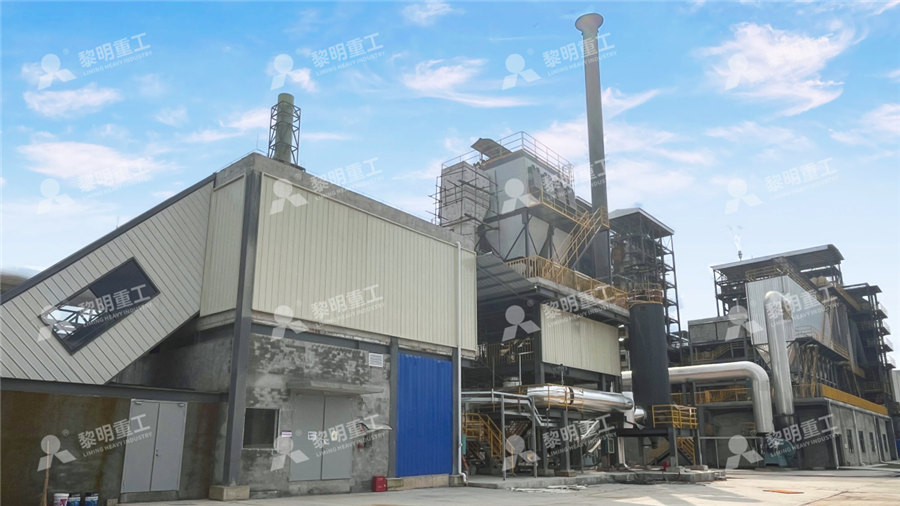
The Extractive Metallurgy of Zinc AusIMM
The world primary zinc smelting industry employs five distinctive processes: Region Distribution of Mines Distribution of Smelters Europe (including Eastern Europe) 10% 27%2014年3月31日 The mechanochemical process, controlled precipitation, solgel method, solvothermal and hydrothermal method, method using emulsion and microemulsion enviroment and other methods of obtaining(PDF) Zinc Oxide—From Synthesis to Application: A 2012年3月15日 Zinc oxide is produced mainly by three distinct processes: directly oxidizing zinc metal, or reduction of an ore to zinc metal followed by controlled reoxidation or, to a far lesser Zinc oxide particles: Synthesis, properties and applicationsSteelmaking slag, or steel slag, is a byproduct from the production of steel during the conversion of hot metal to crude steel in a basic oxygen furnace, or during the melting of scrap in an EAF Steelmaking Slag an overview ScienceDirect Topics
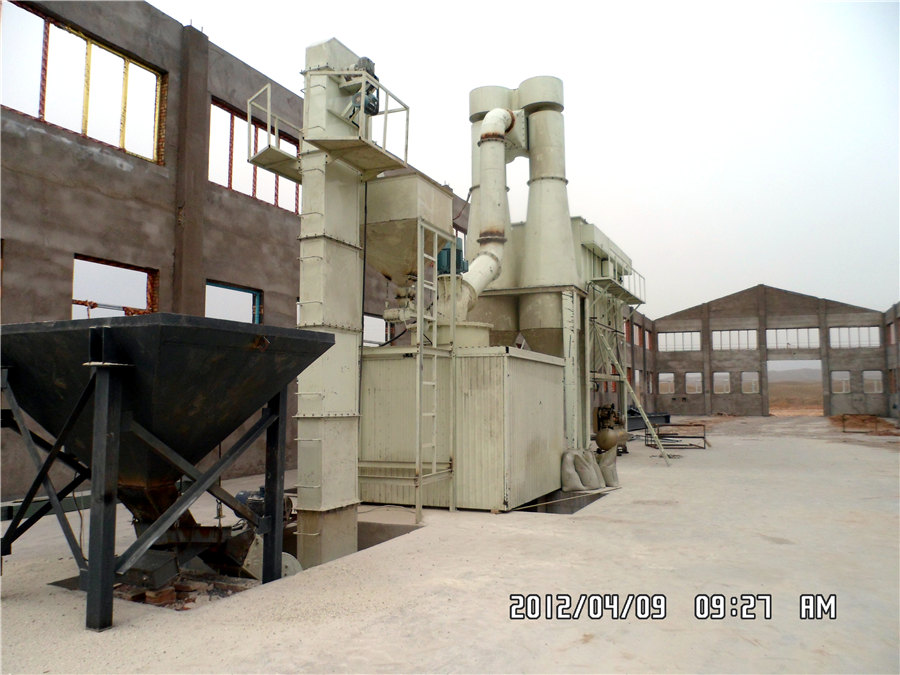
Zinc Oxide—From Synthesis to Application: A Review MDPI
2014年4月9日 Metallurgical processes for obtaining zinc oxide are based on the roasting of zinc ore According to the ISO 9298 standard [68], zinc oxide is classified either as type A, obtained A new process for the preparation of active zinc oxide and synergistic recovery of valuable elements using zinccontaining dust is proposed The process can achieve the maximum Preparation of active zinc oxide from zinccontaining dust and Metallurgical slag and dust (MSD) from lead and zinc smelting, steel dust and galvanized steel scrap are important secondary sources of zinc and other valuable metals This paper Zinc recovery from metallurgical slag and dust by coordination This article reviews the recent progress on the four important topics of BOS slags: 1) slag formation, ie, dissolution of lime in the BOS slag; 2) hightemperature phase transformation Basic Oxygen Steelmaking Slag: Formation, Reaction, and Energy
.jpg)
A Critical Review on Generation, Characteristics, and Utilization of
2020年1月25日 Due to the complex composition of zinc smelting slag and the low content of valuable metals, the economic and efficient recovery of polymetallic elements can be realized Mild steel: Mild steel is iron containing up to about 025% of carbon The presence of the carbon makes the steel stronger and harder than pure iron The higher the percentage of carbon, the harder the steel becomes Mild steel is 233: Metallurgy of Iron and Steel Chemistry 2019年1月1日 This paper explores the various developments for total recycling of slag in steel industry, so that the vision for making “clean green steel with zero waste” can be achieved for survival and Recent trends in slag management utilization in 2021年5月25日 1 Introduction It is widely accepted that alkaliactivated material (AAM) is a potential alternative for ordinary Portland cement (OPC) []These materials are commonly generated by aluminosilicate precursor, Advances in Understanding the Alkali‐Activated
.jpg)
The Extractive Metallurgy of Zinc AusIMM
The Zinc Smelting Industry 3 Process Principles – Electrolytic Zinc Process 6 Process Principles – Carbothermic Reduction 10 Chapter 2 – Historical Background 13 Zinc Production in Early Times 13 Retort Processes 13 The Electrolytic Process 14 Recovery of Zinc From Leach Residues 15 Direct Leaching of Zinc Concentrates 16 Evolutionary Steelmaking slag, or steel slag, is a byproduct from the production of steel during the conversion of hot metal to crude steel in a basic oxygen furnace, or during the melting of scrap in an EAFThe slag is generated as a melt and is a complex solution of silicates and oxides that solidify upon cooling 11 Depending on the specific steel production process, three different types of steel Steelmaking Slag an overview ScienceDirect Topics2023年11月17日 An example of slag chemistries during stainless steel production from Holappa et al (2021) is given in Table 23 where significant quantities of chromium oxide are found in the EAF slag; however, due to the high reactivity of chromium with FeO and the addition of slag reducing agents such as silicon and aluminum in the EAF, there are low levels of FeO and Electric Arc Furnace Steelmaking and Slag Formation, The main challenge of the steel industry for the next decade is the steel production transformation process, starting in Europe The CO 2 intensive blast furnace/basic oxygen furnace (BOF) route will be substituted by a combination of Direct Reduced Iron (DRI), based on natural gas, later on “green” hydrogen, with an Electric Arc Furnace (EAF) or a Submerged Arc Furnace (SAF), The steel production transformation process in Europe: New slag
.jpg)
An overview of utilization of slag and sludge from steel industries
2007年3月1日 Integrated steel plants utilize mostly five materials such as raw materials, air, water, fuel and power to produce steel During the production of steel, 2–4 t of wastes are being generated per tonne of steel producedThe various solid wastes in the form of slags and sludges that are emerged from steel plants are blast furnace slag, blast furnace flue dust and sludge, 2024年6月12日 1 INTRODUCTION Blast furnace slag (BFS) and steel slag (SS), as industrial solid wastes produced in the process of steelmaking, account for 80%–90% of the total smelting slag [] BFS accounts for about 30% of pig iron output, [] while SS accounts for 10%–15% of the crude steel output [] SS comprises various slags, including basic oxygen furnace slag (BOFS) Recycling of iron and steel slag for carbon reduction and low 2023年11月17日 Steelmaking is the process of producing steel from iron ore or steel scrap In 2022, approximately 75 percent of the steel produced in the United States was from the electric arc furnace (EAF) process, in which an electric current is used to produce an arc that melts scrap steel or other ironcontaining materials Slag is the liquid oxide that results from the production Health Risk Considerations for the Use of Unencapsulated Steel Slag2024年3月17日 It helps to remove impurities by combining with them to form slag, which coats the steel with a layer of zinc for corrosion resistance marking the culmination of an intricate process by producing readytouse A Visual Guide: Steel Making Process Chart Cabaro
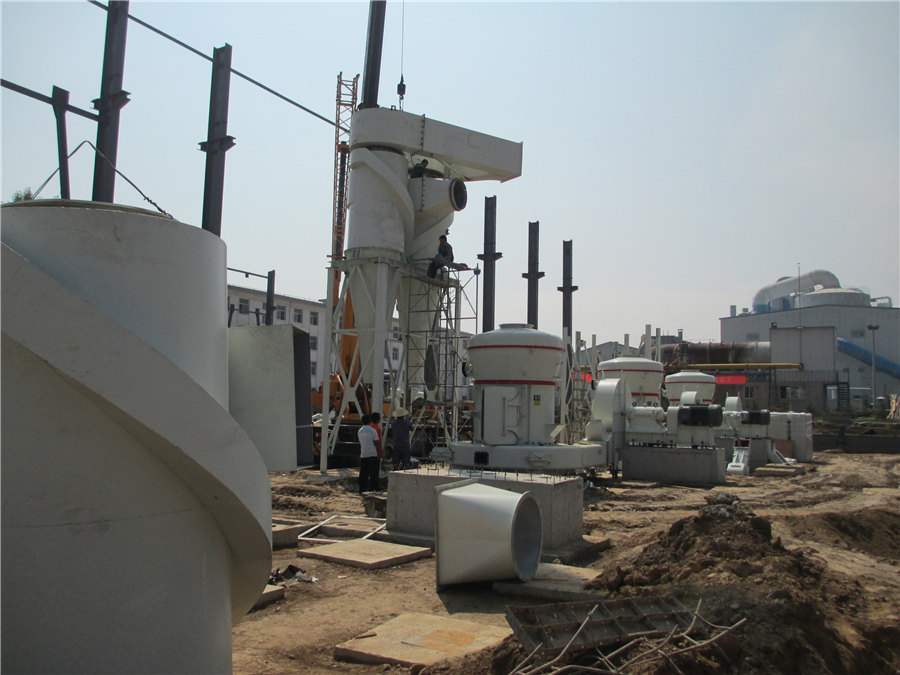
Comprehensive utilization of steel slag: A review ScienceDirect
2023年5月15日 Steel slag is the main solid waste generated in the steelmaking process, accounting for 15 to 20% of crude steel output [1]China's crude steel output in 2021 was 1035 billion tons [2], more than half of the global crude steel output (19505 billion tons) [3], and the steel slag output exceeded 120 million tonsIn contrast, the comprehensive utilization rate of 2009年1月1日 Therefore a method was developed, which allows to apply the reduction process for processing of steelmaking slag into a slagforming material, which can be used for producing refining slag in (PDF) Production of slagforming materials in the 2017年3月5日 Schematic diagram of the integrated steel manufacturing process Rough values of some of the raw material and byproduct streams are presented in parentheses(PDF) Iron and Steel Slags ResearchGate2019年4月5日 All volatile components from the input dust are enriched in the crude zinc oxide product The satisfying dezincification in the RecoDust process provides zinc contents in the final slag product below 05 wt% To recycle the RecoDust slag in the sintering process also a welldefined grain size is neededRecoDust—An Efficient Way of Processing Steel Mill Dusts
.jpg)
Zinc Oxide—From Synthesis to Application: A Review MDPI
2014年4月9日 Zinc oxide can be called a multifunctional material thanks to its unique physical and chemical properties The first part of this paper presents the most important methods of preparation of ZnO divided into metallurgical and chemical methods The mechanochemical process, controlled precipitation, solgel method, solvothermal and hydrothermal method, 2024年1月12日 Steel slag is a byproduct of the steel production process, accounting for approximately 15% of the whole crude steel output [1]The accumulation of untreated steel slag not only occupies a significant amount of land but also leads to the leaching of heavy metal ions (such as vanadium, chromium, arsenic, lead, cadmium), polluting surrounding water sources Review Accelerated carbonation of steel slag: A review of Almost 2957–3846 million tons of zincbearing dust were produced in Chinese iron and steel enterprises annually The recovery of Zn and other metals in zincbearing dust from ironmaking and steelmaking could improve economic efficiency However, zincbearing dust was classified as hazardous waste, and the volatile metals (like Zn, Na, Pb, etc) in zincbearing dust limited the Research status and development of extraction process of zinc 1 Introduction The basic oxygen steelmaking (BOS) process produced over 70% of the global crude steel in 2018, [] generating 100 to 150 kg of slag (“BOS slag”) for every tonne of crude steel produced BOS slag, a product of hot metal element (eg, Si, Mn, Fe, P) oxidation and flux (eg, lime, dolomite) dissolution, plays a critical role in the production of highquality crude steelBasic Oxygen Steelmaking Slag: Formation, Reaction, and Energy
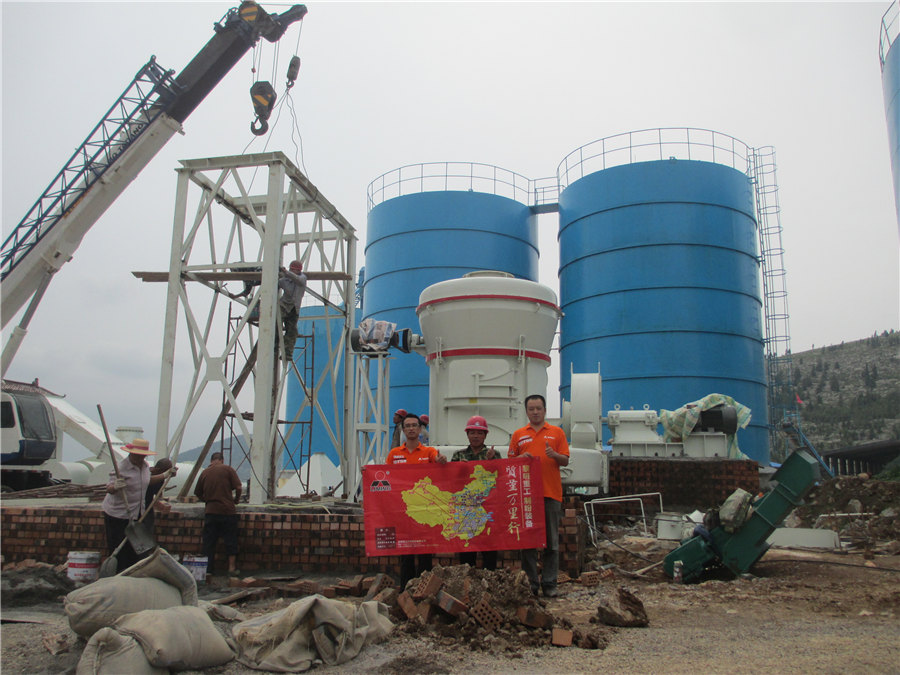
Evaluation of Potential Factors Affecting Steel Slag Carbonation
2023年8月29日 Steel slag is a solid waste product generated during the carbonation stage of steelmaking It has high levels of heavy metals and substantial amounts of free calcium and magnesium oxide, making it unsuitable for use as a cement material Furthermore, the disposal of steel slag in landfills requires many resources and can seriously contaminate the surrounding 2022年1月12日 Imoto T, Harano Y, Nishi Y, Masuda S (1964) The reduction of zinc oxide by hydrogen III The effect of nitrogen on the reduction Bull Chem Soc Jpn 37:441–444 Article CAS Google Scholar Imoto T, Harano Y, Nishi Y (1963) The reduction of zinc oxide by hydrogen J Chem Soc Japan Pure Chem 84:115Metals Production and Metal Oxides Reduction Using Hydrogen: A Granulated steelmaking dust with reducer (coal dust) was the input material The products of the process are zinc oxide, iron alloy and slag, with properties meeting high ecological requirements The technology does not generate solid waste Zinc recovery is HighPerformance Method of Recovery of Metals from EAF Dust 2018年2月5日 Piles of steel slag, a solid waste generated from the iron and steel industry, could be seen due to no utility found for the past century Steel slag has now gained much attention because of its new applications The properties of slag greatly influence its use and thus had got varied applications The chemical composition of steel slag varies as the mineral composition Review on the innovative uses of steel slag for waste minimization
.jpg)
Zinc and Lead Metallurgical Slags as a Potential Source of Metal
2023年10月27日 The process produces two types of slag: shaft furnace slag and refining slag Shaft furnace slag, which is a waste product of the shaft furnace process, due to its physical and chemical properties, especially its high mechanical strength and low solubility in water, is widely used in road construction, for backfilling in the mining industry and for capping waste dumps 2016年4月20日 Steel used for many different applications is more and more often coated with zinc for corrosion protection purposes The growing amount of Electric Arc Furnace Dust (EAFD) generated during the production of steel requires treatment that is able to convert this dust into usable materials The current state of the art for the treatment of these wastes is based on the INDUTEC®/EZINEX® Integrate Process on Secondary Zinc Steel slag is an industrial byproduct of steel production which is obtained during the pyrometallurgical process Technological dissemination on effective utilization of steel slag in vast quantities globally is essential as the generation of steel is escalating year by year and the availability of steel slag is also in millions of tons Though steel slag has been used for various Recent applications of steel slag in construction industry2020年3月5日 of strength than the steel slag; on the other hand, steel slag, due to its content of iron oxide, has shown to be much stronger than granite In addition, lower silica content in steel slag and bottomReuse and Recycling of ByProducts in the Steel Sector: Recent
.jpg)
Basics of slag production Article on the slag industry from Global Slag
2011年10月27日 Slags from the Iron and Steel Industry Background With world steel production now well over a billion tonnes per year, the slag that arises from some of the processes involved is a major resource Traditionally it has been used mainly as an aggregate but for some types there are other applications, such as a raw material for cement or as a 2016年1月21日 As innovative technology developments and synergies with other industries continue to bring the steel industry closer to its goal of zero waste, the upcycling of byproducts such as steel slag remains the best possible solution for now Be sure you never miss any of the exciting steel stories from The Steel Wire by subscribing to our blogSteel Slag: The Incredible, Upcycable Byproduct of Steelmaking Under the conditions in the furnace zinc is a vapour (gas), whereas lead is produced as a liquid by a similar series of reactions The other components of sinter such as silica (SiO 2), lime (CaO), alumina (Al 2 O 3) and iron oxide (Fe 2 O 3 /FeO), form a molten slag of silicates This is tapped from the hearth of the furnace simultaneously with the lead, and then separated in a vessel ZincMild steel: Mild steel is iron containing up to about 025% of carbon The presence of the carbon makes the steel stronger and harder than pure iron The higher the percentage of carbon, the harder the steel becomes Mild steel is 233: Metallurgy of Iron and Steel Chemistry
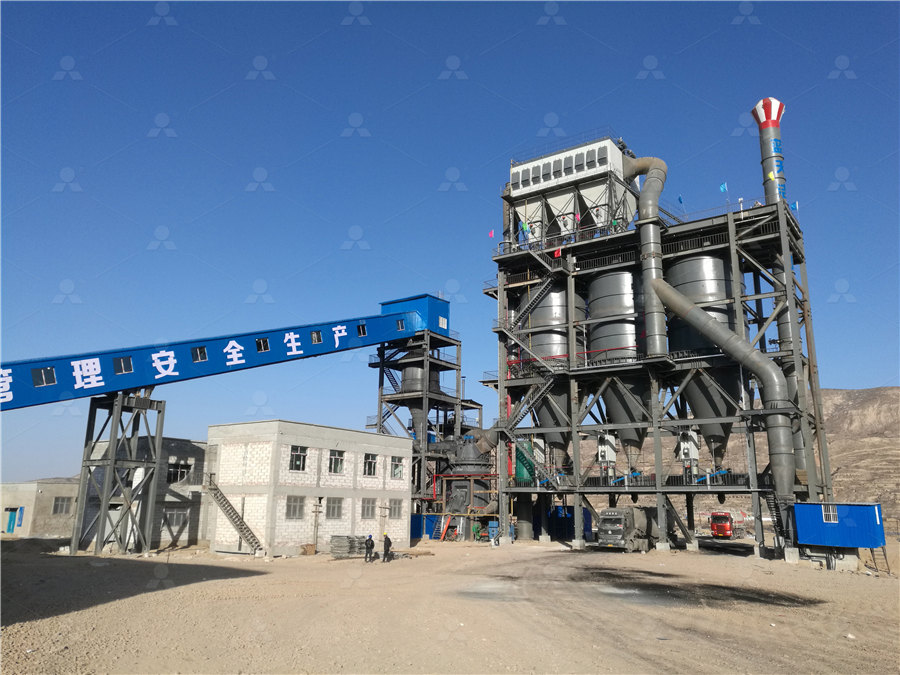
Recent trends in slag management utilization in
2019年1月1日 This paper explores the various developments for total recycling of slag in steel industry, so that the vision for making “clean green steel with zero waste” can be achieved for survival and 2021年5月25日 1 Introduction It is widely accepted that alkaliactivated material (AAM) is a potential alternative for ordinary Portland cement (OPC) []These materials are commonly generated by aluminosilicate precursor, Advances in Understanding the Alkali‐Activated The Zinc Smelting Industry 3 Process Principles – Electrolytic Zinc Process 6 Process Principles – Carbothermic Reduction 10 Chapter 2 – Historical Background 13 Zinc Production in Early Times 13 Retort Processes 13 The Electrolytic Process 14 Recovery of Zinc From Leach Residues 15 Direct Leaching of Zinc Concentrates 16 Evolutionary The Extractive Metallurgy of Zinc AusIMMSteelmaking slag, or steel slag, is a byproduct from the production of steel during the conversion of hot metal to crude steel in a basic oxygen furnace, or during the melting of scrap in an EAFThe slag is generated as a melt and is a complex solution of silicates and oxides that solidify upon cooling 11 Depending on the specific steel production process, three different types of steel Steelmaking Slag an overview ScienceDirect Topics
.jpg)
Electric Arc Furnace Steelmaking and Slag Formation,
2023年11月17日 An example of slag chemistries during stainless steel production from Holappa et al (2021) is given in Table 23 where significant quantities of chromium oxide are found in the EAF slag; however, due to the high reactivity of chromium with FeO and the addition of slag reducing agents such as silicon and aluminum in the EAF, there are low levels of FeO and The main challenge of the steel industry for the next decade is the steel production transformation process, starting in Europe The CO 2 intensive blast furnace/basic oxygen furnace (BOF) route will be substituted by a combination of Direct Reduced Iron (DRI), based on natural gas, later on “green” hydrogen, with an Electric Arc Furnace (EAF) or a Submerged Arc Furnace (SAF), The steel production transformation process in Europe: New slag 2007年3月1日 Integrated steel plants utilize mostly five materials such as raw materials, air, water, fuel and power to produce steel During the production of steel, 2–4 t of wastes are being generated per tonne of steel producedThe various solid wastes in the form of slags and sludges that are emerged from steel plants are blast furnace slag, blast furnace flue dust and sludge, An overview of utilization of slag and sludge from steel industries2024年6月12日 1 INTRODUCTION Blast furnace slag (BFS) and steel slag (SS), as industrial solid wastes produced in the process of steelmaking, account for 80%–90% of the total smelting slag [] BFS accounts for about 30% of pig iron output, [] while SS accounts for 10%–15% of the crude steel output [] SS comprises various slags, including basic oxygen furnace slag (BOFS) Recycling of iron and steel slag for carbon reduction and low
.jpg)
Health Risk Considerations for the Use of Unencapsulated Steel Slag
2023年11月17日 Steelmaking is the process of producing steel from iron ore or steel scrap In 2022, approximately 75 percent of the steel produced in the United States was from the electric arc furnace (EAF) process, in which an electric current is used to produce an arc that melts scrap steel or other ironcontaining materials Slag is the liquid oxide that results from the production