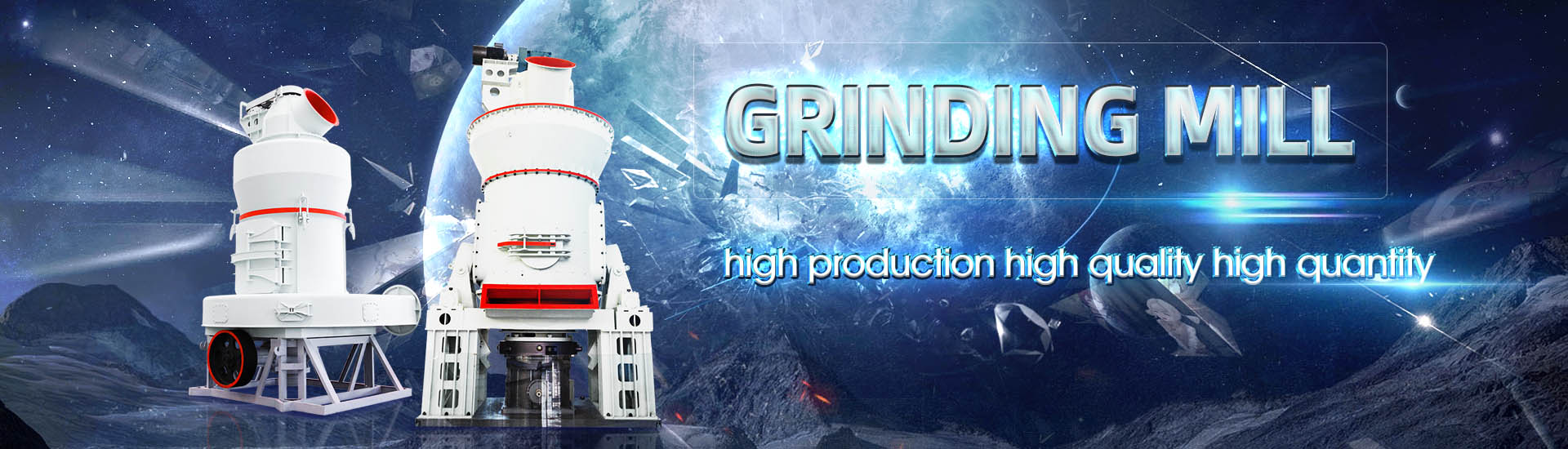
Process flow of grinding water slag
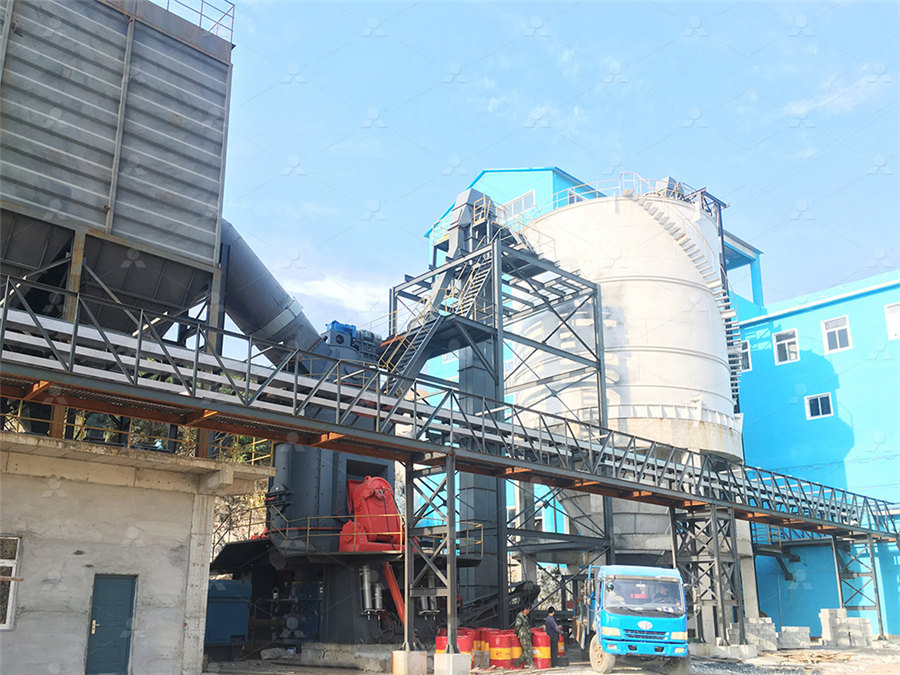
A new technological approach to the granulation of slag melts of
2021年11月3日 It is shown that the main advantage of the proposed HVG process is the provision of forced highspeed vortex convection of water, with the effect of vertical suction, crushing, and degassing of the threephase (water–slag granules–water vapor) heterogeneous Grinding of cement clinker and granulated blast furnace slag in roller grinding mills (vertical airswept grinding mills) is a technology introduced by Loesche The first use of a Loesche mill, 2 µm 5 µm LoescheSteelmaking slag is subjected to the following four process es: ① solidify and cooling of the hot molten slag, ② crushing and magnetic separation treatment of the slag to recover the metal iron,Processing and Reusing Technologies for Steelmaking Slag2019年12月9日 The granulation processes employ mechanical impact or highpressure fluids (eg air or water) to break up the slag into small granules of typically 1–5 mm There are Granulation and Heat Recovery from Metallurgical Slags
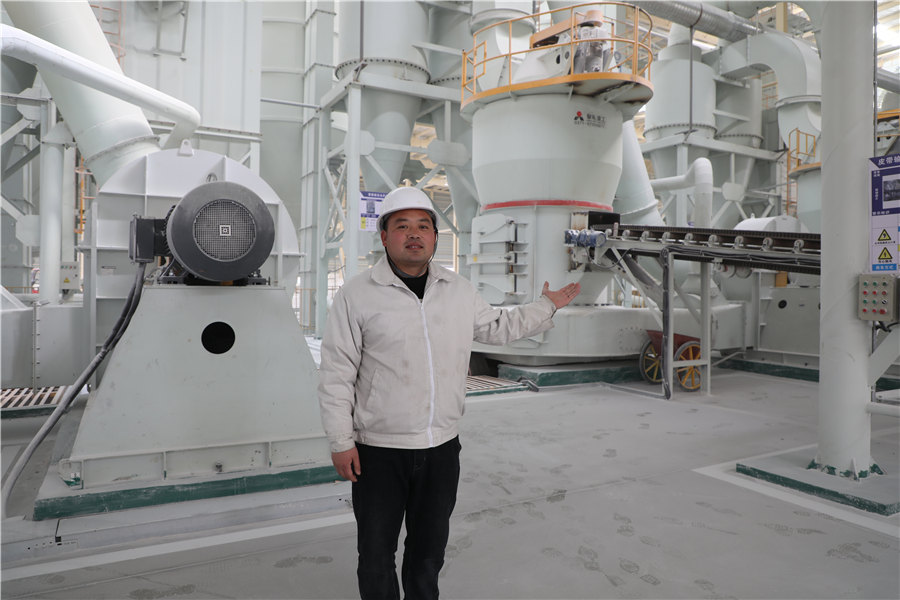
Detailed performance analysis of the wet extractive grinding
2021年9月1日 In this paper, the wet extractive grinding method for efficient recovery of calcium from steelmaking slags was studied This work supports the Sustainable Development Goal of 2020年5月1日 Experimental study on the calcium extraction from steel slag by combining wet grinding and extraction It is found that with the new extractive grinding method 50–60 % yield Wet extractive grinding process for efficient calcium recovery from 2023年7月21日 The water quenching granulation process, also known as the wet treatment process, is a process that uses a highpressure water stream to quickly cool the blast furnace Comprehensive utilisation of blast furnace slag Taylor Francis Process and Equipment Design for the Dry Slag Granulation Technology Abstract: The granulation of blast furnace (BF) slag with water quenching has many disadvantages, such as Process and Equipment Design for the Dry Slag Granulation
.jpg)
Current Development of Slag Valorisation in China
2014年2月19日 In addition to the slag granulation process with pollution control and continuously dewatering (INBA™ process), several modified blast furnace (BF) slag 2016年10月28日 The grinding efficiency of steel slag was obviously increased and the particle characteristics were improved after using grinding aids (GA), especially the particle proportions of 332 Mm were (PDF) Comparison of Grinding Characteristics of 2023年5月15日 Steel slag is the main solid waste generated in the steelmaking process, accounting for 15 to 20% of crude steel output [1]China's crude steel output in 2021 was 1035 billion tons [2], more than half of the global crude steel output (19505 billion tons) [3], and the steel slag output exceeded 120 million tonsIn contrast, the comprehensive utilization rate of Comprehensive utilization of steel slag: A review ScienceDirect2022年2月26日 Blast furnace slag can be processed into the following materials by various processes In China, blast furnace slag is usually processed into water slag, slag gravel, expanded slag and slag beadsWater slag is the process of What is Blast Furnace Slag and How to Process It?
.jpg)
A Review on Environmental Concerns and Technological
2023年11月20日 Mineral process wastes, such as metallurgical slags nowadays, are of significant metals and materials resources in the circular economy The usability of ironmaking slag is well established; however, steel slag still needs to be utilized due to various physicochemical constraints In this context, we have reviewed the global steel slag 2022年2月2日 Yang and Yu used a multistage grinding, subsequent roasting, and flotation method to recover iron from copper slag The process flow chart is shown in Fig 4 When the copper slag grinding fineness was 0074 mm, the roasting temperature was 1000 °C, the roasting time was 1 h, and the final iron ore concentrate was obtainedA Review of Comprehensive Utilization of Copper Slag of China2017年2月8日 Based on the mineralogical analyses of slag, the tested copper smelting slag was composed of fine particles with complex association and dissemination, in which bornite was the main copperbearing mineral Under the condition of the grinding fineness of −0074 mm and the proportion of 80%, flotation exhibited highest efficiencyThe Recovery of Copper from Smelting Slag by Flotation Process2020年11月19日 As the titanium industry rapidly develops, lowgrade ilmenite resources are drawing global attention The direct use of lowgrade ilmenite can result in low production efficiency and heavy pollution In addition, the production of hightitanium slag via electric furnace melting consumes significant energy and possesses low production efficiency Therefore, a HighTitanium Slag Preparation Process by Carbothermic
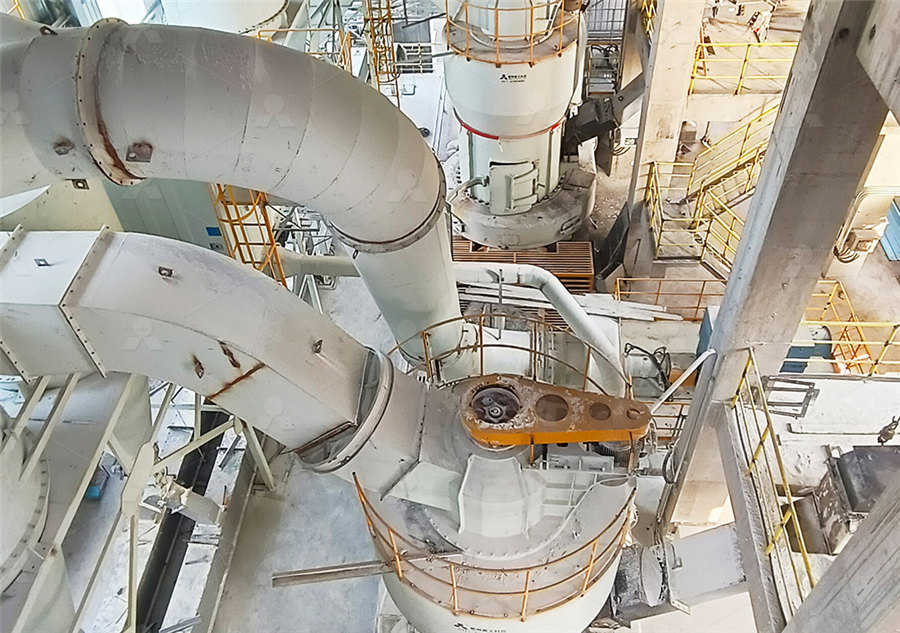
Multiscale analysis of fine slag from pulverized coal gasification in
2024年2月3日 Fine slag (FS) is an unavoidable byproduct of coal gasification FS, which is a simple heap of solid waste left in the open air, easily causes environmental pollution and has a low resource utilization rate, thereby restricting the development of energysaving coal gasification technologies The multiscale analysis of FS performed in this study indicates typical grain size 2022年6月24日 PDF Grinding is a manufacturing process which significantly contributes in producing high precision and durable components required in numerous A heavy stream of water was applied to the(PDF) A comprehensive review on the grinding process: 2023年2月15日 Slag bricks Slag brick production process Slag brick is made by mixing, watering, grinding and pressing slag and limestone In the production process of slag brick, the particle size of the slag is generally smaller than 8 mm, and the steam temperature injected into the kiln is about 80 ℃ to 100 ℃, the maintaining time is about 12 hoursHow to Process Slags (with detailed process)? Fote Machinery2020年3月29日 As mentioned earlier, granulated and aircooled methods are the principal methods for slag cooling The process of production of slag by these two methods are shown in Fig 2GBF slag is a noncrystalline granular material that varies from the source to source depending on the quality of the raw material smelted as well as the method of productionUtilisation perspective on water quenched and aircooled blast
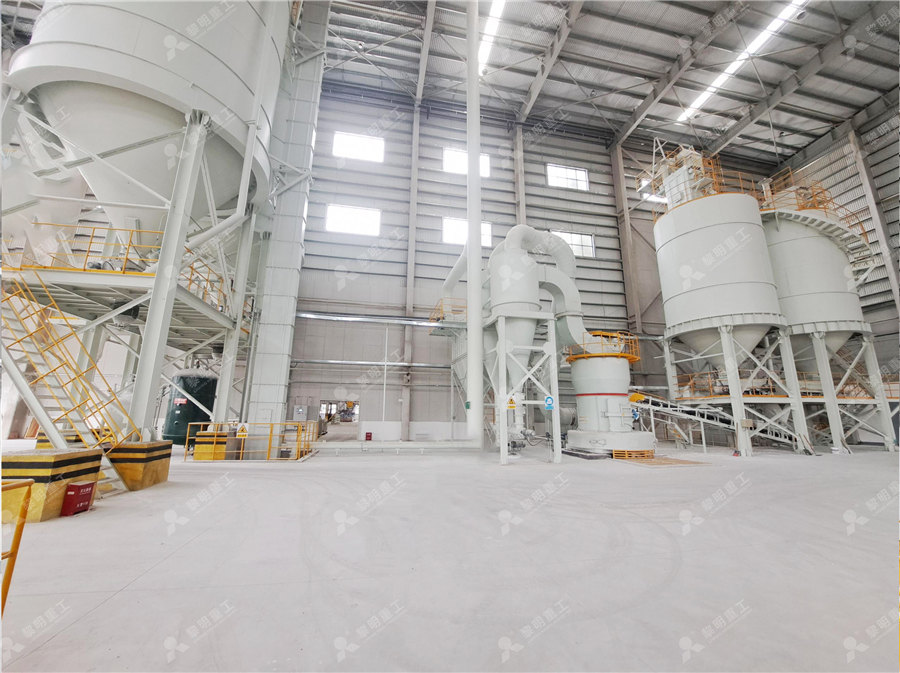
Slag Atomising Technology (SAT): Strategic management of
2007年5月1日 Slag Atomising Technology (SAT) Slag Atomising Technology is a process that converts molten slag (13001350ºC) into small spherical balls with a diameter range of 01 to 45mm The process consists of a high speed air blowing system with catalyst and water exposed to the stream of falling molten slag out of a tundish into the yardvertical roller grinding mills for grinding: • Coal • Cement raw material • Clinker / granulated slag • Industrial minerals, and • Ores The core elements of these plants are the Loesche vertical mills for drygrinding the abovementioned grinding stock Loesche has PROCESS OPTIMISATION FOR LOESCHE GRINDING PLANTS2016年10月28日 The converter steel slag cannot be widely used in building materials for its poor grindability In this paper, the grinding characteristics of untreated and pretreated (ie, magnetic separation) steel slag were compared Additionally, the grinding property of pretreated steel slag was also studied after adding grinding aids The results show that the residues (ie, oversize Comparison of Grinding Characteristics of Converter Steel Slag Process flow diagram (wet process): Wet process: The dryprocess steel slag production process does not need to consume precious water resources After the steel slag is crushed, rod milled, and magnetically separated, the slag steel can be selfgrinding to obtain grade A and B scrap steel The iron content of the slag powder can reach more Steel slag recycling crushing and grinding production line
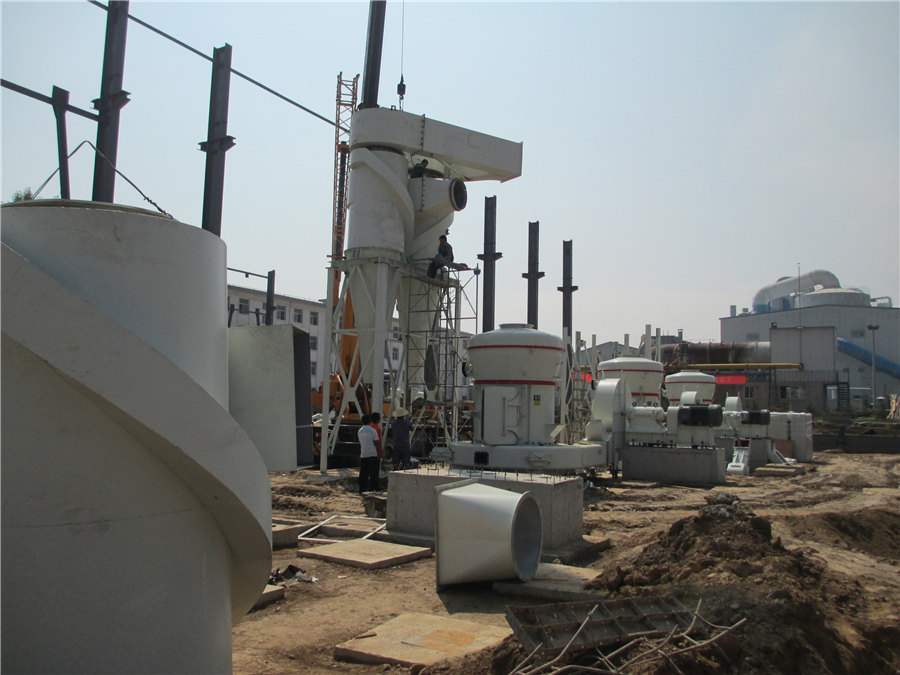
Process Concept for the Dry Recovery of Thermal Energy of Liquid
2021年6月24日 Industrialscale applications incorporating the recycling of those byproducts are common since many decades and include examples like (1) the grinding of waterquenched blast furnace slag (GGBFS) to receive hydraulic properties for their use in cement, (2) using stabilized slags as aggregates in roads and civil installations, (3) using freelime and phosphorous The main challenge of the steel industry for the next decade is the steel production transformation process, starting in Europe The CO 2 intensive blast furnace/basic oxygen furnace (BOF) route will be substituted by a combination of Direct Reduced Iron (DRI), based on natural gas, later on “green” hydrogen, with an Electric Arc Furnace (EAF) or a Submerged Arc Furnace (SAF), The steel production transformation process in Europe: New slag 2023年1月1日 Coal gasification is one of the core technologies for the clean and efficient utilization of coal It is also the basis for process industries such as synthetic coal–based chemicals, synthetic liquid fuels, and integrated coal gasification combined cycle power generation systems (IGCCs) [3]In entrained flow gasifiers, coal is generally gasified at high Recent advances and conceptualizations in process intensification The open circuit grinding process is the earliest slag powder grinding technology It has the advantages of simple process, low technical requirements for operators, and low investment cost The unit power consumption of this system is about 100kWh/t per grinding slag with a specific surface area of 450m 2 /kgGGBS Production Line Slag Mill for Slag Powder Grinding AGICO
.jpg)
Extraction and separation of copper and iron from copper smelting slag
2022年9月25日 The factors affecting the flotation index of copper minerals include slag cooling process, slag properties, flotation process conditions, etc (Stanojlović and Sokolović, 2014; Roy et al, 2015; Linsong et al, 2022) The slag cooling mode is an important factor including slow cooling and water quenched2015年7月30日 Lots of iron molten slag from blast furnace can be produced during iron making process It is generally cooled by water quenching method which causes many problems, such as water consumption Modeling on Dry Centrifugal Granulation Process of2023年8月22日 Grinding is usually used to increase the specific surface area of steel slag to improve its activity However, due to the large amount of hardtogrind minerals in steel slag, a large amount of energy is wasted in the grinding process Therefore, the current investigation aims to remove the hardtogrind minerals in steel slag as much as possible to explore the The Effect of Removing HardtoGrind Minerals from Steel Slag on 2012年1月1日 Basic procedure of ilmenite smelting and rational Ti slag grade in pyrometallurgical process have been summarized and analyzed The rational Ti slag grade is related to reduction degree, FeO A literature review of titanium slag metallurgical
.jpg)
Copper recovery from copper slags through flotation enhanced by
2022年6月1日 On the one hand, the grinding process of fine particles may require more energy On the other hand, the fine particles have a negative effect on flotation [48] To explore the optimal particle size of copper slags, flotation experiments were conducted on copper slags with different grinding time The flotation flow chart is shown in Fig S12019年11月30日 In the wet process, water is added at this point to obtain a blended mixture of very finely ground raw materials and water, called slurry The slurry is stored in tanks under constant agitation and fed into huge firebricklined rotary kilnsManufacture Of Portland Cement Process Flow chart civil 2014年10月1日 To achieve a stable slagtapping process in entrainedflow coal gasifiers, the acceptable viscosity of coal ash slag is within 5–25 Pas in the temperature range 1200–1500 °C and the tapping Slag properties of blending coal in an industrial OMB coal water 2019年9月10日 With prolonging of carbide slag grinding time, the slump flow increased from 190 mm to 210 mm, whether using mix or divide grinding process, slurry slump flow gradually decreased with the extension of grinding time which increased the adsorption water on particles surface and relatively reduced free water for liquidityThe slurry and physicalmechanical performance of autoclaved aerated
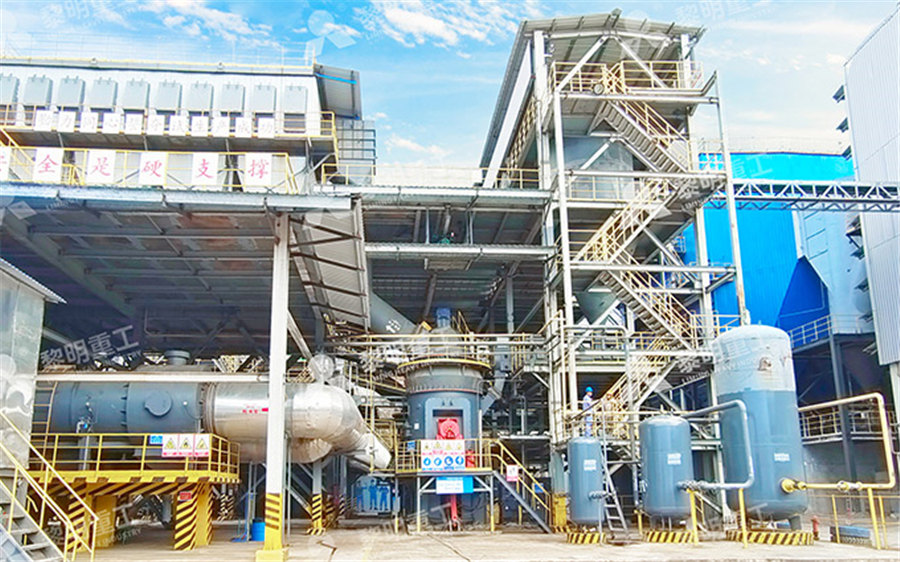
Steel slag in China: Treatment, recycling, and management
2018年8月1日 Slag aging also is used to stabilize freeCaO and freeMgO into calcium or magnesia hydroxide (Nishinohara et al, 2013) This process involves spraying steel slag with water steam and then covering it with tent sheets in a yard The duration of the entire process takes about six days2016年1月1日 The water used in this process is recycled and cooled to less than 50 C, typically by using cooling towers [68] One of the major drawbacks of this technique is the difficulty of achieving heat A Review of Granulation Process for Blast Furnace Slag2012年3月1日 This article describes the results when grinding cement and granulated blastfurnace slag and discusses t h em with regard to factors that affect the engineering process When using grinding aids Operating experience with a vertical roller mill for grinding 2016年10月28日 The grinding efficiency of steel slag was obviously increased and the particle characteristics were improved after using grinding aids (GA), especially the particle proportions of 332 Mm were (PDF) Comparison of Grinding Characteristics of
.jpg)
Comprehensive utilization of steel slag: A review ScienceDirect
2023年5月15日 Steel slag is the main solid waste generated in the steelmaking process, accounting for 15 to 20% of crude steel output [1]China's crude steel output in 2021 was 1035 billion tons [2], more than half of the global crude steel output (19505 billion tons) [3], and the steel slag output exceeded 120 million tonsIn contrast, the comprehensive utilization rate of 2022年2月26日 Blast furnace slag can be processed into the following materials by various processes In China, blast furnace slag is usually processed into water slag, slag gravel, expanded slag and slag beadsWater slag is the process of What is Blast Furnace Slag and How to Process It?2023年11月20日 Mineral process wastes, such as metallurgical slags nowadays, are of significant metals and materials resources in the circular economy The usability of ironmaking slag is well established; however, steel slag still needs to be utilized due to various physicochemical constraints In this context, we have reviewed the global steel slag A Review on Environmental Concerns and Technological 2022年2月2日 Yang and Yu used a multistage grinding, subsequent roasting, and flotation method to recover iron from copper slag The process flow chart is shown in Fig 4 When the copper slag grinding fineness was 0074 mm, the roasting temperature was 1000 °C, the roasting time was 1 h, and the final iron ore concentrate was obtainedA Review of Comprehensive Utilization of Copper Slag of China
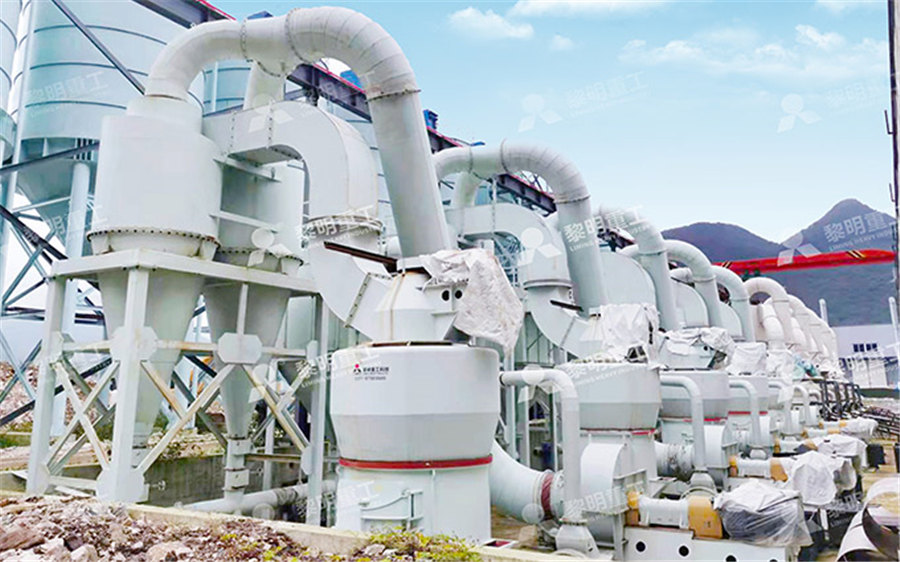
The Recovery of Copper from Smelting Slag by Flotation Process
2017年2月8日 Based on the mineralogical analyses of slag, the tested copper smelting slag was composed of fine particles with complex association and dissemination, in which bornite was the main copperbearing mineral Under the condition of the grinding fineness of −0074 mm and the proportion of 80%, flotation exhibited highest efficiency2020年11月19日 As the titanium industry rapidly develops, lowgrade ilmenite resources are drawing global attention The direct use of lowgrade ilmenite can result in low production efficiency and heavy pollution In addition, the production of hightitanium slag via electric furnace melting consumes significant energy and possesses low production efficiency Therefore, a HighTitanium Slag Preparation Process by Carbothermic2024年2月3日 Fine slag (FS) is an unavoidable byproduct of coal gasification FS, which is a simple heap of solid waste left in the open air, easily causes environmental pollution and has a low resource utilization rate, thereby restricting the development of energysaving coal gasification technologies The multiscale analysis of FS performed in this study indicates typical grain size Multiscale analysis of fine slag from pulverized coal gasification in 2022年6月24日 PDF Grinding is a manufacturing process which significantly contributes in producing high precision and durable components required in numerous A heavy stream of water was applied to the(PDF) A comprehensive review on the grinding process:
.jpg)
How to Process Slags (with detailed process)? Fote Machinery
2023年2月15日 Slag bricks Slag brick production process Slag brick is made by mixing, watering, grinding and pressing slag and limestone In the production process of slag brick, the particle size of the slag is generally smaller than 8 mm, and the steam temperature injected into the kiln is about 80 ℃ to 100 ℃, the maintaining time is about 12 hours