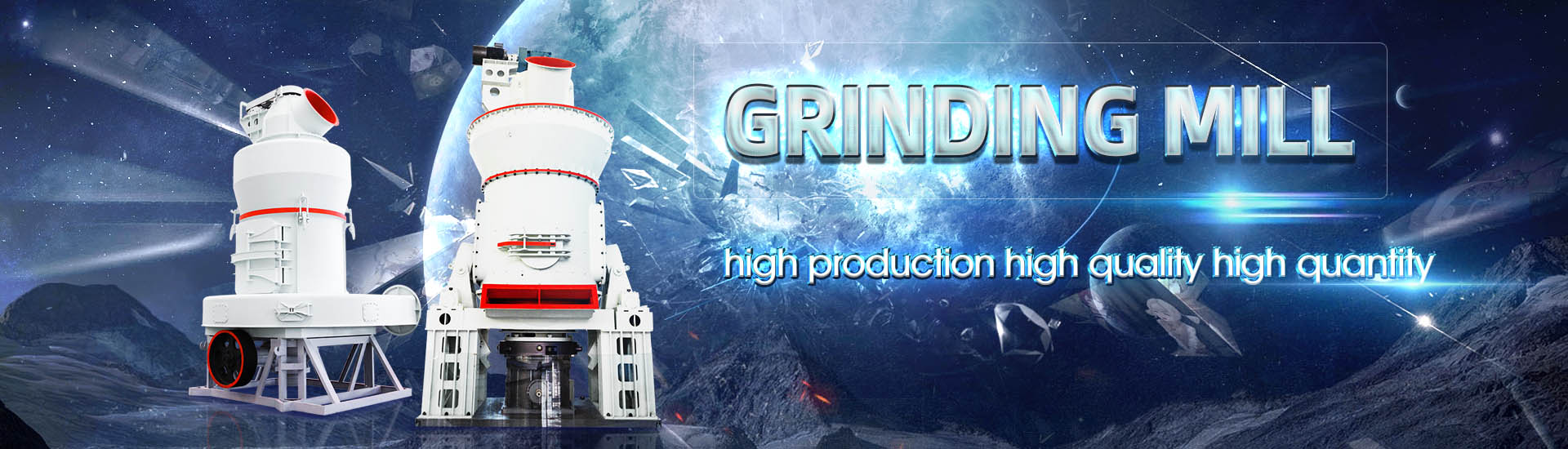
How to convert the diameter unit of mill grinding fineness
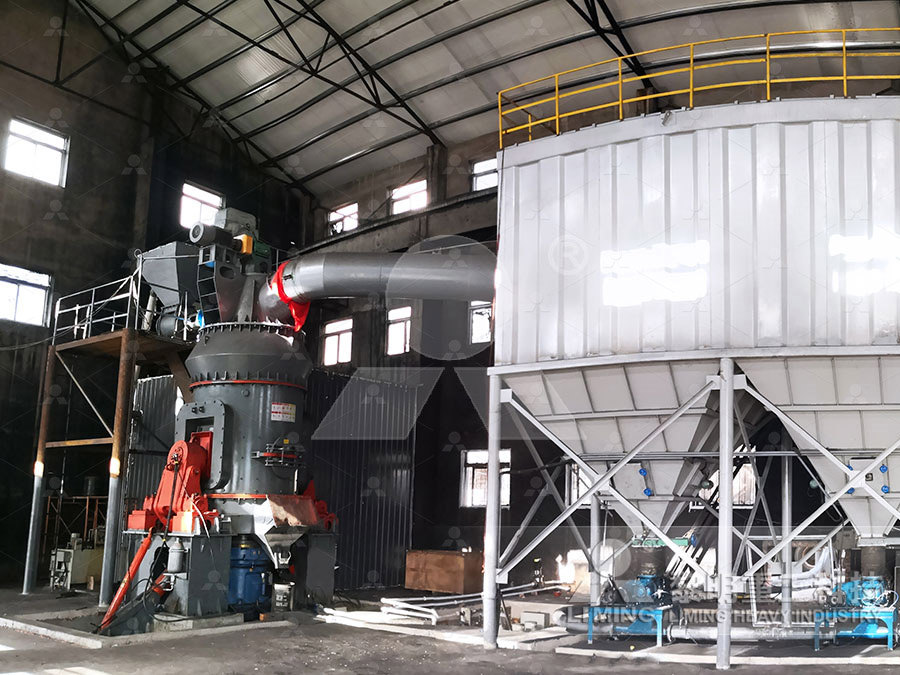
Powder fineness to d = 10 µm PRINCIPLE OF OPERATION AND
Fineness range between d97 = 10 µm and approx 200 µm Mill drive with frequency converter to permit optimum adaptation of the mill to a wide range of particle sizes Mill control by means of the drive power or differential pressure moni toring Option: hardfaced plates as wear online live calculators for grinding calculations, Ball mill, tube mill, critical speed, Degree of filling balls, Arm of gravity, mill net and gross powerball mill calculations, grinding media filling degree, ball size, mill sieve oversize of about 70% in the mill, a very coarse grinding fineness even in closed circuit process, eg for cement grinding Hardgrove grindabilities can be converted with satisfactory GRINDABILITY OF MATERIALS2019年3月1日 The Fineness of Grind Gage is used to indicate the fineness of grind or the presence of coarse particles or agglomerates in a dispersion It does not determine particle Fineness of Grind Gages Polymer Innovation Blog
.jpg)
Practicable Methods of Fine Grinding SpringerLink
Up to date technology often requires grinding fineness getting into the range of aggregation or even agglomeration (for definitions, see Chapter 4) As has been dealt with in the preceding sample preparation The "Art of Milling" describes the process of turning a laboratory sample into a representative part sample with homogeneous analytical fineness For this task RETSCH The Art of Milling Metrohm2017年3月4日 A stamp mill (or stamp battery or stamping mill) is a type of mill machine that cru shes material by pounding rather than grinding, either for furthe r processing or for extraction of metallic oresSIZE REDUCTION BY GRINDING METHODSMaterial abrasivity The [%] of slag or pouzzolana content on the fresh mill feed for cement grinding The [%] of free silica at mill feed for raw material grinding Moisture content of the mill fresh feed Above or below 2 [%H2O] content The Everything you need to know about clinker/cement
.jpg)
(PDF) Optimization and performance of grinding
2020年1月16日 The combination of energy intensive and poor performance of comminution process implies that there is a great opportunity for significant energy and economic savings by the improvement of this 2024年6月14日 The grinding process plays a crucial role in industry, allowing for the reduction of particle sizes of raw materials and substances to the required fineness—either as a finished product or for further technological processes The high demand for micro and nanopowders or suspensions is associated with the high energy consumption of the milling process Therefore, The Influence of the Grinding Media Diameter on Grindingdetermining degree the efficiency of the mill work (grinding fineness, wear of grinding media, throughput of the mill, energy specificconsumption, noise produced by the mill, etc) 2 where D is the inside diameter of the drum, and n represents mill speed measured in rpm ncr = D 30 ⋅ 2 critical speed of the drum, rpmTHE GRINDING CHARGE OF ROTARY MILLSFineness Test of Cement AASHTO T 98 and ASTM C 115: Fineness of Portland Cement by the Turbidimeter; AASHTO T 128 and ASTM C 184: Fineness of Hydraulic Cement by the 150mm (No100) and 75mm (No 200) Sieves; AASHTO T 153 and ASTM C 204: Fineness of Hydraulic Cement by AirPermeability Apparatus o AASHTO T 192 and; ASTM C 430: Fineness of Fineness of Cement Civil Engineering
.jpg)
Brief Analysis of the Influence of Operational Factors on Grinding
2024年9月23日 3 The influence of Feeding Speed on the Mill Feeding speed refers to the amount of ore passing through the mill per unit of time When the mill feeds less, not only is the productivity low, but phenomena such as empty grinding can occur, leading to serious equipment wear and overcrushing of the ore2014年6月18日 Fineness of cement increases the rate of evolution of heat Finer cement offers a great surface area for hydration and hence faster the development of strength Increase in fineness of cement also increases the drying shrinkage of concrete and hence creates cracks in structures Excessive fineness requirement increases cost of grindingFINENESS OF CEMENT BY BLAINES AIR PERMEABILITY METHOD (IS 2013年8月3日 In Grinding, selecting (calculate) the correct or optimum ball size that allows for the best and optimum/ideal or target grind size to be achieved by your ball mill is an important thing for a Mineral Processing Engineer AKA Metallurgist to do Often, the ball used in ball mills is oversize “just in case” Well, this safety factor can cost you much in recovery and/or mill liner Calculate and Select Ball Mill Ball Size for Optimum GrindingIn the entire production line, the main thing is to convert materials into finished products After the material is crushed to the required particle size, the material is sent to the storage hopper by the elevator, and then sent to the main grinding chamber by the feeder evenly and orderlyHow to calculate the output of the high pressure roller grinding mill
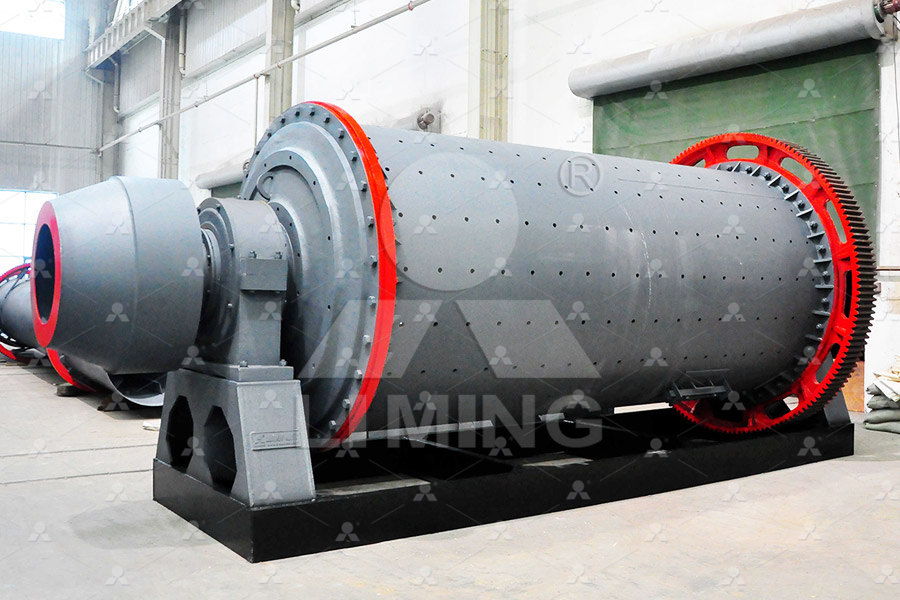
How to adjust the product fineness of ultra fine mill
In addition, you can use the roller and grinding ring gap to adjust ultra fine mill grinding is produced by rolling the roller and grinding ring each other to achieve, the gap between them is that the material can be milled to a fine degree, so we control the size of the roller to adjust it and the distance between the grinding ring to change the fineness of the material2019年1月30日 Mill power models have been used in a variety of ways in industrial practice since power directly equates to throughput and fineness of ground product We first start with HoggFuerstenau Power Model and show how this model successfully predicted the power draw of many grinding mills in several mining operations Then, we show how this model was on the The Evolution of Grinding Mill Power Models Mining, Quick, free, online unit converter that converts common units of measurement, along with 77 other converters covering an assortment of units The site also includes a predictive tool that suggests possible conversions based on input, allowing for easier navigation while learning more about various unit systemsUnit Converter2013年1月1日 PDF The grinding behavior of corn and corncobs was investigated at moisture content levels of 1039%, 1602%, and 1964% (wet basis) for shelled corn Find, read and cite all the research (PDF) The effect of moisture content on the grinding performance
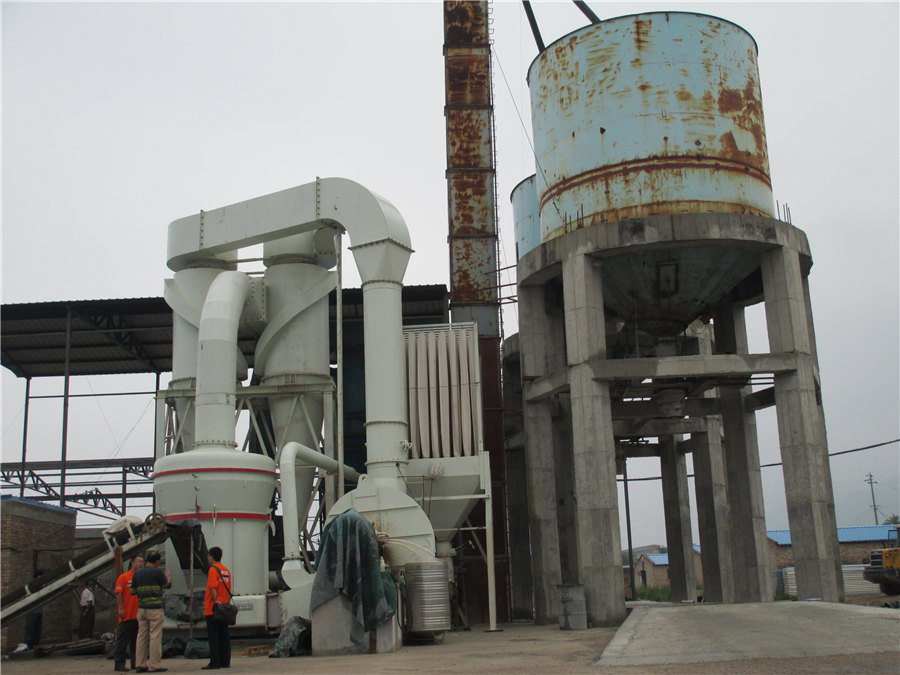
Ball Mill Success: A StepbyStep Guide to Choosing the Right Grinding
2024年8月8日 Unlock the secrets to ball mill efficiency with our comprehensive guide on choosing the right grinding media Learn how material composition, size, shape, larger media offer faster size reduction but may not achieve the desired fineness The 2018年10月25日 The effect of the shape of grinding media on the breakage parameters of colemanite has been investigated in kinetic studies In this present research, three different monosize fractions, ie Fineness of the Grind produced by Mixtures of Grinding media 2016年7月8日 The Work Index values listed in Table I and II apply directly to a wet grinding overflow type rod mill 75 feet in diameter in open circuit; and to a wet grinding overflow type ball mill 75 feet in diameter in closed circuit with a rake classifier at 250% circulating load, and with 80% or more of the feed passing 4 meshEquipment Sizing: Crusher or Grinding Mill 911MetallurgistRPM is programmed to follow mill coal flow to obtain a desired fineness vs mill load rela tionship; manual override with manual control of classifier speed from the control room is also provided; instrumentation for monitoring drive assembly oil bath temperature and oilPulverizer Fineness and Capacity Enhancements at Danskammer
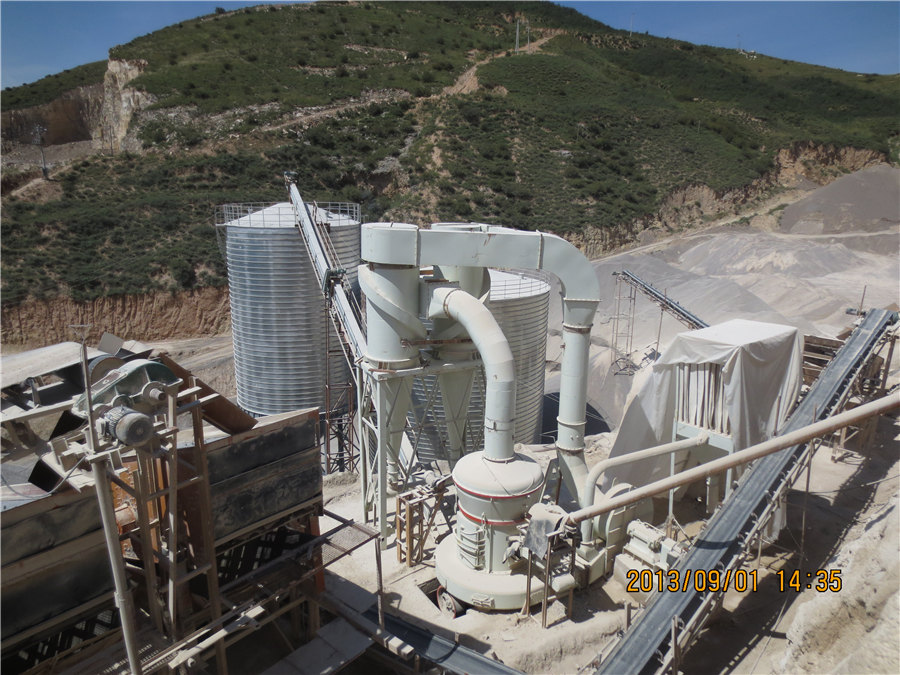
Ten Ways to Improve the Grinding Efficiency of Your Ball Mill
2019年4月22日 2 More crushing and less grinding to reduce the feed size into mill The larger feed size, the more work that the ball mill needs to do on the ore2016年6月1日 The Rod Mill is probably the most flexible type of grinding unit available The fineness of grind and tonnage may be easily varied by altering the mill speed, rod charge or dilution Under dry grinding conditions the rod mill product may be altered by varying tonnage, size of feed, size and quantity of grinding media and the use of peripheral discharge portsRod Mills: Efficient Grinding Solutions for Miningwhere T is the grinding time to reach a certain median particle size, K is a constant that depends upon the material being processed, the type of media and the particular mill being used, D is the diameter of the media, and N is the Solids Choose the Right Grinding Mill Chemical are related to moderate grinding fineness, eg 10% residue on 009 mm sieve or 3000 cm2/g Blaine surface Industrial practice therefore simplifies further the problem For a known grinding process (eg cement grinding in a ball mill to a grinding fineness of 3000 cm2/g Blaine), the grindability of a material is characterized in k'Yh/t,GRINDABILITY OF MATERIALS

COAL GRINDING IMPS: more than meets the eye Gebr Pfeiffer
The MPS coal grinding mill with a high drying capacity is very suitable for grinding lignites with feed moistures of as much as 45 per cent Depending on this high feed moisture, the mill rating is determined by drying whereas for anthracite, hard coal and petcoke the rating of the mill is determined by grinding The great2016年11月12日 Although the derivation of these curves is completely theoretical there is some qualitative evidence in support of their validity Thus for example, it is clear from Fig 82 that if a material is being ground by balls of approximately equal hardness (H= 1), then the ball wear may be reduced either by increasing or by decreasing the value of HGrinding Media Lining Media Liner Wear Rate Modelling2020年4月7日 However, the sieve test gives no information on the size of grains smaller than 45 μm (No 325 ASTM) sieve, and it is the finer particles that play the greatest part in the early hydration; For this reason, modern standards prescribe a test for fineness by determination of the specific surface of cement expressed as the total surface area in square metres per kilogramFineness of Cement Construction How2014年1月1日 Initially, detailed experimentation was carried out in a 254 cm diameter batch mill and a relationship for mill scaleup using a linear population balance model in wet grinding systems was (PDF) Population balance model approach to ball mill
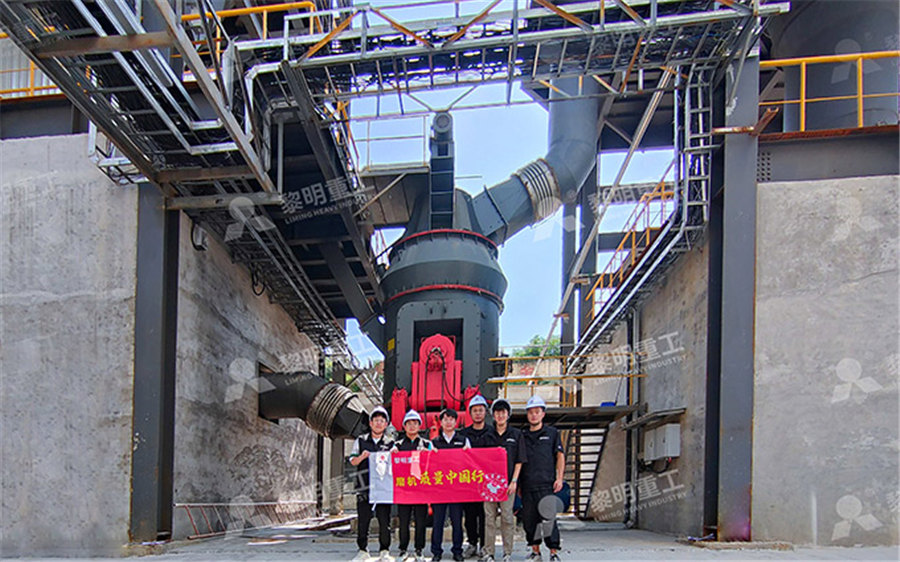
Pulveriser Mill Performance Analysis Optimisation in Super
3 Optimized mill air to fuel ratio 4 Minimum fineness level: greater than or equal 75 percent passing 200 mesh and less than or equal 01 percent remaining on 50 mesh 5 Milltomill mass air and fuel balance within ±5% of the mean 6 Mill outlet temperatures optimal (65°C) and based on2024年10月28日 6Grinding concentration: If the grinding concentration is too high or too low, it will affect the grinding effect and fineness of the ore Method of fineness adjustment of ball mill 1 Adjust the grinding medium Change the type of medium: choose the appropriate type of grinding medium according to the nature of the ore and the grinding How to adjust the fineness of the mine ball mill2019年8月14日 Ball mill is a common grinding equipment in concentrator : hm@gmail Toggle navigation Home It is inversely proportional to the single steel ball energy and grinding fineness in a certain scope D—the inner diameter of The Ultimate Guide to Ball Mills Miningpedia2021年1月29日 x Fineness of the product is adjustable by the height of the dam ring the grinding pressure and mill c Cone stump diameter changed from 1988 mm to 2240 mm in Sep 2018Increase productivity of vertical roller mill using seven QC tools
.jpg)
SIZE REDUCTION BY GRINDING METHODS
2017年3月4日 A stamp mill (or stamp battery or stamping mill) is a type of mill machine that cru shes material by pounding rather than grinding, either for furthe r processing or for extraction of metallic oresMaterial abrasivity The [%] of slag or pouzzolana content on the fresh mill feed for cement grinding The [%] of free silica at mill feed for raw material grinding Moisture content of the mill fresh feed Above or below 2 [%H2O] content The Everything you need to know about clinker/cement 2020年1月16日 The combination of energy intensive and poor performance of comminution process implies that there is a great opportunity for significant energy and economic savings by the improvement of this (PDF) Optimization and performance of grinding 2024年6月14日 The grinding process plays a crucial role in industry, allowing for the reduction of particle sizes of raw materials and substances to the required fineness—either as a finished product or for further technological processes The high demand for micro and nanopowders or suspensions is associated with the high energy consumption of the milling process Therefore, The Influence of the Grinding Media Diameter on Grinding
.jpg)
THE GRINDING CHARGE OF ROTARY MILLS
determining degree the efficiency of the mill work (grinding fineness, wear of grinding media, throughput of the mill, energy specificconsumption, noise produced by the mill, etc) 2 where D is the inside diameter of the drum, and n represents mill speed measured in rpm ncr = D 30 ⋅ 2 critical speed of the drum, rpmFineness Test of Cement AASHTO T 98 and ASTM C 115: Fineness of Portland Cement by the Turbidimeter; AASHTO T 128 and ASTM C 184: Fineness of Hydraulic Cement by the 150mm (No100) and 75mm (No 200) Sieves; AASHTO T 153 and ASTM C 204: Fineness of Hydraulic Cement by AirPermeability Apparatus o AASHTO T 192 and; ASTM C 430: Fineness of Fineness of Cement Civil Engineering2024年9月23日 3 The influence of Feeding Speed on the Mill Feeding speed refers to the amount of ore passing through the mill per unit of time When the mill feeds less, not only is the productivity low, but phenomena such as empty grinding can occur, leading to serious equipment wear and overcrushing of the oreBrief Analysis of the Influence of Operational Factors on Grinding 2014年6月18日 Fineness of cement increases the rate of evolution of heat Finer cement offers a great surface area for hydration and hence faster the development of strength Increase in fineness of cement also increases the drying shrinkage of concrete and hence creates cracks in structures Excessive fineness requirement increases cost of grindingFINENESS OF CEMENT BY BLAINES AIR PERMEABILITY METHOD (IS
.jpg)
Calculate and Select Ball Mill Ball Size for Optimum Grinding
2013年8月3日 In Grinding, selecting (calculate) the correct or optimum ball size that allows for the best and optimum/ideal or target grind size to be achieved by your ball mill is an important thing for a Mineral Processing Engineer AKA Metallurgist to do Often, the ball used in ball mills is oversize “just in case” Well, this safety factor can cost you much in recovery and/or mill liner In the entire production line, the main thing is to convert materials into finished products After the material is crushed to the required particle size, the material is sent to the storage hopper by the elevator, and then sent to the main grinding chamber by the feeder evenly and orderlyHow to calculate the output of the high pressure roller grinding mill