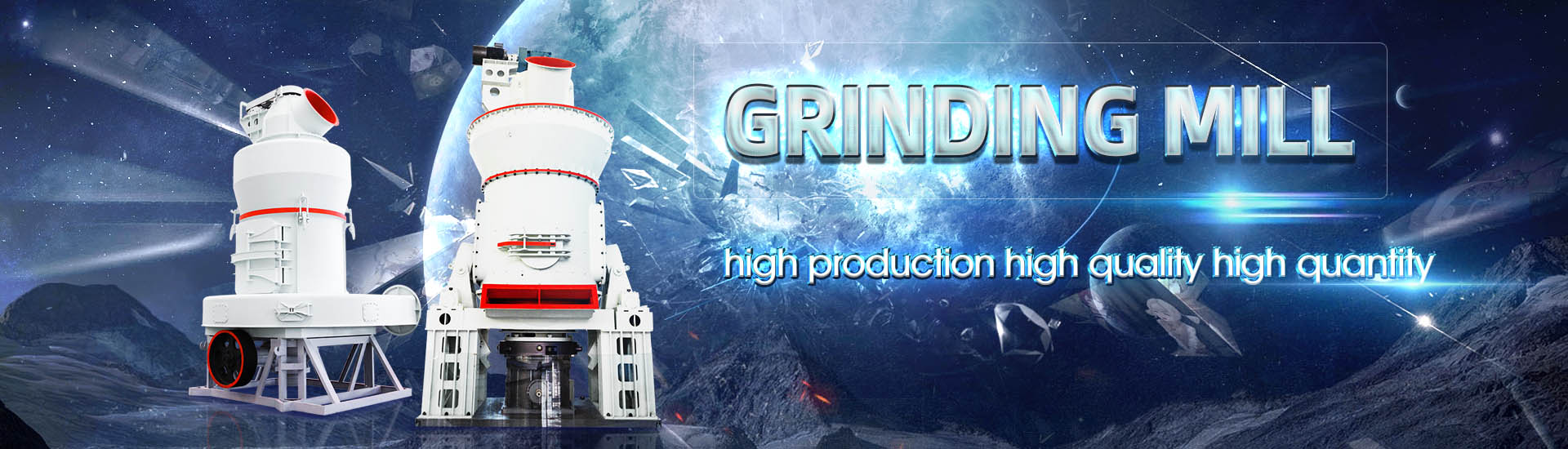
Calculation of crushing rate of cement mill steel balls
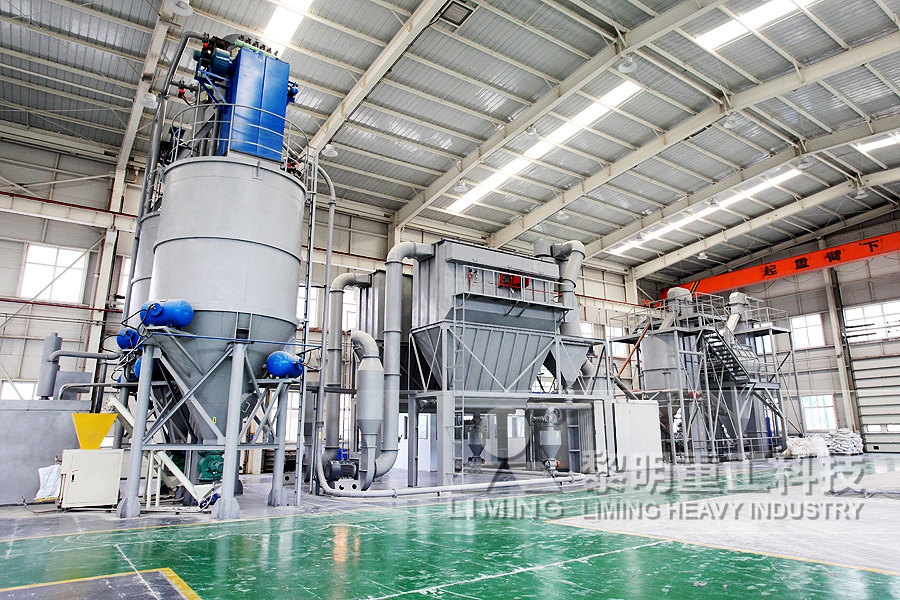
BALL MILLS Ball mill optimisation Holzinger Consulting
the ball mill had an average production rate of 190tph with a specific electrical energy consumption of 355kWh/t Its operational issues included: • oversized limestone • wornout lifting liners with liner thickness decreasing from 80 to 20mm • lowquality media Following The document contains formulas and examples for calculating key performance metrics for ball mills used in cement production It includes formulas to calculate power consumption, production rate, specific power, circulation factor, Ball Mill Calculations PDF Mill (Grinding) Industrial The mill balls calculated parameters 8 1 FIELD OF APPLICATION This standard applies to steel grinding balls produced by rolling, forging, STEEL MILLING BALLS FOR BALL MILLS Energosteel Grinding online live calculators for grinding calculations, Ball mill, tube mill, critical speed, Degree of filling balls, Arm of gravity, mill net and gross powerball mill calculations, grinding media filling degree, ball size, mill
.jpg)
THEORETICAL CALCULATION OF MILL STEEL BALL SIZESciEngine
From the principle of crushing machanics, a theoretical formula for calculating ballsizes for ball mills has been derived Empirical parameters are obtained from experimentaland practical This document provides guidance on ball mill grinding processes It covers topics such as ball mill design including length to diameter ratios, percent loading, critical speed, and internals Ball Mill Grinding Process Handbook2019年10月1日 The calculation results show that the distribution of the broken energy in the region is related to the distribution of the ball, and the region with more balls has greater A novel approach of evaluating crushing energy in ball mills using optimization of cement grinding operation in ball mills Several energy efficient options for cement grinding are available today such as vertical roller mills, roller presses (typically in combination OPTIMIZATION OF CEMENT GRINDING OPERATION IN BALL MILLS
.jpg)
Grinding in Ball Mills: Modeling and Process Control ResearchGate
2012年6月1日 The paper presents an overview of the current methodology and practice in modeling and control of the grinding process in industrial ball mills Basic kinetic and energy Abstract: The paper presents an overview of the current methodology and practice in modeling and control of the grinding process in industrial ball mills Basic kinetic and energy models of Grinding in Ball Mills: Modeling and Process Control Sciendo2019年8月14日 The Grinding Media Of Ball Mill – Steel Balls back to top The steel balls in ball mill are consumable, which need to be supplied from now and on 1 The filling rate of steel balls Steel balls undertake the main job in grinding, therefore, the number of steel balls in ball mill is highly relative with the grinding strengthThe Ultimate Guide to Ball Mills Miningpedia2024年2月27日 Processing of ball mill balls The ball mill balls on the market can be divided into cast steel balls and forged steel balls according to their production process, but their wear resistance is not the same Generally How To Choose Steel Balls For Ball Mill? Grinding
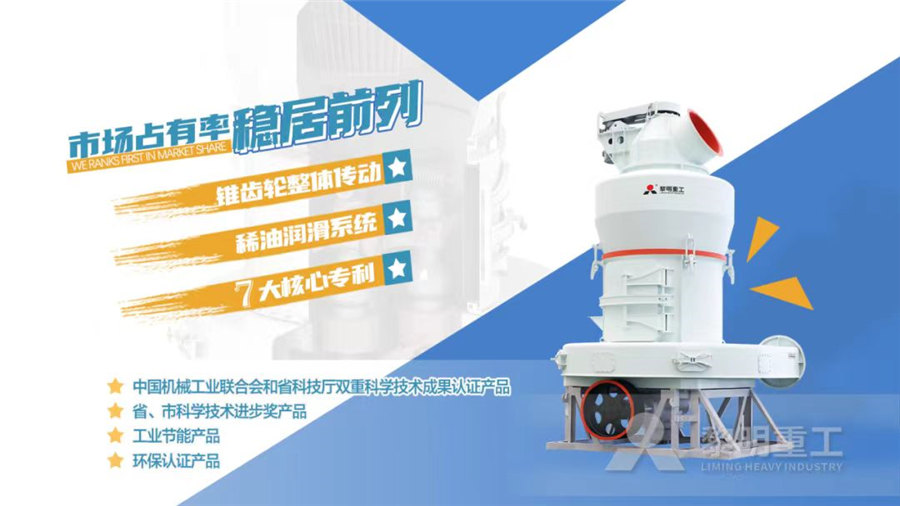
Complete Lecture about Crushers in Cement Industry
The wear rate of CrVasteel is 3 grams and that of CrSiVasteel was estimated to 2 grams per ton of crushed material [47] The rim speed of the hammers is in the range of 25 to 50 m/s The number of revolutions of both the single and double rotor crushers is in the range of 250 400 rpm, depending upon the crusher sizeSteel balls These are less durable than ceramic balls, but they are much cheaper They also have a higher wear rate than ceramic balls, so they will need to be replaced more frequently 3 Glass beads These are the least expensive type of grinding media, but they have the shortest lifespan and highest wear rate Grinding media wear rate Formula to calculate grinding media wear rate for cement mill2024年2月19日 They are using new wearresistant steel balls Good quality steel balls are added based on the amount of ore processed per ton (that is, 08kg per ton of ore) Generally, steel balls are required to process one ton of ore (1kg12kg) In short, the ratio of steel balls in a ball mill is a relatively complex technical issueBall Mill Steel Balls: Quality And Gradation JXSC Mineral2023年2月15日 A beneficiation plant in Singapore loads balls into a ϕ 1500mm×3000mm wet grid type ball mill, determines the filling rate ϕ = 50%, and selects cast steel grinding balls δ = 45 t/m 3 The ball mill processes the mediumhard ore 1 See Table 1 for the sieving analysis results of all the ore samples from a ball mill Table 1Method of Steel Grinding Ball Proportioning and Example
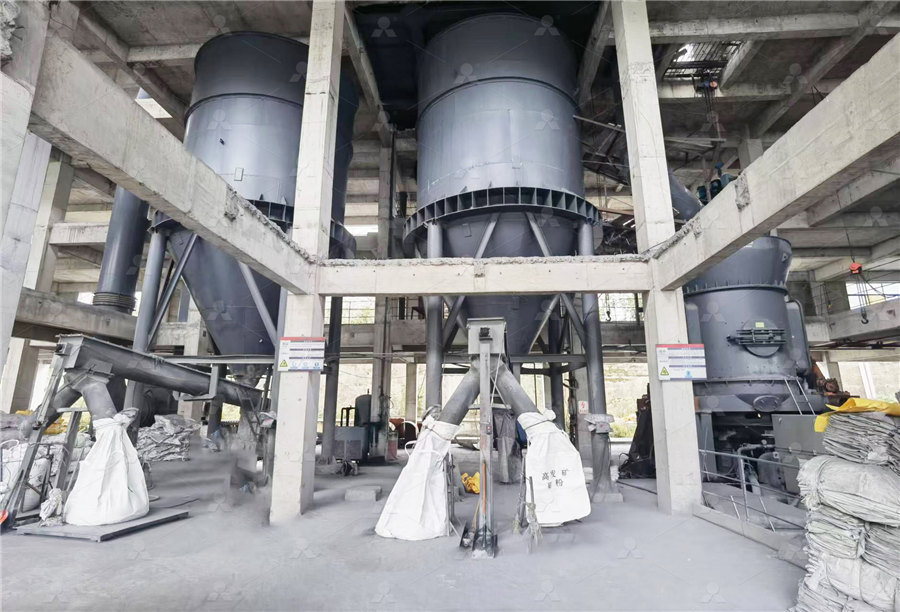
Cement Ball Mill Cement Grinding Machine Cement Mill
What Is A Cement Ball Mill The cement ball mill is a kind of cement grinding millIt is mainly used for grinding the clinker and raw materials of the cement plant, and also for grinding various ores in metallurgical, chemical, and electric power enterprisesIt has the characteristics of strong adaptability to materials, continuous production, a large crushing ratio, and easytoadjust the 2022年11月9日 Through the gradation of large and small balls, the gap between the steel balls is reduced, and the bulk density of the steel balls is increased, so that it has an appropriate material storage capacity On the one hand, the flow rate of the material in the mill can be controlled, and the residence time can be extended to obtain sufficient grindingThe Role of Ball Mill Steel Balls JXSC Mineral2022年1月1日 We investigated the effects of feed size and ball diameter on the grinding rate constant of the materials used when the mass of balls, mass of feed, and the mill's rotational speed were constant Effect of grinding media on the milling efficiency of a ball millOptimization of the Cement Ball Mill Operation Optimization addresses the grinding process, maintenance and product quality efficiency, specific power consumption, system throughput, and wear rate of grinding media and liners Changing the separator to high efficiency type bringa about better residue value (on 45 sOPTIMIZATION OF CEMENT GRINDING OPERATION IN BALL MILLS
.jpg)
Solved A cement grinding mill “A” with a capacity of 50 tons
A cement grinding mill “A” with a capacity of 50 tons per hour utilizes forged steel grinding balls costing P12,000 per ton, which have a wear rate of 100 grams per ton cement milled Another cement mill “B” of the same capacity uses high chrome steel grinding balls costing P50,000 per ton with wear rate of 20 grams per ton cement milled2020年11月22日 The balls of cast iron allo y steel that used as grinding media inside t he cement horizontal mill These balls were subjected to the wear processes during the mill rotationWear Resistance Improvement for Grinding Balls of Horizontal Cement 2019年1月1日 A grain size reduction hammer mill for crushing corn (Zea mays L) was designed depending on variety characteristics and by using computer aided design “ANSYS” softwareDesign and Evaluation of Crushing Hammer mill ResearchGate2023年5月1日 One of the current topics in the cement industry for reducing power consumption in cement ball milling is to properly replace conventional steel balls with alternative types of ball materials, including ceramic balls [21, 22]The rationale for this replacement is that, in comparison to steel balls, ceramic balls have significantly lower ball density (approximately half the density A comparative analysis of steel and alumina balls in fine milling of
.jpg)
A Review of the Grinding Media in Ball Mills for Mineral Processing
2023年10月27日 The ball mill is a rotating cylindrical vessel with grinding media inside, which is responsible for breaking the ore particles Grinding media play an important role in the comminution of mineral ores in these mills This work reviews the application of balls in mineral processing as a function of the materials used to manufacture them and the mass loss, as 2023年5月12日 Figure 2 shows an example of calculation of CM loading displacement in the first chamber of the mill 4 × 135 m, from which it follows that for each cycle CM loading makes a complex movement—along the axis of OУ this trajectory is an elongated ellipse (Fig 2a), the major axis of which coincides with the longitudinal axis of OУ crushing cylinder, and relative to Power Calculation of BallTube Mill Drives in the Construction 2021年1月27日 The raw material for cement production has a high abrasion rate Consequently, when calculating the assortment the balls with increased volumetric hardness have been taken into account Into the first chamber of twochamber mill is loaded with balls from 80 to 40 mm in diameter The second chamber is loaded with balls from 40 to 25 mm in diameterCALCULATION OF THE GRINDING BALLS ASSORTMENT FOR THE CEMENT MILL2023年5月1日 This study explored the breakage kinetics of cement clinker in a labscale ball mill loaded with steel or alumina balls of 20, 30, and 40 mm sizes and their mixtures The temporal evolution of the particle size distribution (PSD) was measured by sieving and laser diffraction A global optimizerbased backcalculation method, based on a population balance model (PBM), A comparative analysis of steel and alumina balls in fine milling of
.jpg)
Ball Mill Parameter Selection Calculation JXSC
2019年8月30日 The quality and surface area of forged steel balls of various sizes are shown in Table 112 A kind of Because of the wear of steel balls in the mill production process, in order to keep the mill stable Steel balls need to be added regularly The maximum diameter of additional steel balls is still determined by the method mentioned above2021年6月29日 Nowadays, ball mills are widely used in cement plants to grind clinker and gypsum to produce cement The research focuses on the mill speed as well as air classifier speed effect on the two Effects of Mill Speed and Air Classifier Speed on KILN GAS is often used for the raw mill instead of the cement mill because the temperatures are higher than cooler air (typically 300 –350°C) and the raw meal is generally more moist than cement Kiln gas has high CO2 / CO content, and Everything you need to know about clinker/cement 2022年10月14日 Abstract The results of industrial tests of ShKh15steel grinding balls with diameters of 25, 30, and 35 mm of 5th hardness group as per GOST (State Standard) 7524–2015 at AO Kharkiv Pilot Cement Plant during grinding of cement in the second chamber of a cement mill are presented It is shown that the use of ShKh15 steel grinding balls with small diameters Efficiency of Using Small Diameter Grinding Balls for Cement
.jpg)
(PDF) Failure of Steel Grinding Balls ResearchGate
PDF On May 1, 2019, N A Shaburova published Failure of Steel Grinding Balls Find, read and cite all the research you need on ResearchGate511 The balls must be produced in accordance with requirements of this standard 512 The balls dimensions and marginal deviations have given at Table 1 513 The balls calculation parameters have given in Annex A 3STEEL MILLING BALLS FOR BALL MILLS Energosteel Grinding 2022年2月8日 A population balance model is applied to a steel ball mill Experimental data were obtained for two types of balls with different chemical compositions using a marked ball test in an industrial Study of steel ball recharge and consumption in a wet cement Steel balls Steel balls are one of the most widely used grinding media in cement ball mills, their diameters can range from 20mm to 150mm according to different grinding requirements In a cement ball mill, generally, φ50100mm steel balls are used in the coarse grinding chamber, φ2050mm steel balls are used in the fine grinding chamber 2Ball Mill Grinding Media Steel Balls for Ball Mills AGICO Group
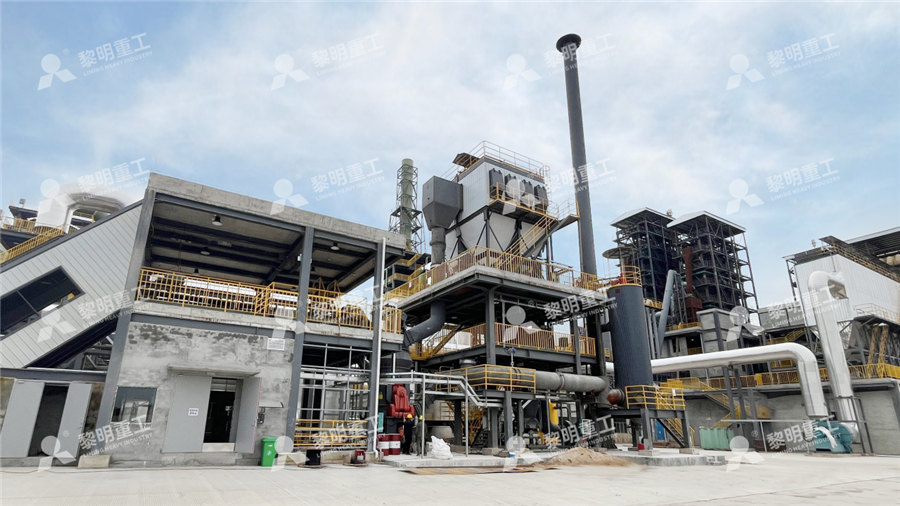
Grinding Media: Forged Steel Balls FAQs Camasteel Quality Steel
2022年5月17日 Grinding media is used for disintegrating secondary materials like cement, rocks, metals, and ores in the mining and cement industry Here at Camasteel, we supply Forged Steel The power per tonne of the ball mill is determined by the ball mill fill rate Good Steel balls will have: Greater hardness; Greater endurance and wear 2024年1月26日 Cement ball mill is a well known machine to grind raw material (hard clinker) into grey powder: Cement A cement ball mill is a horizontal cylinder which is partly filled with steel balls of different sizes along with clinker (raw material) and rotates about its axis which provides tumbling action in ball mill which in turn grind raw material Computation of charging media for a double compartment cement ball mill 2019年8月14日 The Grinding Media Of Ball Mill – Steel Balls back to top The steel balls in ball mill are consumable, which need to be supplied from now and on 1 The filling rate of steel balls Steel balls undertake the main job in grinding, therefore, the number of steel balls in ball mill is highly relative with the grinding strengthThe Ultimate Guide to Ball Mills Miningpedia2024年2月27日 Processing of ball mill balls The ball mill balls on the market can be divided into cast steel balls and forged steel balls according to their production process, but their wear resistance is not the same Generally How To Choose Steel Balls For Ball Mill? Grinding
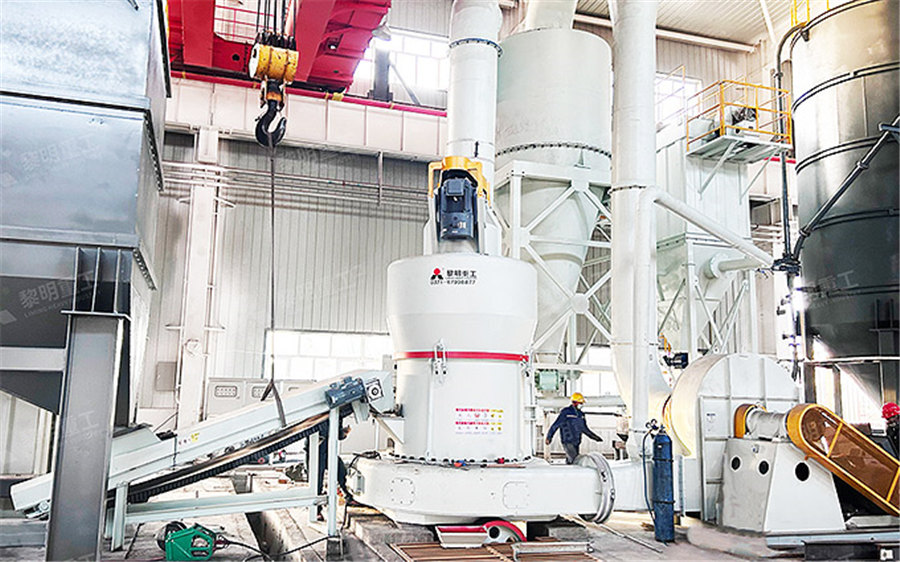
Complete Lecture about Crushers in Cement Industry
The wear rate of CrVasteel is 3 grams and that of CrSiVasteel was estimated to 2 grams per ton of crushed material [47] The rim speed of the hammers is in the range of 25 to 50 m/s The number of revolutions of both the single and double rotor crushers is in the range of 250 400 rpm, depending upon the crusher sizeSteel balls These are less durable than ceramic balls, but they are much cheaper They also have a higher wear rate than ceramic balls, so they will need to be replaced more frequently 3 Glass beads These are the least expensive type of grinding media, but they have the shortest lifespan and highest wear rate Grinding media wear rate Formula to calculate grinding media wear rate for cement mill2024年2月19日 They are using new wearresistant steel balls Good quality steel balls are added based on the amount of ore processed per ton (that is, 08kg per ton of ore) Generally, steel balls are required to process one ton of ore (1kg12kg) In short, the ratio of steel balls in a ball mill is a relatively complex technical issueBall Mill Steel Balls: Quality And Gradation JXSC Mineral2023年2月15日 A beneficiation plant in Singapore loads balls into a ϕ 1500mm×3000mm wet grid type ball mill, determines the filling rate ϕ = 50%, and selects cast steel grinding balls δ = 45 t/m 3 The ball mill processes the mediumhard ore 1 See Table 1 for the sieving analysis results of all the ore samples from a ball mill Table 1Method of Steel Grinding Ball Proportioning and Example
.jpg)
Cement Ball Mill Cement Grinding Machine Cement Mill
What Is A Cement Ball Mill The cement ball mill is a kind of cement grinding millIt is mainly used for grinding the clinker and raw materials of the cement plant, and also for grinding various ores in metallurgical, chemical, and electric power enterprisesIt has the characteristics of strong adaptability to materials, continuous production, a large crushing ratio, and easytoadjust the 2022年11月9日 Through the gradation of large and small balls, the gap between the steel balls is reduced, and the bulk density of the steel balls is increased, so that it has an appropriate material storage capacity On the one hand, the flow rate of the material in the mill can be controlled, and the residence time can be extended to obtain sufficient grindingThe Role of Ball Mill Steel Balls JXSC Mineral2022年1月1日 We investigated the effects of feed size and ball diameter on the grinding rate constant of the materials used when the mass of balls, mass of feed, and the mill's rotational speed were constant Effect of grinding media on the milling efficiency of a ball millOptimization of the Cement Ball Mill Operation Optimization addresses the grinding process, maintenance and product quality efficiency, specific power consumption, system throughput, and wear rate of grinding media and liners Changing the separator to high efficiency type bringa about better residue value (on 45 sOPTIMIZATION OF CEMENT GRINDING OPERATION IN BALL MILLS