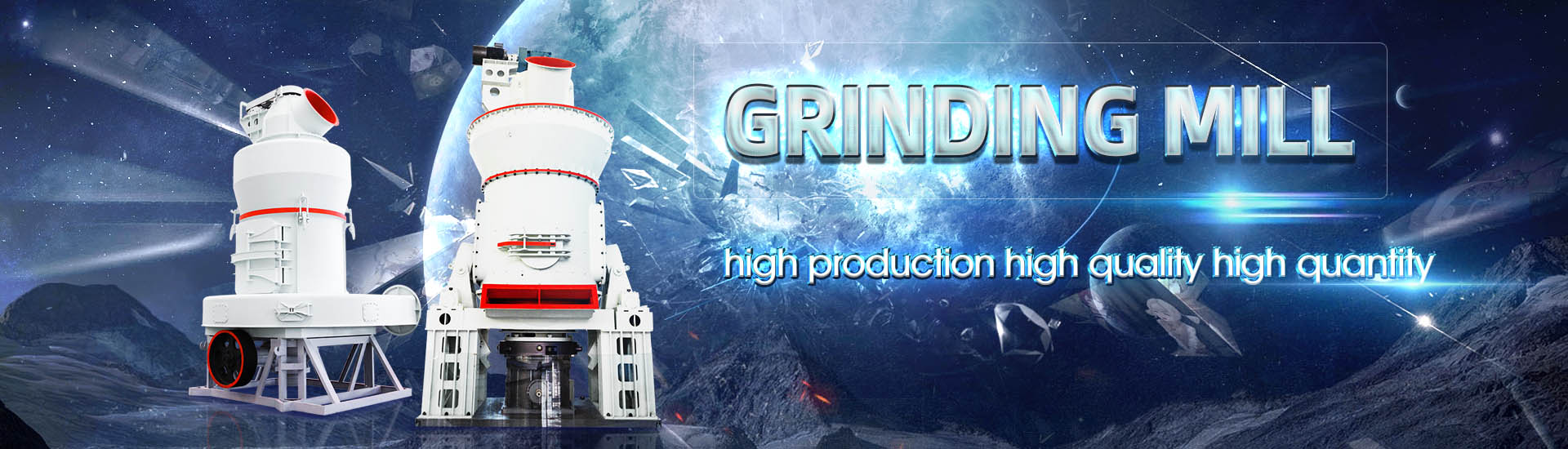
HOME→Iron making, limestone action to make iron, limestone action to make iron, limestone action to make iron
Iron making, limestone action to make iron, limestone action to make iron, limestone action to make iron
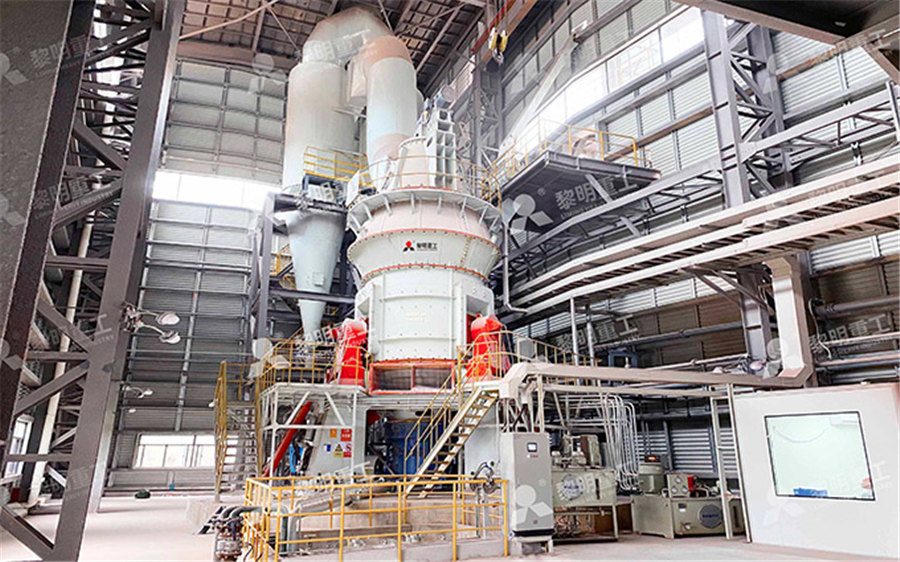
Effect of adding limestone on the metallurgical properties of
2015年8月10日 One of the most common fluxing materials for iron ore pellet production is limestone, which is mainly calcium oxide (CaO) In this study, the effect of adding limestone on the metallurgical properties (reducibility, swelling, cracking, softening temperature, Low 2017年10月10日 Iron is made by reacting iron ore (iron oxide and impurities), coke (a reductant) and limestone (CaCO 3) in a blast furnace Iron ores with lower iron content such as taconite are first processed to concentrate the iron level Ironmaking 101 – From Ore to Iron with Blast 2024年3月14日 Applications of Limestone in Iron and Steel Industry Limestone has several applications in the iron and steel industry Its versatile properties make it an essential Limestone—A Review with Special Reference to the Iron 2024年3月13日 Limestone, Fluorite, and Calcium carbide are the materials used as flux in steel making For steel making, a superior grade of limestone is required to control slag volume and Limestone—A Review with Special Reference to the Iron and
.jpg)
How Iron Is Made Steel Museum
In the blast furnace process, iron ore, coke (processed coal), and limestone (the charge) are poured into a vessel lined with refractory (heatresistant brick) When heated, the coke reacts with oxygen and the limestone combines with In blast furnace (BF) iron making lime stone is used as source of CaO to neutralize the all acidic oxides present in iron ore and make fluid slag of suitable basicity Limestone is the most common source of CaO, abundantly available Development on Iron Ore Pelletization Using Limestone is a very important industrial mineral Its chemical properties make it a valuable mineral for a wide range of industrial/manufacturing uses including in production of iron and steelLIMESTONE – A REVIEW WITH SPECIAL REFERENCE TO The production of iron from its ore involves an oxidationreduction reaction carried out in a blast furnace Iron ore is usually a mixture of iron and vast quantities of impurities such as sand and 41631: Iron Production Chemistry LibreTexts
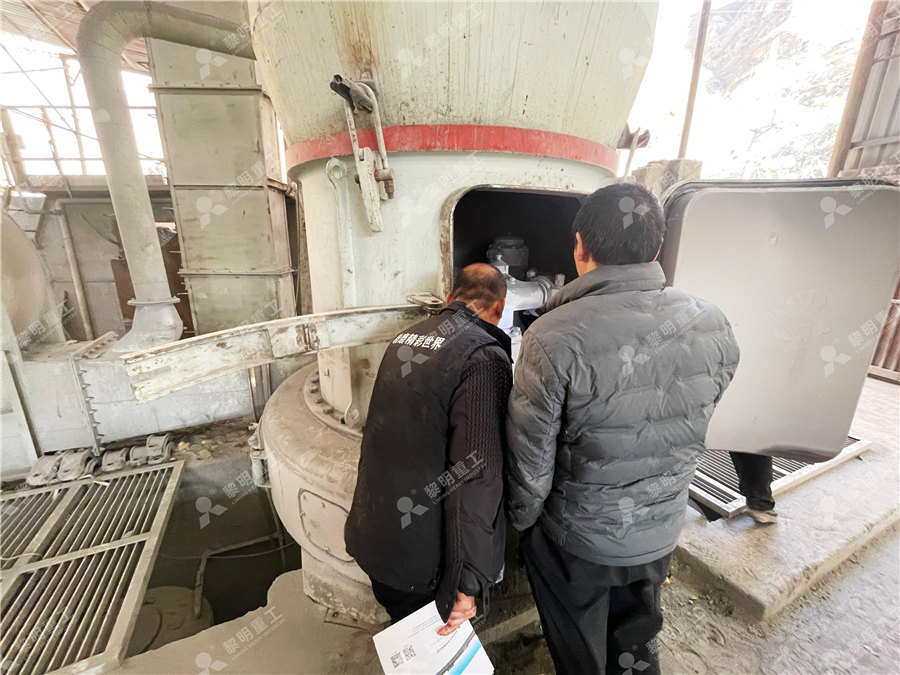
Effect of Adding Limestone on the Metallurgical Properties of Iron
2015年6月5日 10) Various studies on the effects of limestone on slag formation from iron ore have been reported, including: CaO as a raw material component of the sintered iron ore 2021年7月16日 This work investigates the melting behaviour of iron ore with calciumbased fluxes, including lime, limestone and basic oxygen furnace (BOF) steelmaking slag With an Full article: Observation of the reactions between iron ore 2013年5月8日 Specification of limestone and dolomite for iron making is less rigid But for steelmaking limestone is to have very low silica (SiO2) and alumina (Al2O3) since these elements need additional flux to neutralize them which Limestone and Dolomite and their Use in Iron 2023年10月21日 Limestone is a sedimentary rock primarily composed of calcium carbonate (CaCO3) in the form of mineral calcite or aragoniteIt is one of the most common and widely distributed rocks on Earth, with a wide range of Limestone Types, Properties, Composition,
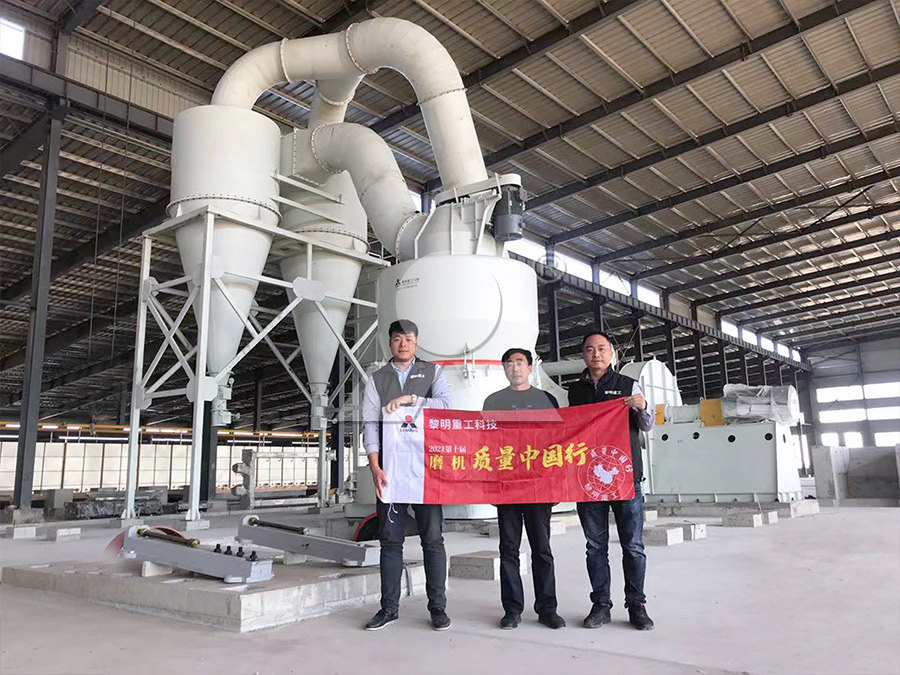
Limestone—A Review with Special Reference to the Iron
2024年3月14日 Limestone—A Review with Special Reference to the Iron and Steel Industry Pradeep Kumar Jain and Gaurav Sharma Abstract Limestone, Fluorite, and Calcium carbide are the materials used as flux in steel making For steel making, a superior grade of limestone is required to control slag volume and improve productivityTo make a useable metal, an ironworks has to get rid of the unwanted components of this mixture and keep as much of the iron as possible, producing a purer metal The ironmaking process develops Ironmaking reached Britain from Europe and the Middle East around 450 BC At this time the process only needed iron ore, charcoal and clayHow iron is made Forestry and Land Scotland2024年3月17日 Steel making is a sophisticated process that turns iron ore into steel, involving methods like the Blast Furnace and Electric Arc Furnace to produce various grades of steel iron ore is combined with coke and limestone which act as a reducing agent and flux respectively Intense heat triggers a series of chemical reactions that strip away A Visual Guide: Steel Making Process Chart Cabaro GroupLimestone is a very common sedimentary rock consisting of calcium carbonate (more than 50%) It is the most common nonsiliciclastic (sandstone and shale are common siliciclastic rocks) sedimentary rockLimestones are rocks that are composed of mostly calcium carbonate (minerals calcite or aragonite) Carbonate rocks where the dominant carbonate is dolomite (calcium Limestone Sedimentary rocks Sandatlas
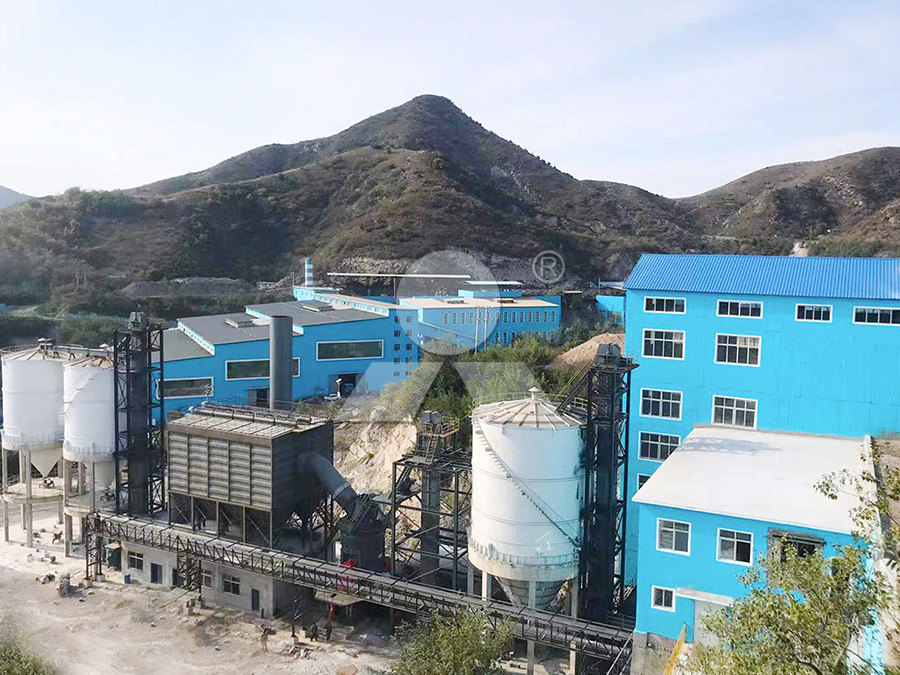
(PDF) Iron Ore Sintering: Process ResearchGate
2017年2月16日 Sintering is a thermal agglomeration process that is applied to a mixture of iron ore fines, recycled ironmaking products, fluxes, slagforming agents and solid fuel (coke)2017年10月10日 Ironmaking Blast Furnace Iron is made by reacting iron ore (iron oxide and impurities), coke (a reductant) and limestone (CaCO 3) in a blast furnace Iron ores with lower iron content such as taconite are first processed to Ironmaking 101 – From Ore to Iron with Blast FurnacesOriginally, the iron was collected in pools called pigs, which is the origin of the name pig iron Figure \(\PageIndex{1}\): A Blast Furnace for Converting Iron Oxides to Iron Metal (a) The furnace is charged with alternating layers of iron ore (largely Fe 2 O 3) and a mixture of coke (C) and limestone (CaCO 3) Blasting hot air into the 233: Metallurgy of Iron and Steel Chemistry LibreTexts2017年10月17日 The generation, storage and transportation of byproducts increases iron and steelmaking cost and energy consumption, so the iron and steel industry is constantly developing processes to reduce or eliminate byproduct generation Direct iron reduction processes produce a form of sponge iron called direct reduced iron (DRI)Ironmaking 101 – From Ore to Iron with Smelting and Direct Iron
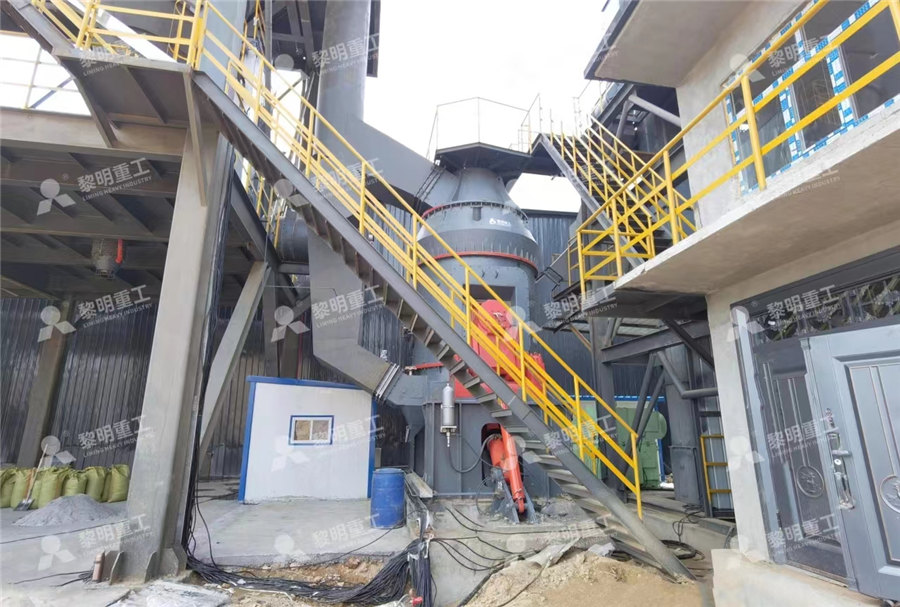
How iron is made material, manufacture, making, history,
The raw materials used to produce pig iron in a blast furnace are iron ore, coke, sinter, and limestone Iron ores are mainly iron oxides and include magnetite, hematite, limonite, and many other rocks The iron content of these ores ranges from 70% down to 20% or lessThis is even harder than pig iron Wrought Iron/ Malleable Iron Wrought iron is the purest form of iron available commercially available and is prepared from cast iron by heating cast iron in a furnace lined with Haematite (Fe 2 O 3) The Extraction of Iron Metallurgy Blast Furnace In limestone’s case, this sediment includes marine fossils, such as shells and coral That’s because millions of years ago, the areas where limestone forms used to be underwater, but as the water receded, the silt and fossils remained The Secret To Limestone’s Strength Is In How It’s 2023年9月8日 A stable and efficient operation of the ironmaking blast furnace is prerequisite to reduce the greenhouse gas emission JSW Steel, Salem have been proposed many projects to reduce greenhouse gas Blast Furnace process optimization for sustainable Iron making
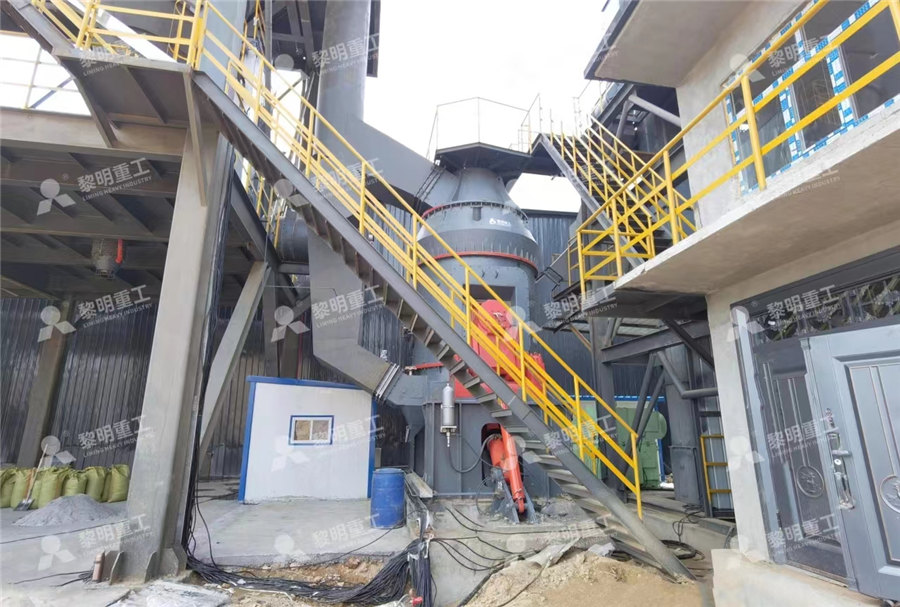
Prospects of utilization of waste dumped lowgrade limestone for iron
2020年5月1日 Low grade dumped limestone sample having high silica of 81%, 368% CaO, and 3% Al 2 O 3 has been studied with the aim to reduce the silica level to below 3% for its utilization in iron making Beneficiation study of the sample was initiated with desliming of the feed sample of −100 µm to remove the siliceous ultrafine particles and to improve the feed quality6 天之前 Limestone reduces the viscosity, making the liquid glass easier to handle and form into the required shape A final benefit of limestone in glassmaking is that it helps to avoid devitrification, a process of crystallization around small impurities in the mix that causes clouding and other defects The basic chemistry of limestone comprises Limestone in Glassmaking: What You Need to Know2024年1月7日 For example, the presence of iron oxide can give limestone a reddish hue, while organic matter can lead to darker shades Different types of limestone form under different conditions and environmentsLimestone: characteristics, formation, uses ZME Science2021年8月16日 Problems with Bloomery Furnaces This way of making iron alloys may seem fine You get wrought iron that can be used to forge steel swords any number of practical iron tools, armor or what notGuide to Historic Iron Making Medium
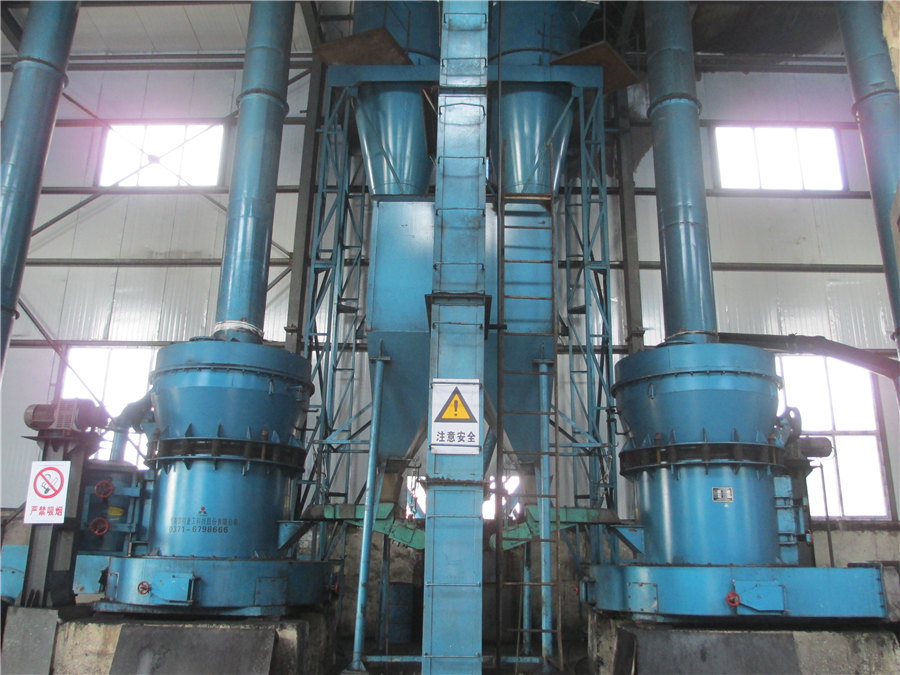
Ironmaking Process an overview ScienceDirect Topics
Quality requirements of iron ore for iron production L Lu, D Zhu, in Iron Ore, 2015 164 Summary The BF ironmaking process is currently the dominant process for providing steelmaking raw materials worldwide However, the BF process relies heavily on metallurgical coke and involves cokemaking and sintering operations, which often attract serious environmental 2019年6月11日 The remaining 2% of domestic iron ore was produced for nonsteel end uses Seven openpit iron ore mines (each with associated concentration and pelletizing plants), and three iron metallic plants—one directreduced iron (DRI) plant and two hotbriquetted iron (HBI) plants— operated during the year to supply steelmaking raw materialsSintering: A Step Between Mining Iron Ore and Steelmaking2015年6月5日 10) Various studies on the effects of limestone on slag formation from iron ore have been reported, including: CaO as a raw material component of the sintered iron ore making process, 15) CaO Effect of Adding Limestone on the Metallurgical Properties of Iron 2024年9月24日 consists of iron sinter/pellets +coke and limestone During descent, iron oxide is reduced to FeO and limestone decomposed to CaO and CO2 The combustion of coke at the tuyere level with air raises the temperature in between 1800 to 2100, and melts slag and metalLecture 28: Materials Balance in Iron making Key words:

LECTURE NOTES ON IRON MAKING SUBJECT CODE:
2021年4月8日 2 An introduction to modern iron making, R H Tupkary, Khanna Publishers (2004) Course Outcomes After completing this course, the student should be able to: 1 Describe the physical and chemical processes that take place during iron making 2 Analyse the effect of change in process parameters in iron making 32023年6月6日 Overview of LimestoneTo gain a comprehensive understanding of limestone in design and installation, dive into the properties and common uses of limestone This versatile material impresses homeowners and DIY enthusiasts alike with its wide range of finishes and durability Learn how to use limestone to elevate your next home projectProperties of Limestone Work: A Comprehensive Guide to Design and 2022年5月2日 Left: Pig iron is the raw material used to make other forms of iron and steel Each of these iron pieces is one pig Middle: Cast iron was used for strong, structural components like bits of engines and bridges before steel became popular Right: Wrought iron is a softer iron once widely used to make everyday things like street railings Today Iron and steel Introduction to their science, properties, uses2021年2月1日 It was observed that the iron ore sample contains 5975% Fe, 452% SiO 2, 384% Al 2 O 3, and higher content of LOI 485%The LOI distribution for the iron ore fine is listed in Table 2 indicating the weight loss% due to goethite at 400 °C; kaolinite at 850 °C and carbonate minerals at 950 °C The heating cycle indicates that maximum weight loss (~65%) occurs at Effect of limestone and dolomite flux on the quality of
.jpg)
Exploring selected pathways to low and zero CO2
2022年3月15日 The carbon cycle includes shortterm processes (eg, photosynthesis, respiration, exchanges between air and sea, etc) and longterm processes (exchanges between the oceans, atmosphere, biosphere, and soils) (Berner, 2003)The consumption of fossil fuels has rapidly increased, resulting in the emission of a large amount of CO 2 disturbing the global 2020年3月13日 The analysis of the pig iron was 927% Fe, 4% C, 2% Si, 09% P 04% Mn The iron ore charged into the furnace contained 78% Fe 2 O 3 , 84% SiO 2 , 5% Al 2 O 3 , 51% H 2 O, 18% MnO, and 17% P 2 O 5 Unit 2 Iron Making Week 1 NPTEL2020年8月19日 What is left is iron The blast furnace’s height lets the rising gases preheat the ore and gives the iron more distance to descend as it softens – so it absorbs more carbon from the fuel Because iron’s melting point falls as its carbon content rises, the iron becomes fully molten A calciumbased “flux,” usually limestone, is addedIron Making Hopewell Furnace National Historic Site (US2021年7月15日 Limestone quarries and their restoration provide a major opportunity to protect and enhance biodiversity Most of the limestone captive mines of the cement industry have a long legacy of goodquality restoration Therefore, one can make a significant contribution in terms of environment preservation and protectionLimestone Mining, Industry, and Society SpringerLink
.jpg)
Limestone and Dolomite and their Use in Iron
2013年5月8日 Specification of limestone and dolomite for iron making is less rigid But for steelmaking limestone is to have very low silica (SiO2) and alumina (Al2O3) since these elements need additional flux to neutralize them which 2023年10月21日 Limestone is a sedimentary rock primarily composed of calcium carbonate (CaCO3) in the form of mineral calcite or aragoniteIt is one of the most common and widely distributed rocks on Earth, with a wide range of Limestone Types, Properties, Composition, 2024年3月14日 Limestone—A Review with Special Reference to the Iron and Steel Industry Pradeep Kumar Jain and Gaurav Sharma Abstract Limestone, Fluorite, and Calcium carbide are the materials used as flux in steel making For steel making, a superior grade of limestone is required to control slag volume and improve productivityLimestone—A Review with Special Reference to the Iron To make a useable metal, an ironworks has to get rid of the unwanted components of this mixture and keep as much of the iron as possible, producing a purer metal The ironmaking process develops Ironmaking reached Britain from Europe and the Middle East around 450 BC At this time the process only needed iron ore, charcoal and clayHow iron is made Forestry and Land Scotland
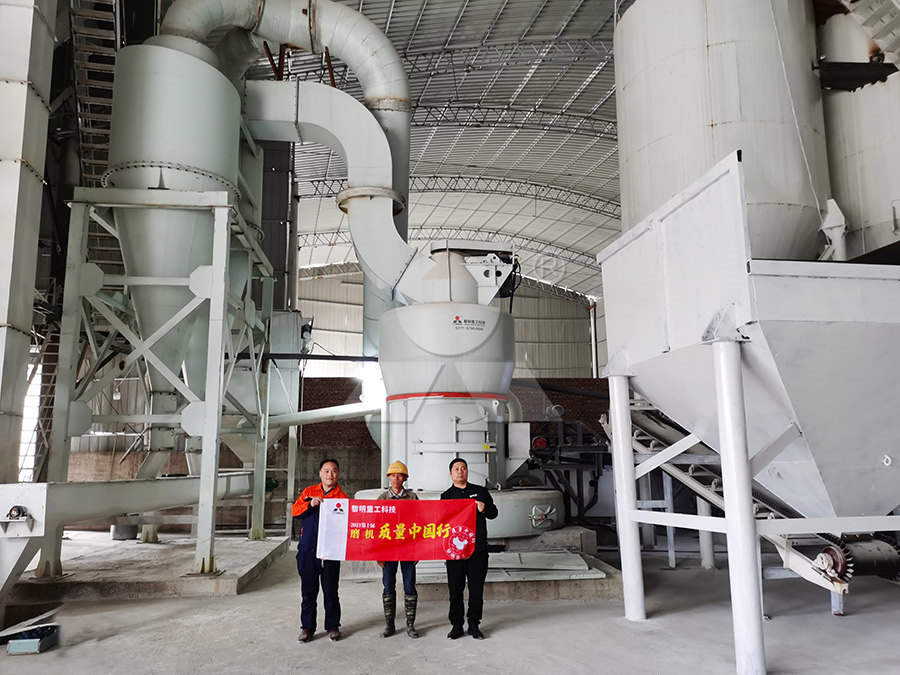
A Visual Guide: Steel Making Process Chart Cabaro Group
2024年3月17日 Steel making is a sophisticated process that turns iron ore into steel, involving methods like the Blast Furnace and Electric Arc Furnace to produce various grades of steel iron ore is combined with coke and limestone which act as a reducing agent and flux respectively Intense heat triggers a series of chemical reactions that strip away Limestone is a very common sedimentary rock consisting of calcium carbonate (more than 50%) It is the most common nonsiliciclastic (sandstone and shale are common siliciclastic rocks) sedimentary rockLimestones are rocks that are composed of mostly calcium carbonate (minerals calcite or aragonite) Carbonate rocks where the dominant carbonate is dolomite (calcium Limestone Sedimentary rocks Sandatlas2017年2月16日 Sintering is a thermal agglomeration process that is applied to a mixture of iron ore fines, recycled ironmaking products, fluxes, slagforming agents and solid fuel (coke)(PDF) Iron Ore Sintering: Process ResearchGate2017年10月10日 Ironmaking Blast Furnace Iron is made by reacting iron ore (iron oxide and impurities), coke (a reductant) and limestone (CaCO 3) in a blast furnace Iron ores with lower iron content such as taconite are first processed to Ironmaking 101 – From Ore to Iron with Blast Furnaces
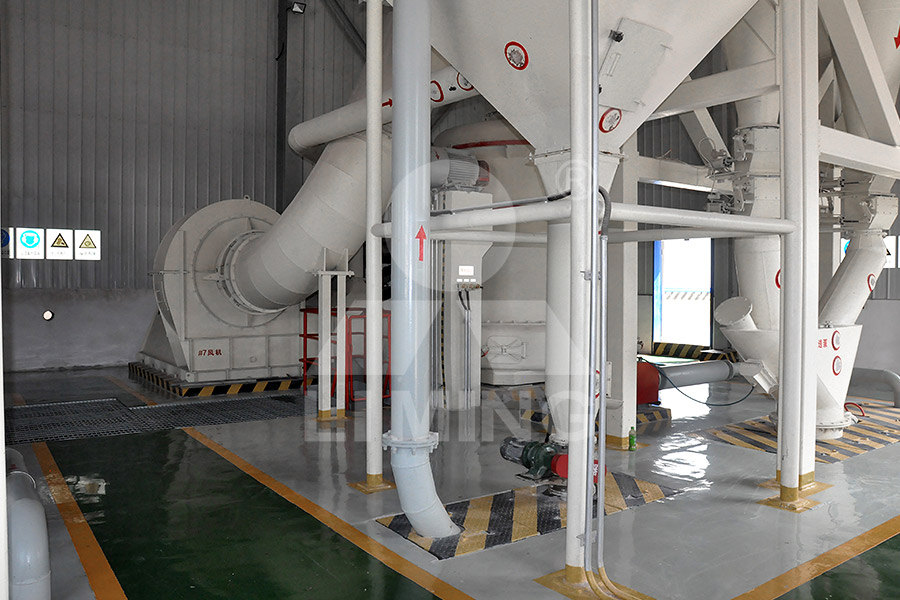
233: Metallurgy of Iron and Steel Chemistry LibreTexts
Originally, the iron was collected in pools called pigs, which is the origin of the name pig iron Figure \(\PageIndex{1}\): A Blast Furnace for Converting Iron Oxides to Iron Metal (a) The furnace is charged with alternating layers of iron ore (largely Fe 2 O 3) and a mixture of coke (C) and limestone (CaCO 3) Blasting hot air into the 2017年10月17日 The generation, storage and transportation of byproducts increases iron and steelmaking cost and energy consumption, so the iron and steel industry is constantly developing processes to reduce or eliminate byproduct generation Direct iron reduction processes produce a form of sponge iron called direct reduced iron (DRI)Ironmaking 101 – From Ore to Iron with Smelting and Direct Iron