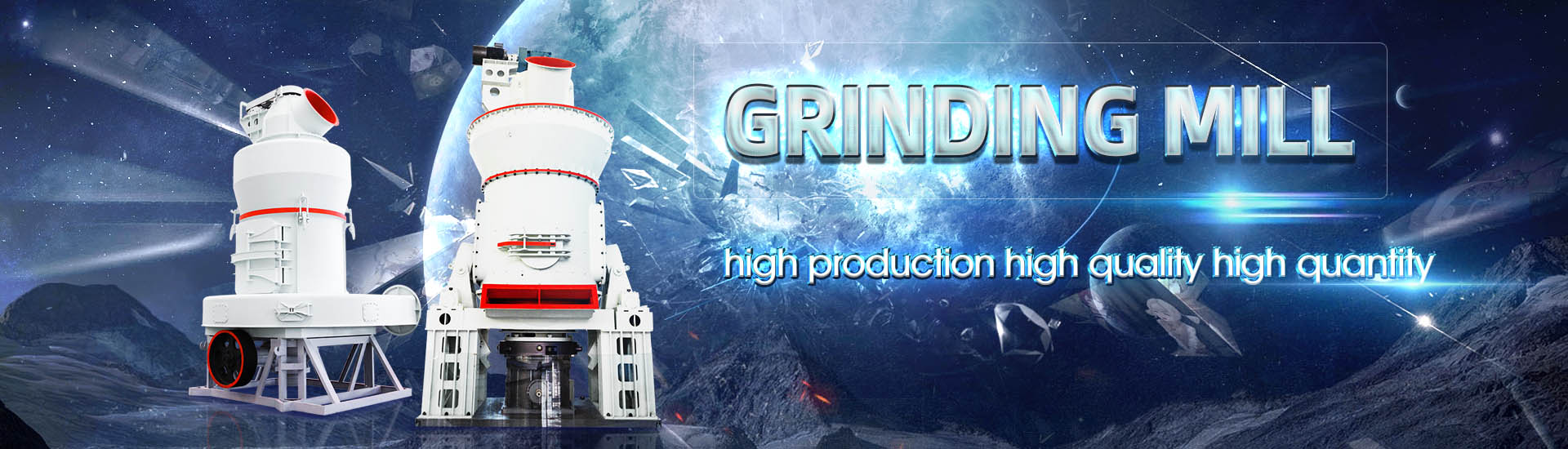
Efficient and energysaving calcite mill
.jpg)
Effective role of grinding aids in the dry grinding performance of calcite
2023年8月1日 Influences of three grinding aids on dry grinding of calcite were investigated The effect of different dosages was examined by changing the grinding time Particle size, energy consumption, and grinding media coating were analyzed Powder flowability and surface area 2018年9月24日 One of the most energyintensive processes for producing submicron range calcite is stirred media mill In the present work, numerous operating parameters such as solid Effect of Operating Parameters on the Breakage Process of Calcite 2022年1月1日 A pilotscale study of highefficiency and energysaving grinding technology using a special stirred mill with the ceramic medium was proposed in this studyHighefficiency and energyconservation grinding technology using 2024年10月13日 Energy Efficiency The calcite grinding mill's innovative process is highly energyefficient, reducing energy consumption by up to 40% compared to traditional grinding Innovative production process of calcite grinding mill
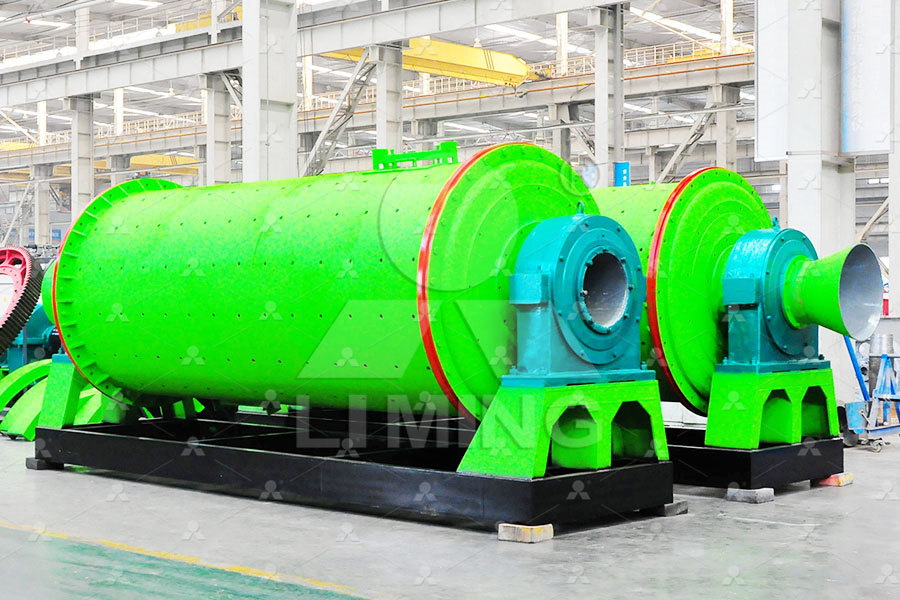
A study on grinding and energy input in stirred media mills
1996年2月1日 One of the most energyintensive processes for producing submicron range calcite is stirred media mill In the present work, numerous operating parameters such as solid 2023年9月14日 In this research, a three‐level Box‐Behnken design was used for the purpose of examining the impact of four independent factors—stirrer speed, grinding time, media filling Optimization of Operating Parameters on Dry Grinding 2020年3月8日 Variance analysis showed a reasonably good value for d50 (R2 = 0965) According to the software solutions, the optimum conditions for minimizing the d50 size were found to be 573 rpm stirrerOptimization of Operating Parameters on Dry 2021年4月21日 For this reason, they suggested that to break particles at an optimum grade (just enough), mills should be operated at a suitable energy level because of the reduction in the The Influence of Stirred Mill Orientation on Calcite Grinding
.jpg)
The Influence of Stirred Mill Orientation on Calcite
2022年8月11日 Manufacturers have improved various stirred mill types which are welladapted to fine and ultrafine grinding applications These stirred mills, which are operated in wet or dry After optimum stress energy levels, temperature in the mill doubles up at the same energy consumption (Figure 4) As a result, the efficiency of grinding is reduced as evidenced byThe Effect of Stirred Mill Orientation on Calcite Grinding2022年5月5日 Calcium carbonate grinding mill is an efficient industrial powder grinder machine (using a fine powder mill or other industrial grinding mills) to directly crush natural calcite, limestone, chalk, shells, etc vertical roller mills Calcium Carbonate Grinding Mill Powder 2023年9月14日 the experiments was compared with the result obtained using the software, a 22% energy saving was achieved The impacts of grinding on the structural characteristics of calcite particles wereOptimization of Operating Parameters on Dry Grinding
.jpg)
The Influence of Stirred Mill Orientation on Calcite Grinding
2021年4月21日 The purpose of this study was to investigate the dry grindability of calcite powders in a vertically and horizontally orientable laboratory batch type stirred mill The experimental results were evaluated using stress intensity analysis The performance was also compared in terms of mill orientation The results showed that the d50 values decreased with High quality Calcium Carbonate Powder Vertical Roller Mill Energy Saving Barite Calcite Grinding Mill from China, China's leading Calcite Mill product market, With strict quality control Calcite Mill factories, Producing high quality Calcium Carbonate Powder Vertical Roller Mill Energy Saving Barite Calcite Grinding Mill productsCalcite Mill, Calcium Carbonate Powder Vertical Roller Mill Energy 2022年1月1日 A pilotscale grinding technology of ceramic medium stirred mill was proposed in this study Based on the specific productivity and grinding efficiency, the appropriate grinding parameters were ascertained as follows: material ball ratio of 07, ceramic ball medium size ratio (10 mm: 15 mm: 20 mm = 3:2:5), stirring speed of 110 rpm, grinding concentration of 50%, Highefficiency and energyconservation grinding technology using 2024年9月14日 The calcium carbonate ball mill plant has the lowest energy consumption and the best particle size distribution, which is most suitable for market demand The ultrafine calcium carbonate ball mill plant is a new energysaving and efficient grinding production line that combines the selfdividing flow micropowder classification technology Calcium Carbonate Ball Mill Plant DASWELL
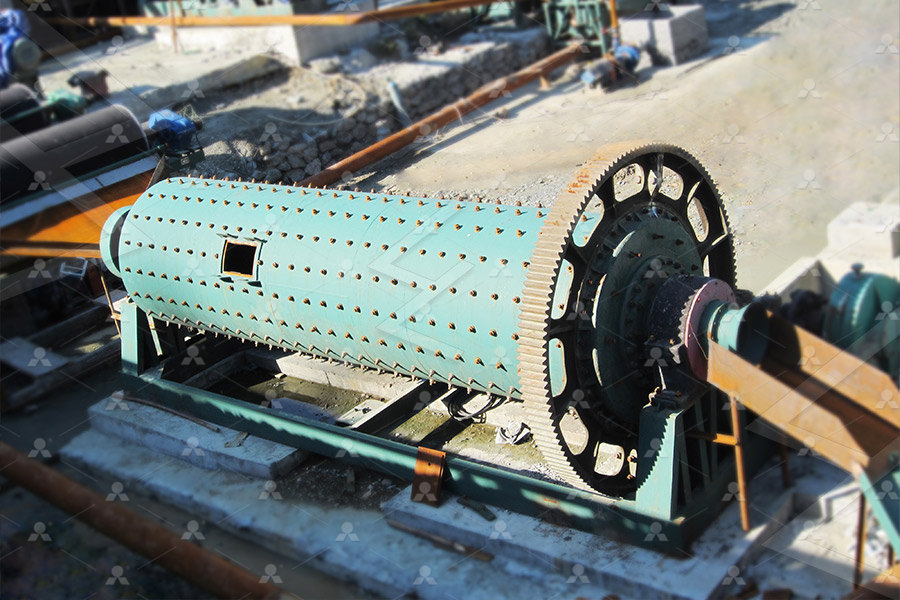
The efficiency of grinding aids in the production of a bio
2023年11月10日 Various studies have been carried out to increase grinding and energy efficiency by adding appropriate chemicals in a HepAc provided energy savings in comparison with other grinding aids Effect of grinding aids on the grinding energy consumed during grinding of calcite in a stirred ball mill Miner Eng, 23 (1) (2010), pp 5457 View HLM vertical grinding mill and vertical roller mill is a highefficiency energysaving advanced pulverizing equipment integrating drying, pulverizing, grading and conveying, which has been researched and developed by Guilin Hongcheng Company for more than 20 years Hongcheng HLM vertical grinding mill has the advantages of high grinding efficiency, low power HLM Vertical Grinding Mill Vertical Roller Mill hcmillsThe HC series vertical pendulum mill is an upgraded pendulum roller mill based on the Raymond mill The technical indicators of this product have been greatly improved compared with the Rtype mill It is a new type of highefficiency and energysaving pendulum roller grinding mill product The fineness of the finished product can be arbitrarily adjusted between 22180μm (80600 HC Series Vertical Pendulum Mill2024年11月1日 Ceramic grinding, which in this paper is defined as a method of using ceramic materials as grinding media, is favored by many processing plants as an emerging highefficiency and energysaving Understanding the EnergySaving mechanism of ceramic
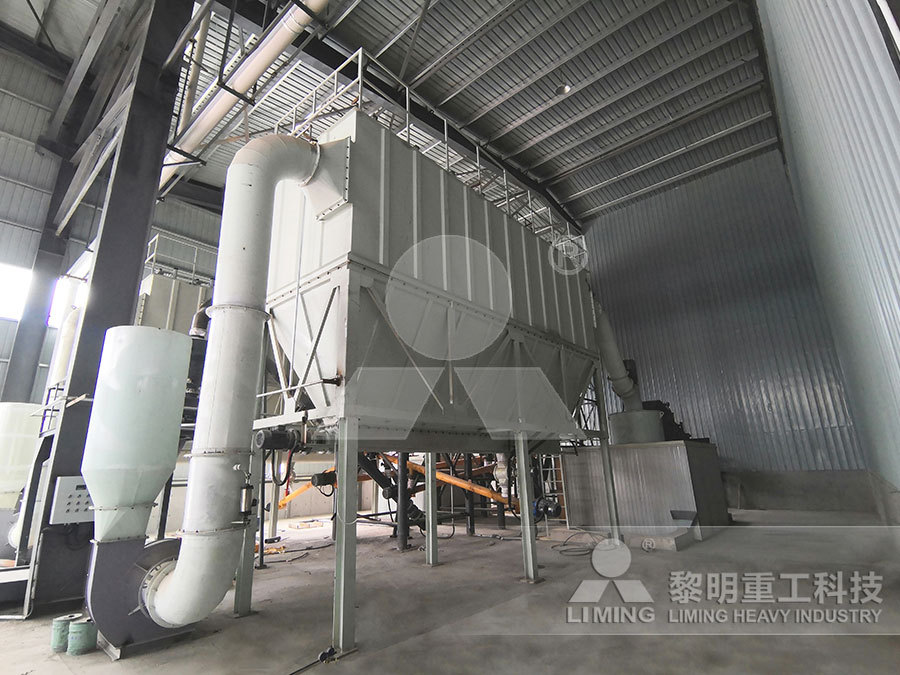
How Does a Raymond Mill Work? Zenith Crusher
2021年10月19日 As one of the key grinding equipment, in order to meet different requirements of various industries, high reliable performance, energy saving and automatic is the inexorable development trend of Raymond mill Energy Saving And Environmental Protection Recent years, people pay more and more attention to environment protection2013年12月18日 Fine grinding, to P80 sizes as low as 7 μm, is becoming increasingly important as mines treat ores with smaller liberation sizes This grinding is typically done using stirred mills such as the Isamill or Stirred Energy Use of Fine Grinding in Mineral Processing2024年9月22日 Features of the Specialist UltraFine Grinding Mill for Calcite 1 High Efficiency Grinding Its high efficiency, customizable particle size, energysaving capabilities, environmental protection measures, ease of maintenance, and wide application range make it an ideal choice for industries requiring ultrafine calcite powder As the demand The specialist ultrafine grinding mill for calcite processing2021年10月1日 As illustrated, some of the grinding results of stirred mill consumed more energy than the ball milling This was the case when coarser bead size was used (25 mm and 4 mm) For p80s of 110 µm and 36 µm, the use of smaller sized beads had brought energy saving of 76% and 26% respectivelyEffects of impact and attrition mechanisms on size
.jpg)
Effect of grinding aids on the grinding energy consumed
DOI: 101016/JMINENG200909011 Corpus ID: ; Effect of grinding aids on the grinding energy consumed during grinding of calcite in a stirred ball mill @article{Choi2010EffectOG, title={Effect of grinding aids on the grinding energy consumed during grinding of calcite in a stirred ball mill}, author={H I Choi and W Lee and D Kim and 2021年5月1日 The rapid growth of the palm oil mill as the primary product dominating Malaysian agriculture industries leads to the increasing of energy usage However, the efficiency of electrical energy usage Improving Energy Efficiency at Palm Oil Mill Industries2022年2月28日 One of the most important advantages of HPGR is its ability to save energy Using HPGR instead of conventional tumbling mills can reduce energy consumption by around 10–50% [85, 88] An investigation conducted on magnetite ore grinding with a dry HPGR machine to reduce the particle size from 50 mm to 90 µm has revealed that using two stages Grinding SpringerLinkal, 2000) However, operating parameters are critical indicators influencing the performance (energy efficiency, fineness, surface area, capacity, fluidity, etc) of a ball mill 752 Physicochem Probl Miner Process, 54(3), 2018, 751762 Test conditions for dry grinding of calcite Mill speed tests Parameters Variable Mill Speed (% of Nc Influences of operating parameters on dry ball mill
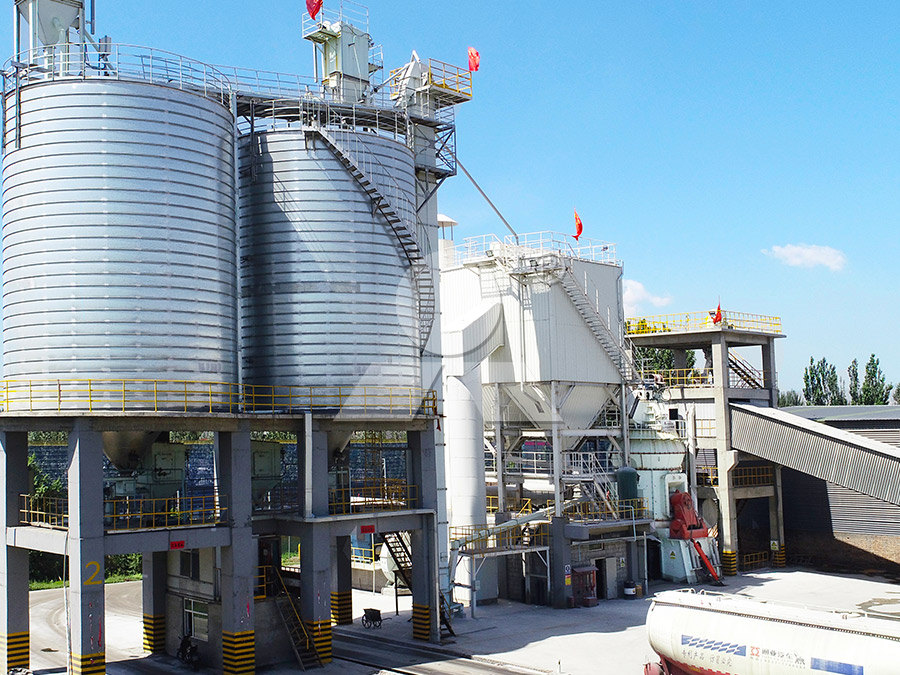
MTM Series Medium Speed Trapezium Mill zenithmills
MTM trapezium mill is a new type of industrial mill designed on the basis of Raymond mill, creating a new mark post in the grinding mill industry The MTM Medium Speed Trapezium Mill is the world's leading industrial mill Feed particle size: 0 2024年10月13日 One of the key advantages of the MTW grinding mill is its energysaving design The mill uses a vertical structure, which reduces the size and weight of the equipment, leading to lower energy consumption The optimized design of the grinding chamber and the use of highquality wearresistant materials further enhance the mill's energy Environmental friendly energysaving MTW europeantype grinding mill 2009年7月1日 The aim of this study is to evaluate the effect that the size of grinding media exerts on ferronickel slag milling efficiency and energy savings A series of tests were performed in a laboratory Effect of grinding aids on the kinetics of fine grinding energy 2017年1月1日 A dry operated, horizontal stirred media mill was used for the fine grinding of limestone and compared in open and closed circuit modes It was found that the choice of grinding aids as well as The Effect of Stirred Mill Orientation on Calcite
FYEFEPS2HDZ49G5Z0[B.jpg)
Optimization of Operating Parameters on Dry
2020年3月8日 The optimization of the operating parameters of a stirred media mill in the dry grinding of calcite was investigated A threelevel BoxBehnken design was used for the purpose of examining the 2023年8月1日 Energy consumption was measured during dry grinding with the objective of evaluating grinding efficiency The energy consumed by the mill was measured by a voltomatmeter called Rev 2580 (Rev Ritter GmBH, Deutschland) It is clearly observed from Fig 2a that approximately 40 kWh/t of energy saving was achieved in the dry grinding test Effective role of grinding aids in the dry grinding performance of calcite2021年4月1日 The most energy efficient operating conditions in terms of mill speed and media size were typically somewhat below the standard operating conditions and it is expected that this is most probably The Influence of Stirred Mill Orientation on Calcite Grinding2002年11月1日 Comminution efficiency is a technical term that relates some measure of the output from a comminution machine to the energy input into it The term has usually been encompassed in controversial The energy efficiency of ball milling in comminution
.jpg)
Energy efficiency challenges in pulp and paper
Readers of this article are urged to also study articles about energy audits at pulp and paper mills (Sweet 1991; Kong et al 2016; Reese 2018; Reese and Deodar 2018; Gilbreath 2019; Reese et al 2020) The largest and quickest savings in energy in pulp and paper mills usually are achieved as a result of system auditsBrief Introduction HGM Ultra fine grinding mill (also called micro powder mill, superfine powder grinding mill, ultra fine powder grinder) is designed by SBM RD department on the basis of multiple innovations and testing It has been proved by thousands of customers that our ultra fine powder grinder has outstanding features, stable quality, easy operation, and maintenanceUltra Fine Grinding Mill SBM Ultrafine Powder Technology2022年8月11日 The Influence of Stirred Mill Orientation on Calcite Grinding Serkan Cayirli1 Hasan Serkan Gokcen2 Received: 28 September 2020/Accepted: 7 April 2021 were in the range of 001–01*10−3 Nm at 1000 kJ/kg energy consumption for all mill volumes In addition, stress intensity analysis in a range of 003–20*10−3 Nm for 20 kWh/t was The Influence of Stirred Mill Orientation on Calcite 2022年5月5日 Calcium carbonate grinding mill is an efficient industrial powder grinder machine (using a fine powder mill or other industrial grinding mills) to directly crush natural calcite, limestone, chalk, shells, etc vertical roller mills Calcium Carbonate Grinding Mill Powder
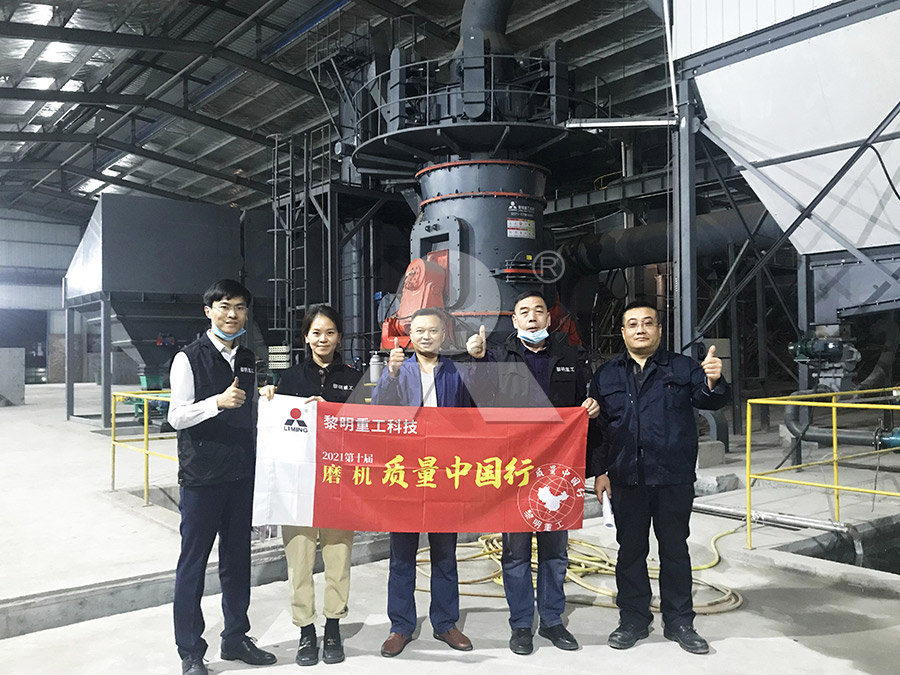
Optimization of Operating Parameters on Dry Grinding
2023年9月14日 the experiments was compared with the result obtained using the software, a 22% energy saving was achieved The impacts of grinding on the structural characteristics of calcite particles were2021年4月21日 The purpose of this study was to investigate the dry grindability of calcite powders in a vertically and horizontally orientable laboratory batch type stirred mill The experimental results were evaluated using stress intensity analysis The performance was also compared in terms of mill orientation The results showed that the d50 values decreased with The Influence of Stirred Mill Orientation on Calcite GrindingHigh quality Calcium Carbonate Powder Vertical Roller Mill Energy Saving Barite Calcite Grinding Mill from China, China's leading Calcite Mill product market, With strict quality control Calcite Mill factories, Producing high quality Calcium Carbonate Powder Vertical Roller Mill Energy Saving Barite Calcite Grinding Mill productsCalcite Mill, Calcium Carbonate Powder Vertical Roller Mill Energy 2022年1月1日 A pilotscale grinding technology of ceramic medium stirred mill was proposed in this study Based on the specific productivity and grinding efficiency, the appropriate grinding parameters were ascertained as follows: material ball ratio of 07, ceramic ball medium size ratio (10 mm: 15 mm: 20 mm = 3:2:5), stirring speed of 110 rpm, grinding concentration of 50%, Highefficiency and energyconservation grinding technology using
.jpg)
Calcium Carbonate Ball Mill Plant DASWELL
2024年9月14日 The calcium carbonate ball mill plant has the lowest energy consumption and the best particle size distribution, which is most suitable for market demand The ultrafine calcium carbonate ball mill plant is a new energysaving and efficient grinding production line that combines the selfdividing flow micropowder classification technology 2023年11月10日 Various studies have been carried out to increase grinding and energy efficiency by adding appropriate chemicals in a HepAc provided energy savings in comparison with other grinding aids Effect of grinding aids on the grinding energy consumed during grinding of calcite in a stirred ball mill Miner Eng, 23 (1) (2010), pp 5457 View The efficiency of grinding aids in the production of a bio HLM vertical grinding mill and vertical roller mill is a highefficiency energysaving advanced pulverizing equipment integrating drying, pulverizing, grading and conveying, which has been researched and developed by Guilin Hongcheng Company for more than 20 years Hongcheng HLM vertical grinding mill has the advantages of high grinding efficiency, low power HLM Vertical Grinding Mill Vertical Roller Mill hcmillsThe HC series vertical pendulum mill is an upgraded pendulum roller mill based on the Raymond mill The technical indicators of this product have been greatly improved compared with the Rtype mill It is a new type of highefficiency and energysaving pendulum roller grinding mill product The fineness of the finished product can be arbitrarily adjusted between 22180μm (80600 HC Series Vertical Pendulum Mill
.jpg)
Understanding the EnergySaving mechanism of ceramic
2024年11月1日 Ceramic grinding, which in this paper is defined as a method of using ceramic materials as grinding media, is favored by many processing plants as an emerging highefficiency and energysaving