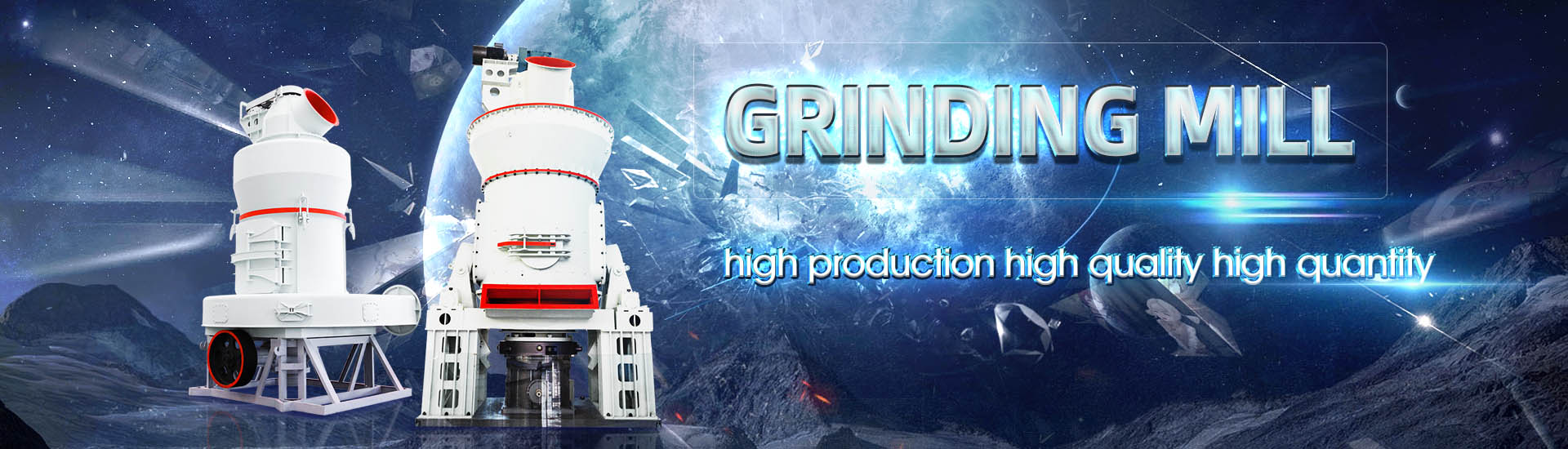
PCF ore mill lining
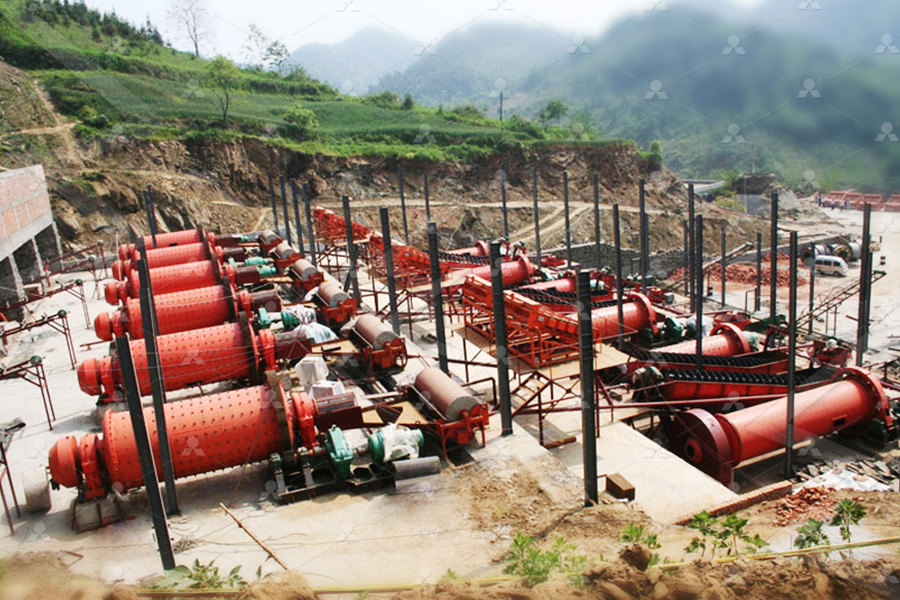
Semiautogenous grinding (SAG) mill liner design and
2024年9月24日 mill is equal to twice the number of the feet in the mill shell diameter (eg, a 34ftdiameter mill shell would have 68 shell lifters) This is also called a 2D shell lining Optimal mill lining solution for your specific mill Promote safety, improve grinding efficiency, reduce downtime and enhance profitability Metallic, PolyMet™, Megaliner™, Rubber and Orebed™ mill liners for all mill typesMill liners Metso2021年8月13日 • For competent ore = low throughput (high SAG mill load) – Design objective = achieve higher operable speed range – Requires higher operable speed range to maintain loadSAG Mill Liner Selection to Maximise Productivity2024年9月24日 Mill linings, Weir Rubber Engineering, Salt Lake City, UT 84126, United States of America ABSTRACT Dramatic shortcomings of mill liner designs, especially of large SAG The Selection and Design of Mill Liners 911 Metallurgist
.jpg)
Mill lining solutions for horizontal Metso
2021年8月11日 Orebed mill linings The Orebed™ magnetic lining system consists of a series of powerful permanent magnets embedded within a matrix of highly abrasionresistant rubber Orebed is a mill liner with totally unique properties If you have a Vertimill or a pebble mill with magnetic ore, Orebed is the superior solution for you offered only by Metso Selecting Orebed, you can count on a longlasting liner that needs Orebed™ mill liners MetsoLargediameter autogenous and semiautogenous grinding mills represent the primary thrust of the expanding grinding technology In spite of initial difficulties, large autogenous and Semiautogenous mill liners: Designs, alloys, and maintenance procedures 2022年11月4日 Vulco® mill linings are customdesigned for each grinding application with consideration given to available mill power, trunnion bearing loads, mill weight restrictions, Minerals Weir Group
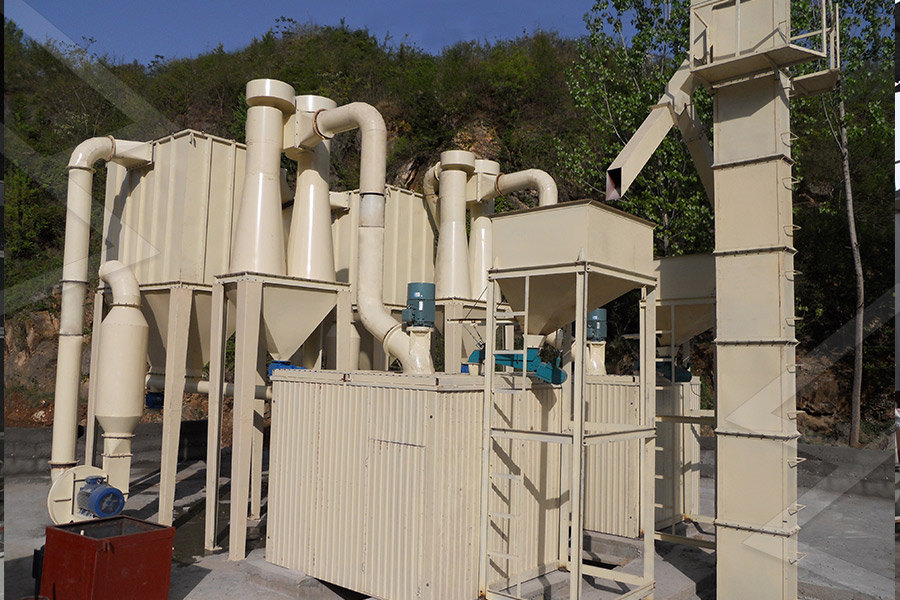
Key considerations when selecting a mill lining
2020年1月27日 A mill lining system serves two purposes: to protect the mill shell from wear caused by the impact and abrasion of the mill charge, and to elevate and tumble the mill contents in the necessary manner to create a grinding 2016年6月6日 Based on experience, millliner designs have moved toward more openshell lifter spacing, increased pulp lifter volumetric capacity, and a grate design to facilitate maximizing both pebblecrushing circuit utilization and SAG SAG Mill Liner Design 911MetallurgistBGF Rubber conducts a full range of works on reequipment of ore grinding mills and their transfer to rubber lining Based on the model of mining and processing equipment, the design, putting into production, joint tests of lining with the Rubber Lining for Ore Grinding Mills and Mining Mill Lining Discover Element's solutions in mill wear protection crafted for various grinding equipment: from AG to MCM Element develops mill lining from a wide array of materials and creates comprehensive design and production Mill Lining Element Mining and Construction Oy
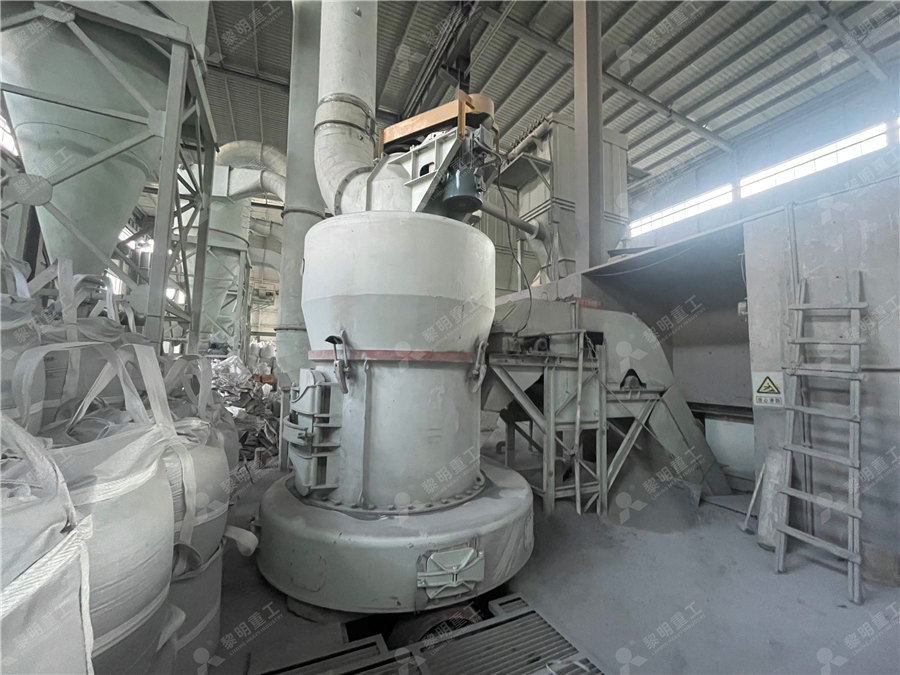
Rubber Mill Liner – Andes Mining
The Andes Mining® rubber lining system is the preferred lining system for secondary ball mills, regrind mills and scrubbers Andes Mining® utilizes the latest technologies and provides customers with an advanced Mill Liner System that increases mill performance and throughput, cementing our standing as a leading supplier of highquality AG Optimal mill lining solution for your specific mill Promote safety, improve grinding efficiency, reduce downtime and enhance profitability Metallic, PolyMet™, Megaliner™, Rubber and Orebed™ mill liners for all mill types With Metso, you can be sure that your mill lining is always designed according to your targets, ore and Mill liners Metso2006年1月1日 The one of main problem in cement industry is the continouse abrasion in lining plates of cement mill as a result of impact, abrasive and erosion by steel balls grinding media inside cement mill (PDF) Selection and design of mill liners ResearchGate2021年1月11日 inside the mill such as increased load, liner shape, mill speed or friction, that causes the cascading ore and steel (in this case 10% steel was used) to hit the shell more than 30o before the vertical diameter will cause reduced Choosing a SAG Mill to Achieve Design Performance
.jpg)
The study of the lining layer abrasing wear in the semiautogenous
2020年1月1日 The successful application of modelling and simulation in design and optimisation rests heavily on having a model which is lifelike In the case of autogenous (AG) and semiautogenous (SAG) mills 2023年12月13日 Mill lining costs account for up to 5% of the overall cost of mineral processing, which can be significant The MML is a maintenancefree mill lining that reduces downtime dramatically and represents major cost savings for most applications This Nexa case study underscores cost savings, safety and an improved working environmentModernising mill lining Engineer Live2020年11月25日 complete mill lining are available for various types and sizes of overflow and grate discharge mills DATASHEET 11/2020 Version 10 • Ore materials: gold, copper, phospate • Minerals: lime, talc MANUFACTURER Teknikum Oy (Business ID FI),TEKNIKUM® Rubber Mill Linings2024年4月26日 Grinding Mills: Grinding mills, such as ball mills and rod mills, are commonly used for grinding iron ore These mills contain grinding media (steel balls or rods) that tumble and impact the ore, causing it to break into smaller particles The choice of grinding mill depends on factors such as the desired product size, capacity requirements Iron Ore Processing: From Extraction to Manufacturing
.jpg)
Tega DynaWear Rubber Mill Liner Manufacturer
The Tega DynaWear® rubber lining system is the preferred lining system for secondary ball mills, regrind mills and scrubbers DynaWear® rubber mill linings are individually designed for your particular working conditions and goals, with 2021年8月11日 design to maximize mill availability The shell lining has a major influence on grinding efficiency It transforms the mill rotation into charge motion, and both profile and spacing must be selected to suit each specific mill When designing a shell lining, the type of ore, mill size and speed, maintenance schedules, safety,Mill lining solutions for horizontal Metso2023年10月2日 design to maximize mill availability The shell lining has a major influence on grinding efficiency It transforms the mill rotation into charge motion, and both profile and spacing must be selected to suit each specific mill When designing a shell lining, the type of ore, mill size and speed, maintenance schedules, safety,Taking your grinding to the next level Mill lining 2020年1月27日 The design configuration and ongoing optimisation of mill lining systems is extremely influential in the effective grinding of material prior to extraction Numerous factors must be considered when selecting a mill liner design, including required grinding action, mill size as well as ore and grinding media characteristics, among others Key considerations when selecting a mill lining system Weir
.jpg)
Customised Vulco® Mill Lining Systems Weir Weir Group
Depending on your goals and application, we offer a range of premium composite and rubber mill lining solutions for rod, ball, AG and SAG mills Rubber mill lining is predominately used for smaller secondary and tertiary ball milling (regrind), whereas our composite mill liners (made from one or more materials) are used for heavyduty primary and secondary AG / SAG mill lining Suitable for pebble mills (magnetic ore), light duty ball mills and Vertimills™ When buying a mill lining from Metso you get more than just a wear part We always do a prestudy and design the lining based on your conditions and targets Wear and performance monitoring are regularly done to better understand your grinding process and to Orebed™ mill liners MetsoMill Linings provide optimal grinding solutions in major mineral processing plants all over the world DynaWear ® rubber lining system is the preferred lining system for secondary ball mills, regrind mills and scrubbers DynaWear ® is fabricated from rubber and has been specially designed for the mills with a less aggressive application Secondary and Regrind applications Rubber Mill Linings High quality Mining Equipment OMIM 6 天之前 Lithium ore ball mill In the grinding and grading stage of lithium ore, in order to ensure that lithium minerals are fully dissociated from gangue mineral monomers, a closedcircuit grinding and grading process can be used The barrel of the wet grid ball mill can be configured with a manganese steel lining plate or a rubber lining plate Ball Mill Is The Key To Grinding Lithium Ore JXSC Machinery
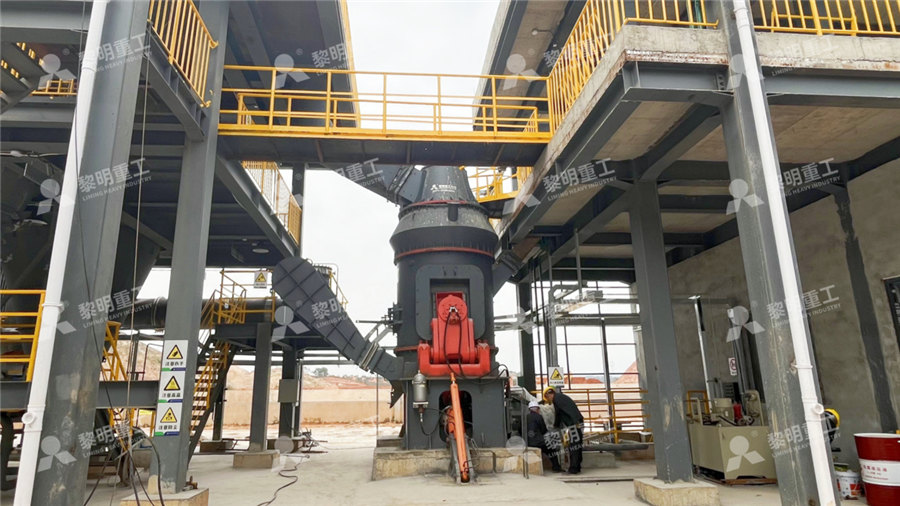
The Selection and Design of Mill Liners 911 Metallurgist
2024年9月24日 The selection of the material of construction is a function of the application, abrasivity of ore, size of mill, corrosion environment, size of balls, mill speed, etc liner design and material of construction are integral and cannot be chosen in isolation A list of the primary material of construction is given, with2023年4月23日 Comminution includes the blasting, crushing, and grinding of ore to liberate valuable mineral particles It consumes most of the energy used in mineral processing plants with grinding using up to (PDF) Grinding Media in Ball MillsA Review ResearchGateThe Mill lining protects the equipment and has a large impact on mill performance Grinding is a tough process, especially when grinding abrasive ores, and the mill liners plays a crutial role Skega Life rubber will give you up Rubber mill liners Pioneering rubber mill Mill liners are an essential component in grinding mills, providing a protective surface to minimize wear and extend the lifespan of the mill In this article, we will explore what mill liners do, their importance, and the different types available Mill liners are protective components that shield the interior of a grinding mill from the abrasive forces generated by grinding media and oreWhat Does Mill Liner Do? ball mills supplier
.jpg)
The advantages of composite mill liners Weir Weir Group
2020年5月28日 Weir Minerals tested this theory at Philsaga Mining Corporation (Philsaga), running a metal cap composite mill lining system against a steel mill lining system under the same process conditions The findings revealed that a properly designed metalcap system can transfer the input energy (motor power) more efficiently for the breakage process Find your ore mill easily amongst the 42 products from the leading brands (Fritsch GmbH, Retsch, Eriez, ) on DirectIndustry, the industry specialist for your professional purchasesOre mill, Ore grinding mill All industrial manufacturers2023年9月11日 Currently commonly used lithium ore ball mills include grate ball mills, overflow ball mills, long barrel ball mills, energysaving ball mills, etc 1 Lithium ore grate ball mill In lithium ore dressing plants, grate ball mills are mainly responsible for grinding coarser minerals and are mostly used in onestage grinding operations Due to Ball Mills for Lithium Ore JXSC Machine2020年10月1日 These include mill power draft calculations, shell lifter design, lifter wear prediction, pulp lifter simulation and ore particle breakage in grinding mills The status of advancement in each of A Review on Current Mill Liner Design and Performance
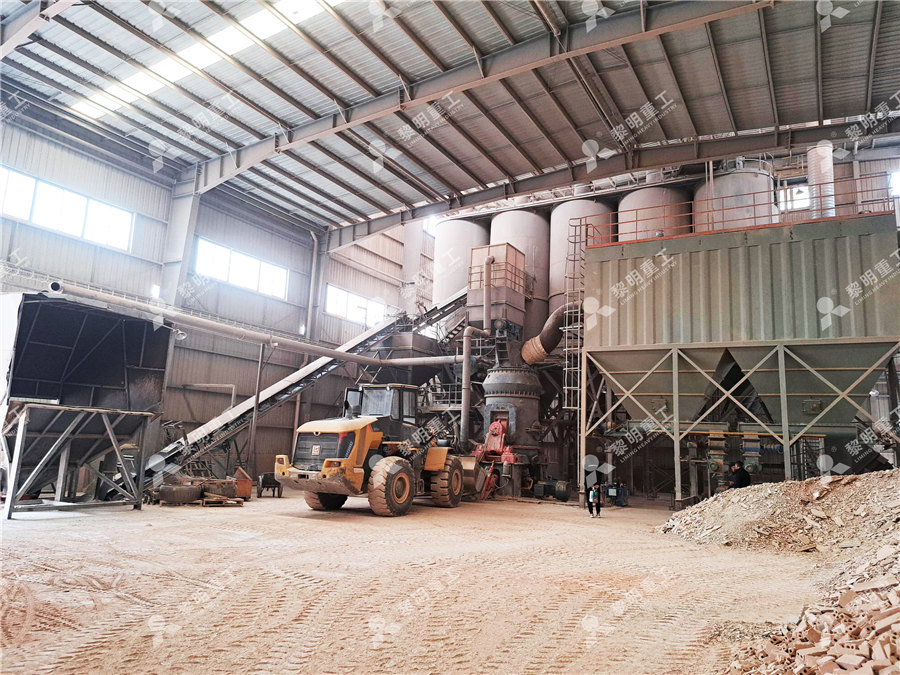
Mining Welcome to AIA Engineering/Vega Industries
The design is based on multiple parameters such as ore quality, feed size, required product, Grinding Media size and media/pulp volume Mining Products and Service (MPS) has over 25 years’ experience in mill lining systems (Liner design, metallurgy, project management, quality control and Optimization) MPS personnel have worked on 2023年10月27日 The ball mill is a rotating cylindrical vessel with grinding media inside, which is responsible for breaking the ore particles Grinding media play an important role in the comminution of mineral A Review of the Grinding Media in Ball Mills for Mineral The mill liner is installed inside the ball mill barrel to protect the inner wall of the barrel from the impact of materials and grinding media (steel balls, steel sylpebs, steel rods, etc) to avoid premature damage to the barrelAs an important part of the ball mill, the mill lining needs to be designed according to the materials to be processed and different grinding typesMill Linings for Sale, Types of Ball Mill Liners ball mills The condition of the backing rubber is critical in achieving optimum performance of the mill lining system We provide specialist tools, materials and expertise to complete work inline with other mill reline activities This reduces downtime and provides tangible efficiencies for our clients by engaging a service provider specialising in the Rubber Lining Relines South Africa

Rubber Lining for Ore Grinding Mills and Mining
BGF Rubber conducts a full range of works on reequipment of ore grinding mills and their transfer to rubber lining Based on the model of mining and processing equipment, the design, putting into production, joint tests of lining with the Mill Lining Discover Element's solutions in mill wear protection crafted for various grinding equipment: from AG to MCM Element develops mill lining from a wide array of materials and creates comprehensive design and production Mill Lining Element Mining and Construction OyThe Andes Mining® rubber lining system is the preferred lining system for secondary ball mills, regrind mills and scrubbers Andes Mining® utilizes the latest technologies and provides customers with an advanced Mill Liner System that increases mill performance and throughput, cementing our standing as a leading supplier of highquality AG Rubber Mill Liner – Andes MiningOptimal mill lining solution for your specific mill Promote safety, improve grinding efficiency, reduce downtime and enhance profitability Metallic, PolyMet™, Megaliner™, Rubber and Orebed™ mill liners for all mill types With Metso, you can be sure that your mill lining is always designed according to your targets, ore and Mill liners Metso
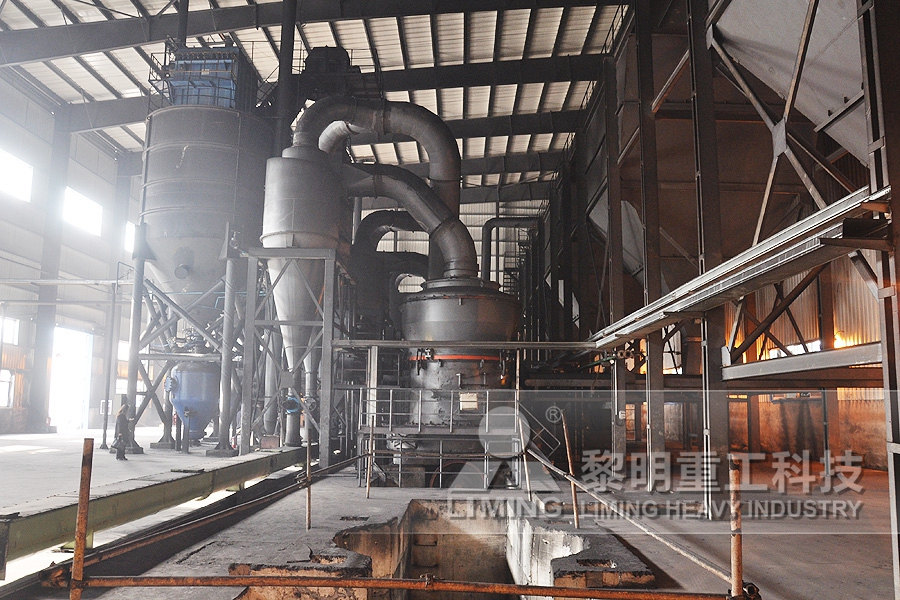
(PDF) Selection and design of mill liners ResearchGate
2006年1月1日 The one of main problem in cement industry is the continouse abrasion in lining plates of cement mill as a result of impact, abrasive and erosion by steel balls grinding media inside cement mill 2021年1月11日 inside the mill such as increased load, liner shape, mill speed or friction, that causes the cascading ore and steel (in this case 10% steel was used) to hit the shell more than 30o before the vertical diameter will cause reduced Choosing a SAG Mill to Achieve Design Performance2020年1月1日 The successful application of modelling and simulation in design and optimisation rests heavily on having a model which is lifelike In the case of autogenous (AG) and semiautogenous (SAG) mills The study of the lining layer abrasing wear in the semiautogenous 2023年12月13日 Mill lining costs account for up to 5% of the overall cost of mineral processing, which can be significant The MML is a maintenancefree mill lining that reduces downtime dramatically and represents major cost savings for most applications This Nexa case study underscores cost savings, safety and an improved working environmentModernising mill lining Engineer Live
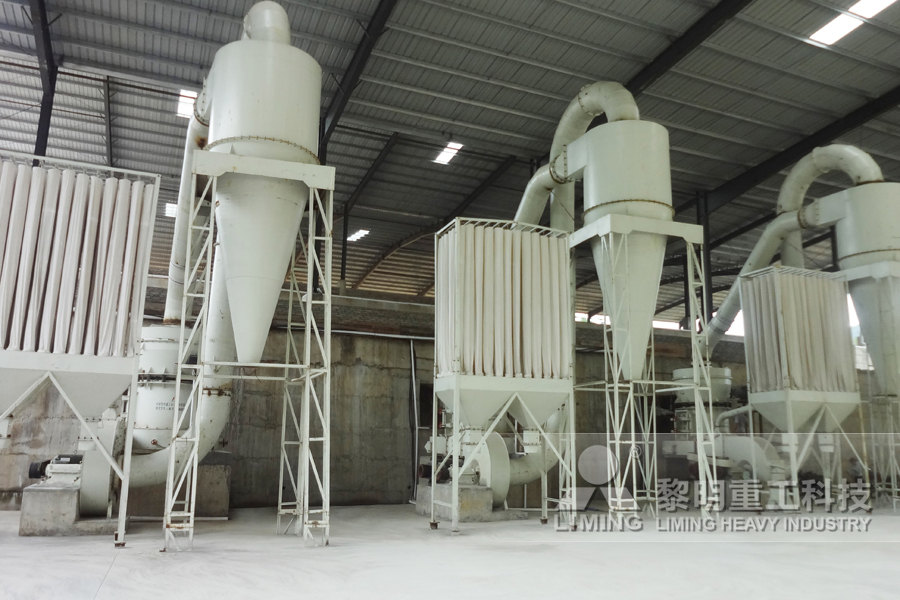
TEKNIKUM® Rubber Mill Linings
2020年11月25日 complete mill lining are available for various types and sizes of overflow and grate discharge mills DATASHEET 11/2020 Version 10 • Ore materials: gold, copper, phospate • Minerals: lime, talc MANUFACTURER Teknikum Oy (Business ID FI),2024年4月26日 Grinding Mills: Grinding mills, such as ball mills and rod mills, are commonly used for grinding iron ore These mills contain grinding media (steel balls or rods) that tumble and impact the ore, causing it to break into smaller particles The choice of grinding mill depends on factors such as the desired product size, capacity requirements Iron Ore Processing: From Extraction to Manufacturing