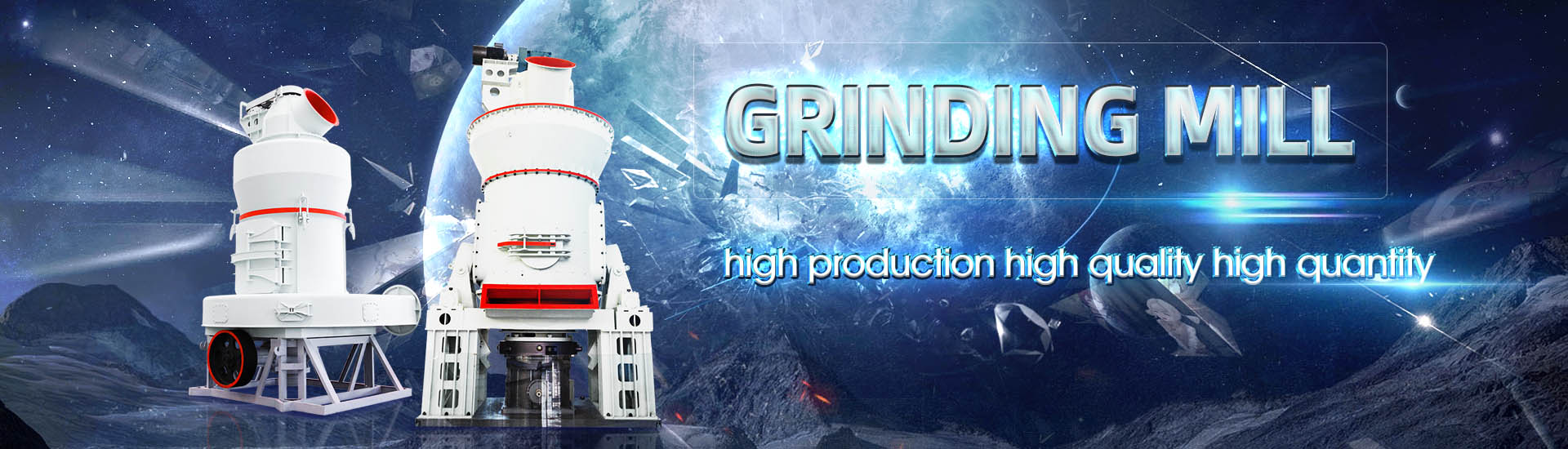
What is the bucket capacity of the ore grinding mill model 220
.jpg)
Small Ball Mill Capacity Sizing Table 911Metallurgist
2016年2月14日 Do you need a quick estimation of a ball mill’s capacity or a simple method to estimate how much can a ball mill of a given size (diameter/lenght) grind for tonnage a product P80 size? Use these 2 tables to get you close2012年6月1日 in modeling and control of the grinding process in industrial ball mills Basic commonly used control strategies are analyzed and discussed Keywords: Ball mills, grinding (PDF) Grinding in Ball Mills: Modeling and Process Control2024年9月24日 ore to ball mill feed In recent years, the trend has been towards largersized SAG mills with diameters of 104 m (34 ft) and above, with the largest being 122 m (40 ft) in Semiautogenous grinding (SAG) mill liner design and 2023年7月20日 (3) Hourly production capacity of the mill, which is the amount of raw ore processed by the mill per unit time under certain conditions of ore feeding and product particle Ore Grinding SpringerLink
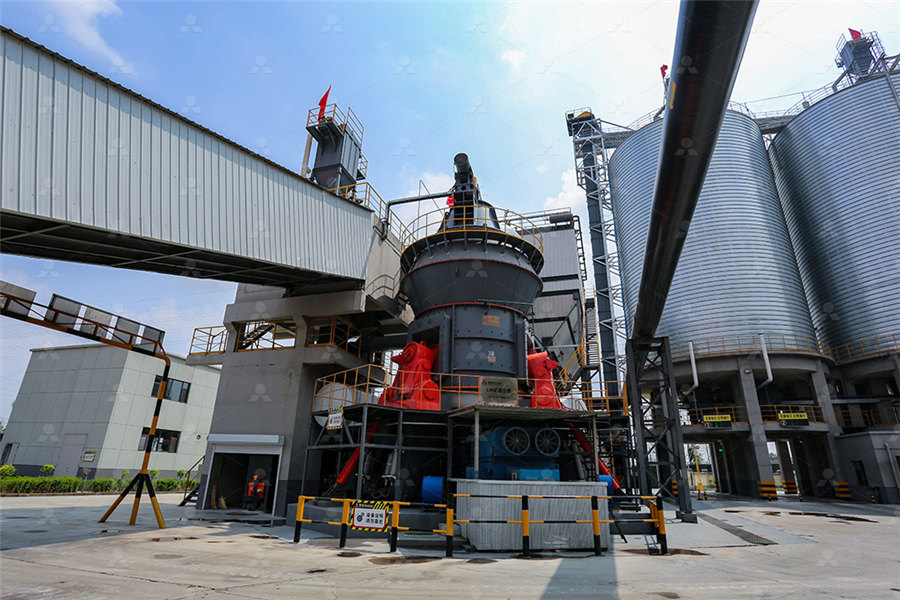
IsaMill™ Glencore Technology
The IsaMill™ is used extensively in base metals, PGM, gold processing and magnetite grinding applications And the power capacity of an IsaMill™ ranges from 75kW to 38mW IsaMill™ is 2023年9月1日 Based on the machine learning method, this study analyzed the full process parameters (ie, ball mill power, fresh ore feed rate, hydrocyclone feed pump power, Analyzing process parameters for industrial grinding circuit 2021年7月1日 The work uses the UFRJ mechanistic mill model and DEM to analyze the effect of several design and operating variables on the apparent breakage rates and breakage Predicting the effect of operating and design variables in grinding The several types of crushers and mills available (Wills and Finch 2015) mainly differ by the stress mecha nism and energy intensity they apply to ore particles, asAll About Particles: Modelling Ore Behaviour in Mineral
.jpg)
Autogenous and SemiAutogenous Mills ScienceDirect
2016年1月1日 Disintegration and size reduction of some ores is possible in tumbling mills without the aid of grinding media Grinding mills in which comminution takes place without These different approaches have one thing in common: they use a single number to describe energy in grinding This number, the specific energy, is the ratio between the power and the A Review of Advanced Ball Mill Modelling JSTAGE2019年8月14日 Reasonable steel ball grading is the key to maximize the grinding capacity of the ball mill, which will have a direct impact on the grinding efficiency, and then affect the ball mill output The ball mill is an indispensable equipment in the beneficiation operation, because it is necessary to grind the ore to a suitable selected particle The Ultimate Guide to Ball Mills MiningpediaBall Mill Grinding Machines: Exploring the Working Principle, Types, Parts, Applications, Advantages, and Recent Developments Ball mill grinding machines are widely used in various industries for the comminution of materials into fine Ball Mill Grinding Machines: Working Principle,

Ball Mill Design/Power Calculation
2015年6月19日 The basic parameters used in ball mill design (power calculations), rod mill or any tumbling mill sizing are; material to be ground, characteristics, Bond Work Index, bulk density, specific density, desired mill 2023年5月23日 The capacity of the grinding mill varies based on the type of product being ground and the fineness required in the final product The capacity also depends on the throughput rate, feed size What is the capacity of the grinding mill? LinkedIn2023年7月31日 operation (1) Structure parameters of grinding mill, including its specifications, model, aspect ratio, ore discharging method, and liner form (2) Various working parameters of grinding mill, including fraction of critical speed for grinding mill, filling rate for grinding mill, grinding concentration,grindingcycleload,etc(3)AndgrindOre Grinding Methods and Process of Ore Grinding2017年3月4日 A simplified model (kinematic diagram) of the mechanism of the double buckling jaw crusher is shown in Fig 20 The mechanism in question is a six membered mechanism formed by attaching a binary (PDF) SIZE REDUCTION BY CRUSHING METHODS
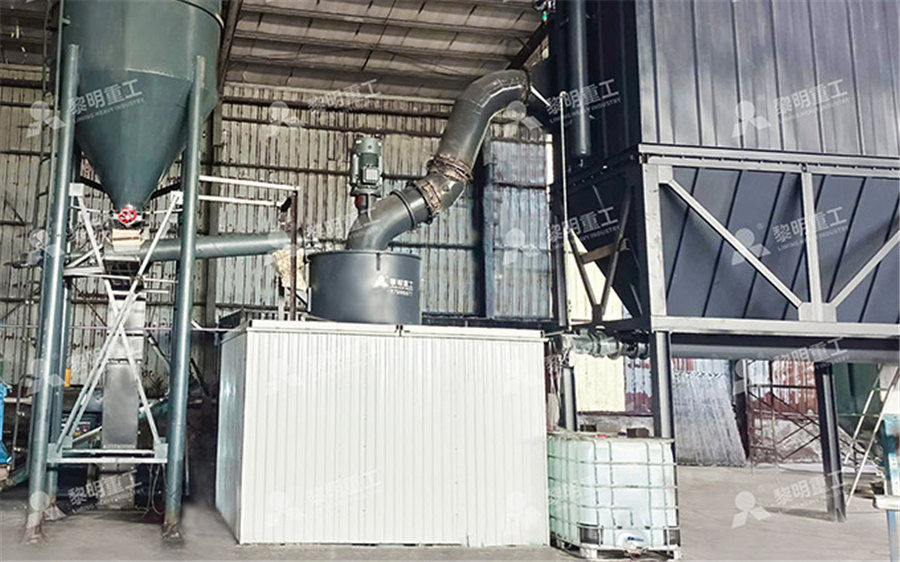
Rod Mills: Efficient Grinding Solutions for Mining
2016年6月1日 Rod Mill Capacity and Sizing Table Rod Mills may be considered either fine crushers or coarse grinding equipment They are capable of taking as large as 2″ feed and making a product as fine as 3548 mesh The type of mill that is used for grinding ore in a modern concentrator is the wet tumbling mill These mills may be divided into 2018年12月24日 The SAG mill model of Leung (1987) is reviewed and tested using the Alcoa survey data According to the desired capacity and the ore communition characteristics observed, a simulation was EVALUATION OF THE ALTERNATIVES FOR GOLD ORE GRINDING 2022年3月15日 The amount of comminution or fineness of minerals in the mill can be described by various parameters, the most important of which is d80 (80% passing size)Power consumption management and simulation of 2017年9月11日 The results of the grinding tests on cement material together with its breakage results obtained from 2 cm and 4 cm diameter beds were used in the model fitting of the mill by using perfect mixing (PDF) Performance Evaluation of Vertical Roller Mill in Cement Grinding
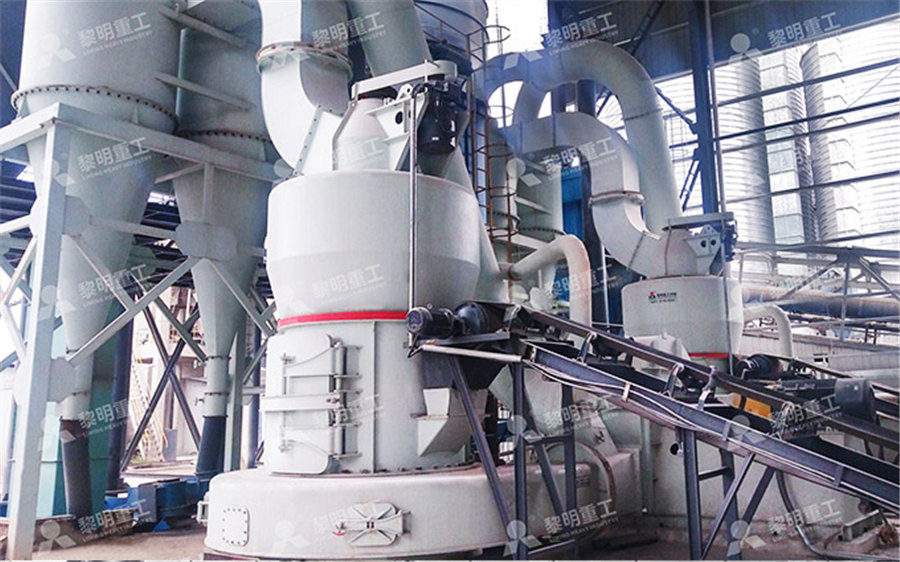
Grinding Mills — Types, Working Principle
2018年8月17日 SemiAutogenous Mills/ SAG Mills (primary grinding mill) — these mills use grinding balls with forces of attrition, impact, and abrasion between grinding balls and ore particles that result in 2024年8月8日 Unlock the secrets to ball mill efficiency with our comprehensive guide on choosing the right grinding media Learn how material composition, size, shape, hardness, and cost impact your milling process and outcomes a Ball Mill Success: A StepbyStep Guide to 2024年10月15日 High costeffectiveness CITIC HIC grinding mills are recognized as China's Manufacturing Industry Single Champion Product CITIC HIC is responsible for setting the national standards of semiautogenous mills Grinding Mills Mineral Processing Equipment2014年1月1日 An analysis of the kinetics of dolomite grinding in a dry ball mill reveals that the following approximations apply for the parameters of the batch grinding model: the size discretized selection Population balance model approach to ball mill optimization in iron ore
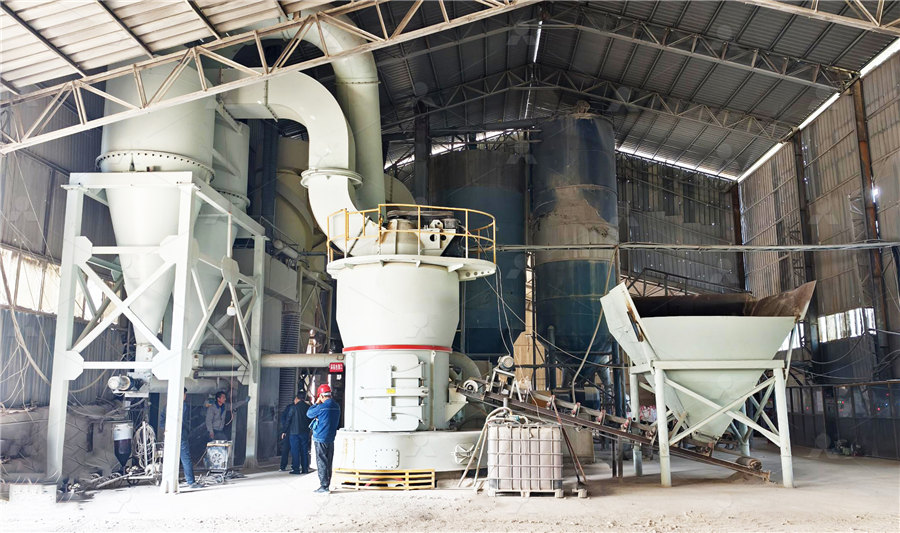
Predicting the effect of operating and design variables in grinding
2021年7月1日 Vertical stirred mills may be classified according to the speed of the stirrer in two groups: gravityinduced or fluidized mills [[1], [2], [3]]In the gravityinduced mills, the stirrer, generally of the screw type, turns so that the grinding charge exhibits an ascending convective motion at the center, descending from the edges of the screw and close to the mill shell, owing 2016年6月6日 Based on experience, millliner designs have moved toward more openshell lifter spacing, increased pulp lifter volumetric capacity, and a grate design to facilitate maximizing both pebblecrushing circuit utilization and SAG mill capacity As a guideline, mill throughput is maximized with shell lifters between ratios of 25:1 and 50:1SAG Mill Grinding Circuit Design 911Metallurgistonline live calculators for grinding calculations, Ball mill, tube mill, critical speed, Degree of filling balls, Arm of gravity, mill net and gross power Optimization Online Trainingball mill calculations, grinding media filling degree, ball size, mill CLUM vertical mills are suitable for largescale and highvolume nonmetallic ore grinding production lines The equipment is controlled intelligently, the work efficiency is high, and the ground powder has high whiteness and good shapeSBM Ore Ultrafine Grinding Mill
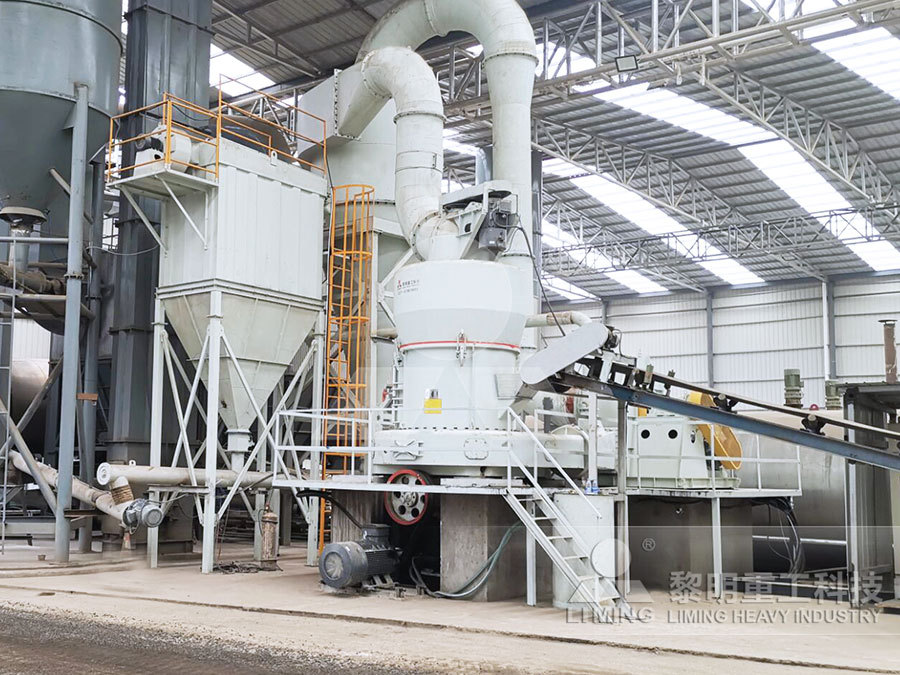
Fine grinding: How mill type affects particle shape characteristics
2017年9月1日 The first stirred mill was installed in the platinum industry in 2002, and by the year 2010, forty stirred mills had been installed at various platinum operations in South Africa, and these led to a step change in flotation recoveries (Rule, 2011, Rule, 2010)Over the last decade, approximately 200 Automated Scanning Electron Microscopy (AutoSEMEDS) systems have 2021年8月19日 EFFECTS OF MILL ROTATIONAL SPEED ON THE BATCH GRINDING KINETICS OF A UG2 PLATINUM ORE By DINEO MOKGANYETJI MAKGOALE Submitted in accordance with the requirements for the degree of MAGISTER TECHNOLOGIAE in the subject ENGINEERING: CHEMICAL at the UNIVERSITY OF SOUTH AFRICA SUPERVISOR: Prof EFFECTS OF MILL ROTATIONAL SPEED ON THE BATCH 1992年3月1日 Batch grinding parameters a T 063 min −1 γ 080 α 137 Λ 47 β 62 Φ 0 060 δ 01 a T 112 mm Table 2 Average input values for the fullscale mill and their corresponding interval ranges Optimization of the makeup ball charge in a 2023年2月15日 Differences between ball mill and rod mill 1 Different capacity and granularity Ball mill The capacity of ball mills is 065 ~ 615t/h, and the discharge particle size of the ground material is 0074 ~ 04mm Rod mill The What Are the Differences between Ball Mill and
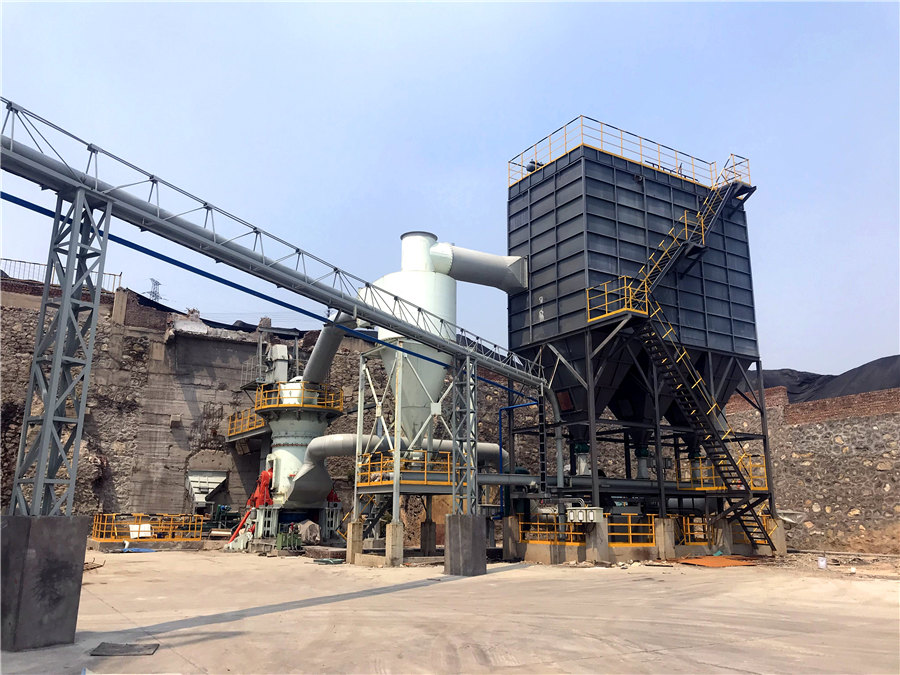
A guide to SAG Mill management Mipac
2024年5月17日 A SAG (SemiAutogenous Grinding) mill is a giant rotating cylinder filled with grinding media and the ore being reduced As the mill rotates, the grinding media lifts and the impact crushes the feed material SAG mill control refers to the practice of managing the mill load, which is the amount of material inside the mill at any given time2018年10月17日 The mill is fed 125 mm grinding balls The ball mill (BALL grinding) is 834 m in diameter and 1326 m in length Its capacity 78206 cubic meters The operating load is 1,272 tons The mill is fed 80mm steel grinding balls The mill grinding performance might be up to 3,100 tons of ore per hour The grinding balls charged to these mills are GRINDING MILLS CHAMPIONS World's biggest Grinding mills2016年11月7日 In Fig 13 is shown a large ball mill, designed for the dry grinding of limestone, dolomite, quartz, refractory and similar materials; this type of mill being made in a series of sizes having diameters ranging from about 26 in to 108 in, with the corresponding lengths of drum ranging from about 15 in to 55 inGrinding Mills Common Types 911Metallurgist2023年10月17日 3 Ultrafine Powder Grinding Mill Ultrafine powder mill (threering / fourring mediumspeed micropowder mill) feed particle size ≤25 mm, production capacity 0545 t/h, production fineness 1503500 mesh,it is a highefficiency and lowconsumption ultrafine powder processing equipment that successfully replaces the traditional jet mill and complex process How to choose a suitable ore powder grinding mill?
.jpg)
(PDF) Grinding Media in Ball MillsA Review ResearchGate
2023年4月23日 grinding media in a grinding mill with about 2630 wt% chrome by Chen et al [37] using a phosphate ore in a modified ball laboratory ball mill whose electrochemical potential could be controlledBrief Introduction HGM Ultra fine grinding mill (also called micro powder mill, superfine powder grinding mill, ultra fine powder grinder) is designed by SBM RD department on the basis of multiple innovations and testing It has been proved by thousands of customers that our ultra fine powder grinder has outstanding features, stable quality, easy operation, and maintenanceUltra Fine Grinding Mill SBM Ultrafine Powder Technology2018年11月5日 HGM80 Ultra Fine Grinder mill is mainly applied to noninflammable, nonexplosive and brittle materials with Mohs hardness under six Such as calcite (calcite carbonate, calcium carbonate), chalk, limestone, dolomite, kaolin, gypsum, etc, HGM80 Ultra Fine Grinder millgrinding mill/ultrafine millA hybrid nonlinear model predictive controller (HNMPC) is developed for a runofmine ore grinding mill circuit A continuoustime grinding mill circuit model is presented with a hydrocyclone Relationship between SAG mill power draw, bearing pressure
.jpg)
The Ultimate Guide to Ball Mills Miningpedia
2019年8月14日 Reasonable steel ball grading is the key to maximize the grinding capacity of the ball mill, which will have a direct impact on the grinding efficiency, and then affect the ball mill output The ball mill is an indispensable equipment in the beneficiation operation, because it is necessary to grind the ore to a suitable selected particle Ball Mill Grinding Machines: Exploring the Working Principle, Types, Parts, Applications, Advantages, and Recent Developments Ball mill grinding machines are widely used in various industries for the comminution of materials into fine Ball Mill Grinding Machines: Working Principle, 2015年6月19日 The basic parameters used in ball mill design (power calculations), rod mill or any tumbling mill sizing are; material to be ground, characteristics, Bond Work Index, bulk density, specific density, desired mill Ball Mill Design/Power Calculation2023年5月23日 The capacity of the grinding mill varies based on the type of product being ground and the fineness required in the final product The capacity also depends on the throughput rate, feed size What is the capacity of the grinding mill? LinkedIn
.jpg)
Ore Grinding Methods and Process of Ore Grinding
2023年7月31日 operation (1) Structure parameters of grinding mill, including its specifications, model, aspect ratio, ore discharging method, and liner form (2) Various working parameters of grinding mill, including fraction of critical speed for grinding mill, filling rate for grinding mill, grinding concentration,grindingcycleload,etc(3)Andgrind2017年3月4日 A simplified model (kinematic diagram) of the mechanism of the double buckling jaw crusher is shown in Fig 20 The mechanism in question is a six membered mechanism formed by attaching a binary (PDF) SIZE REDUCTION BY CRUSHING METHODS2016年6月1日 Rod Mill Capacity and Sizing Table Rod Mills may be considered either fine crushers or coarse grinding equipment They are capable of taking as large as 2″ feed and making a product as fine as 3548 mesh The type of mill that is used for grinding ore in a modern concentrator is the wet tumbling mill These mills may be divided into Rod Mills: Efficient Grinding Solutions for Mining2018年12月24日 The SAG mill model of Leung (1987) is reviewed and tested using the Alcoa survey data According to the desired capacity and the ore communition characteristics observed, a simulation was EVALUATION OF THE ALTERNATIVES FOR GOLD ORE GRINDING
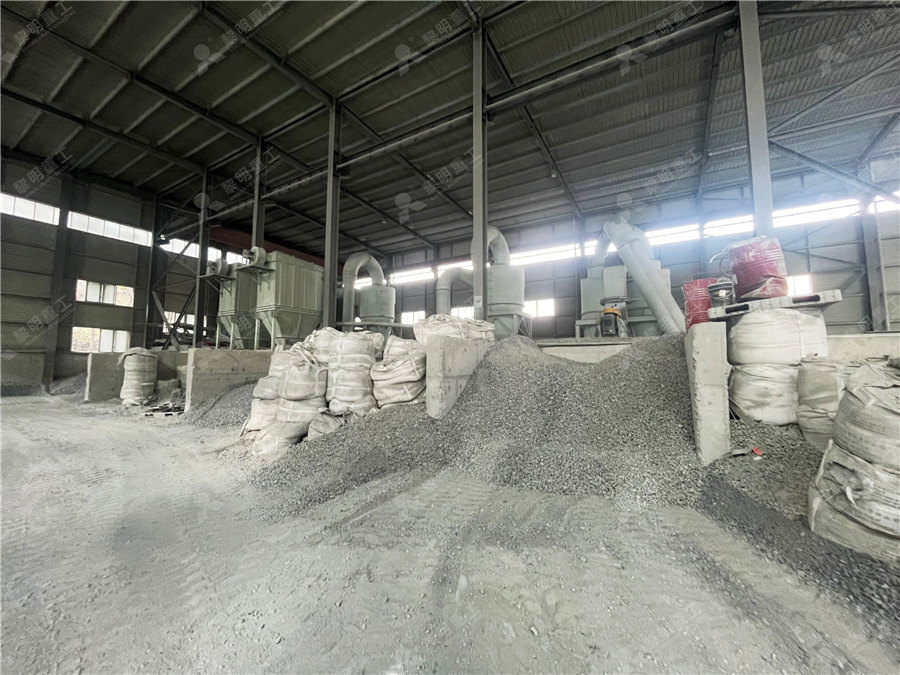
Power consumption management and simulation of
2022年3月15日 The amount of comminution or fineness of minerals in the mill can be described by various parameters, the most important of which is d80 (80% passing size)2017年9月11日 The results of the grinding tests on cement material together with its breakage results obtained from 2 cm and 4 cm diameter beds were used in the model fitting of the mill by using perfect mixing (PDF) Performance Evaluation of Vertical Roller Mill in Cement Grinding