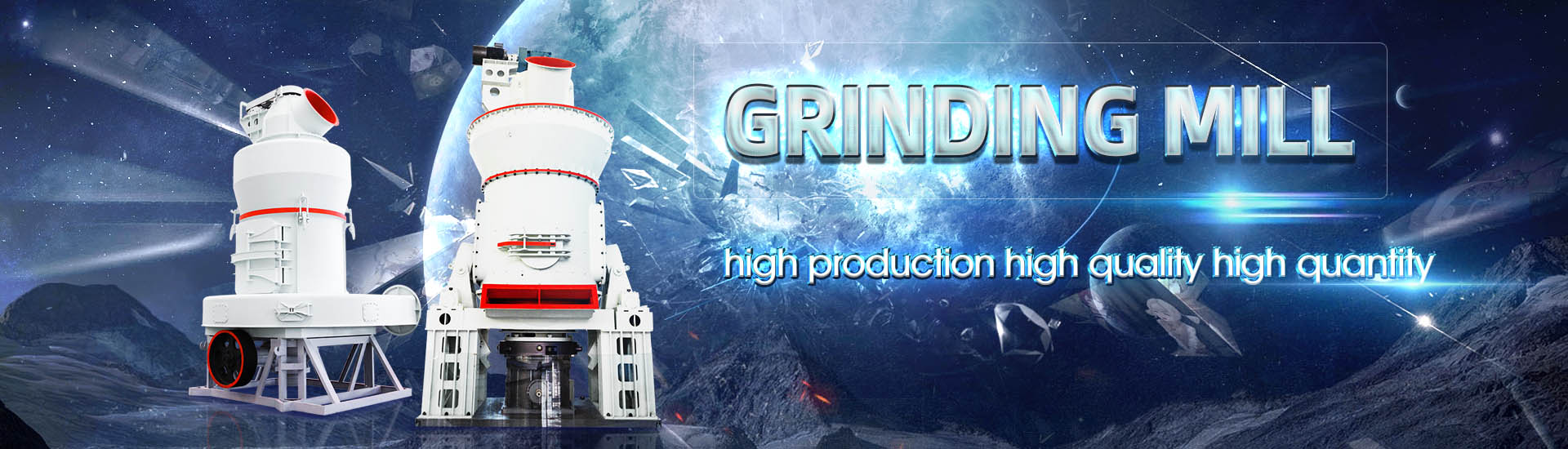
Refractory material powder making process

Processing of Refractory Metals: Melting and Powder
2024年11月18日 Powder metallurgy is a widely used method for processing refractory metals, offering several advantages over melting It involves compacting metal powders into a desired 2024年6月1日 This article introduces to various techniques for fabricating prealloyed refractory highentropy powders and their densification Additionally, it reviews the methods for Refractory highentropy alloys fabricated by powder 2021年9月21日 Manufacturing components from refractory metals presents great challenges due to their high melting temperature and low ductility Until now, powder metallurgy followed Latest Developments in Manufacturing and Recycling of Refractory Materials2024年4月5日 Refractory materials are both economically and socially strategic materials as they enable the production of other crucial products, including steel, nonferrous metals, Design, Manufacturing and Properties of Refractory Materials
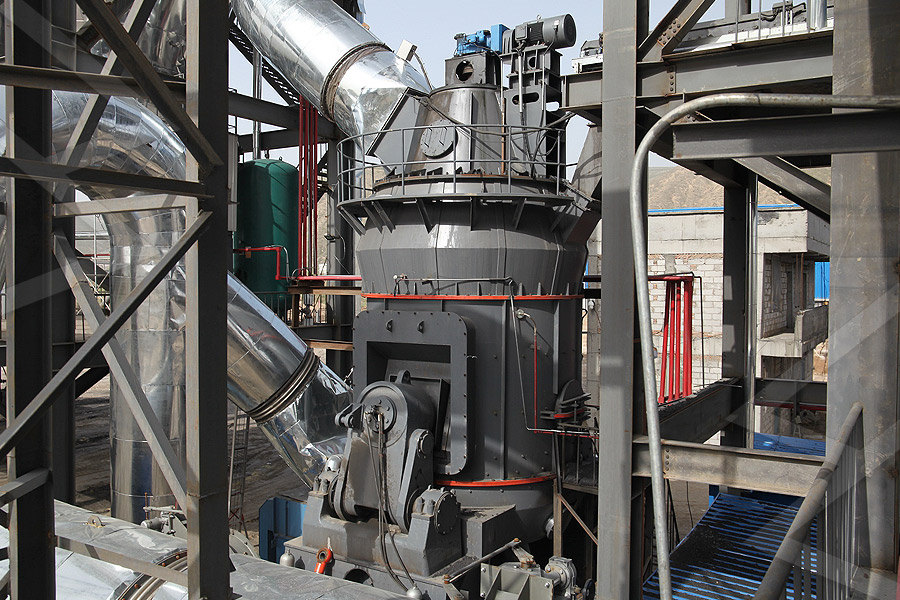
Manufacturing and Properties of Refractories SpringerLink
2020年11月29日 This chapter discusses the general manufacturing processes and properties of different types of refractories The process flow sheets of the manufacturing of all major types 2015年9月10日 Refractory manufacturing involves four processes: raw material processing, forming, firing, and final processing Figure 1151 illustrates the refractory manufacturing 115 Refractory Manufacturing US EPA2021年10月28日 In this contribution, powders made of Mo20Si528Ti (at%) were produced by a novel ultrasonic atomization (UA) process at laboratoryscale using an industrial electrode induction gas atomization (EIGA) process with a Flexible Powder Production for Additive 1993年10月24日 For the past century the processing of refractory metals and alloys has been linked to powder metallurgy (P/M) A firm understanding of processing has been critical to Powder Processing of Refractory Metals and Alloys
.jpg)
Additive manufacturing of defectfree TiZrNbTa refractory
2024年2月16日 Here, we present a method based on a normalized modelbased processing diagram to achieve a nearly defectfree TiZrNbTa alloy via insitu alloying of elemental 2018年3月27日 The material used in this research is a mixture of evaporation boats waste powder, kaolin, and graphite, with a composition of 50%, 25% and 25%, respectively During the mixing process, 15% of (PDF) Review of Refractory Materials for 2023年6月22日 Silica‐Based Refractories for Iron and Steel Melting Silica‐based refractories have long been the standard for foundries using coreless furnaces to melt iron and iron alloys Traditional lining materials include a high purity silica aggregate with a boron‐ based, heatset binder, generally in the form of either boron oxide or boric acidInnovative Refractory Technology for Coreless Induction 2021年9月21日 Manufacturing components from refractory metals presents great challenges due to their high melting temperature and low ductility Until now, powder metallurgy followed by thermomechanical process has been the only viable route for producing bulk refractory materials on an industrial scaleLatest Developments in Manufacturing and Recycling of Refractory Materials
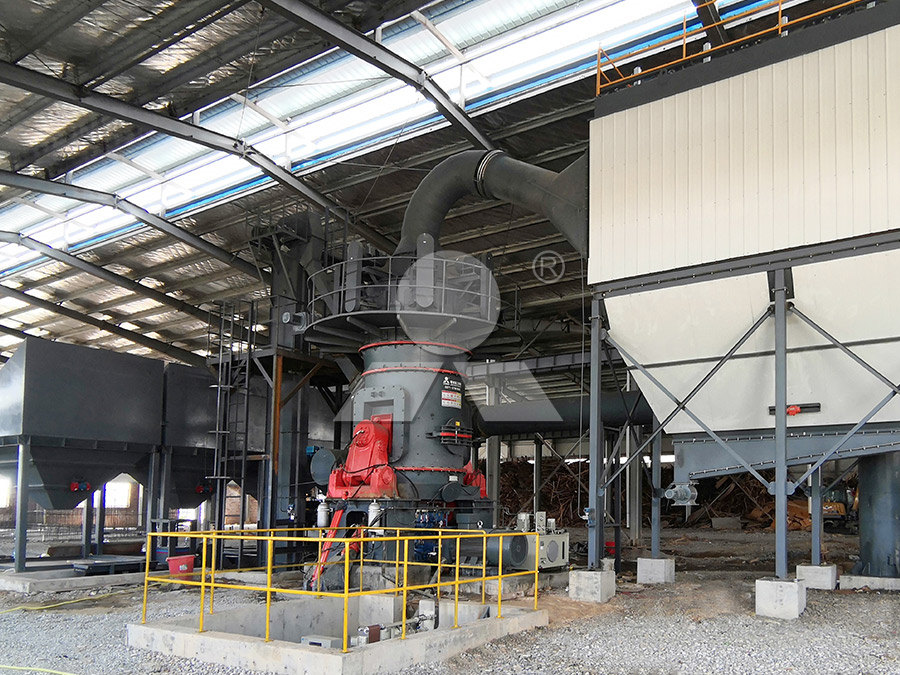
13 Types of Refractory Materials and Their Applications
2024年11月18日 13 Types of Refractory Materials and Their Applications Refractory materials are used in various fields of the national economy, such as iron and steel, nonferrous metal, glass, cement, ceramics, petrochemical, machinery, boiler, light industry, electric power, military industry, etcIt is an essential basic material to ensure the production and operation of the Refractory materials such as Ti, W, Their high melting temperatures, however, make it extremely difficult to process the materials by melting and casting Therefore, tungsten and molybdenumbased alloys and composites are produced by a powder metallurgical method, followed by minor machining or grinding, if necessary Refractory Material an overview ScienceDirect Topics2023年6月9日 Alumina brick is a highperformance refractory material whose main component is alumina (Al2O3) Adding an appropriate amount of fine powder can not only make the secondary mullite reaction that occurs during the firing of highalumina bricks proceed in the fine powder In the general brickmaking process, the upper limit of coarse Alumina Bricks Manufacturing Process RS Kiln Refractory 2023年9月5日 Powder metallurgy is a manufacturing process that involves using metal powder, or a mixture of metal powder and nonmetal powder, as a raw material The powder is then formed and sintered to produce a range of metal materials, composite materials, and various types of articlesPowder Metallurgy: A Comprehensive Guide for Beginners
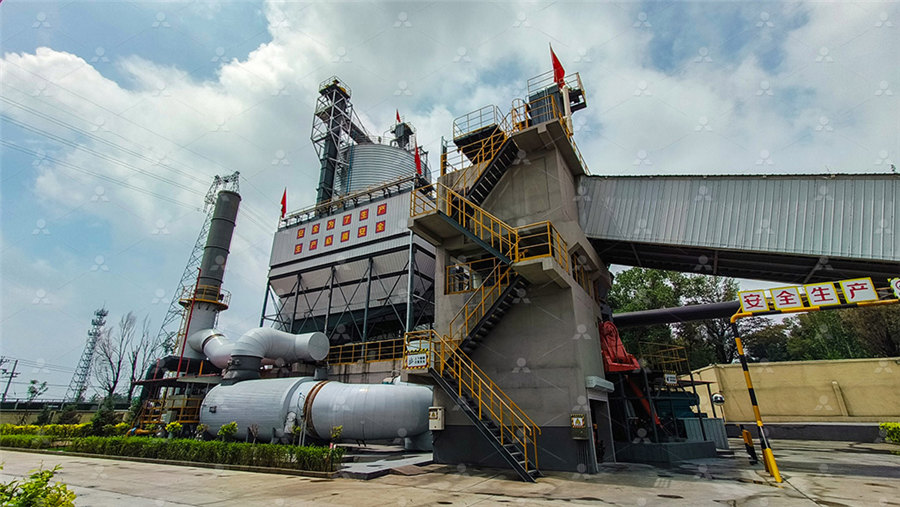
How Investment Casting Works Xometry
2023年9月1日 Antipenetration coatings applied to the pattern can reduce the penetration of melt into the refractory material, to improve the quality of the surface finish StepbyStep Process of Investment Casting Listed and discussed below is the stepbystep process of investment casting: 1 Create and Assemble the Wax Patterns2014年6月1日 Refractories are mostly used in basic metal industries In the steelmaking process by the basic oxygen furnace (BOF), the molten iron from the blast furnace is purified from the impurities including C, S, P, Mn, etc, by blowing oxygen [11]The major characteristic requirement of these refractories is resistance to molten slag (basic) and to the high Recent advances in silicaalumina refractory: A review2024年3月14日 5 Mediumsized coreless induction furnaces that use a variety of scrap steel as raw materials to make steel use Al2O3MgO (about 10% MgO) refractory materials to achieve a long service life 6 Mediumsized induction furnaces that use direct reduced iron balls as additives should use MgOAl2O3Cr2O3 (added chromium ore) refractory materialsSelection and application of nine different refractory materials The first step in the overall powder metallurgy process is making metal powders There are four main processes used in powder production: solidstate reduction, atomization, electrolysis, and chemical Refractory Metals Association Making Metal Powder MPIF
.jpg)
Preparation Process of Ceramic Shells SpringerLink
2021年2月7日 The refractories in the shell can be divided into fine refractory powder used in the slurry preparation and coarse granular sanding materials used in stuccoing The surface quality of the shell is mainly related to the selection of raw materials and shell making process Zengyan et al studied the effect of the binder and refractory on the 2020年6月10日 A special process for making alloy additions is the CAS process (Composition Adjustment by Sealed argon bubbling) In CAS process, a refractory lined snorkel is immersed in the steel bath and argon (Ar) gas is purged through a porous plug, fitted at the centre of the bottom of the ladleIron and SteelMaking Process SpringerLink2021年8月27日 Raw materials => Powder; Powders can be pure elements, prealloyed powders Methods for making powders – Atomization : Produces powders of both ferrous and refractory metals • Parts with controlled porosity can be made • High cost of powder material tooling • Less strong parts than wrought ones process grinds the powder Powder metallurgy – basics applications IIT GuwahatiThe plasma rotating electrode process (PREP system) offers several advantages for the production of metal powders and coatingsSome of the key benefits include: Highquality, spherical metal powders: The process produces fine, spherical metal powders with uniform size distribution and high sphericityWhat is Plasma Rotating Electrode Process PREP?
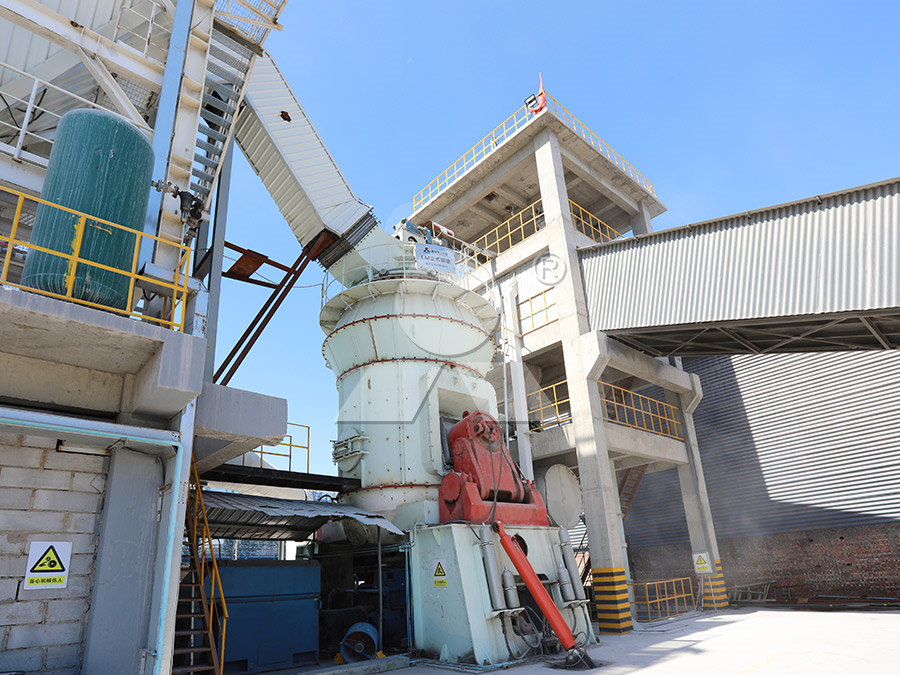
Challenges in thermal spraying of refractory materials
2023年6月7日 N Diagnostics and process control: thermal spraying of refractory materials is a highly complex process with a large number of interrelated variables The multitude of interdependent process parameters results in a range of thermal histories for the molten particles, producing a wide distribution of particle velocities and temperatures within the2023年4月26日 The use of highquality refractory materials is essential to ensure the safety and efficiency of industrial processes, making it a crucial process for businesses to implement Discover the world's Basics of Refractory Production Request PDF ResearchGate2023年1月2日 Refractory Cement is a heatresistant material designed to line fireboxes and withstand very hot environments (2,0003,000*F) such as firebox linings, forges, kilns, ovens, incinerators, crematoriums, and other high temperature equipment Refractory cement is commonly combined with other products like firebrick and other ceramics to further increase Refractory Cement: What it Is, Plus 5 Things You NEED to Know2023年10月10日 A: Satelliting occurs when smaller particles bond to larger particles during solidification This can be reduced by optimizing atomization and cooling parameters Contamination from refractories or improper material handling negatively impacts purity so cleanliness is critical Q: How stable are atomized metal powder properties over time?The Atomizing Metal Powder Industry Additive Manufacturing Material
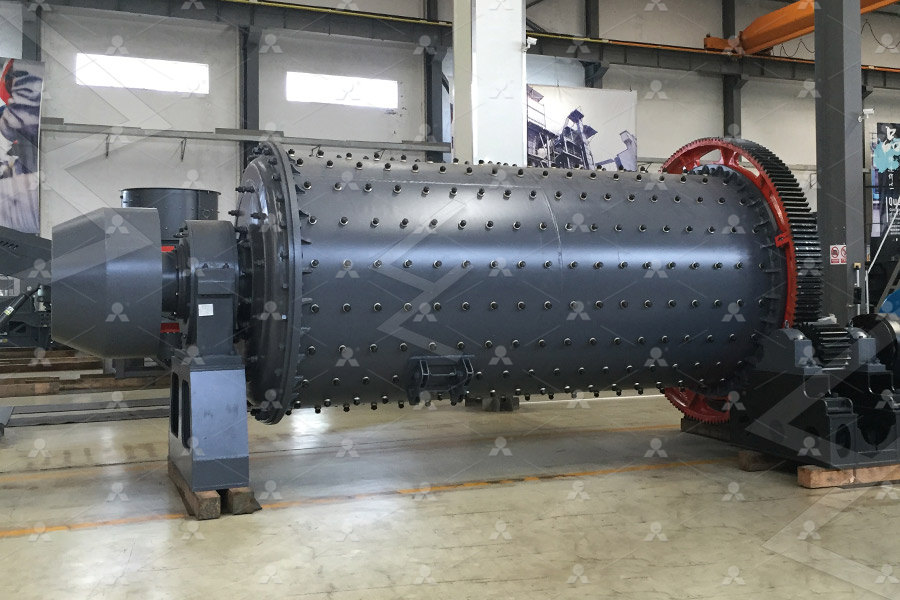
A review on recent progress of refractory high entropy
2024年11月1日 Firstly, the prominence of materials science not only reflects the materials science attributes and critical characteristics of refractory highentropy alloy research but also highlights the focus on alloy composition design, microstructure control, preparation process optimization, and performance characterization23 小时之前 As with any industrial process, how much maintenance is required of a system is a crucial consideration alongside longevity It stands to reason that any material that is physically stronger (in terms of compressive strength or otherwise) will last longer without breaking, therefore reducing maintenance requirements and enhancing the lifetime of the system(5B)Key Properties of Refractory Materials Thermal ConductivitySo what are the commonly used raw materials for refractories? 1 Bauxite clinker Bauxite clinker is made of bauxite ore after high temperature calcination, and its Al2O3content is generally more than 50% In the unshaped refractory Common raw materials for refractory products2022年11月25日 What is Powder Metallurgy? Powder Metallurgy (PM) is a metal solidification technique that involves compacting metal powders into a die and heating it to temperatures just below their melting point to fuse by What is Powder metallurgy Powder metallurgy
.jpg)
Refractory for Casting SpringerLink
2020年6月10日 The continuous casting steelmaking process occurs at a temperature more than 1500 °C, so the interaction between the refractory material of SEN and liquid steel is to be considered The SEN must withstand the corrosion effect with slag and liquid steel, besides its mechanical strength and thermal shock resistance2017年8月15日 Spherical titanium alloy powder is an important raw material for nearnetshape fabrication via a powder metallurgy (PM) manufacturing route, as well as feedstock for powder injection molding, and additive manufacturing (AM) Nevertheless, the cost of Ti powder including spherical Ti alloy has been a major hurdle that prevented PM Ti from being adopted for a wide Review of the Methods for Production of Spherical Ti and Ti Alloy Powder2023年8月10日 Refractory clay undergoes a careful mining, purification, and shaping process to create various refractory products Are there environmentally friendly alternatives to refractory clay? Researchers are exploring ecofriendly refractory materials, but refractory clay remains a reliable and commonly used choiceWhat is Refractory Clay? Exploring Its Basics and Benefits2020年6月10日 Therefore, choice of refractory materials for steel ladle lining and tundish lining is very crucial to produce clean steel When the steel melt is reoxidized by lining refractory materials, the oxygen reacts with dissolved Al (aluminium) in steel to form Al 2 O 3, which partly floats into slag and partly remains in steel as inclusionsModern Refractory Practice for Clean Steel SpringerLink
.jpg)
Tundish Technology for Casting Clean Steel: A Review
2016年3月21日 With increasing demand of highquality clean steel, cleanliness is of paramount importance in steel production and casting Tundish plays an important role in controlling the continuously cast steel quality as it links a batch vessel, ladle, to a continuous casting mold Tundish is also the last vessel in which metal flows before solidifying in mold For controlling 2022年4月6日 Refractory metals also have high density and are chemically inert Their high melting points give way to powder metallurgy as the choice for manufacturing different components A few of the most common applications for refractory metals include wire filaments, tools, chemical vessels within corrosive atmospheres and casting molds With their very high Refractory Metals: Properties, Types and Applications2017年8月28日 ISOSTATIC PRESSING TECHNOLOGY FOR REFRACTORY MATERIALS E V Degtyareva and Ya M Grinberg UDC 6667603265:62170444 energy firing process, but on account of the lower energy consuming processes (preparation of body, pressing) to the powder through the elastic shells 2 and 5 In the case of hot isostatic pressingIsostatic pressing technology for refractory materials2023年2月11日 It is divided into the production process of shaped refractory products and of monolithic refractory materials The production process is shown in Fig 1 The production process of shaped refractory products mainly includes (1) calcination of raw materials Most natural refractory raw materials need calcination to obtain clinker before usingRefractories, Properties and Application of SpringerLink
.jpg)
Design, Manufacturing and Properties of Refractory Materials
2024年4月5日 With pleasure, we present this Special Issue of Materials, titled “Design, Manufacturing and Properties of Refractory Materials”Refractory materials are both economically and socially strategic materials as they enable the production of other crucial products, including steel, nonferrous metals, cement clinker, lime, glass and many others2018年3月27日 The material used in this research is a mixture of evaporation boats waste powder, kaolin, and graphite, with a composition of 50%, 25% and 25%, respectively During the mixing process, 15% of (PDF) Review of Refractory Materials for 2023年6月22日 Silica‐Based Refractories for Iron and Steel Melting Silica‐based refractories have long been the standard for foundries using coreless furnaces to melt iron and iron alloys Traditional lining materials include a high purity silica aggregate with a boron‐ based, heatset binder, generally in the form of either boron oxide or boric acidInnovative Refractory Technology for Coreless Induction 2021年9月21日 Manufacturing components from refractory metals presents great challenges due to their high melting temperature and low ductility Until now, powder metallurgy followed by thermomechanical process has been the only viable route for producing bulk refractory materials on an industrial scaleLatest Developments in Manufacturing and Recycling of Refractory Materials
.jpg)
13 Types of Refractory Materials and Their Applications
2024年11月18日 13 Types of Refractory Materials and Their Applications Refractory materials are used in various fields of the national economy, such as iron and steel, nonferrous metal, glass, cement, ceramics, petrochemical, machinery, boiler, light industry, electric power, military industry, etcIt is an essential basic material to ensure the production and operation of the Refractory materials such as Ti, W, Their high melting temperatures, however, make it extremely difficult to process the materials by melting and casting Therefore, tungsten and molybdenumbased alloys and composites are produced by a powder metallurgical method, followed by minor machining or grinding, if necessary Refractory Material an overview ScienceDirect Topics2023年6月9日 Alumina brick is a highperformance refractory material whose main component is alumina (Al2O3) Adding an appropriate amount of fine powder can not only make the secondary mullite reaction that occurs during the firing of highalumina bricks proceed in the fine powder In the general brickmaking process, the upper limit of coarse Alumina Bricks Manufacturing Process RS Kiln Refractory 2022年7月19日 PREP Refractory Metal and Alloy Powders; PREP Other Metallic Powders; the plasma gas flow, etc In the PREP powder making process, droplets are thrown out when the centrifugal force is greater than the surface tension, therefore, increasing the electrode rod rotation speed or increasing the electrode rod diameter to increase the centrifugal What is Plasma Rotating Electrode Atomizing Powder Making
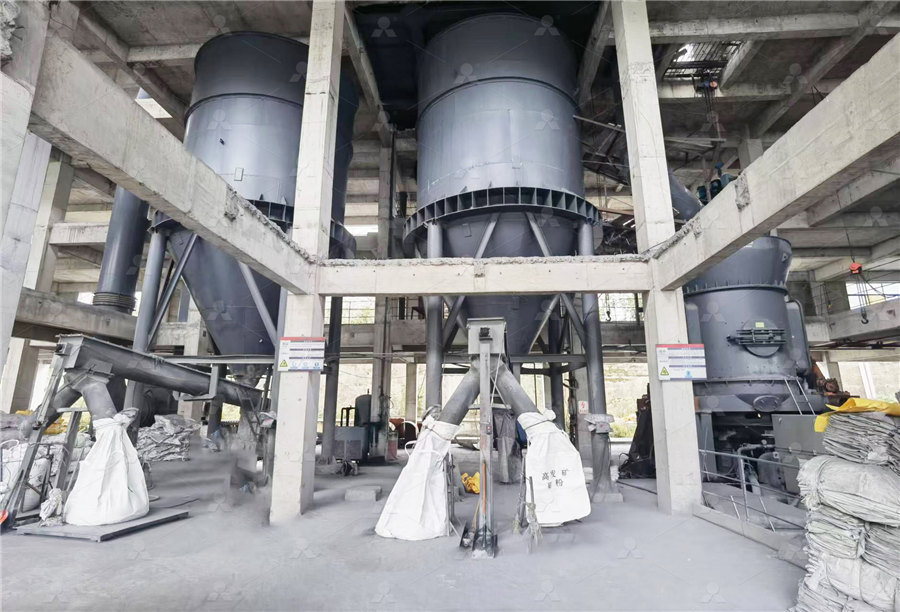
Powder Metallurgy: A Comprehensive Guide for Beginners
2023年9月5日 Powder metallurgy is a manufacturing process that involves using metal powder, or a mixture of metal powder and nonmetal powder, as a raw material The powder is then formed and sintered to produce a range of metal materials, composite materials, and various types of articles