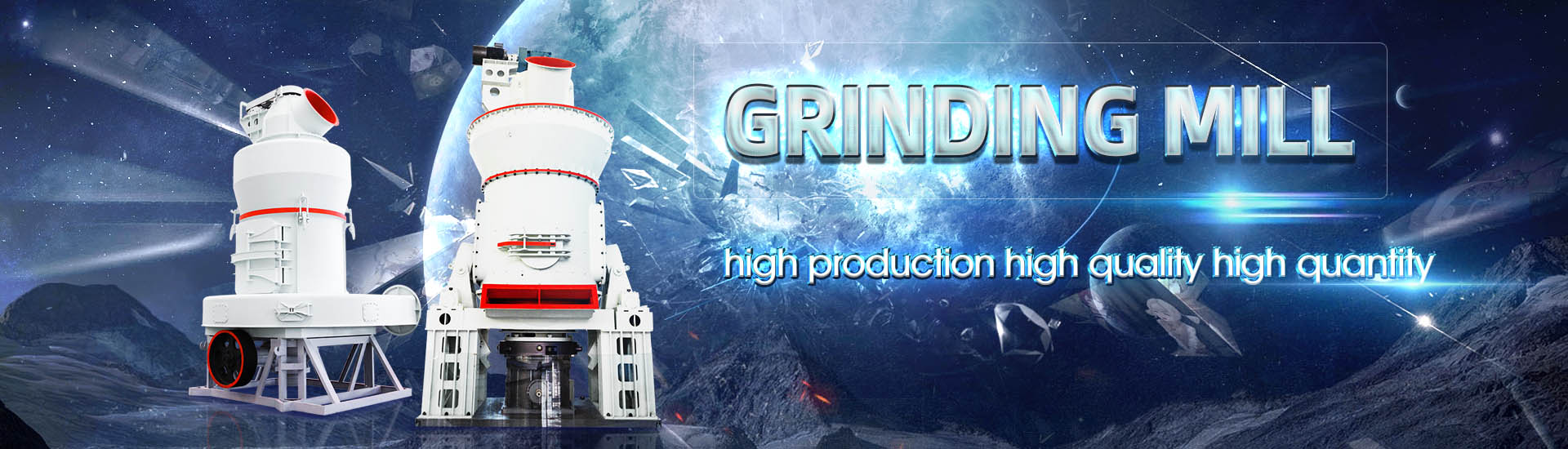
Vogelsang ore grinding mill
.jpg)
The right grinding technology for every application Vogelsang
Grinding technology is needed for many different applications: Whether for avoid blockades caused by wet wipes in sewers, cut down foreign matter and prepare the suspension in biogas The twinshaft grinder XRipper from Vogelsang, has been designed for an economical grinding of solids and foreign matter in fluids It can be used in industrial wastewater plants or even in XRipper: Industrial solids twinshaft grinder VogelsangThanks to the different speeds of the two shafts, the XRipper XRL rotors are selfcleaning To adjust to the medium and the size reduction ratio, various XRipper XRL rotors are available The industrial grinder for the rough stuff VogelsangVogelsang has taken its XRipper twinshaft grinder technology to a new level with the XRipper Giant (XRG) An extension of the company’s XRipper line, this design was developed for the XRipper New Giant in Solids Reduction
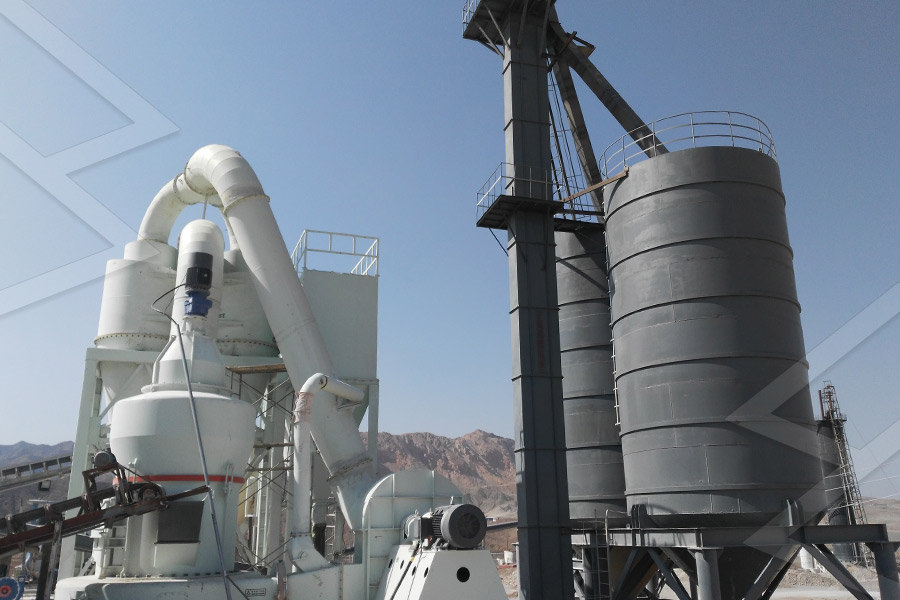
Ore Grinding SpringerLink
2023年7月20日 Ore grinding is completed in the cylinder of the grinding mill With a certain amount of grinding medium in the cylinder, when the cylinder rotates, the grinding medium is 2012年9月1日 Mills (VRM) installations and summarises the main benefits of the dry compressive Loesche grinding technologies in Airflow and OverflowMode Some of these OneMine Latest Installations And Developments Of Loesche 2023年10月27日 Grinding media play an important role in the comminution of mineral ores in these mills This work reviews the application of balls in mineral processing as a function of the A Review of the Grinding Media in Ball Mills for Mineral 2015年3月15日 For the grinding tests, a Loesche mill LM45 (table diameter 045 m) is used (Fig 2a) This pilot scale mill is a special development for ore grinding, which is reflected by Research of iron ore grinding in a verticalrollermill
.jpg)
Protected by the twinshaft grinder XRipper Vogelsang
Grinders and heavy matter protection Installed directly in the fluid current, the wastewater (or other flowable medium) passes through the twinshaft grinder XRipper virtually without 23 小时之前 03 Optimization of gold ore crushing and grinding processes (SAG) and autogenous grinding mills (AG) can be used In addition, the application of the Bond ball mill Operation and Management of Gold Ore Concentrators2023年7月1日 The simplified flowsheet of the copper ore grinding circuit on which the water added points and sampling locations are seen is depicted in Fig 1 Within the circuit, two ball mills and two cyclone clusters are in the operation and only the secondary ball mill is closed circuited Analysis of ball mill grinding operation using mll power Element based ball mill and hydrocyclone modelling for a copper ore 2016年11月7日 In Fig 13 is shown a large ball mill, designed for the dry grinding of limestone, dolomite, quartz, refractory and similar materials; this type of mill being made in a series of sizes having diameters ranging from about 26 Grinding Mills Common Types 911Metallurgist
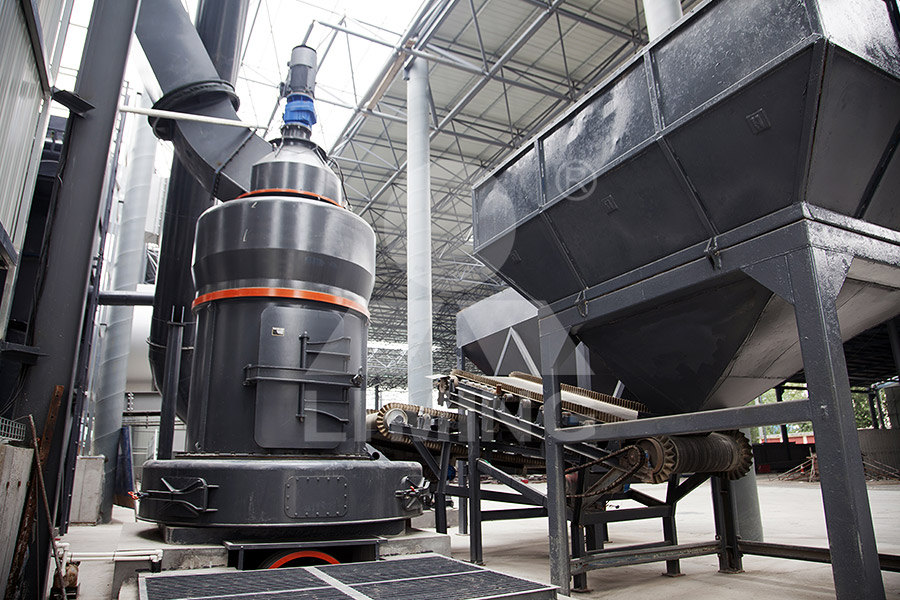
Population balance model approach to ball mill
2014年1月1日 An analysis of the kinetics of dolomite grinding in a dry ball mill reveals that the following approximations apply for the parameters of the batch grinding model: the size discretized selection 2024年10月13日 Effect of mill type on ore grinding performance Ball mills are widely used in the mining and metallurgical industries for the grinding of ores and other materials There are a wide variety of mill types available, each with its own advantages and disadvantages The performance of a ball mill can be affected by a number of factors, including the Factors affecting ores grinding performance in ball millsAutogenous mills are grinding mills that use the ore itself as the grinding medium The ore is fed into the mill, and as it rotates, it crushes and grinds itself, producing a fine powder Autogenous mills are highly efficient and can produce fine particles quickly They are also versatile and can be used for both wet and dry grindingWHAT ARE GRINDING MILLS? Total System Solution TSSGrinding Mills Barry A Wills, James A Finch FRSC, FCIM, PEng, in Wills' Mineral Processing Technology (Eighth Edition), 2016 71 Introduction Grinding is the last stage in the comminution process where particles are reduced in size by a combination of impact and abrasion, either dry, or more commonly, in suspension in waterGrinding Mill an overview ScienceDirect Topics
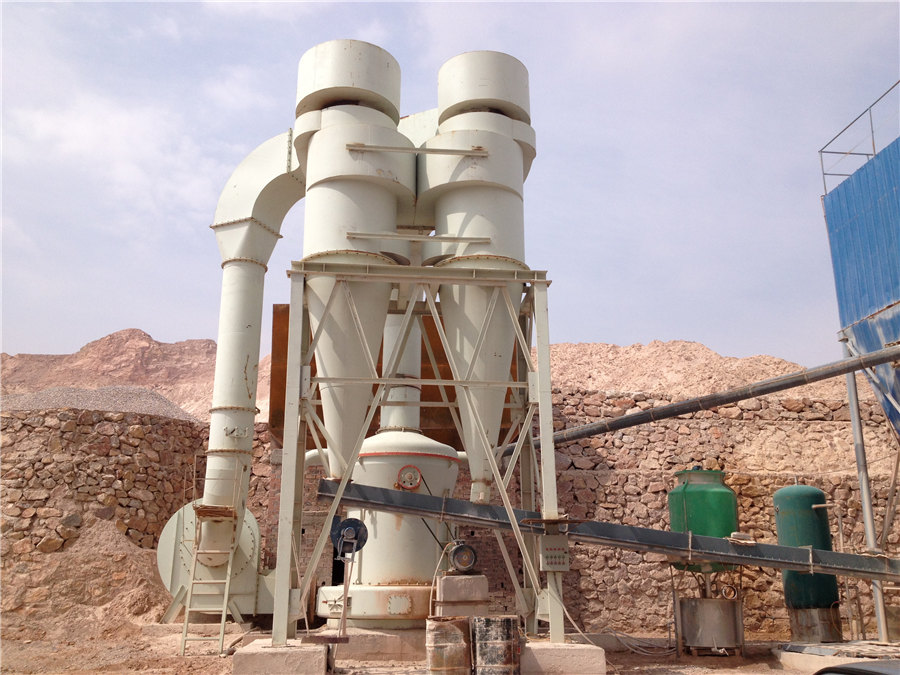
Factors Affecting Ball Mill Grinding Efficiency 911Metallurgist
2017年10月26日 a) Mill Geometry and Speed – Bond (1954) observed grinding efficiency to be a function of ball mill diameter, and established empirical relationships for recommended media size and mill speed that take this factor into account As well, mills with different length to diameter ratios for a given power rating will yield different material 2015年7月29日 The Time that the ore spends in the grinding mill is called, RETENTION TIME This is a very important variable, the longer the retention time, the more the ore comes in contact with the rods, the better and finer the grind becomes To understand this important control it must be remembered that any volume that is added to a circuit must leave Effect of Water Density on Grinding Mill 911Metallurgist2023年10月27日 The ball mill is a rotating cylindrical vessel with grinding media inside, which is responsible for breaking the ore particles Grinding media play an important role in the comminution of mineral A Review of the Grinding Media in Ball Mills for Mineral A crushing plant delivered ore to a wet grinding mill for further size reduction The size of crushed ore (F 80) was 40 mm and the SG 28 t/m 3 The work index of the ore was determined as 122 kWh/t A wet ball mill 1 m × 1 m was chosen to grind the ore down to 200 micronsGrinding Mill an overview ScienceDirect Topics
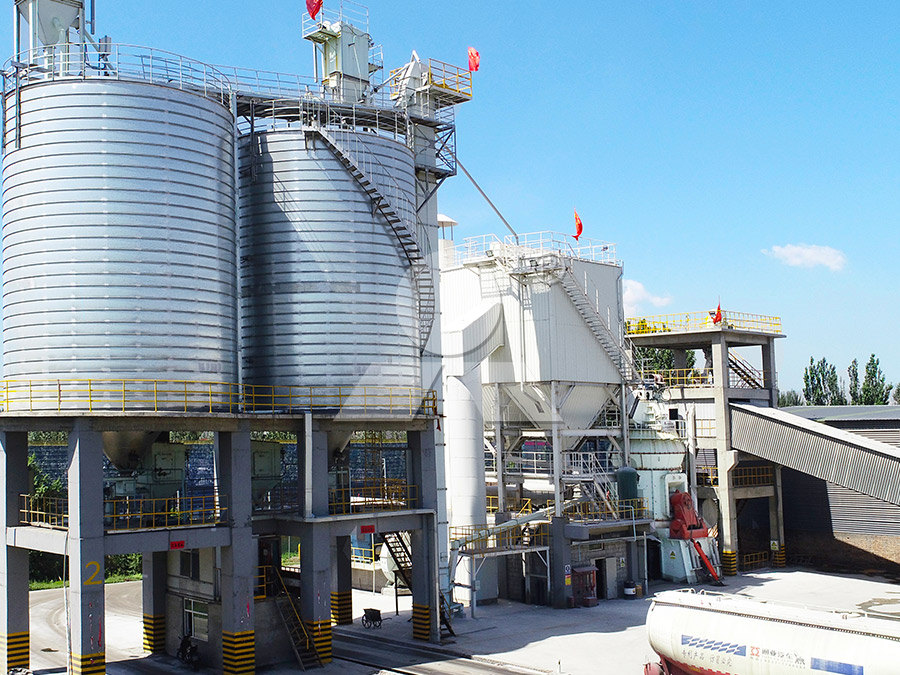
Ball Mill Is Indispensable For Lithium Ore
2024年11月21日 The grinding and grading stage of lithium ore is to ensure that lithium minerals are fully dissociated from gangue mineral monomers Therefore, lithium ore extraction is inseparable from ore grinding, and the common 2017年2月20日 All Grinding Mill Ball Mill Manufacturers understand the object of the grinding process is a mechanical reduction in size of crushable material When choosing primary autogenous grinding, run of mine ore up to 200300 mm in size is fed to the mill When using a crushing step before the grinding, the crusher setting should be 150200 mm Grinding Mill Design Ball Mill Manufacturer2014年10月1日 In a test performed in the Loesche test center in Germany, copper slag grinding saved 229% energy in an airswept model and 344% energy in an overflow model [13,14]Copper Ore Grinding in a Mobile Vertical Roller Mill Pilot Plant2015年8月6日 The high profile liner is designed to give the media the higher lift This type will be used in mills that are designed for primary grinding and as a result require the impact of the higher cascade Ball mills working as the secondary portion of a grinding circuit will utilize the lower profile liners The reason is as lift decreases, friction Grinding Mill Liners 911Metallurgist
.jpg)
Mill, Grinding mill All industrial manufacturers
Vogelsang (1) VOLKMANN (1) Voran (9) W; Wagner Maschinenbau GmbH (1) WAHAL ENGINEERS (5) for ore for cement concrete for clinker for mortar for asphalt for powders (104) for metals (83) Ball mill is common used grinding plant in the industry, and it is key equipment used for milling after materials are crushed This machine can be can 2019年4月16日 These mills combine crushing, grinding, classification and drying operations in one unit and have advantages over conventional machines and literature reports 15% energy saving is achievable in (PDF) LEARNING FROM OTHER INDUSTRIES; WHY THE VRM 2021年5月8日 Kolev et al (2021) –In press Improving the energy efficiency in tumbling mills with the use of Relo grinding media (MDPI) • Lab trials conducted using a standard Bond ball mill (@ Wardell Armstrong) • Standard Bond ball mill procedures were followed –only the RELO media PSD and mass of charge adjusted to match spherical mediaRethinking Grinding Efficiency in Ball Mills RELO 2012年6月1日 As the cylinder starts to rotate, the grinding balls inside the cylinder crush and grind the feed material, generating mechanical energy that aids in breaking bonds, activating the catalyst, and (PDF) Grinding in Ball Mills: Modeling and Process Control
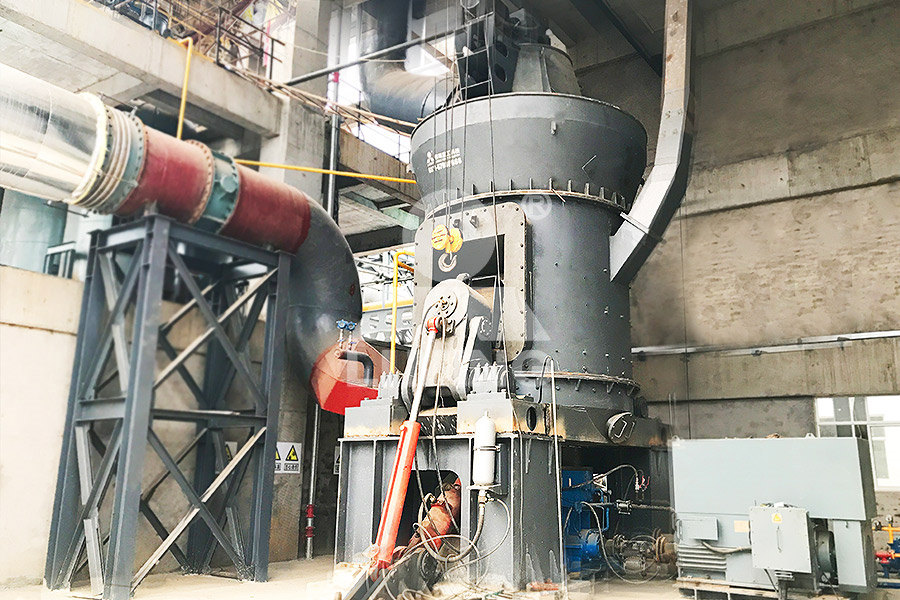
Calculate and Select Ball Mill Ball Size for Optimum Grinding
2013年8月3日 In Grinding, selecting (calculate) the correct or optimum ball size that allows for the best and optimum/ideal or target grind size to be achieved by your ball mill is an important thing for a Mineral Processing Engineer AKA Metallurgist to do Often, the ball used in ball mills is oversize “just in case” Well, this safety factor can cost you much in recovery and/or mill liner CLUM series of ultrafine gypsum powder vertical grinding mills are a new type of ultrafine industrial ore grinding equipment that integrates grinding, grading, powder collection and conveying +17 [ protected] languageCLUM Ultrafine Vertical Grinding MillThe special features of Vogelsang grinding technology As an experienced manufacturer of grinding technology, we are continuously further developing our products Because they are relied upon in a diverse range of applications and sectors, we have the opportunity to learn more about our customers' specific requirements, which allows us not only The right grinding technology for every application VogelsangVogelsang uses its proprietary software to develop cutting screens with optimized geometry for every sizereduction ratio For operators, this means the best geometry at all times for smooth running, with minimal wear The cutting screens are produced from wearresistant special steel and offer twice the performance since they are reversibleRotaCut: Macerator for wastewater and sludges Vogelsang

Fine Grinding as Enabling Technology – The IsaMill
3 天之前 Figure 1 : Grinding Power to produce various product sizes in a Ball Mill (9mm balls) and an Isa Mill (2 mm sand) (for KCGM pyrite concentrate) Chemistry Impacts The use of inert grinding media gives a crucial advantage to stirred milling in fine flotation and leaching applications Even if it were economic to grind to 10 microns in a steel 2015年3月10日 DOI: 101016/JMINPRO201410002 Corpus ID: ; Copper ore grinding in a mobile vertical roller mill pilot plant @article{Altun2015CopperOG, title={Copper ore grinding in a mobile vertical roller mill pilot plant}, author={Deniz Altun and Carsten Gerold and Hakan Benzer and Okay Altun and Namık A Aydogan}, journal={International Journal of Copper ore grinding in a mobile vertical roller mill pilot plant2015年3月15日 The application of vertical roller mills (VRMs) for ore grinding is a part of the strategies against rising energy consumption (Reichert et al, 2015) Research of iron ore grinding in a verticalrollermill2024年7月19日 Grinding mills pulverise and grind ores in mineral processing applications, breaking them down into fine particles to facilitate the extraction of valuable minerals MPT offers a diverse range of grinding mills designed to meet the varied needs of our clients The MPT equipment range ensures optimised performance and efficiency across all Grinding Mills in the Mineral Processing Industry
.jpg)
SBM Ultrafine Powder Technology Industrial Grinding Mill,
SBM ultrafine powder technology co,ltd Is China's excellent ore mill supplier Our main products include ultrafine vertical roller mill, ultrafine grinding mill, stone powder production equipment, Welcome to consult ultrafine grinding mill, stone powder production equipment, Welcome to consult +17 [ protected] language 4 天之前 A wet grinding 4 x 10 center peripheral discharge rod mill used for producing fine aggregates Twelve 7 x 24 Compeb mills grinding cement clinker to a product of 1750 surface area, 90% passing a 200 mesh screen An 8 x 7 diaphragm type ball mill grinding 05″ copper ore to 96% passing 65 meshGrinding Mills 911Metallurgist2023年10月27日 The ball mill is a rotating cylindrical vessel with grinding media inside, which is responsible for breaking the ore particles Grinding media play an important role in the comminution of mineral ores in these mills This work reviews the application of balls in mineral processing as a function of the materials used to manufacture them and the mass loss, as A Review of the Grinding Media in Ball Mills for Mineral 2023年7月1日 The simplified flowsheet of the copper ore grinding circuit on which the water added points and sampling locations are seen is depicted in Fig 1 Within the circuit, two ball mills and two cyclone clusters are in the operation and only the secondary ball mill is closed circuited Analysis of ball mill grinding operation using mll power Element based ball mill and hydrocyclone modelling for a copper ore
.jpg)
Grinding Mills Common Types 911Metallurgist
2016年11月7日 In Fig 13 is shown a large ball mill, designed for the dry grinding of limestone, dolomite, quartz, refractory and similar materials; this type of mill being made in a series of sizes having diameters ranging from about 26 2014年1月1日 An analysis of the kinetics of dolomite grinding in a dry ball mill reveals that the following approximations apply for the parameters of the batch grinding model: the size discretized selection Population balance model approach to ball mill 2024年10月13日 Effect of mill type on ore grinding performance Ball mills are widely used in the mining and metallurgical industries for the grinding of ores and other materials There are a wide variety of mill types available, each with its own advantages and disadvantages The performance of a ball mill can be affected by a number of factors, including the Factors affecting ores grinding performance in ball millsAutogenous mills are grinding mills that use the ore itself as the grinding medium The ore is fed into the mill, and as it rotates, it crushes and grinds itself, producing a fine powder Autogenous mills are highly efficient and can produce fine particles quickly They are also versatile and can be used for both wet and dry grindingWHAT ARE GRINDING MILLS? Total System Solution TSS
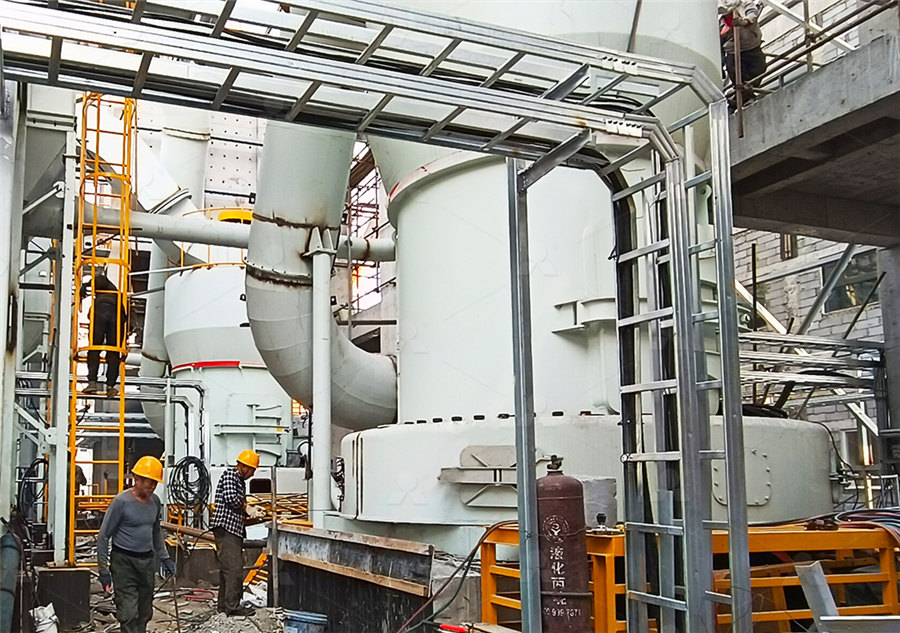
Grinding Mill an overview ScienceDirect Topics
Grinding Mills Barry A Wills, James A Finch FRSC, FCIM, PEng, in Wills' Mineral Processing Technology (Eighth Edition), 2016 71 Introduction Grinding is the last stage in the comminution process where particles are reduced in size by a combination of impact and abrasion, either dry, or more commonly, in suspension in water2017年10月26日 a) Mill Geometry and Speed – Bond (1954) observed grinding efficiency to be a function of ball mill diameter, and established empirical relationships for recommended media size and mill speed that take this factor into account As well, mills with different length to diameter ratios for a given power rating will yield different material Factors Affecting Ball Mill Grinding Efficiency 911Metallurgist2015年7月29日 The Time that the ore spends in the grinding mill is called, RETENTION TIME This is a very important variable, the longer the retention time, the more the ore comes in contact with the rods, the better and finer the grind becomes To understand this important control it must be remembered that any volume that is added to a circuit must leave Effect of Water Density on Grinding Mill 911Metallurgist2023年10月27日 The ball mill is a rotating cylindrical vessel with grinding media inside, which is responsible for breaking the ore particles Grinding media play an important role in the comminution of mineral A Review of the Grinding Media in Ball Mills for Mineral
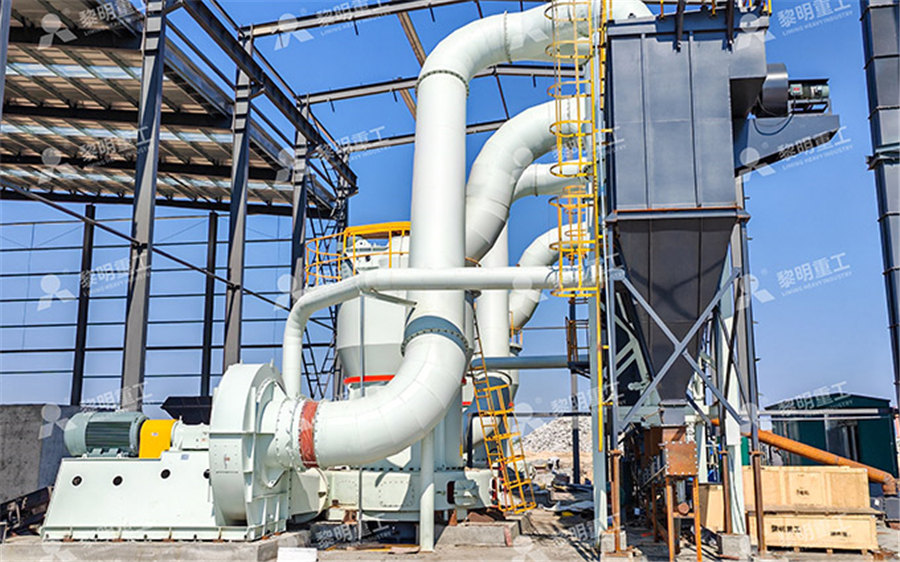
Grinding Mill an overview ScienceDirect Topics
A crushing plant delivered ore to a wet grinding mill for further size reduction The size of crushed ore (F 80) was 40 mm and the SG 28 t/m 3 The work index of the ore was determined as 122 kWh/t A wet ball mill 1 m × 1 m was chosen to grind the ore down to 200 microns