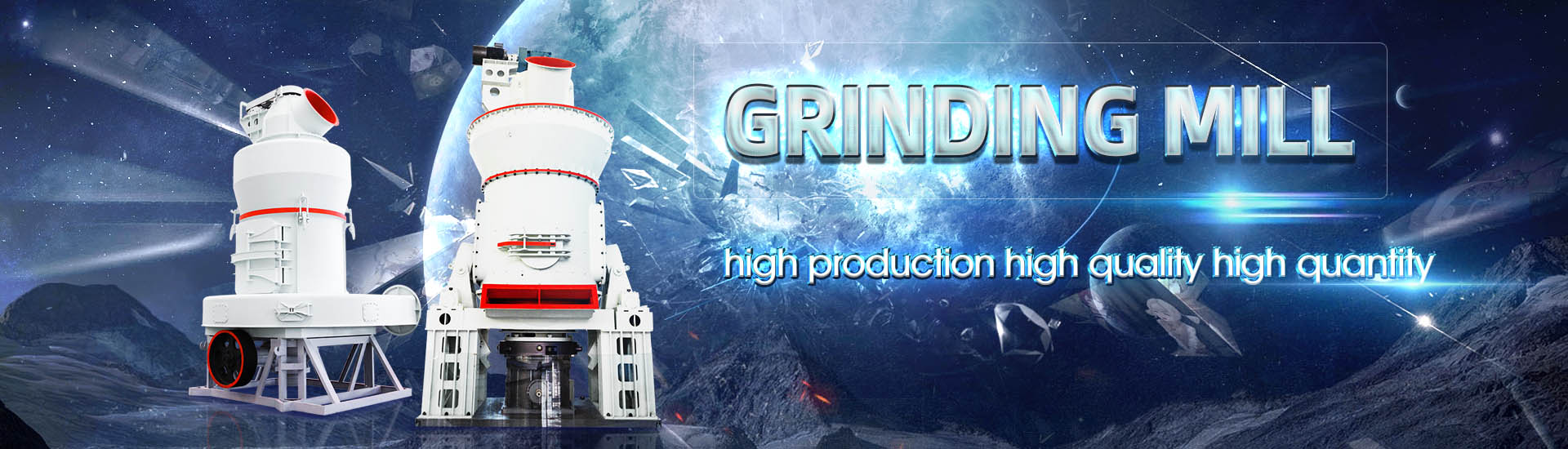
Armenia cement clinker European version ball mill
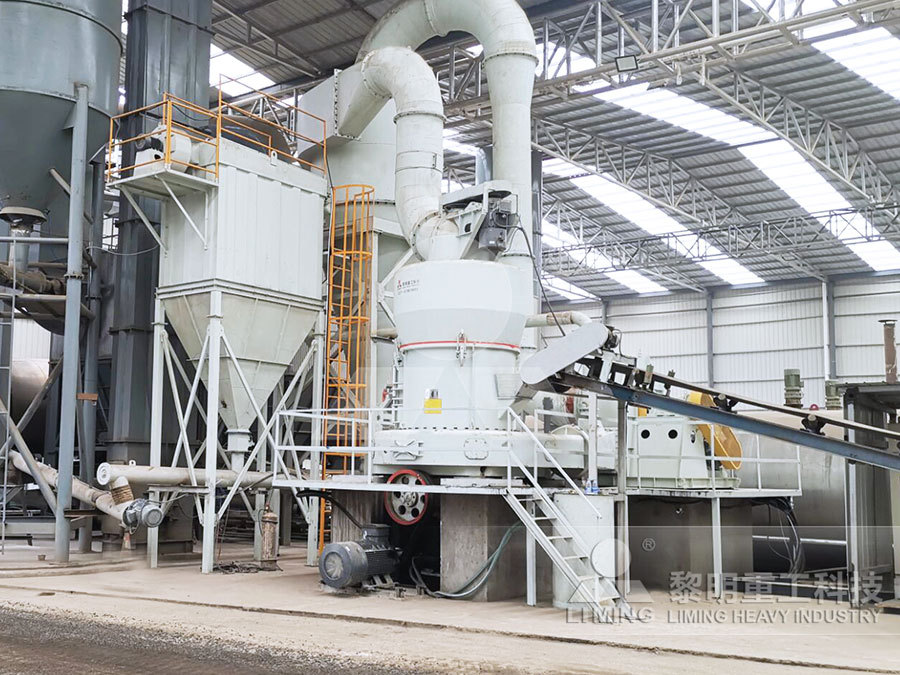
Modeling of closedcircuit ball milling of cement clinker via a
2023年9月1日 Fullscale closedcircuit cement ball milling was modeled using a true unsteadystate simulator (TUSSIM), based on a transient cellbased population balance model (PBM) 2023年5月1日 Our results show that steel balls achieved faster breakage of clinker into finer particles than alumina balls, which was explained by the higher total–mean energy dissipation A comparative analysis of steel and alumina balls in fine Nowadays, ball mills are widely used in cement plants to grind clinker and gypsum to produce cement The research focuses on the mill speed as well as air classifier speed effect on thea) Cement ball mill view, b) Cement mill sketch2022年8月18日 Discrete Element Methods (DEM) is a numerical tool consolidated to the simulations of collisions in particulate systems In this paper, the method was used to study Experimental study of clinker grinding in a ball mill and the
.jpg)
Experimental study of clinker grinding in a ball mill and
2023年6月27日 Discrete Element Methods (DEM) is a numerical tool consolidated to the simulations of collisions in particulate systems In this paper, the method was used to study 2015年1月27日 The use of highpressure grinding rolls (HPGR) prior to ball mills has become a common practice in cement clinker grinding due to significant energy savings in comparison to BallMill Grinding Kinetics of Cement Clinker Comminuted in Ball mills for fine grinding cement clinker and additives are widely used around the world To improve the efficiency of a ball grinding the ball mills are transferred in closed circuit with air Analysis of the efficiency of the process in closed circuit 2023年10月19日 It relies on the use of steel balls to crush and grind the clinker Ball mills are often used for grinding cement clinker into a fine powder before it is mixed with other materials to produce cement Vertical Roller Mill (VRM): Understanding the Role of Clinker Grinding in
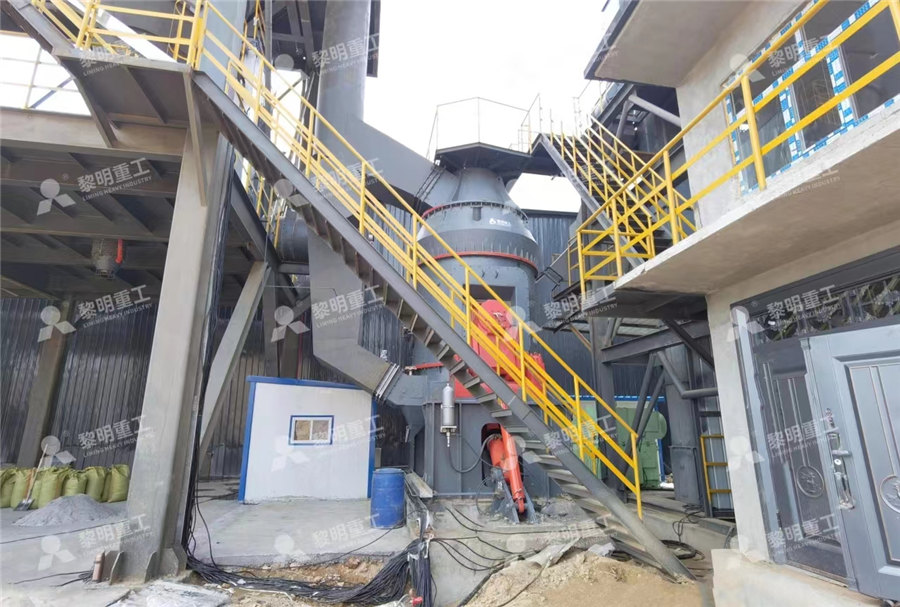
Determination of granulometrical composition
2020年7月24日 This paper presents results regarding the grinding behaviour of two batches of material (clinker) in a ball mill with its own twostep grinding process: the first one with a ball load, the second 2024年10月13日 This is where cement ball mills play a significant role A cement ball mill is a type of grinder used to grind and blend raw materials and clinker in the cement production process Functioning of Cement Ball Mill A cement ball mill is Cement ball mill: A key component in cement production2021年6月29日 Nowadays, ball mills are widely used in cement plants to grind clinker and gypsum to produce cement The research focuses on the mill speed as well as air classifier speed effect on the two Effects of Mill Speed and Air Classifier Speed on 2024年7月31日 The production of cement, an essential material in civil engineering, requires a substantial energy input, with a significant portion of this energy consumed during the grinding stage This study addresses the gap in the literature concerning the collective impact of key parameters, including ball size, feed rate, and mill speed, on grinding efficiency Nine spherical Effect of Grinding Conditions on Clinker Grinding Efficiency: Ball
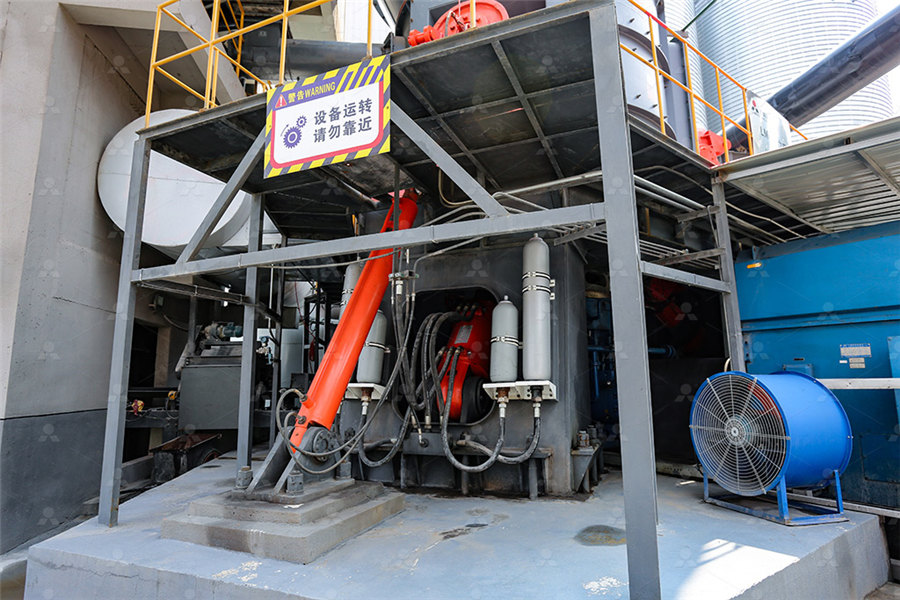
MODELING AND SIMULATION OF A CLOSED LOOP BALL
2016年4月11日 horizontal axis The raw material fed to the ball mill is cement clinker Mill drum is filled with steel balls that grind the cement clinker upon impact When the ball mill rotates, the steel balls are lifted up and dropped down on the feed material and hence due to the impact, the cement clinker breaks into smaller fragments2009年6月1日 In this study, the milling of clinker was evaluated by varying the mill speed (24 and 72 RPM), residence time (3 and 5 hours) and grinding media load (30 and 40 %) in a ball millCement clinker grinding: Evaluation of mill spin speed, 2020年2月1日 Nowadays, ball mills are used widely in cement plants to grind clinker and gypsum to produce cement In this work, the energy and exergy analyses of a cement ball mill (CBM) were performed and Energy and exergy analyses for a cement ball mill of a new 2023年9月1日 Fullscale closedcircuit cement ball milling was modeled using a true unsteadystate simulator (TUSSIM), based on a transient cellbased population balance model (PBM) with a set of differential algebraic equations (DAEs) As a major novelty, the PBM for the mill was coupled with a dust loaddependent, variable Tromp curve for the air classifierModeling of closedcircuit ball milling of cement clinker via a
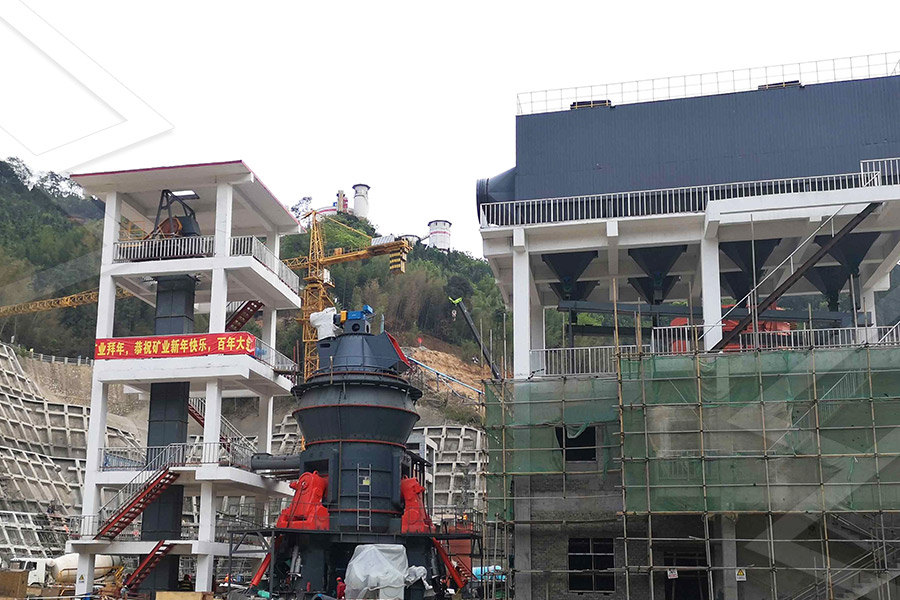
What Are the Parts of a Cement Mills? Cement
2023年8月23日 A cement mill is a fundamental component of the cement manufacturing process, playing a vital role in breaking down and grinding cement clinker into fine powder This finely ground powder, when mixed with other 2017年11月24日 In the article attention is paid to improving the efficiency of production of fine powders, in particular Portland cement clinker The questions of Portland cement clinker grinding in closed circuit ball mills Noted that the main task of modeling the grinding process is predicting the granulometric composition of the finished product taking Matrix model of the grinding process of cement clinker in the ball mill 2016年1月23日 invention in France which involved a tube mill with a charge of steel balls or flint pebbles for fine grinding of sand or cement FLSmidth acquired the rights to his patent and started selling an improved version of this mill all over the world For the cement industry the ball mill was really an epochmaking breakthrough as for almostCement grinding Vertical roller mills versus ball mills2023年10月23日 In this study we compare the effects of three different grinding aids on clinker grinding using a ball mill A commercial grinding additive, triethanolamine (TEA), and two industrial grinding aids (PDF) A study of different grinding aids for lowenergy cement clinker
.jpg)
Cement clinker ball mill suppliers in Turkey miningasia
2024年2月26日 The ball mill is a large, rotating cylinder that is filled with steel balls The cement clinker is fed into the ball mill, and the balls grind it into a fine powder Design Manufacture of Crushing Screening, and Grinding Equipment >European version hammer crusher in cement process plant >Vertical Cement Pulverizer Mill Price2016年10月5日 In this chapter an introduction of widely applied energyefficient grinding technologies in cement grinding and description of the operating principles of the related equipments and comparisons over each other in terms of grinding efficiency, specific energy consumption, production capacity and cement quality are given A case study performed on a EnergyEfficient Technologies in Cement Grinding2022年11月1日 In numerous cement ball mill operations (Genc, 2008, ε c and ε B denote the void fraction of cement clinker and steel balls, The set of DAEs in Eqs (1), (3), and (4) was solved simultaneously using the function “ode15s” in MATLAB version 99, which is a highly accurate, variable order–stepsize ordinary differential equation Impact of ball size distribution, compartment configuration, o Cement manufacture consumes typically 3,100 – 3,400 MJ of fuel/t clinker 90 130 kWh / t cement in a modern plant, more for older or less efficient plants; Europe’s largest ball mill supplied by CPB for Heidelberger Cement in Poland Improvements in New Existing Cement Grinding Mills by
.jpg)
Cement clinker ball mill manufacturer NEWS SMMVIK
2024年10月13日 The ball rotates around two sets of blades, which crush the clinker into small pieces The ball mill can be used to grind a variety of materials, including clinker from cement plants The ball mill is also used to produce other types of industrial materials, such as aggregate for road construction Benefits of using a cement clinker grinding 2018年2月1日 The prospects of application in ball mills for grinding cement clinker with inclined partitions are shown It is noted that ball mills with inclined partitions are more effective An algorithm is Matrix model of the grinding process of cement clinker in the ball mill2021年3月12日 Ball mills and grinding tools Cement ball mills are typically twochamber mills (Figure 2), where the first chamber has larger media with lifting liners installed, providing the coarse grinding stage, whereas, in the second chamber, medium and fine grinding is carried out with smaller media and classifying linersBALL MILLS Ball mill optimisation Holzinger Consulting2020年9月17日 The annual cement consumption in the world is around 17 billion tonnes and is increasing by 1% every year [1] Cement industries consume 5% of the total industrial energy utilised in the world [2] A total of 40% of the total energy consumption of a cement plant is used in clinker grinding in a ball mill to produce the final cement product [3]Predictive Controller Design for a Cement Ball Mill
.jpg)
Ball Mill Clinker Grinding Ball Mill Manufacturer from
We bring forth a highly advanced Ball Mill, specifically engineered for both wet as well as dry cement grinding applications Classified depending on the circuit design, bearing, grinding type and drive, the selection is made on the basis of the product fineness, quality, and nature of raw material, site conditions and specific requirementsA radiotracer investigation was carried out in a ball mill of a cement plant in Kenya Residence time distribution (RTD) of raw feed to the mill was measured using Technetium99m adsorbed on the Design of clinker grinding system; mill and separator2004年12月1日 During the last decade, semifinishgrinding plants have been used more and more for the energy efficient grinding of highquality cement In 1999, it was found that by decreasing the ball charge Optimization of continuous ball mills used for finishgrinding 2020年11月5日 As you all know, the process of a cement manufacturing plant can be divided into several steps, including crushing, raw milling, clinker calcining, cement milling (or cement grinding), packing and etc In the complete cement production line, the cement mill process plays a very important role The design of cement milling and cement mill process will produce a 3 Necessary Cement Milling Comparison Ball Mill Cement

The effects of grinding media shapes on the grinding kinetics of cement
2013年2月1日 To investigate the effects of grinding media shapes on the grinding kinetics of ball mill cement clinker, the grinding effects with ϕ20 mm balls and ϕ20 × 20 mm cylinders on six different size 2016年1月1日 Ball mills for fine grinding cement clinker and additives are widely used around the world To improve the efficiency of a ball grinding the ball mills are transferred in closed circuit with air Analysis of the efficiency of the grinding process in closed Vertical cement mill has high grinding efficiency and low power consumption (20% – 30% less than ball mill) The granularity of the feeding material is larger(VRM cement mill is 80mm120mm, cement ball mill is less than or equal to 30mm) Cement vertical mill occupies less space and saves 30% of construction costVertical Cement Mill Cement Clinker Grinding ball mills 2023年10月19日 It relies on the use of steel balls to crush and grind the clinker Ball mills are often used for grinding cement clinker into a fine powder before it is mixed with other materials to produce cement Vertical Roller Mill (VRM): Understanding the Role of Clinker Grinding in
.jpg)
Determination of granulometrical composition
2020年7月24日 This paper presents results regarding the grinding behaviour of two batches of material (clinker) in a ball mill with its own twostep grinding process: the first one with a ball load, the second 2024年10月13日 This is where cement ball mills play a significant role A cement ball mill is a type of grinder used to grind and blend raw materials and clinker in the cement production process Functioning of Cement Ball Mill A cement ball mill is Cement ball mill: A key component in cement production2021年6月29日 Nowadays, ball mills are widely used in cement plants to grind clinker and gypsum to produce cement The research focuses on the mill speed as well as air classifier speed effect on the two Effects of Mill Speed and Air Classifier Speed on 2024年7月31日 The production of cement, an essential material in civil engineering, requires a substantial energy input, with a significant portion of this energy consumed during the grinding stage This study addresses the gap in the literature concerning the collective impact of key parameters, including ball size, feed rate, and mill speed, on grinding efficiency Nine spherical Effect of Grinding Conditions on Clinker Grinding Efficiency: Ball
.jpg)
MODELING AND SIMULATION OF A CLOSED LOOP BALL
2016年4月11日 horizontal axis The raw material fed to the ball mill is cement clinker Mill drum is filled with steel balls that grind the cement clinker upon impact When the ball mill rotates, the steel balls are lifted up and dropped down on the feed material and hence due to the impact, the cement clinker breaks into smaller fragments2009年6月1日 In this study, the milling of clinker was evaluated by varying the mill speed (24 and 72 RPM), residence time (3 and 5 hours) and grinding media load (30 and 40 %) in a ball millCement clinker grinding: Evaluation of mill spin speed, 2020年2月1日 Nowadays, ball mills are used widely in cement plants to grind clinker and gypsum to produce cement In this work, the energy and exergy analyses of a cement ball mill (CBM) were performed and Energy and exergy analyses for a cement ball mill of a new 2023年9月1日 Fullscale closedcircuit cement ball milling was modeled using a true unsteadystate simulator (TUSSIM), based on a transient cellbased population balance model (PBM) with a set of differential algebraic equations (DAEs) As a major novelty, the PBM for the mill was coupled with a dust loaddependent, variable Tromp curve for the air classifierModeling of closedcircuit ball milling of cement clinker via a