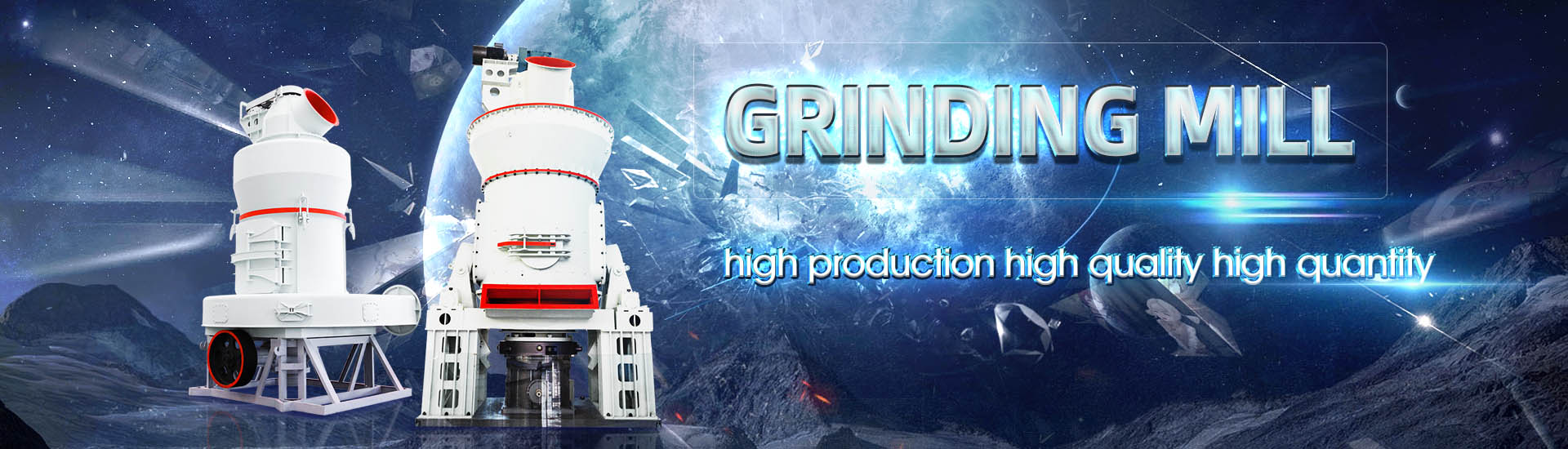
Iron oxide green grinding equipment process flow
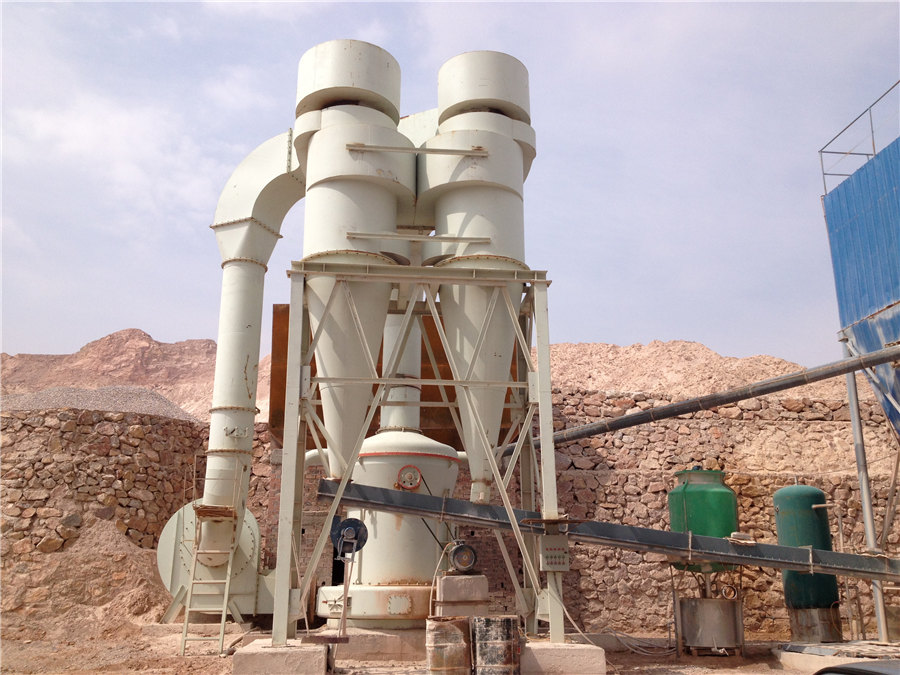
Economics of Electrowinning Iron from Ore for Green Steel
2024年8月5日 By comparing process flow diagrams, capital and operational expenditures, specific energy consumption, and production footprint, this work provides a highlevel assessment of the economic viability of these processes as they mature5 天之前 Process Flow: 1 Raw Material Preparation Input Material: Iron oxide Initial Size: ≤20 mm Moisture Content: ≤6% (predrying required if higher) 2 Grinding Process Core Iron Oxide Grinding Production Line With HGM80 Ultrafine Mill2024年8月5日 This study presents a comprehensive technoeconomic analysis of various green steel production methods, including hydrogen reduction and three different electrolysis Economics of Electrowinning Iron from Ore for Green Steel 2019年8月23日 Stage grinding, stage selection, coarsefine separation, gravitymagnetic separationreverse flotation process have been applied in China’s mixed iron ore dressing plant The fine sieving and regrinding process is an Iron Processing Equipment, Process Flow, Cases
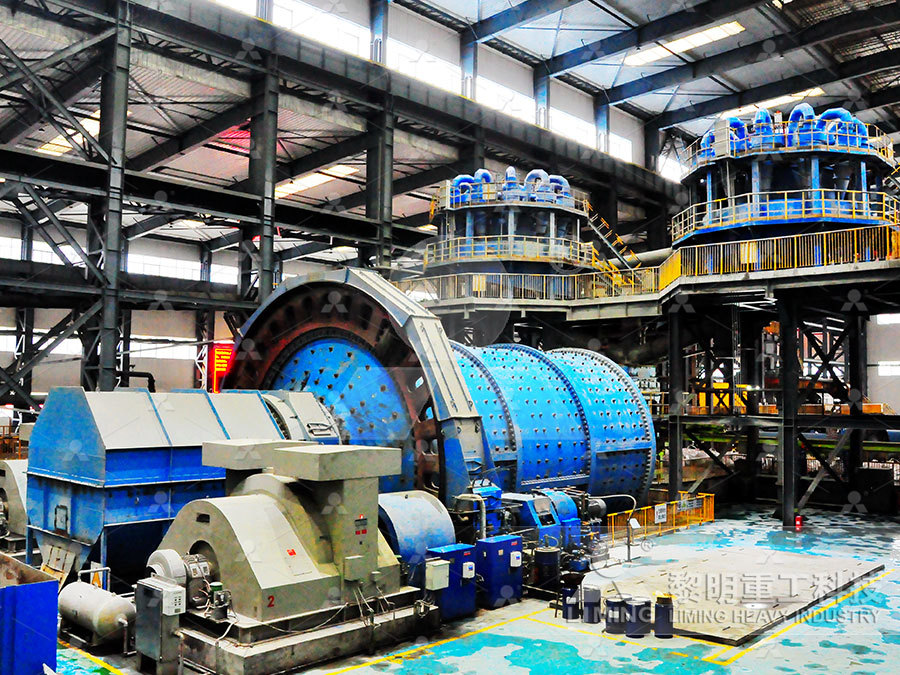
Green steel from red mud through climateneutral hydrogen
2024年1月24日 Replacing the carbonbased reducing substances by highly energetic hydrogen species contained in a hydrogen plasma is an energyefficient and partially electrified pathway 2023年10月9日 Fluidized bed technology has become a crucial method used to process iron ore powder in nonblast furnace ironmaking, such as smelting reduction and direct reduction This Development and Problems of Fluidized Bed Ironmaking Process2019年3月21日 The hightemperature reduction of iron oxide suspension is characterized by having: rapid reaction, obvious thermal decomposition and melting process Evaluation of the Review and data evaluation for hightemperature reduction of iron oxide 2023年10月1日 Batch thermal decomposition syntheses of iron oxide nanoparticles (IONPs) provide precise control of particle properties, but their scalability and reproducibility is High temperature flow synthesis of iron oxide nanoparticles:
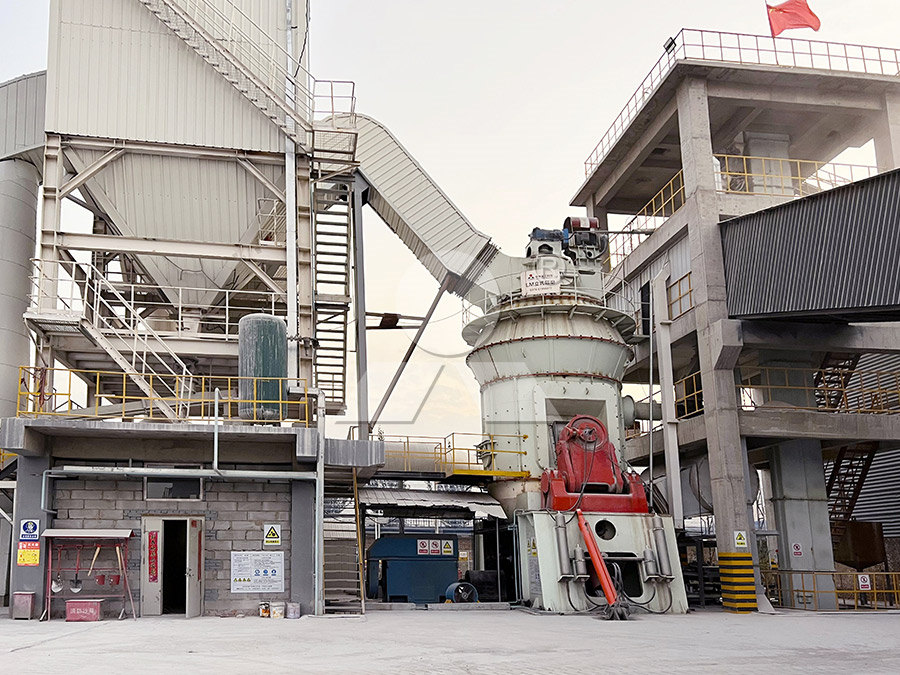
Producing green iron with a zeroCarbon
2023年2月9日 develop a new understanding of iron ore dissolution kinetics and a novel electrochemical regeneration scheme that enhances iron ore dissolution and increases the 2018年4月15日 Using iron‑chromium hydroxide precursors from the wet treatment of ICGW as raw material, monodisperse micaceous iron oxide (MIO) has been prepared via hydrothermal Preparation and formation mechanism of monodisperse micaceous iron 2023年10月1日 High temperature flow synthesis of iron oxide nanoparticles: Size tuning via reactor engineering Hence, a different flow process allowing selfseeded growth was designed to produce larger IONPs 33 Green Chem, 18 (2016), pp 31843209 View in High temperature flow synthesis of iron oxide nanoparticles: 2021年11月15日 Grinding Equipment (SiO2) icollidal suspension For certain materials, cerium oxide, chromium oxide, magnesium oxide or iron oxide may be used, although these the late 1920s, as Hoyt [7] mentions a visit to the Grinding and Polishing Guide Buehler
.jpg)
Iron Ore Pelletizing Process: An Overview IntechOpen
2018年7月17日 In the blast furnace, iron is reduced and melted and the most common product is liquid iron called hot metal In direct reduction, iron remains in solid state and the product is the socalled direct reduced iron (DRI) Generically, the iron ore products for ironmaking can be classified as shown in Table 1 2023年11月15日 PDF Iron Ore, Iron Ore Pellets, Direct Reduced Iron )DRI( Pellets, Iron Ore Pellets Market, Pelletizing Process, Sintering, Binder, Induration Find, read and cite all the research you need (PDF) IRON ORE PELLETIZING PROCESS ResearchGate2023年4月1日 An iron concentrate with iron content of 5544% and iron recovery of 8934% was obtained at a roasting temperature of 560 °C, the reaction time of 15 min, CO concentration of 30%, and a gas flow rate of 500 mL/min Hydrogen is also used to reduce red mud and decrease CO 2 emissions [85], [176]Toward sustainable green alumina production: A critical 2020年10月1日 After some other processes, αFe 2 O 3 red powder particles byproduct of regeneration of spent pickling liquor in ARP in iron and steel industry should be ground up to pigment grade to convert it to a value added product, red iron oxide pigment In this study, grinding tests on αFe 2 O 3 red powder were performed using four different types of An investigation on optimum grinding system and conditions
.jpg)
Process flow sheet for Pelletization using wet grinding process
Around 810 million tons of slimes are discarded during the washing process in India, containing about 4860% of Fe every year (Prakash et al, 2000), almost 15% of the total ore mined2023年10月9日 Comprehensive control of greenhouse gas emissions and response to climate change are concerns of countries around the world to protect living homes The steel industry is responsible for over 10% of global CO2 emissions, with approximately 80% of these emissions coming from the ironmaking process Great efforts have been made in both blast furnace (BF) Development and Problems of Fluidized Bed Ironmaking Process2021年6月15日 Biosynthesis of Iron Oxide Nanoparticles using Fungi Extracellular synthesis of iron oxide nanoparticles by using fungal species is considered to be advantageous bearing in mind the ease of scale up, use of economical raw materials for growth, high biomass forming capacity, simple downstreaming steps, low toxicity of residue and economic feasibility Green Synthesis: An Ecofriendly Route for the Synthesis of Iron Oxide 2024年8月17日 Defect name: features: Main causes: Stoma : There are smooth holes of different sizes inside or on the surface of the casting ① The furnace charge is not dry or contains many oxides and impurities; ② Pouring tools or additives in front of the furnace are not dried; ③ Too much water is contained in the molding sand or too much water is brushed during mold Casting Production: Process Flow, Equipment, Principle and
.jpg)
The six main steps of iron ore processing
Six steps to process iron ore 1 Screening This step involves breaking up the iron ore to obtain an F 80 grind size before it can be ground Once the ore has been crushed, it is diverted to a stockpile The aim of this step is to ensure a Green pellets of around 18 mm size were made with optimum water content by prolonged hand rolling of moistened iron ore fines of BS 72 mesh size without bentonite as per flow chart (Fig 1) F Process flow chart of preparation of pellets2017年2月16日 Sintering is a thermal agglomeration process that is applied to a mixture of iron ore fines, recycled ironmaking products, fluxes, slagforming agents and solid fuel (coke)(PDF) Iron Ore Sintering: Process ResearchGate1 天前 The reds, oranges and yellows seen in some soils and on rocks are probably iron oxides Iron is the third most common element making up the Earth Iron is one of the three naturally magnetic elements; the others are cobalt and nickel Iron is the most magnetic of the three The principle ores of iron are hematite, (70% iron) and magnetite, (72% Iron Mining Process Equipment Flow Cases JXSC
.jpg)
Electrochemical chloriron process for iron production from iron oxide
2024年3月20日 Ironmaking processes that do not generate greenhouse gas (GHG) emissions are needed for netzeroemissions energy systems 1 Most emissions associated with iron and steel production result from stochiometric quantities of CO 2 (∼15 kg CO 2 per kg Fe) produced during reduction of iron oxide ores in blast furnaces 2, 3 Demand for steel is unlikely to 2022年10月20日 Iron ore handling, which may account for 20–50% of the total delivered cost of raw materials, covers the processes of transportation, storage, feeding, and washing of the ore en route to or during its various stages of treatment in the mill Since the physical state of iron ores in situ may range from friable, or even sandy materials, to monolithic deposits with hardness of Iron Ore Processing, General SpringerLink2023年8月19日 Process Mineralogical Assessment of the Grinding Products of the Per Geijer Iron OxideApatite Deposits Patrick Krolop a, Kari Niiranen , Sabine Gilbrichtb, and Thomas Seifertb aProcess and Product Development, LuossavaaraKiirunavaara AB (Publ), Kiruna, Sweden; bInstitute of Mineralogy, TU Bergakademie Freiberg, Process Mineralogical Assessment of the Grinding Around 810 million tons of slimes are discarded during the washing process in India, containing about 4860% of Fe every year (Prakash et al, 2000), almost 15% of the total ore minedProcess flow sheet for Pelletization using dry grinding process
制粉项目-2023.11.17.jpg)
Processing of Magnetite Iron Ores–Comparing Grinding Options
2009年1月1日 The design outcome is a process flowsheet that specifies the required equipment and their arrangements in the beneficiation plant The iron ore beneficiation plants normally include a series 2019年3月8日 Electrolytic inprocess dressing (ELID) is a grinding technique used to generate highquality surfaces on hard and brittle material Oxide layer formed on grinding wheel during ELID grinding heavily influences the surface roughness of the workpiece To study the microscopic structure of the oxide layer and model the thickness of it, we conducted a Microscopic characterization and modeling of oxide layer for 2023年11月8日 The rise of antimicrobial resistance caused by inappropriate use of these agents in various settings has become a global health threat Nanotechnology offers the potential for the synthesis of nanoparticles (NPs) Iron Oxide Nanoparticles: Green Synthesis and 2022年1月13日 For finegrained iron oxide minerals, the iron oxide minerals distribution of 80–100% composition class differed by 22% at −75 + 53 μm size fraction with the two grinding methods, and its Process Mineralogical Assessment of the
.jpg)
Cement Manufacturing Process INFINITY FOR
The raw materials and fuel are counted as the major sources of the corrosive gases such as: sulphur oxides (SOx), calcium chloride (CaCl2), and nitrogen oxides (NOx)Corrosion situation affects the performance of raw milling 2024年4月1日 Fig 2 illustrates the iron ore beneficiation process, particularly magnetic separation, resulting in the generation of inevitable tailings Due to the characteristics of iron ores and the conditions during beneficiation, it is inevitable that approximately 25–3 tons of IOTs are generated for every 1 ton of iron ore concentrate produced [7]In 2019, the global annual A critical review on metallurgical recovery of iron from iron 2022年6月24日 Grinding is a manufacturing process which significantly contributes in producing high precision and durable components required in numerous applications such as aerospace, defence and automobiles(PDF) A comprehensive review on the grinding process: 2018年7月11日 The iron ore production has significantly expanded in recent years, owing to increasing steel demands in developing countries However, the content of iron in ore deposits has deteriorated and lowgrade iron ore has been processed The fines resulting from the concentration process must be agglomerated for use in iron and steelmaking This chapter Iron Ore Pelletizing Process: An Overview Semantic Scholar
.jpg)
Ultimate Guide to Aluminum Oxide Grinding Wheels RUISHI
2024年2月20日 A: You can purchase aluminum oxide grinding wheels online or at your local hardware store They are commonly found in the abrasive tools section or grinding accessories department Q: Can aluminum oxide grinding wheels be used on a bench grinder? A: Yes, aluminum oxide grinding wheels are compatible with bench grinders2019年3月21日 While there are many studies on the reduction from wüstite to iron [Citation 31–38] and reduction of iron oxides from 673 to 1473 K, this work focusses on the suspension reduction process of haematite and magnetite above 1473 K for emerging alternative ironmaking processes A reaction kinetics study is a basis for a study of the whole Review and data evaluation for hightemperature reduction of iron oxide 2021年8月13日 Thus, this work evaluates the performance of the VP50IM mold steel grinding process using feed rates of 025, 050, and 075 mm/min under the conventional lubrication method, comparing the results obtained with conventional wheels of white aluminum oxide, green silicon carbide, and white aluminum oxide and black silicon carbide grain toolGrinding behavior of VP50IM steel using green and black2023年9月8日 A stable and efficient operation of the ironmaking blast furnace is prerequisite to reduce the greenhouse gas emission JSW Steel, Salem have been proposed many projects to reduce greenhouse gas Blast Furnace process optimization for sustainable Iron making
.jpg)
High temperature flow synthesis of iron oxide nanoparticles:
2023年10月1日 High temperature flow synthesis of iron oxide nanoparticles: Size tuning via reactor engineering Hence, a different flow process allowing selfseeded growth was designed to produce larger IONPs 33 Green Chem, 18 (2016), pp 31843209 View in 2021年11月15日 Grinding Equipment (SiO2) icollidal suspension For certain materials, cerium oxide, chromium oxide, magnesium oxide or iron oxide may be used, although these the late 1920s, as Hoyt [7] mentions a visit to the Grinding and Polishing Guide Buehler2018年7月17日 In the blast furnace, iron is reduced and melted and the most common product is liquid iron called hot metal In direct reduction, iron remains in solid state and the product is the socalled direct reduced iron (DRI) Generically, the iron ore products for ironmaking can be classified as shown in Table 1 Iron Ore Pelletizing Process: An Overview IntechOpen2023年11月15日 PDF Iron Ore, Iron Ore Pellets, Direct Reduced Iron )DRI( Pellets, Iron Ore Pellets Market, Pelletizing Process, Sintering, Binder, Induration Find, read and cite all the research you need (PDF) IRON ORE PELLETIZING PROCESS ResearchGate
.jpg)
Toward sustainable green alumina production: A critical
2023年4月1日 An iron concentrate with iron content of 5544% and iron recovery of 8934% was obtained at a roasting temperature of 560 °C, the reaction time of 15 min, CO concentration of 30%, and a gas flow rate of 500 mL/min Hydrogen is also used to reduce red mud and decrease CO 2 emissions [85], [176]2020年10月1日 After some other processes, αFe 2 O 3 red powder particles byproduct of regeneration of spent pickling liquor in ARP in iron and steel industry should be ground up to pigment grade to convert it to a value added product, red iron oxide pigment In this study, grinding tests on αFe 2 O 3 red powder were performed using four different types of An investigation on optimum grinding system and conditions Around 810 million tons of slimes are discarded during the washing process in India, containing about 4860% of Fe every year (Prakash et al, 2000), almost 15% of the total ore minedProcess flow sheet for Pelletization using wet grinding process2023年10月9日 Comprehensive control of greenhouse gas emissions and response to climate change are concerns of countries around the world to protect living homes The steel industry is responsible for over 10% of global CO2 emissions, with approximately 80% of these emissions coming from the ironmaking process Great efforts have been made in both blast furnace (BF) Development and Problems of Fluidized Bed Ironmaking Process
.jpg)
Green Synthesis: An Ecofriendly Route for the Synthesis of Iron Oxide
2021年6月15日 Biosynthesis of Iron Oxide Nanoparticles using Fungi Extracellular synthesis of iron oxide nanoparticles by using fungal species is considered to be advantageous bearing in mind the ease of scale up, use of economical raw materials for growth, high biomass forming capacity, simple downstreaming steps, low toxicity of residue and economic feasibility 2024年8月17日 Defect name: features: Main causes: Stoma : There are smooth holes of different sizes inside or on the surface of the casting ① The furnace charge is not dry or contains many oxides and impurities; ② Pouring tools or additives in front of the furnace are not dried; ③ Too much water is contained in the molding sand or too much water is brushed during mold Casting Production: Process Flow, Equipment, Principle and