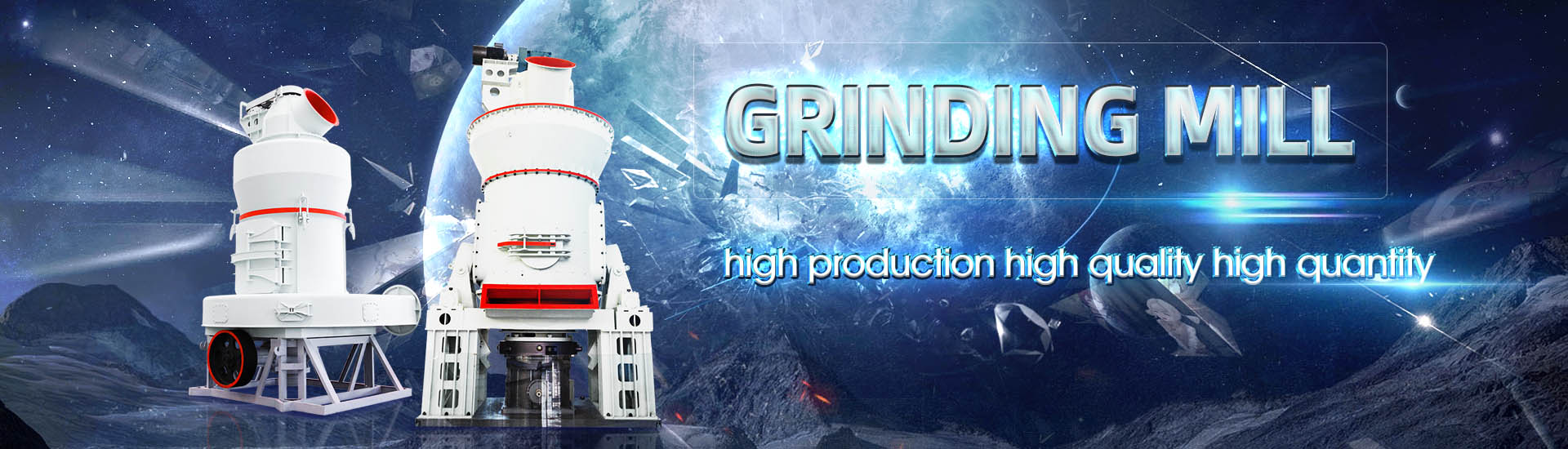
Research on new coal grinding method using steel ball coal mill
.jpg)
Grinding kinetics of coal in wet ballmilling using the Taguchi method
2019年4月19日 Grinding kinetics of −30 + 10 mm coal in wet ballmilling were investigated using the breakage rate and primary breakage distribution functions The deceleration effect 2020年1月1日 In this study, experimental data for wet and dryground coal samples under wet and dry grinding are characterized by commonly used distribution functions First, both the R Wet and dry grinding of coal in a laboratoryscale ball mill: 2023年10月27日 Grinding media play an important role in the comminution of mineral ores in these mills This work reviews the application of balls in mineral processing as a function of the A Review of the Grinding Media in Ball Mills for Mineral 2024年11月1日 To fill this gap, this study aims not only to explore dissociation characteristics and particle shape properties resulting from the grinding of coking coal in a planetary ball mill Effect of grinding methods on slime dissociation
.jpg)
Effect of Grinding Behavior on Liberation of Coal Macerals J
Reactive macerals or vitrinite is mainly responsible for coking potential of a coal during carbonization method The effect of a novel grinding on coal maceral separation is studied in In the ball milling process, steel balls function as not only a grinding action implementer but also energy Understanding the energysize reduction relationship is vital to grinding process; Wet and dry grinding of coal in a laboratoryscale ball mill: 2022年5月10日 Grinding of coal up to μm size is indispensable to achieve its maximum calorific value and better combustion A systematic experiment, as well as modeling of grinding of A statistical analysis and optimization of Indian coal 2021年4月20日 The liberation characteristics of long flame coal from the Chinese Shenhua were studied by comparison of ball grinding and rod grinding First, the effects of grinding time on Study on maceral liberation characteristics of ball grinding
.jpg)
Optimization and transformation of 300MV units steel
2023年11月7日 Pulverized Coal System of Steel Ball Mill for 300MW Unit In modern pulverized coal boilers, pulverizing system has become an indispensable part of the2016年8月1日 In the presented study, a nonlinear duplex inlet and outlet ball mill model with four inputs and four outputs is established The dynamic characteristics of coal moisture, fill level Modeling and control of ball mill system considering coal moisture2016年4月1日 Using a ball mill coalpulverizing system as a motivating/application example, a class of complex industrial processes is investigated in this paper, which has strong couplings among loops, high Modeling and control of ball mill system considering coal 2014年1月1日 Two mill systems are employed for most coal grinding applications in the cement industry These are, on the one hand, vertical roller mills (VRM) that have achieved a share of almost 90% and, on (PDF) MPS mills for coal grinding ResearchGate

Monitoring the fill level of a ball mill using vibration sensing
2019年10月19日 Ball mills are extensively used in the size reduction process of different ores and minerals The fill level inside a ball mill is a crucial parameter which needs to be monitored regularly for optimal operation of the ball mill In this paper, a vibration monitoringbased method is proposed and tested for estimating the fill level inside a laboratoryscale ball mill A vibration 2022年2月24日 An experimental study was performed in order to determine the main factors (rotational speed of the drum mill, the degree of loading with the grinding balls, and the velocity of the supplied air Improving the efficiency of the coal grinding process in ball What is a coal grinding mill, including the different types of grinding media, safety measures, and tips for optimizing efficiency How to choose the right coal grinding mill for your application They use steel balls to crush and grind the coal material, which is then discharged through a screen to separate the fine particles from the What is a Coal Grinding Mill ballmillssupplier2019年10月1日 The sizes of carbon particles of microscope photos were estimated using ImageJ software The calculation method of the cumulative size distribution of carbon particles referred to the literature Wet and dry grinding of coal in a laboratoryscale ball mill: Particle
.jpg)
Grinding kinetics of coal in wet ballmilling using the Taguchi method
2019年4月19日 Grinding kinetics of −30 + 10 mm coal in wet ballmilling were investigated using the breakage rate and primary breakage distribution functions The deceleration effect for the wet grinding of this coal sample was due to the relatively stronger material (quartz), which had a slower breakage rate compared to the weaker material (organic matter)2023年11月7日 systemThe advantages of using steel ball mill are:It is safe and reliable, easy to operate and maintain coal with low grindability and high moisture contentBut it also has its shortcomings:The Optimization and transformation of 300MV units steel 2014年5月1日 In the present work, a grinding rate constant, ie, a selection function was measured for five solid materials using a tumbling ball mill, and effects of a grinding ball diameter and a feed Exploring ball size distribution in coal grinding millsMill Feeders: Feeders for coal mill are generally installed directly under hoppers with rod gate in between The feeders are generally 2 to 3 m long and discharge on to conveyor or feeding chute to mill For coal mill feeding, table feeders, belt feeders, Coal Grinding Cement Plant Optimization
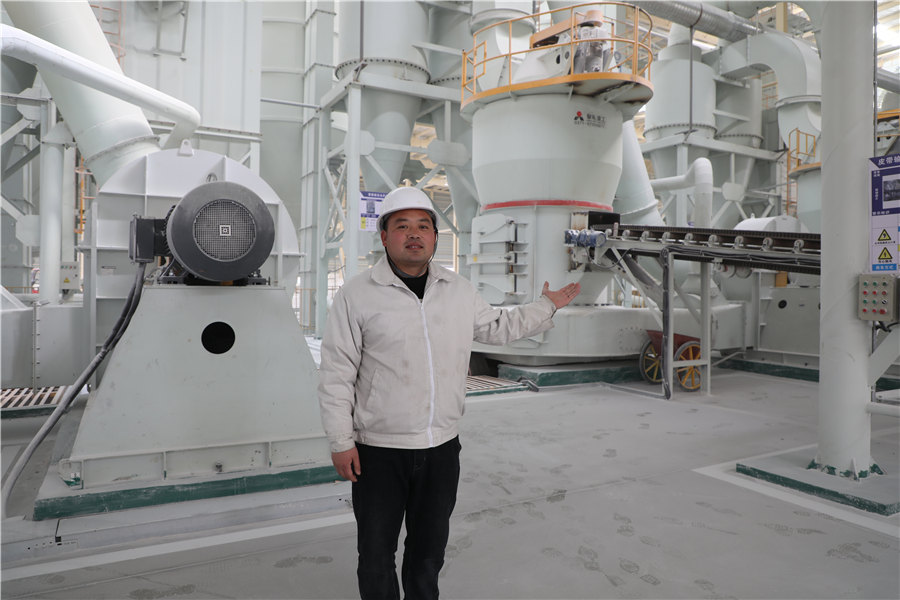
Ball Mill an overview ScienceDirect Topics
The correct sizes are often determined by trial and error, primary grinding usually requiring a graded charge of 105 cm diameter balls, and secondary grinding requiring 52 cm Concha et al (1988) have developed a method to calculate ball mill charge by using a grinding circuit simulator with a model of ball wear in a tumbling millThere are three types of grinding media that are commonly used in ball mills: • steel and other metal balls; • metal cylindrical bodies called cylpebs; • ceramic balls with regular or high density Steel and other metal balls are the most frequently used grinding media with sizes of the balls ranging from 10 to 150 mm in diameter [30]Grinding in Ball Mills: Modeling and Process Control2018年2月1日 In another study to investigate ball size distribution on ball mill efficiency by Hlabangana et al [50] using the attainable region technique on a silica ore by dry milling, a threeball mix of Effect of ball and feed particle size distribution 2023年5月25日 The difference in grinding productivity between semicoke and coal widens as grinding time increases, suggesting that the HGI method may overestimate the actual grindability of semicokeImpacts of Blending Semicoke in PCI Coal on Grinding
.jpg)
Ball Mill Grinding Process Handbook
2024年7月7日 This document provides guidance on ball mill grinding processes It covers topics such as ball mill design including length to diameter ratios, percent loading, critical speed, and internals evaluation Methods for assessing ball charge, wear rates, and liner management are described Empirical relationships for power draw and grinding laws are presented The is employed to determine the grindability of coal The HGI method involves placing a 50 g of airdried sample of 16+30 mesh (+118 mm 600µm) size coal in a miniature vertical spindle ball mill’s mortar along with 1inch steel balls A weighted upper race is placed on the coal sample and the steel balls and the ball mill is madeA Study on 500 MW Coal Fired Boiler Unit’s Bowl Mill 2021年6月29日 The rotating mill is filled with different steel balls of sizes 25 mm, 40mm, 50mm, 60 mm, 70mm and 80 mm with 45%, 40% and by crushing and grinding using a ball jar mill After gridding, the Effects of Mill Speed and Air Classifier Speed on 2021年11月1日 Monitoring mill load is vital for the optimization and control of grinding process This study proposed the use of an instrumented grinding media to assess solid loading inside a ball mill, with Assessing load in ball mill using instrumented grinding media
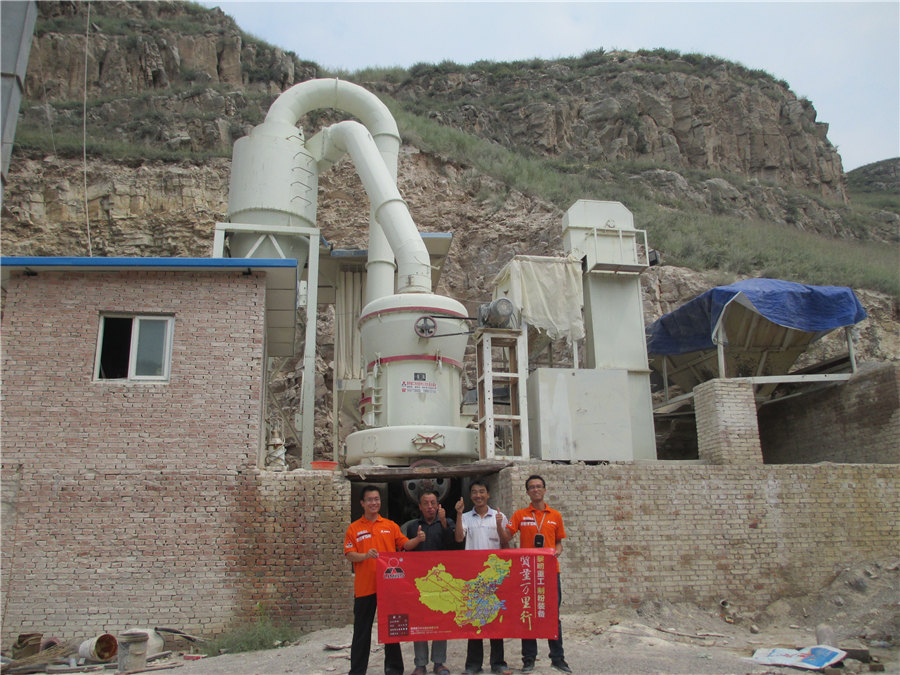
Correlation Analysis of Boiler Operation Parameters Based on Mill Ball
2015年10月13日 Coal fired boiler includes the combustion system, steamwater system, attemperation system, air and flue gas system, pulverizing system and the soot blower system []Ball mill is an important part of the combustion system, and the coal pulverizing and treating process is shown in Fig 1The coal falling into coal feeder from coal bunker is grinded up in 2017年3月20日 An effect of a grinding method, that is ball mill and high pressure grinding rolls (HPGR), on the particle size, specific surface area and particle shape of an iron ore concentrate was studiedPhysicochemical Problems of Mineral Processing Investigation 2022年5月10日 size of coal particles for ball mill feed was 35 +1 mm Grinding tests were performed in a cylindrical laboratoryscale ball mill and specifications of the ball mill and balls are mentioned in Table 2 The rotation speed of the ball mill was kept below the critical speed Table 1 The values of F 80, P 80, G b and W i of differentA statistical analysis and optimization of Indian coal In this test, a vertical stirring ball mill with 5 mm and 8 mm alumina ceramic ball grinding media was used The media filling rate was 40%, and the spindle speed of the mill was 300 r/min The process flow for preparing UCC from slime is shown in Fig 1 Fig 1 The process flow of preparing ultra clean coal from slimeInfluence of grinding methods on the preparation of
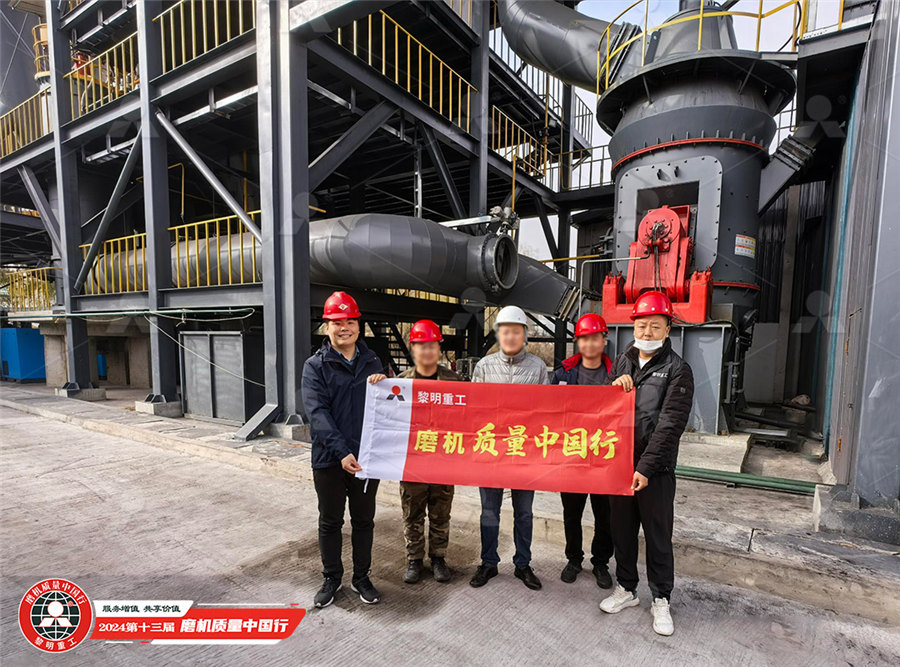
Operation Analysis of a SAG Mill under Different
2020年10月9日 In order to obtain the optimal operation parameters of a SAG mill, in this paper, the discrete element method (DEM) is used to simulate the breakage process of the particles by controlling three 2022年1月1日 The d80 and the amount of −37 μm fraction in the product were defined as process responses to model the ball mill grinding based on BoxBhenken design method using DX software Ball size Effect of grinding media on the milling efficiency of a ball millPDF On May 1, 2019, N A Shaburova published Failure of Steel Grinding Balls Find, read and cite all the research you need on ResearchGate(PDF) Failure of Steel Grinding Balls ResearchGateTube mills use steel balls as grinding media Due to wear in the abrasive environment it is necessary to charge new balls periodically to maintain a steady balanced ball charge in the mill The amount and ball size distribution in this charge, as well as the frequency with which new balls are added to the mill, have significant effects on Exploring ball size distribution in coal grinding mills
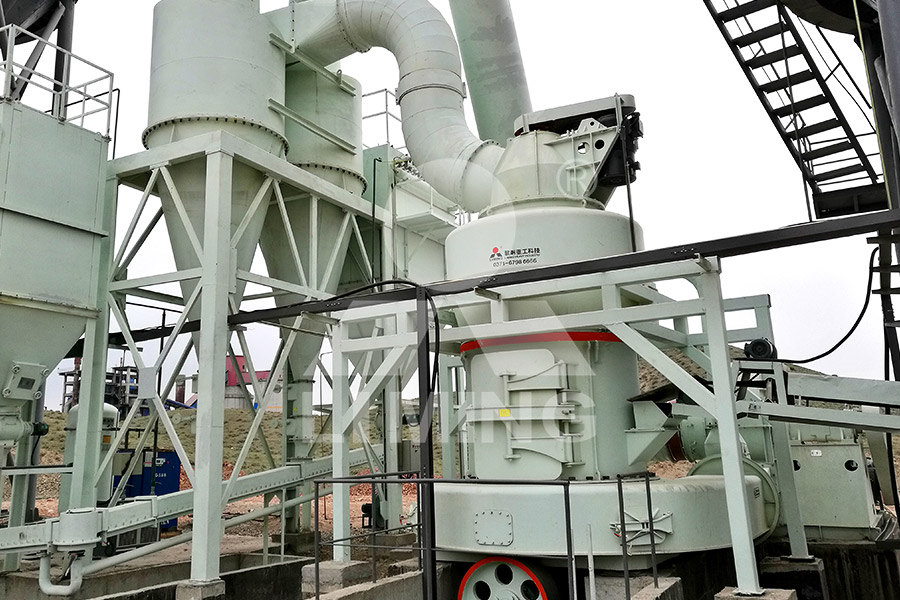
(PDF) SIZE REDUCTION BY GRINDING METHODS
2017年3月4日 ball mills, grinding (steel) balls or pebbles are often added to stirred mills to help grind ore, howev er these mills contain a large screw mounted ver tically to lift and grind material In tow 2020年1月1日 The results demonstrated that the proposed method can effectively detect critical blockage in a coal mill and issue a timely warning, which allows operators to detect potential faults Schematic Early Warning of Critical Blockage in Coal Mills Based on 2022年4月16日 This study investigated ultrafine coal grinding performance of four low to moderatecost grinding media in a laboratory stirred mill Kinetic grinding tests showed that silica beads generated Optimization of operating conditions on ultrafine coal grinding 2024年11月23日 Grinding steel balls are made by a series of processing methods: rough, heating, forging (rolling) into balls, then are hardened by heat treatment 1 Rough: Steel grinding balls use bearing scrap steel as raw material, with a large amount of copper, molybdenum, nickel and other precious metal elements added to make the structure more compact Choose the Best Grinding Steel Balls for Your Ball Mill Fote
.jpg)
Modeling and control of ball mill system considering coal
2016年4月1日 Using a ball mill coalpulverizing system as a motivating/application example, a class of complex industrial processes is investigated in this paper, which has strong couplings among loops, high 2014年1月1日 Two mill systems are employed for most coal grinding applications in the cement industry These are, on the one hand, vertical roller mills (VRM) that have achieved a share of almost 90% and, on (PDF) MPS mills for coal grinding ResearchGate2019年10月19日 Ball mills are extensively used in the size reduction process of different ores and minerals The fill level inside a ball mill is a crucial parameter which needs to be monitored regularly for optimal operation of the ball mill In this paper, a vibration monitoringbased method is proposed and tested for estimating the fill level inside a laboratoryscale ball mill A vibration Monitoring the fill level of a ball mill using vibration sensing 2022年2月24日 An experimental study was performed in order to determine the main factors (rotational speed of the drum mill, the degree of loading with the grinding balls, and the velocity of the supplied air Improving the efficiency of the coal grinding process in ball
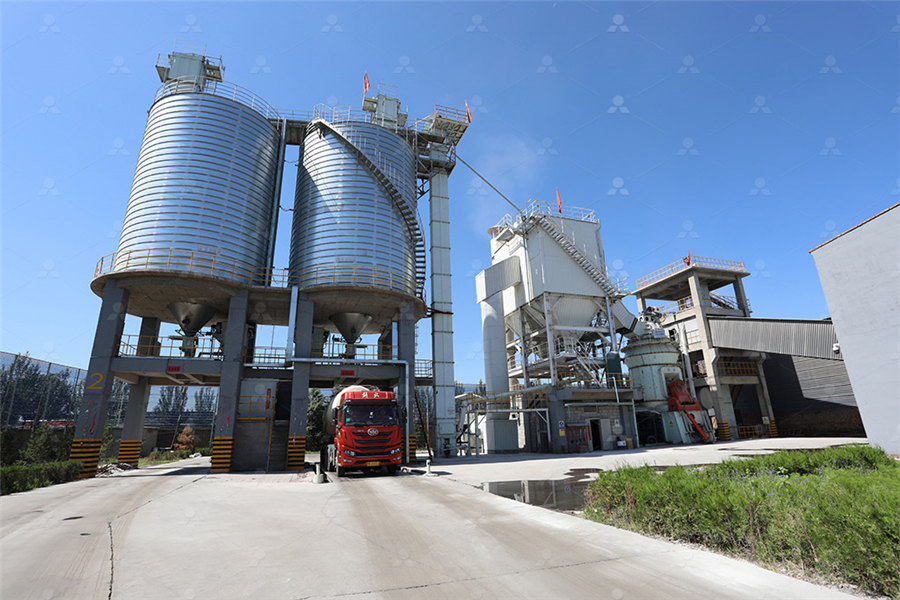
What is a Coal Grinding Mill ballmillssupplier
What is a coal grinding mill, including the different types of grinding media, safety measures, and tips for optimizing efficiency How to choose the right coal grinding mill for your application They use steel balls to crush and grind the coal material, which is then discharged through a screen to separate the fine particles from the 2019年10月1日 The sizes of carbon particles of microscope photos were estimated using ImageJ software The calculation method of the cumulative size distribution of carbon particles referred to the literature Wet and dry grinding of coal in a laboratoryscale ball mill: Particle 2019年4月19日 Grinding kinetics of −30 + 10 mm coal in wet ballmilling were investigated using the breakage rate and primary breakage distribution functions The deceleration effect for the wet grinding of this coal sample was due to the relatively stronger material (quartz), which had a slower breakage rate compared to the weaker material (organic matter)Grinding kinetics of coal in wet ballmilling using the Taguchi method 2023年11月7日 systemThe advantages of using steel ball mill are:It is safe and reliable, easy to operate and maintain coal with low grindability and high moisture contentBut it also has its shortcomings:The Optimization and transformation of 300MV units steel
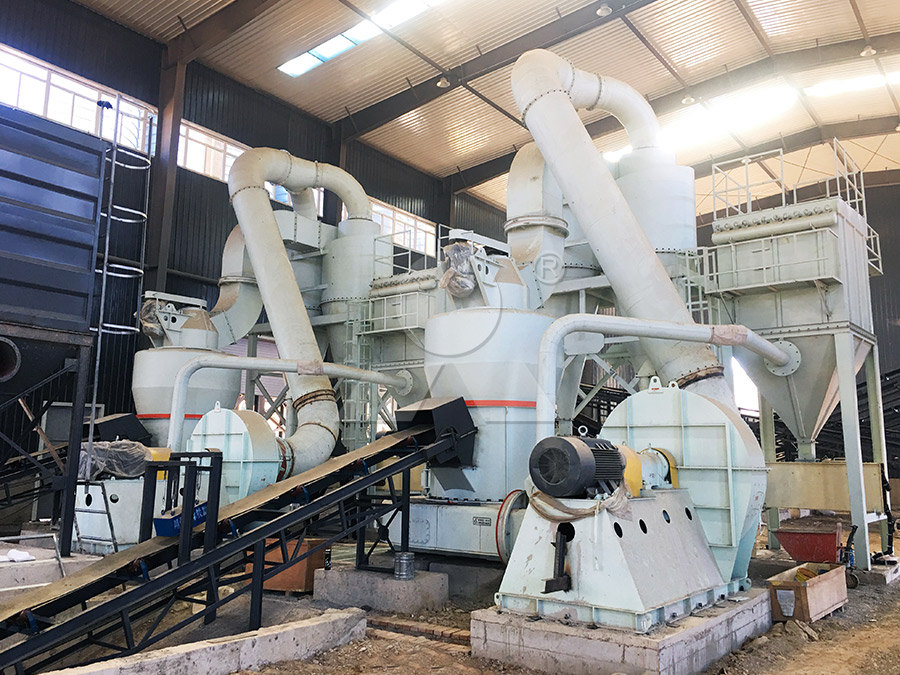
Exploring ball size distribution in coal grinding mills
2014年5月1日 In the present work, a grinding rate constant, ie, a selection function was measured for five solid materials using a tumbling ball mill, and effects of a grinding ball diameter and a feed Mill Feeders: Feeders for coal mill are generally installed directly under hoppers with rod gate in between The feeders are generally 2 to 3 m long and discharge on to conveyor or feeding chute to mill For coal mill feeding, table feeders, belt feeders, Coal Grinding Cement Plant Optimization